In Mexico, Schneider Electric Showcases “Lighthouse” Accomplishments
Founded in 1836 when two brothers, Adolphe and Joseph-Eugene Schneider, took over the Le Creusot foundry in Burgundy, France, Schneider Electric today is a €38 billion energy management and automation provider with 150,000 employees doing business in more than 100 countries.
The company manufactures its broad array of electrical and automation products at 200 factories around the globe, seven of which have achieved the distinction of being awarded World Economic Forum Lighthouse status. The WEF Lighthouse program measures adoption of advanced 4IR technologies, the financial and operational accomplishments, and its set of transformation enablers. There are 189 Lighthouses worldwide.
Approximately 100 Manufacturing Leadership Council members and guests toured one of Schneider Electric’s Lighthouse facilities earlier this month in Monterrey, Mexico. Known as Monterrey Plant 1, the seven-year-old, 450,000-square foot facility makes, warehouses, and distributes electrical products such as circuit breakers, panel boards, and numerous electrical distribution products.
The Monterrey factory’s digital management backbone is Schneider’s EcoStruxure platform, described by the company as an open, Internet-of-Things-based system that combines embedded connectivity, intelligence, and standard communication protocols to generate operational data, analyze that data, and make control decisions.
The EcoStruxure system has enabled the Monterrey plant to reduce downtime by 25% while achieving a 29% reduction in energy consumption. Schneider Electric says the Monterrey factory is the first factory in Mexico to achieve zero waste to landfill. The factory’s sustainability effort is part of Schneider Electric’s corporate goal to achieve Net Zero by 2050.
The tour for MLC members consisted of 10 stops on the factory floor. At each stop, Schneider Electric team members explained how they work, the systems they use, and how their particular work area fits into the factory’s overall flow. Among these stops, visitors witnessed data center resiliency, the company’s Lean Digitization System, deep learning vision for quality, IoT and machine learning for metal finishing operation uptime, and standardized MES for panel board assembly operations. Advanced MPH was also on display with the use of drone technology for warehouse cycle count and AGV utilization.
After the tour, a panel discussion with plant management, moderated by MLC, was held to allow MLC members to ask questions about what they had seen on the plant floor. Breakout sessions on brownfield plants, the Schneider supply chain, and the WEF’s Lighthouse program were also held during the day.
The MLC’s next plant tour will take place at United Scrap Metal on August 12-13, 2025 in Cicero, Illinois. Register for this tour and learn more about all of MLC’s plant tours: https://manufacturingleadershipcouncil.com/event/plant-tours.
About the Authors:
David R. Brousell is founder, vice president and executive director of the Manufacturing Leadership Council
Steven Moskowitz, Ph.D., is the senior director, event content at the Manufacturing Leadership Council.
Reflections on Hannover Fair 2025
Now in its 14th year, Industrie 4.0 is still leading the way to manufacturing’s future in Europe as the continent seeks to become more competitive in a changed geopolitical environment.
A burning question for me as I was planning my visit to the Hannover Fair last week was: after 14 years in the market, what’s the state of Industrie 4.0 in Europe today?
I had a sneaky suspicion that it was going to be hard to get an answer to this question as I toured the massive exhibit halls, attended conference sessions, and spoke to many German and other European manufacturing and technology executives.
My suspicion proved to be correct. The reason: it’s a complicated question. There are many variables that influence the answer—company size, industry sector, and country dynamics as well as the standard leadership, organizational, and cultural factors in companies. The other major factor at work is that the Hannover Fair is primarily a technology supplier exhibition, so I had to guard against hype and bias that might shape opinions.
Nevertheless, there were signals, indications that suggest that digital transformation in manufacturing is an evolving concept in a Europe that, because of the current geopolitical climate, has a greater motivation and urgency to find new ways to innovate and compete.
Assessing Digital Maturity
In the U.S., MLC research has been showing that manufacturers’ digital maturity has slowly progressed from initial stages of adoption to what MLC has been calling the next phase of 4.0 characterized by larger and more extensive projects and the beginnings of business model transformation, where the real payoff from 4.0 will be found.
Most manufacturers surveyed by MLC cluster around the middle of a digital maturity scale of one to 10. Only a few inhabit the rarified higher ground, and there are still many small and medium size companies that are trying to climb up to the middle of the curve. Would I find a similar status among the manufacturing community in Europe, I asked myself, or would there be a substantial difference and even the possibility that European manufacturers are ahead of their U.S. counterparts?
My sense coming out of Hannover is that, in the main, there is a rough equivalence in where the industries stand in adoption of digital transformation. This sense was validated in a conversation I had at Hannover with Raimund Klein, chief executive officer of the International Center for Industrial Transformation, which describes itself as a non-profit environmental, social and governance institution which champions manufacturing transformation.
Klein, who spent 37 years at Siemens, claims his Smart Manufacturing Readiness Index shows that, globally, manufacturers are still at an early stage with the digital work. Using a zero to five scale, the index pegs global manufacturing readiness for digital transformation as a whole at 1.88, with North America at 1.80 and Europe at 1.62.
Why the relatively low numbers? Leadership and organizational constraints, as well as legacy system issues, are the key factors governing readiness and adoption, he says. MLC research has been showing similar findings for many years.
Leading the Charge in Data Management
But whatever the numbers, I suspect that the Europeans may be ahead in one crucial area – data management.
The reason I say this is because the Europeans are addressing important aspects of data management such as interoperability and data sharing via a large collection of technical associations and initiatives, some of which are unknown to many U.S. manufacturing executives.
The theory behind the emphasis on data is that manufacturers will innovate faster and compete more effectively if they can share and leverage data up and down supply chain ecosystems, while maintaining what is called “data sovereignty”, the ability to control IP and who can access data.
One of the latest European initiatives I learned about at Hannover last week is called 8ra. Begun about one year ago, the 8ra Cloud Edge Continuum is an attempt to deal with a “fragmented” European cloud landscape that is said to be holding back interoperability and integration.
8ra’s mission, a Platform Industrie 4.0 initiative backed by 12 EU member states and about 120 industrial and research partners, is to “establish a resilient, open and future-proof” next-generation cloud infrastructure.
“Without a coordinated effort, Europe risks falling behind in key technology fields such as AI, industrial IoT, the metaverse, and cybersecurity,” the organization says.
A Reliance on Platform Industrie 4.0
The concept of Industrie 4.0, backed by the German government, was introduced at Hannover in 2011 (MLC introduced its Progressive Manufacturing idea, which it later called Manufacturing 4.0, in 2005). Over the years, the Industrie 4.0 concept has evolved to include adoption of the OPC UA specification, in 2020; the formation of the Industrial Digital Twin Association (IDTA), also in 2020; and 8ra in 2024. This year at Hannover, Platform Industrie 4.0 was emphasizing the industrial metaverse, which MLC and Deloitte have defined as a collection of technologies.
Platform Industrie 4.0, a German government-based organization, also promotes its Manufacturing-X initiative to digitize supply chains as well as its 2030 Vision to shape digital ecosystems.
There is also a plethora of technical associations addressing different aspects of data interoperability. For example, the Industrial Data Spaces Association, a Dortmund-based non-profit that says it has 170 members from 30 countries, is focused on establishing technical standards for so-called data spaces. The goal is to enable trusted data sharing across industries and borders.
Another group, which grew out of the Platform Industrie 4.0 initiative, is the IDTA. Based in Frankfurt, the IDTA provides education on digital twin technology, including training and seminars. The IDTA claims about 120 members.
In the U.S., CESMII, The Smart Manufacturing Institute, a Department of Energy program and part of the Manufacturing USA network of 16 manufacturing-oriented institutes, has been working with the IDTA, the OPC Foundation, and other organizations to create a best of breed system architecture for digital product passports, which will be required by the European Union in 2027. CESMII has also been working with the Manufacturing-X group. (In the U.S., NIST has also been working on data interoperability; MLC Board member Jim Davis of UCLA has been participating in this work).
At Hannover, CESMII CEO John Dyck, a new member of the MLC Board of Governors, announced an agreement with the OPC Foundation, a Scottsdale, Arizona-based group, involving a tool CESMII has developed to build what are called standard manufacturing information models (MIMs) for manufacturing assets/processes and supply chain data exchanges. This open-source tool is called the CESMII SM Profile Designer. In order to accelerate the adoption of these MIMs, the OPC Foundation will launch an open-source project and work together with the CESMII ecosystem to sustain it, empower the OPC community of over 1,000 members to learn about and use the tool, and develop new MIMs for CESMII’s SM Marketplace.
In addition to its collaboration with CESMII, the OPC Foundation in March announced an “expanded collaboration” with IDSA to enhance data interoperability and data governance in the automation industry. And OPC also has a cloud initiative underway. It held a conference on this topic at Hannover.
But there appears to be a larger critical mass of organizations working on the various aspects of data interoperability and sharing in Europe than in the U.S. The question is: can all the European associations and organizations working on data collaborate effectively and not overlap and create confusion? Time will reveal the answer to that question but what is clear today is that it would be very difficult for most manufacturing companies, particularly those in the U.S and especially small and medium size companies, to even be aware of what many of these groups are doing let alone understanding their concepts and adopting their approaches to data interoperability and data sharing.
As Douglas Ramsey, a managing partner at Axial GA, a consulting firm, and CESMII’s delegate to the International Manufacturing-X Council, said at a meeting of the IDTA at Hannover last week: “If I asked an American manufacturing audience about data spaces, I would get a blank look.”
A Heightened Worry About Bureaucracy
There was a pervasive feeling at Hannover Fair this year that the best way for European industry to become more competitive, in order to deal with issues such as the current disruptive geopolitical environment, is to double-down on innovation, cooperation, investments in technologies such as AI, and to reduce bureaucracy to speed up change.
Although there have been complaints about bureaucracy in the past, there was a heightened intensity about it at the Fair this past week.
“Sometimes we don’t believe in ourselves in Germany,” said Cedric Neike, CEO of Digital Industries at Siemens, during a panel session called Leaders’ Dialogue. “It is difficult to get rid of the bureaucracy. We need to have boldness to invest in the right things and not to invest in the past.”
Added Peter Leibinger, President of the Federation of German Industries and Chairman of the Supervisory and Administrative Board at TRUMPF SE & Co. KG: “We have an attitude, knowledge and power problem. We have to kill the monster bureaucracy. It creates a defensive attitude in our companies. We must get back to risk affinity.”
Convinced that Industrie 4.0 has been the right technological foundation to ensure industry competitiveness, industry leaders believe that they can “upgrade” the I4.0 concept with AI – if adoption can be accelerated. There was an abundance of AI products in the thousands of exhibitions at Hannover last week – nearly every tech vendor was supporting AI in one way or another.
The need for a new European mindset based on greater cooperation and collaboration, data sharing, and less regulation will be key to making Europe more competitive. This will require extraordinary levels of coordination, cooperation, and, most importantly, leadership. Can European industry rise to the occasion?
The challenge was perhaps best summed up by Valentino Valentini, Deputy Minister, Ministry of Enterprises and Made in Italy, who said: “We have to get out of the triangle of the U.S. invents, China copies, and Europe regulates.”
About the author:
David R. Brousell is the Founder, Vice President and Executive Director, Manufacturing Leadership Council
Germany, Canada Push Back on U.S. Policies at Opening of Hannover Fair
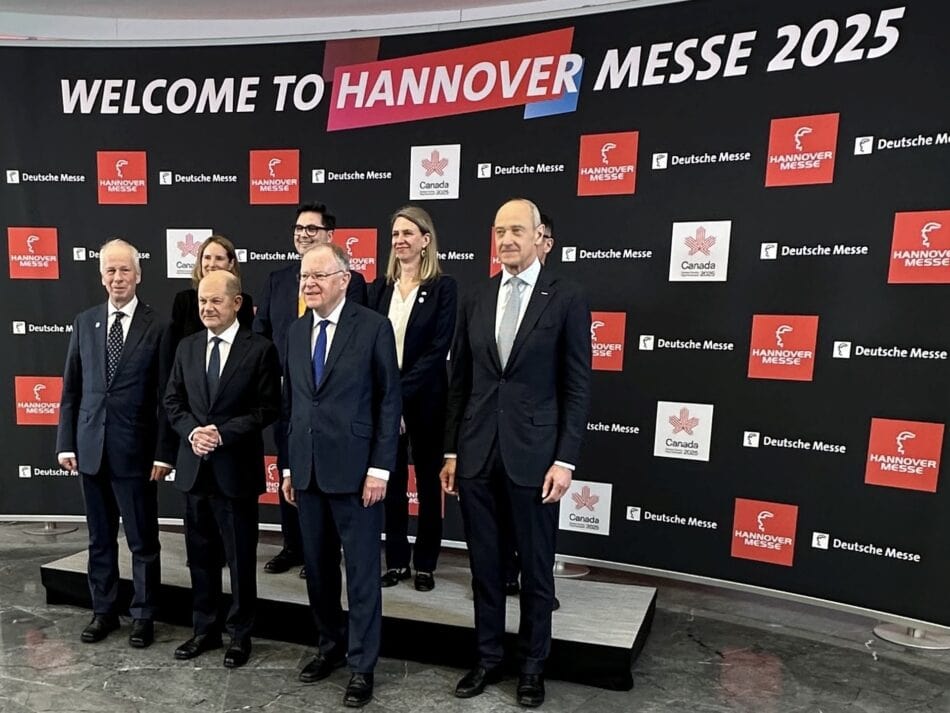
Geopolitics took center stage at the opening ceremonies of the Hannover Fair in Germany last night, as German and Canadian government and industry officials criticized U.S. policy on tariffs and trade and declared their support for the independence of Canada.
“Rarely has there been so many political messages at a Hannover Fair,” said German Chancellor Olaf Scholz. “Trade wars have no real winner, not even the U.S. Europe’s goal is cooperation. But if there is no chance of this, we will act as a unified front.”
Even though Scholz and other speakers did not mention the Trump Administration by name, their messages were clearly targeted at the tariff, trade, and defense polices of the new U.S. administration. Phrases such as “open markets”, “reliable partners”, “respect for neighbors”, and “stable environments” dominated the opening ceremony speeches.
President Donald Trump’s statements about Canada, the partner country for this year’s Hannover Fair, becoming the 51st state of the U.S. received pointed rebukes.
“Canada is not a state of any other nation,” said Scholz. “It will never be part of the U.S.”
It is customary for the Hannover Fair partner country to have its head of state or government participate in the Fair’s opening ceremonies in person. Because Canada is in the midst of a national election, the new Prime Minister, Mark Carney, could not attend. Instead, Stephane Dion, Special Envoy to the European Union and Europe, spoke at the ceremonies, emphasizing Canada’s commitment to free trade, its reliability as a partner, and its willingness to strengthen ties with friendly nations.
“Canada is an ally, a friend,” Dion said. “We believe in win/win agreements. We have respect for international law and mutual trust.” With regard to trade relations with Germany, he said: “We knew we liked each other; now, we know we need each other.
But it was also clear from the speeches at the opening ceremonies that the countries and their industrial companies are now operating in a new environment. Siemens AG CEO Roland Busch said the new geopolitical environment is an opportunity Germany must seize.
“The operating system of the world is becoming obsolete,” he said. “It is time for a new one. We must re-invent how we grow together. Germany has been held back by excessive bureaucracy. We need less and more and faster innovation.”
Busch also addressed a major focus of the Hannover Fair this year – artificial intelligence.
He said companies won’t succeed by just adding AI into what they are currently doing. They have to re-think their processes and rebuild. He also warned about the stakes of not moving aggressively to adopt and learn about AI.
“In a few years from now, there will be a divide between those that embrace AI and those that don’t,” Busch said. “This may be the last generation of managing companies with just humans.”
Last night, Siemens won the Fair’s coveted Hermes Award for its Industrial Co-Pilot generative AI tool.
On Monday, the Hannover Fair exhibition opens. There are approximately 4,000 companies showing and demonstrating their technology and industrial products. About 130,000 people are expected to attend.
About the author:
David R. Brousell is the Manufacturing Leadership Council’s Founder, Vice President and Executive Director
The AI Glossary for Manufacturing Leaders: Key Terms You Need to Know
AI is revolutionizing manufacturing, but do you know the essential terms? This quick guide breaks down key technologies driving the future of industrial innovation.
As manufacturing leaders navigate Manufacturing 4.0’s complexities, artificial intelligence has emerged as a critical enabler of digital transformation. With AI evolving rapidly, staying on top of the latest terms and technologies can feel overwhelming.
To cut through the complexity, we’ve put together a quick guide to key AI concepts shaping manufacturing today. Whether you’re exploring predictive maintenance, product development, or human-machine collaboration, understanding these AI technologies will give you a clearer picture of their potential impact on your operations.
- Agentic AI: AI systems capable of autonomous decision-making and action-taking to accomplish goals, often integrating planning, reasoning, and adaptability to dynamic environments.
- Causal AI: AI that goes beyond correlation-based learning to understand cause-and-effect relationships, improving decision-making, diagnostics, and scientific discoveries.
- Edge AI: AI that runs on local devices rather than centralized cloud servers, enabling real-time processing and low-latency applications in areas like IoT, industrial automation, and smart devices.
- Generative AI: AI models that create new content, such as text, images, audio, or code, based on training data. Examples include ChatGPT for text and DALL·E for images.
- Large Language Models/Small Language Models: LLMs are advanced AI models trained on vast amounts of text to generate human-like language, while SLMs are smaller, more efficient models optimized for specific tasks with lower computational requirements.
- Machine Learning: A subset of AI that enables systems to learn from data, identify patterns, and make decisions with minimal human intervention. It includes supervised, unsupervised, and reinforcement learning techniques.
- Natural Language Processing: AI focused on enabling computers to understand, interpret, and generate human language, allowing for applications like chatbots, translation services, and sentiment analysis.
- Physical AI: AI integrated into physical systems, such as robots or autonomous vehicles, enabling interaction with the physical world through sensors, actuators, and adaptive control.
- Vision Systems: AI that processes and interprets visual data from the world, such as images or videos, enabling tasks like facial recognition, object detection, and quality control in manufacturing.
Future of Manufacturing Project: The Growing Competition for AI Supremacy
The Future of Manufacturing Project has become the premier platform for exploring the transformative forces shaping the manufacturing industry. At the 2024 event, David R. Brousell, MLC’s Founder, Vice President and Executive Director, delivered a powerful opening address that set the tone for the discussions and presentations to come. In his speech, Brousell examined the meteoric rise of AI technologies like ChatGPT, the growing global competition for AI leadership, and the profound implications for manufacturers. He offered data-driven insights, candid reflections on challenges, and practical guidance for navigating the AI-driven future. Below is a recording and the full text of his address — an essential read for anyone seeking to understand the opportunities and responsibilities that lie ahead for manufacturing and beyond.
Good morning, everyone, and welcome to the fourth annual Future of Manufacturing Project event.
Two years ago in Nashville, when MLC first devoted this event to examine the potential as well as challenges with artificial intelligence in manufacturing operations, OpenAI had just released the generative AI tool ChatGPT.
I had mentioned OpenAI in my talk that day, but little did we know what would soon be coming. ChatGPT took off like a rocket ship, capturing the imagination of the public, businesses, and governments, raising both aspirations as well as fears about the technology.
ChatGPT reached 100 million users in just two months after its launch, becoming the fastest growing consumer application in history at that time. Today, ChatGPT has a reported 200 million users.
ChatGPT became an inflection point for AI in general. The energy and momentum around AI in its many forms – IBM alone has identified seven types of AI — have not only continued but appear to be picking up even more steam. In the generative AI market alone, a flood of competitors has joined ChatGPT including Midjourney, Stable Diffusion, Bard, and, of course, Copilot, and others.
The amount of literature being produced about AI – and I use the term “literature” with an asterisk attached – is almost impossible to keep up with. Every day, it seems, there are multiple newspaper and magazine articles, research reports, case studies, government reports, product and service announcements, and conferences extolling both the virtues and warning of the challenges with the technology.
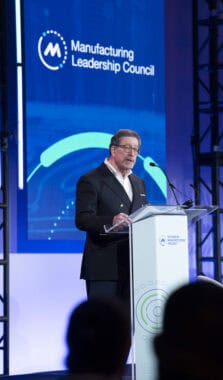
Huge sums of money are flowing into the AI market as nations earmark funds, announce national strategies, and set up organizations to capitalize on the technology; as technology and service providers produce new AI and augmented products and offer implementation methods; and as businesses assess the effect of AI on their competitive posture and develop their own goals and objectives with the technology.
As I said in Nashville two years ago, a worldwide competition for dominance in AI is underway – and it appears to be intensifying.
Here are a few datapoints to consider:
- In a report published in September, International Data Corp. predicted that AI would have a cumulative global economic impact of $19.9 trillion through 2030, representing 3.5% of global GDP by that year. Every new dollar spent on business-related AI solutions and services will generate, IDC estimated, $4.60 into the global economy, in terms of indirect and induced effects.
- Meanwhile, spending on AI is growing at double-digit rates. IDC estimated that worldwide spending on AI, including AI-enabled applications, infrastructure, and related IT and business services, will grow at a 29% compound annual growth rate between this year and 2028, reaching $632 billion in 2028. In terms of use cases, Smart Factory floor investments are expected to grow at a 32.5% CAGR in that time period.
- The number of AI patents granted worldwide rose 62.7% between 2021 and 2023, according to the 2024 Stanford AI Index Report. In 2022, China led global AI patent origins with a 61.1% share, significantly outpacing the U.S., which accounted for 20.9% of AI patent origins. In that same year, however, the U.S. far exceeded China in terms of financial investments. In the U.S., AI investments reached $67.2 billion in 2022, 8.7 times more than China.
- Announcing AI strategies has become commonplace among nation states. The U.S. has its National AI Initiative Act, a Presidential Executive Order on AI, and is in the process of standing up an AI Institute under the America Makes program.
- In China, well, we know there is much activity but getting reliable data is a challenge. For example, International Data Corp. estimates that China’s investment in AI will reach $38 billion in 2027. Meanwhile, a report in Yahoo Finance in September said that China’s AI industry could invest $1.4 trillion into developing the technology in the next six years. Pass the salt!
- On the other side of the world, the European Union has its AI Innovation Strategy, which calls for the creation of AI Factories across the European Union. Back in Asia, India has its AI Mission initiative; Japan’s Ministry of Economy, Trade and Industry has allocated $740 million to subsidize the AI computing industry in Japan; and South Korea has a plan to spend $6.9 billion by 2027 on artificial neural processing units and high bandwidth memory chips.
But one of the more notable announcements this year came from Saudi Arabia, which created a $100 billion fund to invest in AI and other technologies.
***
Now, cautious observers, particularly those with a historical context, might say that all the posturing and the financial projections and investment numbers merely reflect an inflated state of expectations, a euphoria born of excitement about the shiny new car. We are in what Gartner calls a hype cycle that will, in time, deflate as the challenges of implementing and optimizing use of the technology become better understood and experienced.
No doubt there is some truth in this. As we know from the experiences we’ve had with other technologies, strategic, organizational, cultural, and human behavioral challenges govern whether a technology project will ultimately be successful. I myself have talked for many years about what I call The Absorption Gap – the time and effort required to go from implementation to benefit. It often takes much longer to get to benefit than we think at the outset.
Could history repeat itself with AI? Could we yet experience a third AI winter, after the two that occurred last century when expectations were disappointed?
Anything is possible, of course, but I wouldn’t bet on it. The foundational conditions that were lacking years ago to enable AI to take off – compute power, storage, communications bandwidth, sufficiently large data sets – have all been addressed. Moore’s Law will ensure that price/performance will improve, perhaps significantly, over time. And the unrelenting need to find new competitive advantage will compel companies to go forward into the known and, perhaps more importantly, the unknown.
My friends, the AI train is leaving the station – and you must be on it.
***
The encouraging news is that aspirations with AI among manufacturers are strong and there is already some evidence that AI is, as they say, worth the squeeze.
Recent MLC research shines a light on what manufacturers are thinking about the use of AI in their operations.
Among the many findings of our new AI study, results of which were published in the Manufacturing Leadership Journal in August, perhaps the most important is that a majority of manufacturers, 55%, see AI as a “game-changer” in the industry by 2030, even though only 5% at this point in time assess their maturity level with AI in operations as “advanced”.
Perhaps propelled by this perception, 78% said they plan to increase spending overall on AI tools over the next 12 to 24 months, with
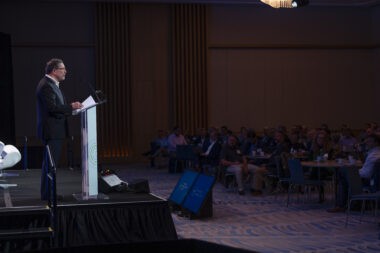
one-fifth expecting to increase their spending by more than 30%. Already, more than half are using GenAI tools such as ChatGPT or Microsoft’s Copilot, and more than 80% said they expect to increase the use of such tools in the next two years.
As manufacturers ramp up their AI investments, early indications about the impact and return on these investments are looking positive.
In July, EY, a member of the Manufacturing Leadership Council and a partner in the Future of Manufacturing Project, published the results of its first AI Pulse survey, which asked 500 senior leaders across industries in the U.S. about AI investments, impacts, and challenges.
The study found that senior leaders whose organizations are investing in AI have seen tangible results across business functions, including about three-quarters who are already experiencing positive ROI in operational efficiencies, employee productivity, and customer satisfaction.
Moreover, the EY study found that organizations that are committing 5% or more of their budgets on AI are seeing “outsized returns.”
And all of this is happening as AI continues to advance. This year’s Stanford report assessed that AI has now surpassed human performance on several benchmarks, including in image classification, visual reasoning, and English understanding. However, the technology still lags human capabilities in competition-level mathematics, visual common-sense reasoning, and planning, Stanford said.
I suppose that we can all take some comfort in those findings. We humans will continue to dominate – at least for the moment. We don’t know how fast AI will evolve and how capable and powerful it will become in the years ahead, but we know one thing for sure – with the amount of capital flowing into the AI market and the amount of effort being applied to its development, AI will not sit still.
As it continues to move, manufacturers have a host of issues to deal with to ensure that AI is used effectively to advance their organizations’ business and operational goals, and in a responsible manner.
Once again, MLC research spotlights some of the challenges.
The top concern, say 68%, is around data – quality, contextualization, and validation. More than 40% also identify AI skills and AI business case development as issues. Sixty-six percent say they do not have a specific set of metrics to measure the effectiveness and impact of AI implementations at this time.
This all goes back to that single digit finding I mentioned earlier about maturity levels with AI. The question is: what will it take to accelerate adoption and use of AI in operations and enable companies to climb up the maturity curve?
The easy answer is time, money, and persistence. But there’s a bit more to it than these three foundational elements. Please allow me to offer a few recommendations:
First, I can’t emphasize strongly enough about having a vision for what you want to do with AI. That may sound obvious, and it is on one level, but it takes a lot of thinking, strategizing and even soul-searching to craft an idea of what your company could be in 10 or 15 or 20 years.
So, think big about AI and what your company might be able to do with it. Think about the art of the possible. Think about growth and not just in what you are doing now but what you could be doing that’s new, innovative, and exciting.
At first, you will turn your attention to using AI to become more efficient, more cost-effective, faster. These are all important objectives, but don’t stop there. Imagine a better future.
And once you craft a business vision for the future – a vision that should be flexible enough to change when needed – make sure your AI strategy “functions as the fuel,” as Council member Deloitte says, for the business strategy.
Second, keep up with the evolution of the technology. There is a lot of energy and momentum around AI, as I have detailed, and new developments are occurring frequently. The technology must be monitored and understood, as well as the rules, laws, and regulations that will govern its use. Designate someone or a specific business unit in your company to keep track of developments to understand their potential to help your business.
Third, don’t try to go it alone. Plug into the community. MLC is here to bring together your fellow manufacturers, technology and services providers, academics and research organizations, and sister groups such as the IRI, CESMII, and MxD so you have access to a robust community for help.
Fourth, work on the metrics. Experimentation with AI is necessary and important, but the laws of business must be served. Find, adopt, and use ROI models to prove return so that investment continues.
Fifth, it is essential to take a human-centered approach to AI. Bring people along by showing them the benefits and being candid with them about the challenges. Change management and training are key.
Taken together, these simple, common-sense tenets can help you navigate your journey with AI.
***
What we do here today, and what you do after this conference when you go back to your companies, will help propel the manufacturing industry forward.
But our responsibility is greater than just our own industry. AI has not only the potential to reshape manufacturing but society itself. As it has many times throughout history, this industry is playing a vital role in deciding what the future might look like. Once again, the mantle of change lies at our feet.
I would like to close with a quote from a book called “The Age of AI And Our Human Future,” authored by Henry Kissinger, Eric Schmidt and Daniel Huttenlocher:
“The advent of AI, with its capacity to learn and process information in ways that human reason alone cannot, may yield progress on questions that have proven beyond our capacity to answer. But success will produce new questions … Human intelligence and artificial intelligence are meeting, being applied to pursuits on national, continental, and even global scales.
“Understanding this transition, and developing a guiding ethic for it, will require commitment and insight from many elements of society: scientists and strategists, statesmen and philosophers, clerics and CEOs. This commitment must be made within nations and among them. Now is the time to define both our partnership with AI and the reality that will result.”
Thank you and have a great conference.
About the author:
David R. Brousell is the Founder, Vice President and Executive Director, Manufacturing Leadership Council
Photos by David Bohrer / National Assoc. of Manufacturers
Get Ready for the Best of Manufacturing Leadership
As 2024 winds down, the Manufacturing Leadership Journal is capping off the year with a special “Best of” issue that celebrates the most impactful moments, insights, and innovations from the Manufacturing Leadership Council. Launching in December, this edition is a treasure trove of highlights showcasing the best content we’ve produced this year — and it’s not to be missed!
Here’s what’s inside:
- Best of MLC Research: Unlock the top takeaways from our groundbreaking research surveys that shaped conversations around Manufacturing 4.0 in 2024.
- Best of Rethink: Relive the energy of our premier event with video highlights from thought-provoking sessions, dynamic panels, and more.
- Best of the Future of Manufacturing Project: Discover insights from this year’s flagship initiative, including highlights from virtual events, Future of Manufacturing Project Crystal Ball articles, and the pivotal survey report, Data Mastery: A Key to Industrial Competitiveness.
- Best of the Manufacturing Leadership Journal: Revisit this year’s standout articles, which are packed with ideas and insights sure to move your Manufacturing 4.0 journey forward.
- Best of Decision Compass Calls: Access this year’s standout Decision Compass calls and hear discussions that provided actionable strategies and inspiration for manufacturing leaders.
Plus, dive into a photo retrospective celebrating the 20th anniversary of Rethink and the Manufacturing Leadership Awards Gala, and exclusive plant tours at EnerSys and Amazon.
In addition to the “Best of” features, this issue includes brand-new content including an introduction to the MLC’s newest members, a Future of Manufacturing Project article by EY, and an exclusive Executive Dialogue interview with Angela Accurso, co-winner of the Manufacturing Leadership Award for Next-Generation Leadership.
This “Best of” edition is your chance to reflect on the strides made in manufacturing leadership this year and gear up for the opportunities ahead. Be sure to check it out this December to celebrate and learn from the best of 2024!
The MLC Elects New Chair, Vice Chair and Two Leading Industry Figures to its Board of Governors
The Manufacturing Leadership Council (MLC), the digital transformation arm of the National Association of Manufacturers (NAM), has announced the election of new leadership for the MLC Board of Governors for 2024. Additionally, two leading figures from industry have been elected to join the Board. The MLC is the nation’s foremost executive leadership organization dedicated to helping manufacturing companies transition to the digital model of manufacturing by focusing on the technological, organizational, and leadership dimensions of change.
Two long-serving board members have assumed new leadership roles. Dan Dwight has been elected as the MLC Board of Governors Chair. Dwight is President and CEO of Cooley Group and a member of the NAM Executive Committee and Board of Directors. Meanwhile, the new Vice Chair is Ron Castro, Vice President and Chief Supply Chain Officer at IBM Corporation.
Joining as new members of the Board of Governors are Dan Dralle, Executive Director US Government Affairs and Global CIP at Nexteer Automotive, and Larry Megan, Head of Digital at Baldwin Richardson Foods.
“We are very fortunate to have Dan Dralle and Larry Megan join the MLC Board of Governors,” said David R. Brousell, MLC’s Founder, Vice President and Executive Director. “Under Dan Dwight and Ron Castro’s leadership, the Board will vigorously pursue its mission of keeping MLC in the forefront of Manufacturing 4.0 leadership with renewed commitment and energy.”
As an advisory body, the MLC Board of Governors provides guidance to the MLC on its Critical Issues agenda, research studies, and its programs and services for the MLC membership.
“The MLC is leading the manufacturing digital transformation charge,” said Dan Dwight, new Chair. “The Board of Governors keeps its finger on the pulse on what’s happening in factories and connects the dots to technology partners and academia so MLC members can forge a path to a more resilient future for manufacturing.”
With these appointments, the MLC Board of Governors now consists of 18 industry thought leaders who represent the full spectrum of industries and functional roles including large global enterprises, small and medium-sized manufacturers, leading academic institutions and a full array of areas of expertise.
Board members whose terms expired or who have retired include immediate past Board Chair Mike Packer, Eric Fidoten, Brad Heath, Krishna Srinivasan, and Bart Talloen.
Crystal Ball: Business Resilience in 2030 and the Digital Dexterity Effect
Digital transformation is today’s tested and proven path to business resilience. We help manufacturers digitally transform to strengthen their resilience every day. But our era is defined less by permanence than by alacrity of adaptation. Manufacturers must already evolve their approach to business resilience to remain competitive.
Granted, the need for this evolution is neither intuitive nor obvious. And in fairness, resilient manufacturing enterprises in 2030 will look much like such enterprises do today. But the means for achieving and sustaining resilience by decade’s end will be radically different. Here’s why, and how to prepare for it.
Why business resilience will be different in 2030
Resilience describes a business’s ability to adapt to change effectively and efficiently. For many reasons, data-driven manufacturers are indeed able to adapt well. That’s why businesses that aren’t already data-driven are becoming so.
But digital transformation is a continuum. And few companies believe they have done all they need to do in their transformation. Most recognize that they are in the early or intermediate stages of digital transformation. That will change.
By 2030, businesses that lead their industry will have passed beyond the stages of digital transformation. The businesses will have entered a state of digital dexterity. In that state, business resilience manifests in sharply different ways than it does today.
How business resilience will be different in 2030
Business resilience based on digital dexterity has many facets. Among them, three stand out as being potentially unexpected. First, high-level objectives will remain vital to defining initiatives aimed at strengthening business resilience. But those objectives will not be the exclusive driver. Digitally dexterous manufacturers will employ a fluid governance model. This reflects the future reality wherein company-wide resilience initiatives will emerge from diverse organizational levels, and not always from the top.
A second difference in the way business resilience will manifest lies with the workforce. Digital dexterity means making sure that the workforce has access to, and understands how to use, your business’s data and technologies. Employees will have the information they need to understand how changing their own workflows could have wide-reaching benefits. They will be able to see ways to boost resilience from their specific position. These will be ways not obvious from a top-down view.
In fact, the top-down view will itself be different, which is the third key facet we are considering. Digital dexterity will mean that all executives – not just those in IT – feel at home with technology. In the same way that an executive today can assess how well one staff member is performing, they will be able to assess how well a technology is performing. For example, is a particular AI algorithm doing what it should, and is it enabling the desired business resilience outcomes? That level of digital literacy will be a basic requirement for leaders in digitally dexterous companies.
What you can do now to prepare for the future of business resilience
We’ve called out ways of enabling business resilience in the future that will be strikingly different. Preparing for those differences will set you on the right path. A cultural awareness and acceptance of shared responsibility for business resilience takes time to develop. But it also follows naturally as your workforce evolves on the path to digital dexterity. The key here is to ensure that everyone in your organization has the opportunity to participate in the digitization of their roles. Organizational change management will be instrumental in this workforce development.
Establishing a higher baseline of digital literacy among your leadership team takes time as well, and you’ll need to begin soon. Leaders must be able to evaluate technologies for their effectiveness as intuitively as they do employees, but that is predicated on educating and training leaders with the requisite skills. Ideally, upskilling and reskilling should always remain slightly ahead of technological change.
Business resilience in 2030 will be decentralized and deeply integrated in the manufacturing enterprises’ people, processes and technologies. It will be the inevitable outcome of your organization’s digital dexterity.
To learn more, please visit NTT DATA’s manufacturing page.
About the Author
Siva Gurupackiam is Senior Vice President of Manufacturing Industry Solutions at NTT DATA.
Digital Leadership – An Imperative for Manufacturing 4.0
Improving people-centric leadership, psychological safety and intergenerational dynamics drive digital transformation forward
Digital transformation has been around as long as I have been in the workforce. The depth, capabilities and reach of technology has vastly grown, but the reality is we have been working on digital transformation for decades, in all industries and all capabilities. Yet, with all this experience, the percentage of digital transformations that fail continues to hover at around 70%, a dismal number[1].
Today, we are bringing some of our latest technologies in IoT, big data and analytics, and artificial intelligence into the industrial space with vast opportunities in efficiencies, quality improvement and increased safety. It is an exciting time for manufacturers and the stakes are high. However, as Manufacturing 4.0 technologies offer enhanced efficiency, manufacturing leaders are faced with both new and old challenges while implementing these new systems and processes. How can we improve on that 70% failure rate? Is digital transformation different on the shopfloor? How do I get everyone on board?
A digital leadership approach is key to achieving Manufacturing 4.0. It extends beyond the processes and technology. It requires taking a people-centered approach throughout the organization, creating a culture and atmosphere that drives resilience, agility and innovation, and encouraging participation and open communication at all levels of the organization.
The events of the last few years have shown that people are critical to manufacturing operations, even in our digital future. Manufacturers who successfully achieve their adoption of Manufacturing 4.0 technologies will have done so by engaging their leaders and employees and enabling organizational participation from top to bottom. They will have employed digital leadership.
What is Digital Leadership?
At its core, digital leadership involves leading through disruption and transformation, harnessing digital technologies to achieve organizational objectives. It calls for an understanding of emerging digital technologies and the ability to guide their integration into existing processes. But underpinning this is your employee base who must adapt to the fast-paced changes driven by technology. An even more critical key to any transformation’s success, these employees must understand the inner workings of the organization. A digital leader must foster an environment that encourages participation, drives agility and resilience, and rewards innovation at all levels of the organization. It is critical this leadership approach extend beyond the executive suite and managerial roles all the way to the front-line supervisors. Digital leadership focusing on the people first is key to achieving a successful transformation.
What Skills Do Your Leaders Need?
Effective leaders in the digital age are not just those in the C-suite. They are individuals across the organization who champion innovation, collaborate across levels and functions, and prioritize continual learning. that looked at leadership styles and their success during the COVID disruption, leaders using a coaching style had teams that were more resilient, engaged and productive[2].
We will call this digital leadership, and there are a few key skill sets that make digital leaders so effective in driving transformation through a manufacturing environment.
- Communication – Many change management programs focus on outward communication, informing about and justifying change. However, a strong digital leader focuses on active listening and curiosity. Through this type of communication, issues, concerns and blockages will be found earlier and resolved sooner.
- Conflict Resolution – There will be many conflicts that arise in any digital transformation. A successful leader ensures that respect for all parties is the basis upon which any conflict is addressed and resolved. By insisting on and modeling respect first, a leader shows each person they are valued and encourages issues to be brought forward.
- Accountability – Leading by example and doing what you say builds trust. Trust is one of the hardest things to build when introducing new processes and technologies. A digital leader is aware of their words and actions and acts in a way that builds trust.
- Self-Reflection/Vulnerability – Digital leaders have learned to embrace the uncomfortable. They acknowledge their own feelings and are open to where there may be gaps in the transformation program or their own knowledge. It is very important that digital leaders do not feel like they have to be the ultimate experts. A strong digital leader conducts a consistent self-reflection on the program and progress and is open to bringing in outside experts when needed.
- Empathy – A strong leader spends time noticing the people in the organization. They look for who is speaking up and who is quiet. They engage and seek to understand both types of people. In times of disruption, your biggest distractors will not actively speak to you as the leader. It is important to engage every member of the team to bring everyone along and find issues at the place and time they arise. This need for empathy at the individual level is why digital leadership must span the organization, from executive to front-line leader. Leaders must actively involve and include team members, understanding their motivations and aligning individual strengths with organizational goals.
Why Take a People-Centered Approach?
Manufacturers do not run without people. The people in your factories and central offices deeply understand the business and will be on the front lines of adopting the digital changes. In some cases, they will be contributing to the technology itself by supplying the knowledge and input needed for AI and ML models. In all cases, the people running the manufacturing lines will have a front-row seat into the impact and success of any technology implemented. It is critical that these employees and leaders feel comfortable voicing their concerns, sharing ideas and taking calculated risks. By taking a people-centric approach to digital transformation, organizations can tap into an enormous well of knowledge, support and energy to help drive the program’s success. On the contrary, if a command-and-control approach is taken, people will distrust the transformation, issues will not be reported, and innovative ideas will be silenced.
Psychological Safety – the Key to Success
Psychological safety refers to an environment where employees feel comfortable, secure and confident in expressing their opinions, concerns, ideas, and identifying mistakes without the fear of negative consequences. Creating a culture of psychological safety is critical in a manufacturing environment where safety, quality and efficiency are paramount. Considering the added complexity of a Manufacturing 4.0 transformation, building a culture of psychological safety can be the difference between success and failure.
Creating and maintaining psychological safety in manufacturing requires proactive efforts from leadership, clear communication channels, training programs and a commitment to address issues without blame or retaliation. When psychological safety is prioritized, employees are more likely to engage in the ongoing process of identifying and mitigating risks, ultimately contributing to a safer, more efficient, and higher-quality manufacturing operation and a successful digital transformation.
Some of the key components of a psychologically safe manufacturing environment that should be employed throughout the organization:
- Open communication is modeled and fostered
- Failures and learnings from mistakes are openly discussed with no blame
- Raising concerns or issues is celebrated and retaliation is not tolerated
- New ideas are considered and encouraged
- Employees feel comfortable expressing well-being concerns with leadership or HR
Fostering a culture where individuals are encouraged to voice their opinions or concerns and learn from their mistakes is essential. It will not only improve operations during the transformation but for the long haul as well.
Navigating Intergenerational Challenges
Today’s businesses encompass a diverse range of generations, from Generation Z to boomers and much has been made about intergenerational dynamics, particularly when it comes to digital participation. You could probably fill a library with the amount of material written on how to engage each generation, what they care about and how they work. With all of this noise, there is a strong risk that we make assumptions based upon generational classification. As leaders, we must understand how to manage intergenerational dynamics effectively, but at the same time challenge stereotypes and focus on each person individually with empathy and respect.
Baby boomers or Generation X have likely grown up in more of a command-and-control leadership environment which tends to minimize psychological safety. Yet, these more experienced employees also tend to possess invaluable experience and institutional knowledge that you do not want to lose, so building trust through empathy, respect and active listening will be critical to helping this persona be an active participant in the transformation. Building an inclusive environment invites this generation to contribute their experience, transferring know-how to the digital framework and to newer employees.
Younger generations, such as millennials and Generation Z have grown up in more of an open, collaborative environment where information is democratized and individuals have more power. Open communication, active listening and authenticity will be critical for this generation.
Although different generations might have varying approaches and motivations, it is critical that leaders avoid making stereotypical assumptions. Creating an inclusive environment where everyone’s voice matters and everyone is valued will create thriving intergenerational teams
Front Line Leaders are the Key to Success
Front-line leaders (or shopfloor leaders) are normally the newest leaders, have the largest span of control, and touch the largest section of the organization. Yet, these leaders are often not considered critical to a Manufacturing 4.0 transformation. Successful digital leadership expands to all levels of the organization. Since our front-line leaders touch such a large section of the organization, their impact must be considered and encouraged. Here are some ideas:
- Educate these leaders on the transformation’s goals and be open about timelines and changes.
- Actively listen to this leadership level on a regular basis taking their input and ideas into the program. Coach them to do the same with their teams and share that feedback up the chain.
- Supply adequate leadership training and ensure their leaders are modeling those skill sets critical to driving agility, resilience and innovation.
Having all levels of the organization acknowledge front-line leaders as key to a transformation’s success will support a positive outcome.
Digital Transformation is a Team Sport
The art of digital leadership lies in striking a balance between technological innovation and people-centric leadership. But this responsibility does not sit with one person or even a few. Each layer of the organization will be critical for success in both aspects. As organizations undergo digital transformation, it will be critical to supply leaders from the executive suite to the shopfloor guidance and resources needed for success. By fostering a culture of psychological safety, valuing intergenerational perspectives, and embracing employee input and dissent, leaders will build cohesive teams that trust one another and feel a sense of belonging. This will lead to better problem-solving, greater innovation and overall productivity – all critical for thriving through disruption.
Conclusion
Digital disruption and transformation have reached the shopfloor. The combination of IoT, big data and analytics, and artificial intelligence will drive significant improvements in quality, efficiency, safety and energy use. How quickly and extensively a manufacturer can get there will affect everything from that organization’s competitiveness to regulatory compliance. This era of rapid technological advancement requires manufacturing leadership to evolve. It’s not just about knowing how to leverage the latest tools; it’s about knowing how to empower, inspire and guide teams toward a future where technology and human potential intersect seamlessly. Employing this people-centric, digital leadership approach to transformation will provide a lift and accelerant to any Manufacturing 4.0 program.
As industries continue to change, it’s these digital leaders who will navigate the complexities of digital transformation, engage their employees in embracing the change, and propel their organizations to new heights.
About the Author:
Diane Guganig, an experienced Strategic Advisor and Sales Executive at Hitachi Digital Services, began her tech obsession at age five after touring a room-sized computer. Starting as a systems engineer, she spearheaded software development initiatives, led teams, and played pivotal roles in resolving significant business challenges. Transitioning to sales allowed her to partner with and solve a wider number of challenges, including intricate cross-industry issues. Her passion for technology has evolved into a mission to enhance the human experience, leading her to partner with purpose-driven enterprises dedicated to solving real-world problems for a better future.
[1] McKinsey: https://www.mckinsey.com/capabilities/people-and-organizational-performance/our-insights/successful-transformations
[2] https://www.betterup.com/blog/coaching-during-crisis International Journal of Evidence Based Coaching and Mentoring 2022, Vol. 20(2), pp.3-19. DOI: 10.24384/ektn-xx15
The Surprising Keys to Manufacturing Digital Transformation
From IT and HR to finance and leadership, the keys to successful digital transformation lie in a cross-functional approach
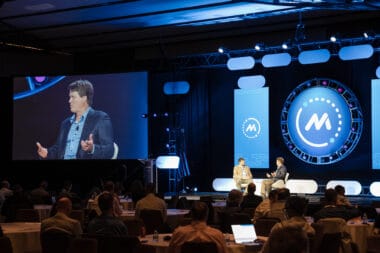
Few would argue that automation and digital transformation (DT) are not critical to the future of industrial automation. According to Gartner, 80% of manufacturing CEOs are increasing investments in digital technologies — led by artificial intelligence (AI), Internet of Things (IoT), and data and analytics — to counter economic pressures and to drive growth and profitability. Meanwhile, a 2023 MLC survey of manufacturing leaders indicates that 85% see an increase or no change to their companies’ Manufacturing 4.0 investment despite economic concerns.
And yet Gartner reports only 8% of industrial organizations say their DT initiatives are successful.
Eight percent?
It is a dismal number. Why so few?
It is tempting to pin the blame on technology snags. But technology is rarely the issue. Most organizations nowadays are engineering-led. They tend to jump on new technology right away. It’s cool and fun, and the solutions typically are readily available in the market.
Digital transformation initiatives in manufacturing fail because of organizational readiness. Or more specifically, the lack thereof.
To be clear, both organizational readiness and technical readiness are critical. But companies are generally better off when it comes to technical readiness due to the aforementioned reasons, and because they have a history of technology investments and the requisite skilled workers. With that as a backdrop, we advise industrial manufacturers to adhere to the following best practices when implementing digital transformation initiatives, with a particular emphasis on managing various organizational readiness issues, which span from the cultural to the financial.
Digital transformations should be cross-functional — but led by manufacturing operations
Digital transformation teams should be cross-functional, with representation from manufacturing, engineering, supply chain, and material operations. But cross-functional DT teams should be led by manufacturing operations. Why? Because manufacturing ops understands the floor — specifically, the problems on the floor and how to drive value.
IT is partner #1
Manufacturing operations and IT have to work hand-in-hand, with IT responsible for reliability, security and data — the latter of which is obviously the fuel for data-driven manufacturing. There are several best-practices specifically when it comes to the data.
- Data must be centralized so that the entire organization is working off of one source of truth.
- Data should be collected according to the problem you are trying to solve. Data isn’t free, so you do not need to collect it all. Start with the problem on the manufacturing floor, and let that dictate the data you collect.
- Data should be driven down to the appropriate people to make the appropriate decisions. Think through any data user — operator, team leader, quality leader, maintenance leader — and their standardized work. Then design your system to get the correct data in their hands for their jobs. (We will come back to some of the implications of getting this wrong.)
Don’t forget HR
HR support is critical in a few regards. First, HR can lead on the critical task of bridging the gap between newer, younger employees and older employees. Our workforce is transitioning and changing, and we are getting many new employees who have a great understanding of the technology and who bring new ways of thinking. At the same time, we have our older workers – I often refer to them as our “oak trees.” They really know how the floor runs and how it operates. Companies need both, and both can learn and benefit from each other.
HR’s other critical role is bringing team leaders and operators on the floor along on the journey. People will have concerns with any DT initiative. Will I get left behind? Is this going to replace me? Is Big Brother watching me? From day one, companies need to engage the floor — operators, team leaders, quality operators, maintenance operators — and make sure that they understand why the company is bringing technology in, the purpose, and how it is ultimately going to make their lives better and their jobs easier.
Be realistic about finances
Digital transformations are often under-capitalized. Ongoing costs are overlooked. Companies need to carefully account for expenses like ongoing maintenance costs, integration work, data collection and potential downtime. Many of these add-on costs aren’t properly captured in the budgeting process and later bite companies during implementation.
Leadership must protect the culture and drive decentralized data-driven decision-making
Leaders must embrace the transformation and ensure that digitization doesn’t degrade or destroy company culture.
First, leaders should never allow “data hoarding” at the top of the company, falling into the trap of thinking, Now I can solve all of these problems myself. Empower the right people with the right data to do their jobs. Problem-solving and continuous improvement should advance as long as data is being drive down to the right level of the organization.
Second, leaders must bring the operator along on the journey so they understand why the organization is making changes. This is similar to HR’s role mentioned above, but the questions that leaders answer are different. Why a wearable? How are these changes going to make me more effective and my job better? Leaders must not only manage the change — they have to inspire the workforce in the process.
Ultimately, company leaders should ask themselves, How do I make sure that we stay true to the philosophies that we learned from the Toyota Way — Kaizen and Genchi and Genbutsu … teamwork, respect and challenge? Culturally, nothing really has to change in the digitized world. The key is staying true to the philosophy of operator and team leader first, while driving data-driven decision-making throughout the organization.
About J.R. Automation
JR Automation, a Hitachi Group Company, partners with industrial manufacturers all over the world to design, build, and integrate advanced automation solutions — from assembly automation, dispensing, and vision systems to process design, controls engineering, and software integrations. We have built custom technology solutions for every application, process and industry, and helped ensure our customers were organizationally ready for the change.
About the Author:
Mike Lashbrook is Vice President Digital Solutions and Senior Vice President, M&A Connected Industry, JR Automation, a Hitachi Group Company.