AI Driven Solutions for Manufacturing Excellence
Thanks to the rising ease of adopting cutting-edge technologies like artificial intelligence, Internet of Things (IoT), big data analytics, and robotics, manufacturing is booming across the world. In the United States, for instance, a manufacturing boom has swept across the country in the last two and a half years, with the South and Mountain West having especially strong growth, according to Bureau of Labor Statistics (BLS) data1. The U.S. economy has added some 800,000 manufacturing jobs nationwide in just the last couple of years. In terms of numbers, Texas is the top state for new manufacturing jobs, with 86,000 new positions, from January 2021 to May 2023, according to BLS data. Next comes California with 79,000 jobs; Florida with 37,000; Ohio with 31,000; and Georgia with 29,000. Nevada had the greatest percentage increase at 15%, followed by Montana at 11% and Wyoming at 10%.
Manufacturing has never not been a strong suit of the U.S. In fact, the country produces 40% more factory output today versus 20 years ago, but with 5 million fewer workers, per the American Enterprise Institute2. In 2017, the U.S. produced about four times more factory output than in the 1940s with about the same number of factory workers, which is around 12.5 million! The “culprit,” if any, has been automation, including advances in technology and the rising productivity of U.S. factory workers.
New, smart manufacturing investments provide a perfect opportunity to build (back) smarter and stronger. Manufacturers now are unlocking new levels of efficiency, productivity, and competitiveness as they quickly adopt automation and digitalization. The combined power of OT and IT DataOps and domain-specialized AI and ML models is enabling manufacturers to unlock new levels of efficiency, productivity, and competitiveness. However, there are challenges to overcome on the path to realizing the full potential of smart manufacturing. In this article, and based upon the discussions we had at the recently held MLC Rethink Summit, we will explore some strategies to overcome these challenges and drive enterprise-wide transformation.
The adoption of advanced tools, solutions and processes in smart manufacturing is gaining traction across industries. It is projected that the global smart manufacturing market will grow from $297.2 billion to $787.5 billion by 2030, at a compound annual growth rate (CAGR) of 14.9% (source: Grand View Research). According to MarketsandMarkets, use of AI in the manufacturing market is projected to reach $16.7 billion, at a CAGR of 47.9% from 2022 to 2027. These figures highlight the immense business value of smart manufacturing practices.
What are some of the biggest obstacles that manufacturers face when it comes to unleashing full-scale digital transformation? Broadly speaking, they fall under the themes of legacy products and infrastructure, change and people management, and needing expertise that spans IT-OT data integration, analytical modeling and data management. Let’s take a closer look at each.
Product Legacies
One of the key challenges in scaling smart manufacturing initiatives is the complexity of integrating diverse systems and technologies. According to Deloitte, 44% of executives identified legacy systems as a barrier to implementing advanced solutions. Modern manufacturing environments are complex mixes of disconnected systems that do not communicate with each other. This lack of interoperability hampers data sharing and insights, preventing organizations from harnessing their full potential and measuring ROI. A Frost & Sullivan survey revealed that 79% of manufacturers face challenges in integrating legacy systems with new technologies. To overcome these, companies need to invest in a robust digital infrastructure that can seamlessly connect and integrate various systems.
Change Management
Change management is a critical factor that can and has sunk many smart manufacturing digital transformation projects. Years of experience working with multiple stakeholders in a manufacturing organization has revealed a near unanimous conclusion: if everyone in an organization is not onboard with clear expectations and benefits caused by the changes brought on by digital transformation, initiatives will fail.
Let’s consider change management inside the realm of dynamic scheduling. Much of industrial scheduling is reactive, where the shop floor adjusts to complete work as it comes in. Dynamic scheduling is proactive, with the schedule being adjusted to maximize production. A dynamic scheduling system adjusts production to minimize resource issues (like machine breakdown, tool failures, quality issues) or job-related (rush jobs or cancellations), and ensures optimal use of shop floor resources. Here’s an example where dynamic scheduling failed due to an overlooked human element (change management). A manufacturer had undergone a major investment in a dynamic scheduling system that failed to yield results. The change required employees who worked on a particular assembly line to swipe in to start work at their station. There were no incentives provided to workers that explained the need to swipe in because they had already swiped in for their shift at work. Since they were not on board with the value of this extra step, the system didn’t work and was abandoned.
Obstacles can abound, but a careful analysis of changes to all stakeholders can help sustain a digital transformation process.
Technologies like Predictive Maintenance (PdM) and Quality Control
Traditionally, manufacturers use reactive maintenance, fixing equipment only when it breaks down. By leveraging AI/ML-driven algorithms, including analyzing historical data, manufacturers can predict and prevent equipment failures before they occur. These algorithms can identify patterns and anomalies, enabling manufacturers to schedule maintenance proactively, optimize spare parts inventory, and minimize unplanned downtime. PdM also prevents waste by precluding the need for unnecessary maintenance.
Another key application of AI and ML is quality control. AI and ML algorithms can be trained to analyze vast amounts of data, including images, sensor readings, and production parameters, to detect defects and anomalies in real-time. By automating inspection processes, manufacturers can achieve higher accuracy and consistency while reducing the need for manual inspection. According to a study by Capgemini, AI-based quality control systems can reduce the cost of quality by up to 50% and increase productivity by up to 25%.
However, choosing the right technology partner is crucial to success. PdM and quality control are two areas where plenty of tools and providers exist, but few have found repeated and large-scale success. In reality, digital industrial transformation is a very high-touch activity: it takes much more than a software product or singular service that enables long-term, repeatable success. It takes a bridging of the IT, OT and business operations worlds with a portfolio of factory hardened industrial IoT solutions, versatile and easy-to-use software products, and professional system integration and advisory services and support.
Secure IT + OT Data Systems
As the use of IoT, analytics, digital twins and other advances facilitated by better gleaning of insights from contextualized IT and OT systems data proliferates, their impact on smart manufacturing is becoming more profound. However, continued success of AI and ML requires a wholesome approach, including investing in talent, data infrastructure, and robust OT cybersecurity. As more connected devices gather larger amounts of data, implementing robust cybersecurity measures to protect information needs to be a focus.
The risks are high. According to IBM, 61% of cybersecurity incidents at OT-connected organizations last year were in the manufacturing industry. Implementing strong cybersecurity and establishing strong governance frameworks are essential to protect sensitive data. This includes implementing strong access controls, encrypting data, updated software and firmware, and conducting rigorous vulnerability assessments. Establishing a strong governance framework to define policies and procedures for data handling, storage, and sharing is critical.
By utilizing secure AI-based edge computing and optimized multicloud adoption, manufacturers can create a unified, scalable ecosystem where data flows seamlessly and securely throughout the organization and its stakeholders.
The Experienced Leadership Difference
Since leading the Industrial IoT charge from its earliest days, the best providers in the industry, like Hitachi Vantara, have learned a few things. From hundreds of IoT projects deployed globally in manufacturing, energy and transportation sectors, they’ve witnessed that IIoT projects erase IT and OT data boundaries, and are almost always transformational, high-touch affairs. The truth is, no two customer projects are the same. Successful, scalable, repeatable, data-converged, edge-analytics-enabled delivery requires a trifecta approach – expertise and availability of three critical factors including:
- Industry-specific AI/ML-based solutions and models
- Tried-and-tested templates and accelerators that are secure and repeatable and can run where required, and
- World-class ecosystem of group companies and a strong partnership expertise to deliver it.
That is what customers need: not just tools and software, but the ability to put it all together and bring it home for their business outcomes.
Consider the use case of Logan Aluminum. Over the past six years, Hitachi Vantara has worked with their plant in Kentucky to bring the optimal benefits from insights derived from the 4M sources of data: hu(m)an, Machines, Methods, and Materials. By definition, these data sources are from IT and OT sources. IT data examples are employee information, their training details, experience and expertise levels, clearances for different areas of the factory, shift information, management information and backup personnel, PPE use depending on the day’s shift or task, etc. Material and method data sources can include tags from databases that hold information on orders, suppliers, supplier quality, stock and lot codes, shipment and inventory on hand, and more. OT sources are asset and machine data: pressure, vibrations, temperature, oil viscosity levels, date of last service, and the how/what/when/who associated with past repairs, and hundreds of others.
Working within the customer’s existing processes and with their systems, 500,000 tags/second are organized and collected and ETL’d (Extract-Transform-Load) into a data warehouse of their choice, both on-premises and in their cloud vendor’s systems. Countless possibilities of combinations on these yielded information that helped the customer improve quality, energy efficiency issues, enhance safety indices, shift from scheduled to predictive maintenance, optimize coil rolling and finished goods handling, and many more.
With hundreds of vendors and platforms and solutions around, customers need expert guidance on integrating digitized edge technology with their IT backend quickly and cost-effectively more than ever. Hitachi Vantara combines OT DataOps capabilities – knowledge and experience in managing, handling and analyzing OT data – with software products, IT best practices and consulting-through-implementation offerings that are applicable to operations, IIoT-based accelerators, data catalog and ETL/ELT platforms, and versatile reporting dashboards that are customizable for multiple persona.
Conclusions
Smart manufacturing is new manufacturing, a crucial driver of industrial success, with the global market projected to reach $787.5 billion by 2030. Overcoming integration challenges and investing in a robust digital infrastructure are essential to enable seamless connectivity and getting real-time insights. Change management is a significant hurdle in sustaining smart manufacturing practices, so organizations are addressing it by spending more time in articulating the value for all involved stakeholders earlier. Data security is a high priority, and strong cybersecurity measures and governance to protect sensitive information and build trust are essential for success and getting out of “pilot PoC purgatory”.
Customers need long-term partners that invest to understand their pain points from multiple viewpoints, offering secure, verticalized edge-to-multicloud solutions, templates and best practices to help them successfully and repeatedly achieve their high-touch digital transformation objectives.
1 https://www.axios.com/2023/03/07/us-manufacturing-growth-outpaced-world
2 https://www.aei.org/carpe-diem/the-us-produces-40-more-factory-output-today-vs-20-years-ago-with-5m-fewer-workers-technology-job-theft/#:~:text=The%20US%20Produces%2040%25%20More,Ago%20with%205M%20Fewer%20Workers.
About the Author:
Shamik Mehta is the Director of Industrial Digital Services at Hitachi Vantara with 25 years of experience in IIoT, AI/ML-based data analytics, semiconductors, renewable energy, and e-mobility. He specializes in thought leadership for technology applications in smart manufacturing, energy, and electrified transportation.
Crystal Ball: Quo vadis, Industry 4.0 and digital transformation?
In the latest in our Manufacturing in 2030 Crystal Ball series, we look at where Industry 4.0, transformation and digital value creation are headed
Global economic disruptions include supply chain bottlenecks, trade restrictions and rising prices for raw materials, all of which give manufacturers a big headache. Producers are also under increasing pressure to readjust their manufacturing footprint and reduce consumption to meet sustainability targets. Most manufacturers are still stuck with a geographic footprint set down in the 1980s, driven by ongoing labor arbitrage around the globe. Large factories are still predominant in low-cost regions like Asia, Eastern Europe, and South America. Accelerating trends toward automation, upskilling and high demand for customized products, combined with increasing regulatory requirements for sustainable manufacturing, are pressuring companies to rebalance this equation. To increase efficiency and respond to threats and trends, many producers have implemented Industry 4.0 technologies.
But quo vadis? Where are these trends going?
The Industry 4.0 vision – smart, networked factories, closer to customers
Industry 4.0 technologies offer no less than the ability to redesign the global manufacturing footprint, to position factories closer to markets, reduce logistical nightmares and increase the visibility of suppliers and customers.
The digital transformation offered by Industry 4.0 technology has four central goals:
1. Customization, insight-driven manufacturing and lot sizes of one
With customers increasingly demanding highly personalized products, mass customization has become a competitive playground. Western manufacturers need to differentiate their offering (via customization) from cheaper offshore competition to retain their markets. Industry 4.0 includes a wide range of technology innovations like 5G, artificial intelligence (AI), machine learning (ML), PLM and digital twins, MES, IoT platforms, and additive manufacturing (3D printing). These can support the agility, flexibility, and efficiency to offer customers such highly personalized products and services, thereby enhancing their brand experience, increasing loyalty, satisfaction, and ultimately, profitability.
Infor customers in manufacturing have switched from series production to highly customized operations in segments as diverse as the fabrication of individual sports rifles for biathlon athletes, medical science equipment, commercial laser pointing products, the fenestration industry (producers of windows and doors) and industrial cranes. Product individualization based on unique combinations of modular components and very late customer change requests have become essential ways to improve the customer experience. The vision is that consumers can switch their product configuration on the fly.
With an increasing shift of focus toward software-driven experience-based services, there will be pre-purchase changes for specific experiences. Today, some cars already come with three driving modes: sports, comfort and eco. In the future, cars may be chosen for events instead of a car’s lifetime – a camper van just for the summer holidays, an SUV for the winter holidays, a limousine for the business trip. All these will be equipped with event-based options, possibly an extra seat row for the children and special cooling options for the summer holidays, heated steering wheel and a snow-drive option for the winter holidays, and additional horsepower for a long-distance business trip.
2. Incremental innovation and transformation to product-as-a-service
Product lifecycles are becoming shorter as customer attachment to one-size-fits-all physical products decreases. Companies no longer compete exclusively on product features, instead offering value-added services, and manufacturers are adapting their operations to optimize business efficiency. In automotive, software-enabled service platforms are a new ground for differentiation, replacing hardware-related factors such as engine power and precision-engineered door handles. Success in this realm requires more knowledge about customers, software-based services and the ability to innovate and respond quickly to changing customer preferences.
3. Digital innovation reducing market distance
To reduce delays and transportation costs, leading manufacturers build smart factories closer to the customer. Redesigning the manufacturing footprint is especially imperative for the manufacturing industry, with its notoriously complex, fragile, and logistically challenging global operations and supply chain. New business models and technologies help reduce the distance to the end consumer. With digitalization, automation and robots, factories need fewer workers but more skilled ones. Thus, locations in Western countries become attractive despite higher labor costs.
With the digital revolution unfolding, there will be more ways to overcome global footprint constraints, such as these two concepts.
First, a widespread network of high-tech automated micro-factories. The micro-factory was invented in 1990 by the Mechanical Engineering Laboratory of Japan, referring to cell-based manufacturing in a multitude of small and highly automated plants, to deliver customizable designs locally. But it has not yet become widespread. Today, we observe much interest, but few operational implementations of micro-factories. Despite the appeal of quick deployment, higher flexibility, lower capital investment, and reduced environmental impact, the implementation of micro-factories is limited to start-ups and new business models. Even the discussion about micro-factories has quieted down. The assembly line still plays a major role, and the efficiency of a modern automated volume production site with just-in-sequence operations are hard to beat with a more distributed approach to production. Gartner® places Mobile Factories just before reaching the tipping point of “Peak of Inflated Expectations” on the just released Hype Cycle™ for Advanced Technologies for Manufacturers, 2023 and classifies them as: “5-10 years to mainstream adoption.”1
So, the micro-factory concept could become a strong factor to increase the value of customization and higher flexibility, fueled by zero distance and innovation in computing, robotics and AI. But it is not yet a top priority for operational executives.
Second, a relocation to high-cost countries for access to resources and customers. In contrast to the slow development of micro-factories, a counter-trend of companies setting up rather large factories in Western countries is burgeoning. First, there is a plethora of gigafactories. Introduced by Elon Musk, the term refers to giant plants to produce power units generating gigawatts of power via EV batteries. Gigafactories are set up in places like Canada, Austria, the United States, and Norway, by companies including Volkswagen, Northvolt, Miba and Frey. In addition, Infineon and Intel launched large factories in Austria and Germany to produce their core microchips, while Rheinmetall created a factory for producing electronic components for the F-35 fighter plane. This trend is driven by access to excellent logistics and highly qualified resources rather than by cheap labor.
4. Agility to deliver business and technology requirements
An effective platform enabling swift reaction to change, adjustment of the global footprint and further efficiencies via automation requires a comprehensive digital transformation. But for many organizations, challenges to connect separate technologies, true digitalization of processes and the complexity of existing systems continue to be roadblocks to executing a digital vision.
McKinsey has outlined critical success factors, including these four:
– A truly scalable operating model
– Distributed technology allowing local and independent innovation
– Access to reliable and current data when needed
– Strong adoption and change management
Cloud ERP at the core of Industry 4.0
Historically, manufacturers have architected their organizations and IT portfolios with a traditional monolithic enterprise-centric and on-premises ERP. But this inside-out model, with static, scheduled interfaces to the “outside world,” is unfit for tomorrow’s intelligent factories in response to an even more dynamic, constantly changing and truly real-time business environment. Legacy ERP systems focus on structured data from ERP transactions, not unstructured data that has become business relevant (e.g., IoT, clickstream, social media). This siloed, intra-organizational and structured-data focus does not provide the agility to adapt to and get ahead of current and anticipated business conditions.
The demands of the modern economy and the forces discussed above have led to replacement of monolithic ERP with a more modular, standardized cloud-based “hub and spoke” network approach, which can adapt and scale in line with business priorities. The capabilities to integrate, manage data, secure data and applications, and identify and provide optimal user experience have become the focus of overall enterprise strategy. The modular ERP approach is built around a core, vertical-specific ERP solution as a strategic integration platform to connect to supplemental applications, potentially from multiple vendors. This core ERP becomes the foundational platform for agility and innovation at scale. Additionally, embedded and advanced capabilities enable more intelligent automation by leveraging AI- and ML-driven insights and actions to improve the manufacturing process.
Digital cloud platform impact on time-to-value
The Infor digital ERP platform is designed to shorten time-to-value and improve customer experience to ensure success and improved business outcomes.
It is an industry-specific solution with preconfigured processes built in, and incorporates learnings from the sales process into the provisioned product. This is coupled with a heavy investment in tooling and content to shorten the initial implementation effort, cost and risk, and have the catalogue of predefined industry processes to accelerate deployment. The cloud simplifies updates and eliminates the need for major upgrades and for a large technical team to implement and maintain business applications.
It is set to become the central platform for dynamically driven innovation. Every company that joins increases the industry cloud scale in sectors such as automotive, industrial manufacturing and A&D, and accelerates the need and pace for relevant industry-specific additions. In 2030, industry communities will drive standardized cloud-based functionality based on their needs for manufacturing functionality, compliance with regulation, and process optimization through deep strategic interaction to set priorities per industry. Upgrades will be deployed immediately as standard additions with transparent and global KPIs throughout their entire manufacturing footprint. Over time, there will be a rich library of relevant tested use cases for process optimization based on AI per industry, available to all participants.
And the winner is … the smart, agile factory
Success belongs to the prepared. In today’s digitally transforming and connected discrete manufacturing industry, being prepared requires a re-evaluation of traditional business processes, technology capabilities and the main traditional asset, the global manufacturing footprint. Critical across each of these dimensions is effectively connecting systems and locations in an open and standardized structure and harnessing the power of data.
Manufacturing companies started to invest in new digital technologies such as AI to improve operational efficiency in areas such as demand forecasting, fault finding in production and warehousing. But today, most organizations struggle to roll out new technologies to the global universe. Those who will seriously invest in their digital platform to build a dynamic, intelligent and connected factory network put themselves into a favorable position to deploy consistent innovation steadily, quickly and globally. This change will not happen overnight. The move toward digital workflows and transparent open standards requires the whole organization to shift. Those who commit to that journey will be able to use the digital innovation benefits immediately to their business advantage in 2030. They will gain the ability to instantly respond to market disruptions, customer requirements and regulation, and create new products and services on the fly.
In an increasingly uncertain market environment, success will reward manufacturers that most effectively align new data management skills with modern information technology platforms to render their factories truly smart and insight driven. This includes the enablement of closeness to customers and their need for experiences rather than traditional products, decision-making adapted to swift reaction to change, and real-time, dynamic, sustainable and market-relevant manufacturing.
About the Author:
Dr. Henning Dransfeld is Director Industry & Solution Strategy at Infor. He is responsible for the development and implementation of Infor’s growth strategy in the discrete manufacturing in segments including A&D and automotive manufacturing in EMEA. Dransfeld has years of experience as an industry analyst. At Information Services Group (ISG), he was responsible for manufacturing, data analytics and IoT across Europe. He also led numerous consulting projects in these and related specialties. Prior to that, Dransfeld held positions at Ovum (now Omedia), T-Systems, Forrester and Experton.
1Gartner Hype Cycle for Advanced Technologies for Manufacturers, 2023 Published 25 July 2023 – ID G00789107 By Marc Halpern, Sudip Pattanayak, Christian Hestermann, Alexander Hoeppe
GARTNER is a registered trademark and service mark of Gartner, Inc. and/or its affiliates in the U.S. and internationally and is used herein with permission. All rights reserved.
Extrapolating from the results of NTT DATA’s recent research report, Innovation Index: Shifting from Disruption to Growth, John Petrusick, Managing Director, Manufacturing — Data and Analytics Practice, offers insights into the future of data in the latest in MLC’s Manufacturing in 2030: Crystal Ball series.
Data-Driven Transformation and the Future of Human-Centric Innovation by 2030
By 2030, I envision a significant change where data flows freely from sources including the shop floor, enterprise resource planning systems and third-party external providers. Manufacturers will centralize, harmonize and analyze data to enable real-time action. This encompasses all actions, including automated actions, to maximize business efficiency. Doing so will impact aspects of the business ranging from daily production operations on the plant floor, to engaging customers in selling activities, to the development and testing of new products.
With respect to sales, products and services, manufacturers will create seamless customer experiences in which customers can purchase goods using their preferred interface. Infusing data into a design thinking-led approach will also improve overall experiences once the product is in use. From an operational data perspective, employees on the shop floor or within the business will see performance data in real time and act instantly.
Highly commoditized or repetitious manufacturing environments might function as a largely ‘headless’ or ‘dark’ operating environment. Such environments rely on processes that are highly routine, reproducible and repeatable. They will, therefore, be able to leverage physical robots in the ecosystem to take the place of today’s manual interventions. These environments will have a significant advantage in productivity and efficiency while improving safety. They may use technologies including robotic process automation for monitoring and control, generative AI for requests from outside observers, and physical robots to take actions when physical interventions are required. Nevertheless, I do not foresee a near-term scenario in which manufacturing is 100% automated with no human involvement. Through 2030 there will continue to be entire plants, production lines and core processes where the need for creativity will keep humans integral.
Empowering Manufacturing through Data-Driven Insights
Data’s role will evolve naturally, and part of the role will entail solving problems. But the primary function data will serve is to enable insights that guide the actions of individuals, software or machinery so that they deliver increasing business value.
Currently, the data sphere focuses on providing high-quality, reliable data to manufacturing business actors — humans, software, physical robots and so on. These actors need specific analytics or insights in forms such as real-time or near-real-time Key Performance Indicators from a production line on quality to make value-adding decisions. When such data indicates deteriorating quality, we may need to halt the line and perform a root cause analysis to remediate the issue to re-gain performance with thresholds.
In a preventive maintenance scenario, telemetry data from machinery might show that a machine will fail within two hours. A worker would then receive an alert prompting them to reallocate capacity from that line to others, if possible, to allow for necessary maintenance. Alternatively, in a product development scenario, we might be able to design and test a product virtually. This will help manufacturers create the right product to the correct specifications the first time around, thereby reducing time to market.
As the right analytics become available in 2030 and beyond, manufacturers will gain the real-time insights to deploy end-to-end automation using autonomous tooling. Automation may extend even to the point of delivery, potentially with no human intervention. This data-driven automation will create additional value through improved efficiency and shorter time to revenue generation.
Unlocking Future Manufacturing Success for Enhanced Plant Operations
Currently, we are observing advantages in various aspects of plant operations such as preventive maintenance and quality improvement. For example, vision robotics is already providing assessment data at all stages of manufacturing, from raw materials to finished products. Moving toward 2030, we see manufacturers that start or continue to follow data and analytics best practices gaining significant benefits. These benefits will be in part due to the advantages of an expanded role for AI and the benefits it can provide, enabled by continuously improving data quality. In combination with the Internet of Things (IoT), AI will have the potential to help manufacturers build factories that are more agile, transform their workforce, make significant progress against sustainability objectives, improve security and compliance, and more. Again, this is contingent on establishing the right data standards and practices.
Building Technology Ecosystems that Unleash Data’s Power
Realizing the potential of data as we are discussing it here will not require any singular technology, but rather an ecosystem of solutions working in concert.
Even today, when we consider the data stack, we emphasize cloud-native data solutions that shift away from monolithic platforms towards an ecosystem of best-in-breed, loosely coupled and high-use technologies and tools.
Data in 2030 will similarly require an array of elements. These range from IoT sensors on machines — many of our clients already have such systems in place or are testing them — to the ability to centralize this data and provide global visibility to it. To cite just one example, manufacturers will increasingly implement machine vision, which involves converting video into data for analysis across a wide variety of use cases from quality inspection to safety compliance.
Finding Future Success by Navigating Data’s Complexities to Overcoming Storage, Reliability, and Analytics Challenges
Data storage and reliability challenges I alluded earlier to the need for data centralization. Many of our clients have already conducted pilot projects or have implemented some of the technologies previously discussed in various plants. But most have yet to successfully centralize their data for global visibility. At the heart of this issue will be the need for investment as, historically speaking, manufacturers have not made the significant investments in their data ecosystem needed to resolve this key dependency.
On the flip side, despite the importance of data centralization, there are cases where manufacturers will need to balance their need for centralization versus a need for rapid analysis and action. In such cases, the challenge will be how to embed intelligence into a local system and thereby enable machine-learning-based decision-making at the edge.
Both challenges will be pervasive. Consider a global manufacturer or a multi-site operator aiming to achieve visibility across all their operations. They may have plants that are almost entirely automated with minimal human intervention and others that have a larger human presence. Both environments present the need for clear visibility into each plant’s operations via data, so the different plants might all require a sort of “control room” view. The first step to enabling that view is to store the data on which to base the view. The data may reside in a centralized location or at defined edge locations.
The next step is to ensure the data’s reliability, whether the data is in storage or in transit. This phase involves a data management component that underpins everything before proceeding to the analytical stage.
Data analytics challenges
After overcoming data storage and reliability challenges, manufacturers can shift to the challenge of data analytics. For most manufacturers, the data management in place today is not at a level where they can trust the data without question.
At the same time, there are potential solutions to these challenges from which two separate elements come to mind. First, from a data management perspective, manufacturers could use machine learning algorithms to conduct quality checks and make recommendations on how to master the data. This process is crucial to effective analytics.
The second element pertains to both the techniques of analysis and the human factor involved. Often, achieving success with analytics depends on clearly defining the question we are trying to answer and the action we aim to take. When discussing data and analytics, our shop floor personnel may say they lack the needed technical knowledge. But the reality is, they do not need to understand all the complexities of data. Instead, as data professionals or leaders, we should focus on the actions they take and the decisions they must make in their roles, and develop analytics capabilities accordingly.
Traditional data analytics versus decision-based analytics
Anticipating the evolved and central role the workforce will play in manufacturing in 2030, decision-driven analytics is about determining the necessary actions the workforce must take to create value in a business. First, we need to ask the right questions to guide these actions. We then identify metrics or measures to establish decision points and gauge results. Lastly, we must determine the type of data needed to create those metrics and measures.
The decision-driven approach to analytics can be simplified to four elements: actions, questions, metrics and data. The goal is to understand the actions that create value in a business, then enable these with data strategies and analytics that also yield value.
Fostering Data Literacy and Collaboration to Bridge the Gap Between IT and Business for Action-Oriented Analytics
From a technologist’s perspective, it is essential to understand what is happening in the business and what actions or decisions we are informing or enabling with the technologies we are deploying. As such, IT organizations must enhance their engagement with the business. Simultaneously, business actors might need to upskill their data comprehension.
This does not mean that all business actors must learn to write SQL queries and Python scripts or be up to speed on the latest data science modeling techniques. Rather, it means they must have the requisite level of data literacy to understand the actions they take in their business and how data could help them make better decisions. Approaching it from this angle will help manufacturers find success, in part because business teams and IT organizations are thinking similarly and working towards achieving specific business outcomes.
Infographic. Aspirent, an NTT DATA Company.
To bridge the gap between IT and business teams, we have found success using a structured Decision Architecture framework focused on the following critical topics:
- What actions do we have at our disposal to drive value for the business?
- What questions do we need to answer in order to decide which actions to take?
- What metrics will help us answer those questions?
- What data do we need to construct those metrics?
This decision-driven framework offers manufacturers a more targeted, action-oriented approach to data and analytics that enables the creation of specific business cases and a clear path to unlocking their data’s potential.
Empowering Manufacturing Excellence by Navigating Data-Driven Insights for Collaborative Success and Outcomes
Ultimately, data analysis and subsequent actions depend on the workforce. It is essential to ensure that we provide data in a format that the workforce can use effectively. Similarly, the speed and effectiveness with which currently top-of-mind technologies can grow is constrained by the need for data that is accurate, complete, reliable, relevant and timely. Data and analytics reside at the core of high-value business outcomes — whether driven by the workforce, AI or combinations thereof. Potential outcomes range from creating more resilient supply chains to accelerating innovation and delivering new services to engaging customers in new ways.
In short, although we have covered a lot of ground here, my single most important piece of advice is to create and maintain a focus on driving collaboration at the intersection of IT and business teams with a focus on the business context and outcomes of data usage. By doing so, manufacturers will be able to increase the business value that data solutions create and avoid complications preventing the realization of that value.
If this data discussion has sparked your interest, we invite you to check out our infographic “Innovate Confidently with Data-Driven Decisions.” It features relevant data from the 2023 NTT DATA Innovation Index.
About the Author
John Petrusick is a Data and Analytics Managing Director at NTT DATA, serving as the Manufacturing Industry Lead. In his role he advises manufacturers on how best to leverage their data to create business value-driven, actionable, and analytic insights to increase efficiency, sustainability, and competitiveness. He is passionate about helping clients solve their data challenges, specifically in data governance, architecture, engineering and integration, advanced analytics and business intelligence, and intelligent automation, as well as helping them implement strategies to drive digital transformation.
Six Key Takeaways: Be ‘Predictive’ to Be ‘Preventive’
A recent MLC Master Class focused on how manufacturers are using condition monitoring and predictive maintenance to avoid downtime, maximize productivity, and enhance operational efficiency. Micah Statler, Director of Industrial Technologies at Advanced Technology Services (ATS) shared his experiences and expertise in an engaging conversation with MLC’s Senior Content Director, Penelope Brown.
Here are six key takeaways from their discussion:
1. Transforming data charts into prescriptive actions
According to Statler, no matter how mature a maintenance organization is, any change is difficult and change management techniques are important because there are outside influences and new tools involved. But transforming data from a squiggly line on a chart into action is paramount.
“The biggest challenge facing any manufacturers out there today is not necessarily the collection of data, but the interpretation of that data to gain a level of insight that allows them to be successful in taking action and recognizing a return,” Statler said.
Figure 1 – maintenance maturity levels
He identified four maturity levels for overall equipment effectiveness (OEE) and uptime reliability: reactive, preventative, predictive, and precision. To find where an organization falls on this maintenance maturity scale, Statler provided a few assessment questions:
- Are you planning your work?
- Are you able to put a plan forward and able to execute that without a lot of schedule breakers?
- Are you able hit your production targets?
2. Eating the condition monitoring elephant one bite at a time
For companies looking to implement best practices for condition monitoring, don’t try to boil the ocean. Instead look to where you’re seeing the most impactful downtime and eat the elephant one bite at a time. Some areas to look at first include where you are spending the most on MRO parts and repairs, what problems cause your most expensive maintenance labor, and what assets experience issues regularly.
Statler also recommended avoiding a single firefighter to look at these issues.
“We have an opportunity to do it in a much more efficient way, and also in a way that doesn’t mean it is an individual contributor, and therefore your progress – if you’re not dependent on an individual – can’t backslide from it. It’s more ingrained in your culture and it just becomes how you do business,” he said.
3. Combatting alert fatigue with collaboration
“Cross-functional teams are critical. It’s not just about the data collection,” Statler said. “We have to do something with that data, and we have to really align on what the ultimate outcome is.”
Further, to avoid what Statler called “alert fatigue,” there must be trust and the right level of communication between the factory floor and those asking them to take an action from the data. Change management comes into play here, and the collaborative team – including data scientists, developers, technology departments and the maintenance team – needs to be realistic about how mature a company’s maintenance program is.
4. The beautiful circle: AI and data analytics
Analytics and statistical process control has been around for a long time, but newer technologies like artificial intelligence (AI) help manufacturers see broader trends and take findings from one measure to another.
To illustrate this, Statler mentioned the core four traditional predictive maintenance analysis: oil, vibration, ultrasonic, and thermographic.
“What we’re able to do with the tools that we have today is, say there’s something else that I want to measure, we can apply a lot of the same models to that,” he said. “We’re getting a lot better at being able to not only say there’s a problem, there’s a change in that trend, but being able to predict what is the remaining useful life of that component that’s being monitored.”
“Ultimately,” he said, “we don’t want to get to a position where, when we notice a change in trend, we make a component change. We want to be at a point where we’re able to make minor but precision adjustments to anything that’s being measured.”
This is where AI and advanced analytics come into play.
“The better we can deliver the service, the better we can train the model, the better we can deliver the service. It’s a beautiful circle,” Statler concluded.
5. Avoiding “service on a stick” partners
For those looking to partner with a technology provider to achieve better predictive maintenance, it’s as important to look at what a company does now as it is to look at the company’s vision for the future.
“You want to pick a partner that is going to grow long-term with you and be able to work within the platforms and the tools and the data sets that you have today and in the future,” said Statler.
He also recommended looking at the service offering, itself: is it an end-to-end solution that not only collects the data and monitors the equipment but also helps you interpret the data in real time?
Statler cautioned against providers who offer one-size-fits-all solutions, and likened them to getting a plain corn dog at the fair.
“There are an infinite number of options out there for you to buy hardware, tons of platforms available, and a lot of them have coupled those together,” he said. “Internally, we call that ‘service on a stick.’”
6. A fully digital future for condition monitoring and predictive maintenance
Condition monitoring and predictive maintenance are primed for a future full of innovation.
“The technology will be accelerating so quickly and be so ingrained that we’re not even going to notice that the industry has transformed. It will be fully digital,” he said.
In fact, he pointed to technologies that we’re already seeing today. In particular, smart hands or augmented reality tools will transform the business, and people will view dashboards through heads-up displays in proximity of specific assets.
Beyond the technology itself, Statler expects to see a shift in the technical capabilities of on-site staff as well.
“There’s going to be a real integration of vendors with technology vendors and equipment vendors being able to, real-time, see what maintenance technicians see – and that’s where the smart hands come into play,” Statler said.
MLC members may access the full recording under Master Class in the Resource Center of the Member Dashboard.
More information about the Master Class Series is available online.
Crystal Ball: A Futuristic Workforce Odyssey
For humans and machines to work together by 2030, the workforce evolution must start now
Extrapolating from the results of NTT DATA’s recent research report, Innovation Index: Shifting from Disruption to Growth, Kim Curley, NTT DATA’s Digital Evolution Leader and Vice President of People & Organization, shares her insights about the future of the manufacturing workforce in the first of our Manufacturing in 2030: Crystal Ball series.
Picture this: the year is 2030. Across the U.S., the manufacturing workforce has evolved into a symphony of humans and machines working in harmony. This dramatic transformation has made the workforce a technology-enabled powerhouse. Artificial intelligence, robotics, and virtual reality lead the charge, transforming the factory floor into a buzzing and orchestrated hub of activity.
Workers use advanced technologies to perform their tasks more efficiently and safely, collaborating seamlessly with their robotic counterparts. The shop floor thrums with the smooth whirr of precise machinery and the hum of advanced systems. Augmented reality displays guide workers through complex tasks. And to make this possible, the workforce has become a melting pot of diverse talents and skills that is continuously learning and developing
It is a rosy view of the future, but realistic based on current data and trends that illuminate a path to this future state.
Changing Skillsets for 2030
The 2030 manufacturing workforce will be doing things quite differently than they do today. Four in 10 manufacturers have already begun leveraging augmented or virtual reality devices, and that will only increase. That usage will expand to support workforce instruction and training. One example of this could be teaching workers to switch over a production line. Providing that training in a virtual reality environment would mean the company doesn’t need to shut down real-world production.
As the usage of advanced technologies rapidly expands, the skillsets of the manufacturing workforce must expand, too. In addition to physical technical skills, workers will need to strengthen their understanding of technologies as well as problem solving, critical thinking and leadership skills. To build that workforce over time, you must start by expanding the skillsets of managers and leaders now. Starting today is critical to being successful in 2030, indeed, 39% of manufacturers report that they have already increased their investment in leadership development.
A More Resilient Enterprise
The evolved workforce will enable significant benefits. The big one is resilience. An augmented workforce better enables the company to respond to changes in the marketplace. With such a workforce, companies can train faster, reset the lines, and change worker skillsets more rapidly. Paving the way for this evolution, upskilling and reskilling programs for new and/or existing workers are underway today at 54% of manufacturers. More broadly, making your workforce future-ready entails steps such as improving safety, productivity and talent; incentivizing workforce agility; teaching new leadership skills; engaging the workforce; and maintaining a future-focused mindset. We’ll look at each in turn.
Improving Safety, Productivity, and Talent
The NTT DATA 2023 Innovation Index survey showed that businesses are increasingly addressing potential disruptions in strategic plans because these events present opportunities for those businesses that can act with resilience and speed.
So, it is not surprising that manufacturers are placing increased importance on their workforce and the workforce’s ability to adapt and move quickly. The more connected and engaged the workforce is, the better it can shift and flex when the unexpected happens.
Three vital areas come immediately to mind when considering how these coming changes address the problems facing today’s manufacturing industry. The first is safety. As noted earlier, one of the best commercial applications of virtual technologies is training. Training workers to complete physically demanding or potentially hazardous tasks in a completely safe environment — without the cost of physically constructing such simulated environments — is a game changer. Fully 77% of manufacturers report plans to use these technologies within the next two years. That’s well ahead of the cross-industry average of 64%. Using these tools for ongoing training programs helps ensure that workers know exactly what they need to do and how to do it. And it does that while protecting their safety and the safety of the products they manufacture.
A second area of lift is in productivity — specifically, decreasing production errors and downtime. The proliferation of sensors enabled by 5G, advanced computing and machine learning technologies gives us better insights than ever before. These insights enable us to better plan and use scarce resources, another game changer.
The third area is talent. Emerging technologies in the factory call for a new-collar workforce that understands both manufacturing and Manufacturing 4.0. As the industry increases its use of and innovation with advanced technologies, more visionaries will be attracted to manufacturing. At the same time, advocacy initiatives like the Manufacturing Institute’s Creators Wanted program help spread information about this shift in manufacturing work so the next generation of young talent is aware of these opportunities to work with technology. This shift in the reputation of the industry overall can help bring the best and the brightest talent into manufacturing. The workforce will transform from the outside in as it changes from the inside as well.
Incentivizing Workforce Agility
For people and technology to align more closely, it will be important that the workforce sees the benefits of change. Many additional technologies come into play with a technology-enabled workforce. Remote collaboration tools and digital twins can allow manufacturers to assess and optimize processes virtually. These tools may require their users to have specific skills, such as a familiarity with the way data is used to create digital twins, to realize their full value. An agile and augmented workforce will be prepared with those skills or will be readily able to develop them.
The heightened importance of the workforce will call for momentous changes. Historically, manufacturing has considered the human as a component of the manufacturing line. The concept of human capital itself came from the manufacturing industry. Shifting our thinking changes how we develop people and give them desirable career progressions. It also impacts how we pay and incentivize people.
Adopting practices for compensation, rewards, and training from other industries to attract and keep the best and brightest can be beneficial. In high tech, for example, companies such as Google, Apple, and Facebook prioritize employee development and learning opportunities. They offer training programs, mentorships, and career advancement pathways. Some 84% of manufacturers have at least piloted investments in training for employees in areas such as factoring customer behavior into decision-making. To date, though, just three in 10 manufacturers report adjusting total rewards packages to increase their competitiveness when searching for new talent or retaining existing workers.
New Leadership Skills
The path to a future-ready workforce will include overcoming hurdles. One of the biggest is the need for a radically new style of leadership. Leaders in-house today often have massive institutional knowledge and a long history of viewing the workforce in a particular way. Having such leadership has often led to success. But going forward, that will need to change. That is a challenge. You have to teach the most senior leaders to see the workforce — both its potential and its needs—differently. But even incremental change comes slowly. Presently, for example, only 13% of manufacturers report being highly effective at delivering on worker-centric policies such as flexible working options and schedules.
Certainly, you cannot change a whole company’s culture unless you’re working from the top down as well as the bottom up. But once you do, you are positioned to develop and sustain a culture of innovation, experimentation, and resilience.
Engaging the Workforce
The workforce can and should be an active part of its own evolution. First, engage with your workforce – truly engage. Understand who your people are and what is important to them. Find ways to connect them to your company’s purpose and the impact you want to have on the world around you. The stronger those connections are, the more powerful a force your workforce can be in driving the transformation you’ll need over the coming years.
Second, expose more of the workforce to technologies and how these tools can help them and the business. Manufacturers are slightly behind the cross-industry average at the use of updated tools and technologies, with only 29% considering it important to employee satisfaction and engagement. Our Innovation Index shows that the best ideas to advance the business most often come from the individuals who already know the most — your workforce.
A Future-Focused Mindset
Mindset is everything. Without a growth mindset at every level of your organization, you will struggle to accomplish a transformation that will drive success between now and 2030. This mindset must be pervasive, encompassing everything from policies to hiring practices, investment decisions and the employee value proposition you put into the marketplace. When you embrace a mindset that says we are going to try new things and grow, and your workforce embodies it every day, you will create a resilient organization that is comfortable pushing boundaries to create the future.
About the author
Kim Curley is Digital Evolution Leader and Vice President of People & Organization at NTT DATA.
Hannover Fair 2023: It’s Not Technology Anymore. It’s All About Data, Data, Data.
Whatever advanced technologies manufacturers adopt, future transformational success will ultimately depend on data, from powering the latest digital tools to deliver more value, to creating entirely new industry-wide data ecosystems, to the foundation of enticing new Industrial Metaverse applications for the future, reveals this year’s Hannover Fair in Germany.
Emerging from three years of COVID disruption, the world’s largest industrial fair in Hannover, Germany, began to bounce back this year with a renewed sense of optimism about the future of digitally enabled manufacturing, hosting more than 4,000 exhibitors from 62 countries showcasing their latest innovations, and over 130,000 visitors from around the world.
Many of the impressive and varied transformational solutions on display, however, also revealed a fundamental change of emphasis from years gone by. This year, Hannover was a lot less about promoting individual products and technologies, and much more about the underlying power of data to fuel those advanced digital tools in order to drive greater efficiencies, resiliency, value, and sustainability, for both internal operations and entire manufacturing value chains.
“Without data, we will never take manufacturing to the next level and scale,” declared Rainer Brehm, CEO of Factory Automation at Siemens, launching the company’s new Industrial Operations X approach, which is based on the three pillars of software-defined automation, data-driven production, and access to an open, industry-wide data ecosystem.
Manufacturing X
The use of the letter X in the Siemens’ nomenclature is highly significant. It echoes a new and rapidly emerging industrial data sharing initiative in Europe called “Manufacturing X”, an approach showcased by multiple companies throughout the 17 busy exhibition halls at this year’s event.
Manufacturing X aims to create a safe and agile next generation data infrastructure for manufacturing industry players to network, share, and exchange key product and other information with approved partners and customers in a compliant, standardized way, solving many of the current issues companies face in creating end-to-end real-time visibility across supply chains and making it easier for manufacturers to drive and scale transformational change.
The concept envisages a federated cloud-based “data space” where companies can upload dedicated “data containers” housing fully detailed, standardized information on any manufactured product or service, whether that is a factory machine tool or a wind turbine. Each data container can include key information ranging from authenticated product documentation (sometimes known as a Product Passport) to full maintenance and service manuals, compliance details, lifecycle frameworks, performance data, CAD files, ready-made digital twins, and even details of the carbon footprint of each unit or component.
In the same way that standardized freight containers revolutionized the freight transport industry, explained the team at German automation company Phoenix Connect, Manufacturing X aims to create an industry-wide data ecosystem where standardized containers of data can be easily accessed and securely shared across qualified partners and customers within a manufacturing value chain.
Easy access to the digital twin of each manufacturing asset, for example, can make it far simpler for companies to build plant-wide virtual digital twins, or train service engineers to troubleshoot equipment issues, and detailed production specifications can be instantly shared with key manufacturing partners to help cut time to market for new products or mitigate sudden supply chain disruptions.
Based on open standards and interoperability, Manufacturing X also aims to break industry dependency on today’s proprietary systems and networks by building an open and trusted framework that allows all industrial companies, automation providers and manufacturing customers alike greater control and sovereignty over their data in the future.
Many examples of this new X data space concept were already in action at the Fair, including the advanced Production Level 4 ecosystem created by German research group SmartFactory KL, in which a rapidly reconfigurable, modular, shared production line harnesses interconnected machines and technologies from multiple suppliers, combining advanced digital process tools, AI, collaborative robotics, its own implementation of the data space concept called SmartMA-X, and the Asset Administration Shell (AAS) specification, which creates detailed standardized descriptions of each individual asset.
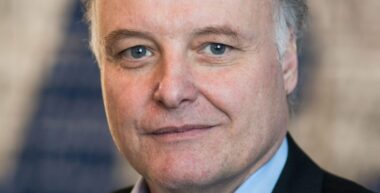
“Manufacturing X represents the next stage of Industry 4.0,” Dr. Gunther Kegel, President of the German Electronics and Digital Industry Association, ZVEI, told German Chancellor Olaf Scholz and the packed audience of senior industry leaders and dignitaries at the Hannover Fair’s high-profile Opening Ceremony on the eve of this year’s Fair. Manufacturing X, he continued, is an important element in the creation of a safe and secure industrial data economy of the future that fosters increased networking, resiliency, sustainability, and climate protection among all industry players.
Foundations of a Future Data Economy
Manufacturing X is only one implementation of a much broader data ecosystem concept called Gaia-X, initially conceived as a European initiative in 2019 but now with evolving global ambitions.
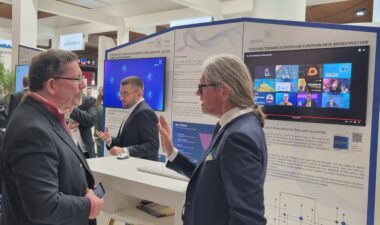
Gaia-X aims to build the foundation of a future data economy across multiple industry sectors based on the same idea of a shared and secure data ecosystem, explained Gaia-X CEO Francesco Bonfiglio, in an interview with MLC.
Other implementations include Catena-X, designed to support auto industry companies to share data on products and parts across their value chains. It has already attracted many leading auto industry partners, including BMW, Mercedes Benz, Volkswagen, Ford, Volvo, Renault, and tire maker Continental, plus technology innovators including Microsoft, IBM, SAP, Siemens, Fujitsu, Hewlett Packard, and many more. A health industry X-version for the pharmaceutical and medical devices sector is also preparing to launch in the near future, with future plans for similar data ecosystems covering other sectors including aerospace, agriculture, energy, logistics, and more.
Ecosystem Challenges
Such next generation industrial data ecosystem initiatives are both innovative and ambitious, but they are still in their early stages and there are many challenges yet to be overcome, from political infighting among European members, to the practicalities of sector-wide implementation.
In a panel discussion entitled “Towards a Federated Industry Data Ecosystem”, representatives from the Industrial Digital Twin Association (IDTA), Gaia-X, BMW, and German automation company Festo were candid about a host of challenges ahead for companies, as well as the industry as a whole, in building data ecosystems.
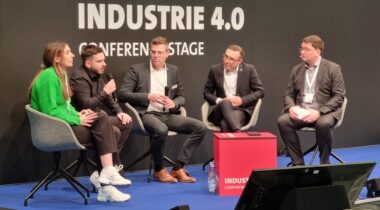
Chief among the challenges the group identified were establishing trust among participants; assembling a critical mass of participants to make an ecosystem work properly; understanding and adopting a common legal framework to enable intellectual property protection, an important foundational element of trust; and dealing with the technological complexities of such elements as data spaces and data containers.
But perhaps the most significant challenge voiced by the panel was bringing along small and medium size manufacturers, a group that often doesn’t have the focus, expertise, and financial wherewithal to undertake what by any measure will be a significant effort to adopt and operate data ecosystems.
To help bring the small manufacturers along, the panel recommended the development of technology tool kits to simplify the development of new business models based on the data ecosystem idea. One such example already exists within the Catena-X group.
The other emerging consideration for any manufacturers adopting the data ecosystem idea is how it will affect their competitive profile as well as the competitive landscape of the markets in which they do business. Will participation in such ecosystems, should they take hold in a substantial way, become essentially a requirement in order to remain competitive? By establishing a common data playing field, will manufacturers then be able to compete on higher level factors such as more targeted products and services?
And what of potential legal issues? Will such data ecosystems be viewed in some countries in an antitrust light, prompting challenges by non-participants and government bodies? There will clearly be more developments to come in the months ahead.
Inspiring Innovations
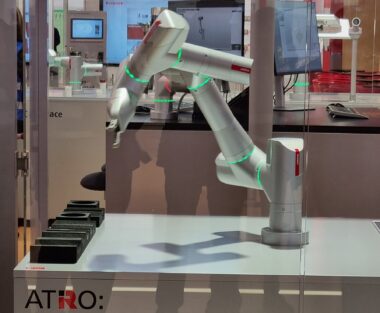
There was certainly no shortage of inspirational technologies on the stands at this year’s Hannover Fair, of course. Advanced digital twins were everywhere; AI is being embedded into almost every kind of offering; 5G is now the connecting technology of choice; and systems specifically designed to support sustainable operations – from advanced energy efficiency algorithms and on-site hydrogen production units to digital threads and twins supporting full circular economy strategies from initial product design to end of life reclamation.
AI Everywhere: Now It’s Time to Scale
The critical importance of data to drive these ever-advancing digital tools is perhaps most evident with AI systems, which were extensively showcased across the Fair this year.
While a decade of adoption of M4.0 technologies has made data better organized and more available than ever before, “An estimated 80% of data in industry remains unused,” noted Philippe Rambach, Chief AI Officer at Schneider Electric. “So, the time for AI in industry is now,” he continued, “and the next stage is to scale.”
A number of suppliers admit, of course, that overcoming the challenges of adopting and scaling AI is still a learning journey for many manufacturing companies, so products like Altair’s RapidMIner or Festo’s Automation Experience (AX) AI platform for predictive maintenance, among others, are designed to provide easier entry points for companies new to the AI arena.
Schneider Electric, meanwhile, is already applying AI in multiple ways across the company, explained Rambach, from energy optimization to driving an increasingly self-healing supply chain that supports a network of around 14,000 suppliers and 150,000 order lines a day. He identified three key areas of business focus for AI the company – to enhance customer facing services, to improve internal process efficiencies, and as an advisory tool to provide monetized consulting services in areas such as energy management and industrial automation.
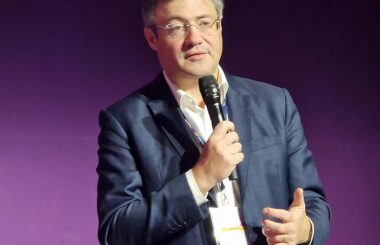
Based on his experience, Rambach advises manufacturers to approach AI adoption with three key considerations in mind. First, don’t start with AI; start with a use case that can deliver value and then ask if AI can help. Secondly, build a joint AI team made up of data specialists merged with people who have real front-line domain knowledge. In fact, Schneider’s AI team is not allowed to launch any new product in the company until it has been tested and verified by workshops of domain experts and frontline workers. Finally, to help build trust and support in AI adoption, socialize successes within the company to get all levels of employees engaged.
And to help companies ensure the AI systems they develop deliver meaningful and unbiased results, the Fraunhofer Institute was also showcasing its “Trustworthy AI” toolset on a nearby stand. This provides companies with a framework to test the quality and worthiness of their AI solutions, especially in human-dependent applications such as plant safety, medical advice, chemical processing, or even traffic management. Such formal testing and approval criteria will become increasingly essential, says Fraunhofer, with the rapid emergence of popular new generative AI tools like ChatGPT.
Omnipresent Digital Twins
While AI permeated many areas of activity, there is also little doubt that digital twins have become a primary foundational technology in driving the future of digital manufacturing across multiple application areas. Almost every digital solutions provider at the event had one or more digital twins on show, from digital versions of individual products or factory assets to full plant floor planning and monitoring systems, to end-to-end lifecycle process and circular economy applications.
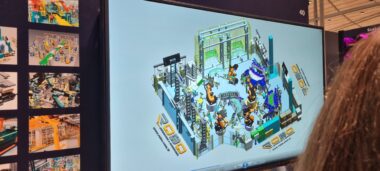
Many of those digital twin examples were built around the rapidly dominating Asset Administration Shell standard, which allows greater compatibility and interoperability between different digital twins and is backed by a collaboration between the OPC Foundation’s Open Architecture standard and the IDTA. In fact, digital twins are now so commonplace that many suppliers are proactively including digital twins of their products with every purchase so customers can more easily integrate them into their own systems for maintenance, plant floor planning, and other key use cases. These include companies like Siemens, Festo, or Harting with its product life-cycle digital twin.
The Sustainability Imperative
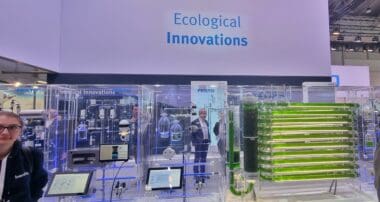
With Germany’s ambition to become the world’s first climate neutral industrial economy in the world by 2045, the presence of digitally enabled green industrial solutions was also far more in evidence than at any other previous Hannover Fair. Every company either had an explicit focus on energy reduction or showcased green energy production and infrastructure innovations – from improved plant-scale energy management applications to digitally supported processes for battery production and on-site energy storage, new low-scale green hydrogen production systems, systems for easier monitoring and reporting of Scope 3 supply chain partner emissions, and circular economy lifecycle digital twins with precise details of reclaimable content and dismantling procedures for recycling key materials and components.
One other innovative green-energy focused display was SEW Eurodrive, which has developed a family of automated guided vehicles (AGVs) that know when their power is low and can autonomously replace their own power packs with new hydrogen fuel cells as needed.
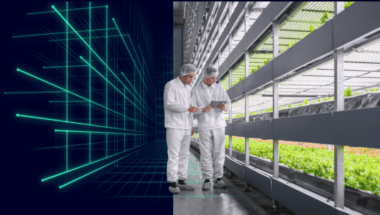
Siemens, meanwhile, showed an impressive example of how combining multiple digital technologies including AI, robotics, and visual inspection can autonomously manage vertical farms capable of delivered 300 times more fresh food yield on a comparable area of ground, using 95% less water than traditional farming methods, but without the need for any harmful pesticides or fertilizer run off.
The Dawn of an Industrial Metaverse
But perhaps the most forward-looking and engaging displays at this year’s Fair, and there were many of them, were multiple examples of emerging Industrial Metaverse applications in action. These combine multiple technologies including advanced digital twins, embedded AI, VR/AR visors, and rapid 5G communication to show how early Metaverse use cases could create collaborative virtual spaces for training, e-commerce, remote operations, factory design, product maintenance, and troubleshooting.
Once again, it is data that will drive this latest digital evolution, believes Charlie Sheridan, Technical Director of Industry Solutions/Manufacturing at Google Cloud. “Data is the foundation of the Industrial Metaverse journey”, he believes.
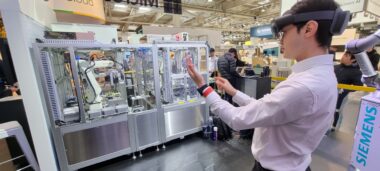
On Microsoft’s stand, for example, partner Kawasaki was using an advanced digital twin, combined with embedded AI and engineers wearing HoloLens mixed reality headsets, to show how they could work together remotely from anywhere in the world using a collaborative mixed real world/virtual environment to exchange expertise in real time to troubleshoot and fix equipment problems. “It’s the beginning of a new era,” predicts Kawasaki.
Early Industrial Metaverse applications are not all just pilots either. Real life projects are already in place at auto companies such as BMW and Renault where they are being used to create virtual factory and plant floor environments, while global chemical giant BASF is reported to have 20 Metaverse projects underway, and Norwegian battery maker Freyer is now using Siemens Metaverse technologies to help scale production capacity at both existing and new plants in rapid time to meet the predicted 700-fold increase in global demand by 2030. “We are already paving the way into the Industrial Metaverse of the future,” asserted Siemen’s Brehm.
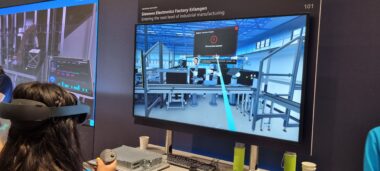
The momentum around Metaverse developments is certainly growing fast. The recently launched Metaverse Standards Forum, noted Dietmar Laß, senior researcher manager at the Fraunhofer Institute, already has over 4,000 members and is expanding fast. “We are only getting a glimpse of what may be possible now with the Industrial Metaverse, but the basics are already in place”, said Laß.
Perhaps the promise of an immersive world for future production operations, where virtual and augmented realities take digital twins and collaborative cultures to a new level, is closer than many industry leaders may think.
The Future of Data
When Stephan Weil, Minister of Lower Saxony, officially began the opening of the Fair on the Sunday evening, he hoped that the 2023 event would reveal how the power of innovation can help solve some of the world’s toughest problems, help companies balance sustainability with growth, and help foster an equitable balance between people and machines working together.
Yet, as the days went by, there was clearly more to the event than just a series of high aims this year in Hannover. There was also a fundamental sea change of emphasis across the Halls that revealed a new focus on data and perhaps a more mature ecosystem direction for future innovation and adoption to enable industrial companies to truly accelerate transformation and drive greater value.
As German industry 4.0 pioneer, founder of the German SmartFactoryKL research initiative, and former MLC Board member Detlef Zülkhe reflected: “Hannover is not about technology anymore. Today, it’s all about data, data, data.”
About the authors
Paul Tate is Co-Founding Executive Editor and Senior Content Director at the NAM’s Manufacturing Leadership Council.
David R. Brousell is Co-Founder, Vice President, and Executive Director at the NAM’s Manufacturing Leadership Council.
Davos 2023: Takeaways for Manufacturing
A personal perspective by Augury CEO Saar Yoskovitz on his most important takeaways for manufacturers from the World Economic Forum’s annual meeting in Davos last month.
This year’s World Economic Forum’s (WEF) Annual Meeting at the Swiss resort of Davos was both intense and inspiring. Among the many attendees, world leaders in government, business, and social institutions were present. Speaking to them and hearing their thoughts is a unique opportunity as those conversations can shed light on global problems and innovative solutions. And since the previous WEF Annual Meeting last May, the mood has shifted.
Last year, during Davos 2022, the world was in the midst of a recession, the Russia-Ukraine War had just started, supply chains were at risk, and “de-globalization” was one of the most used words at the event. Any discussion about the environment or financial support for sustainability seemed hollow in those conditions.
This year, things appear to be considerably more stable: Ukraine is holding up, the energy crisis has been avoided in most countries, the world’s inflation appears to be under control, and supply networks are expanding. All these together made it possible to have a far more fruitful discussion on how to address the main problems manufacturers are currently facing.
In It Together
The first key takeaway was that manufacturers are increasingly coming together as the challenges smaller and mid-size companies are experiencing look very similar to those that some of the world’s largest companies are battling with at the moment. Everyone is looking for signs of economic certainty over the next couple of years. Leaders of all types of companies are trying to balance the need for expansion with wise resource management.
Simultaneously, global issues such as sustainability, workforce change, efficiency, and the effectiveness of a global industrial and manufacturing base are all being considered seriously by manufacturers big and small, with workforce and skills-related topics being top of mind. Businesses of all sizes now understand that progress and growth still depend on the fundamentals: people coming together to work out the details, agree on a course of action, and put in a genuine effort to bring about change.
Technology’s Coming of Age
Each annual meeting brings a rush of studies on a range of topics. This year these included how the circular transformation of industries is unlocking new value, how over a hundred WEF Lighthouse Factories are showing the way forward to a more sustainable future, and how various industrial clusters are using technology to move towards Net Zero. What’s good about these reports is how they’re starting to focus more on what’s actually happening, rather than what should be done.
The next stage of this involves scaling those world-leading Lighthouses, highlighting the unique cases of transformational success that shine brightly across manufacturing. In many ways, this represents the next step in building a global society in which the combined efforts of humans and machines improve the quality of life in all respects.
Enter Glocalization and Friendshoring
While “de-globalization” was last year’s big word, in 2023 it was replaced by “glocalization”. This captures the idea that while our supply chains are becoming more localized, they still need to be internationally connected. Glocalization strategies can help manufacturers become more resilient, a trend that is also happening naturally as part of the global energy transition. Alternative energy sources are typically closer to home and more difficult to move. For example, solar energy is produced during the day and wind energy during windy conditions in multiple locations but, at the moment, neither the bulk storage nor transportation methods exist for these two types of energy to be easily transferred any significant distance, which naturally leads to more decentralization. Factories will tend to be located where the cheapest and cleanest energy is available, as previously happened with data centres.
Friendshoring was another emerging term at the WEF this year. It is swiftly replacing the traditional strategy of offshoring and reflects how manufacturers are now turning towards countries that share similar values and have more compatible trading approaches. Friendshoring can also help reduce reliance on a single source. This is especially evident in the semiconductor sector where approaches like the US/EU IRA and CHIPS laws represent a significant step forward.
Circular Supply Chains
Larger organisations are also giving more sustainable and circular supply chains top priority as a result of impending regulations around carbon reporting, like Scope 3. This reporting looks at a product’s whole footprint by taking into account the upstream and downstream environmental impacts of its supply chain.
Some people have already called such developments “a nightmare.” It can definitely be hard. Many companies are doing their best to track supply chain emissions effectively, but there is a severe lack of the necessary frameworks or tools to do so. To make matters worse, Scope 3 also varies depending on the manufactured product. For example, Scope 3 only accounts for 6% of the emissions from a cement factory, but it might account for 80% of emissions in the automobile or food sectors. As a result, manufacturers need to come together as an industry to make the reductions needed to their overall carbon emissions.
Talent and Talent Again
Access to talent is still a hot topic, but with a new twist. Now, companies are shifting their focus from Labour Cost Arbitrage to Skills Arbitrage when making investments in new geographies. In other words, people are asking themselves about the locations of the best talent that can make better use of automation and digital tools to increase productivity. This shift towards skills is expanding the talent pool.
A Way Forward
In short, this year’s WEF leaves space for optimism. Manufacturers have more clarity on the challenges that lie ahead, they understand more about how to overcome them, and they have the right tools to do so. It certainly won’t be easy, but by working together, manufacturers, governments, and wider industries, have a better chance than ever to make a difference and chart a clearer path forward for the future.
Saar Yoskovitz is Co-Founder and CEO of machine health company Augury.
A Guide to Digital Transformation in Manufacturing
Digital Transformation (DX) is a broad business strategy to solve traditional business challenges and create new disruptive opportunities using digital technology – such as maximize revenue, reduce cost, improve quality, and increase flexibility. Use cases range from asset optimization to workforce productivity to industrialization.
Why Manufacturers Need Digital Transformation
To remain competitive, DX for manufacturers is a necessity. Global market intelligence firm IDC predicts that in 2025 global DX spend among manufacturing industry companies will total more than $816 billion. Forrester Consulting found that more than 90% of manufacturing leaders believe that DX is important for their success. Clearly there is a lot at stake and developing a DX strategy is critical to capturing the most value.
The range of opportunities for DX in manufacturing is both a positive and negative. On the one hand, for whatever challenges facing an organization, there is likely a solution out there to address it. But manufacturers are faced with dozens of challenges. Such initiatives are usually driven by a scattergun, technology-driven approach. Ultimately, this results in resources being misdirected and just a small set of initiatives driving true transformation. Instead, companies must employ a laser-focused approach, that emphasizes impact, speed, and scale.
Manufacturers that have successfully adopted DX strategies are more efficient than their competition. That efficiency may be generated by greater worker productivity, asset uptime, better cross-organizational collaboration, or other DX opportunities. Ultimately, regardless of how efficiency is gained, it can be leveraged to increase revenue and/or reduce costs.
Achieving Transformation with Impact, Speed, and Scale
Regardless of the many different challenges an organization faces and the many different solutions on the market, there are fundamentally four objectives for manufacturers that have not changed: maximize revenue, reduce cost, improve quality, and increase flexibility. Impact, speed, and scale are the three key success factors for delivering transformational outcomes, and each must be tied to at least one of the objectives. Here’s how:
Impact – Focus resources on the most important constraints to drive P&L. Based on the dynamics of an industry and strategic roadmap, manufacturers should determine which of the fundamental goals are most important to improve upon and which are most likely to impact these goals in order of their criticality to the business.
Speed – With impactful opportunities identified, attention should turn to speed and scale. Quick wins can make or break a good initiative by building early, positive momentum. A quick win will generate team buy-in and can be leveraged for greater executive support. This rapid time to initial value is best achieved with proven off-the-shelf solutions.
Scale – Scalability must be considered early. No initiative should take place without a comprehensive and actionable scaling plan. If a project is slow to scale it is more likely to lose support and fold. If it cannot scale, then it is not delivering transformational value. The most reliable way to build a scalable plan is to model it after approaches that have already proven to be successful. The key here is finding repeatable use cases, that check off the high impact requirement and can be deployed with off-the-shelf solutions.
Final Thoughts
A recent PTC survey found that there is a stark difference between the companies that succeed in DX and those that do not. Companies that meet ROI goals expectations beat them by an average of 50%; those that fail miss expectations by an average of 30%.
This insight underscores the requirement for strategic DX for manufacturing organizations, and the PTC Impact, Speed, and Value Framework described here creates a foundation for DX success.
Will Hastings is Director of Product Marketing, PLM for PTC.
Achieving Measurable Value through Data-Driven Manufacturing
“Data collection doesn’t equal success” and other observations from a powerful visit to EY’s Digital Operations Hub @ MxD
The Manufacturing Leadership Council recently partnered with EY for a two-day event focused on preparing for the future of manufacturing. Hosted at MxD in Chicago, Ill., the event focused on data-driven manufacturing and included a tour of EY’s Digital Operations Hub, several discussion panels and presentations, and a collaborative workshop.
Diving deep into manufacturing at EY’s Digital Operations Hub: Day one featured a round-robin visit to a selection of experience modules within the EY Digital Operations Hub. Participants had the option to visit five of the hub’s 31 modules where they heard about topics including workforce upskilling, intelligent demand forecasting and planning, digital performance management, digital worker enablement, edge computing, and more.
As participants made their way around the Digital Operations Hub, led by EY’s Mark Heidenreich, who leads the Digital Operations Hub, EY’s expert team and partners shared a deep dive into each topic, demonstrating the latest technologies and thinking on this important array of manufacturing topics.
Focusing on the future: The second day of programming kicked off with a conversation between David Brousell, MLC’s Co-Founder and Executive Director, and Scott Dixon, EY’s Managing Director – Advanced Manufacturing Technology Leader. The topic at hand was MLC’s latest white paper, The Next Phase of Digital Evolution and what it tells us about the future of manufacturing.
The two focused on data and its important role in manufacturing. While data may be difficult to get to – particularly on-demand – it is an important driver of decisions and value. However, they cautioned that data collection doesn’t equal success. Instead, Brousell and Dixon urged organizations to balance resilience while adding complexity. Brousell recommended that organizations not focus on data’s ability to “knock down silos.” That phrase, he warned, can be scary for subject matter experts. Instead, he recommended weaving silos together so that systems are integrated and domain expertise can be maintained.
Becoming data-driven: Next up, the event covered the top challenges for data-driven manufacturing with a presentation by EY’s Sachin Lulla and Amy Burke, the Americas Consulting Sector Leader – Advanced Manufacturing & Mobility and Advanced Manufacturing & Mobility Markets Leader, respectively. With a survey of 400 manufacturing companies as its basis, the presenters shared how only 10% were experimenting with digital, while only six percent were tackling digital at scale.
Throughout the conversation Lulla and Burke emphasized the need to put humans at the center of any transformation, building digitization and operational excellence around that core. For Lulla, the purpose of technology is to augment human intelligence. The pair agreed that starting with an end goal in mind is important when formulating a data strategy. The organization and employees need to know “the why” behind the data collection and use.
Further, Burke and Lulla recommended that organizations should not just look at gaps in their current workforce, but at what employee skills exist on the team and how upskilling and a learning environment can cultivate a fertile ground for data to be used successfully.
Driving digital with data: Pfizer’s Vice President of Digital Manufacturing, Mike Tomasco, was on hand to share how the pharmaceutical and biotechnology company uses data-driven decision making to create value. Tomasco shared how the company’s initial failures with capturing and using data led to significant successes and allowed Pfizer to move beyond pilot purgatory to large-scale transformation.
Moving beyond: The idea of moving beyond pilot purgatory was explored further to start the final panel discussion moderated by Brousell. Panelist Jim Fledderjohn, Dell’s Manufacturing Vertical Field Director, advised organizations to align pilots to the bigger strategic vision and fail fast. According to fellow panelist Terry Davenport, Rheem’s Executive Vice President, Global Operations, leaders should use the scientific method to learn from pilot projects and prove the value before scaling. From a collaboration standpoint, Microsoft’s Americas Regional Business Lead – Manufacturing, David Breaugh suggests that cross-functional teams help keep an eye on the big picture and unlock insights faster. Meanwhile, James Zhan, PTC’s Vice President, Market Development, IoT Solutions cautioned the audience not to focus solely on pilot purgatory and to be sure to keep an eye on workforce skills purgatory.
The panel also tackled the topic of data measurement, with Fledderjohn urging organizations to be selective about what data they collect – a proactive strategy that will help ensure the data is used and useful. Any process should have a metric that makes things faster, safer, eases worker burden, and offers higher quality and cheaper outputs, added Davenport. To that end, panelist Steve Pavlosky, GE Digital’s Vice President of Product Management, shared that GE shifted its technology roadmap to help customers move data into a single system so operators could make decisions quicker.
Capping it off with idea sharing: The event was capped off by a series of collaborative breakout sessions during which participants brainstormed go-forward ideas and feedback around the topics covered throughout the course of the entire event. Beyond the content that participants absorbed throughout the event, the breakouts gave them a chance to add their own two cents to the discussion, share their own experiences, and take away new perspectives that can be applied to their organizations.
Visit https://www.mxdusa.org/partners/ey/ to learn more.
All photos courtesy of EY.
Effective Communication – The Start-Up’s Biggest Challenge
If you were looking for a dose of optimism to counter the troubling reality of the post-pandemic world, you could do a lot worse than turn to the start-up community. Even in the best of times, the odds are stacked ruthlessly against anyone considering starting a business. And these are hardly the best of times. Yet new ideas and the magic combination of hope and conviction that supports them, continue to pour forth in a torrent. According to the U.S. Census Bureau, Americans started 4.3 million businesses in 2020, a 24% increase from 2019, and by far the biggest number in a calendar year in the previous decade and a half.
As an investor, and a mentor for Creative Destruction Labs (CDL) I meet a lot of founders, and I watch a lot of introductory pitches. And while the enthusiasm is ever-present, it is not uncommon, after the founder has left the room, for those who have just watched the pitch to turn to one another and say something like: “I still don’t know what they actually do.”
The effective communication of a new product’s value and function is, I believe, the biggest challenge facing any start-up founder. This is about knowledge transfer. It is a prerequisite of every progressive step the company hopes to take. And it is particularly difficult for companies that are bringing to market – either as a core product or as part of a wider service or solution – a complex mechanical object (CDL focuses on science and technology start-ups).
These founders have to convince investors to fund their project; they have to explain defensible intellectual property to patent attorneys and granting authorities; they have to communicate requirements to sub-component suppliers and manufacturing partners; they need to convince buyers and users that the product can deliver; they must ensure anyone responsible for maintenance and repair knows exactly what’s required to keep it operational.
That is a broad audience, each with a specific set of knowledge transfer needs. So to be effective, communication needs to be highly versatile, and to deliver absolute clarity through the most efficient processes. If this capability isn’t baked into the organization from the outset, the best case scenario is that the challenge scales as the company becomes successful, creating a much bigger problem which can have a direct impact on operational KPIs.
As products come to market they bring with them a host of documentation and content requirements associated with that knowledge transfer. Creating and maintaining this content is a huge task and one that can easily become a bottleneck. If the content isn’t ready, the product can’t be promoted or sold. If it isn’t completely accurate, if it’s hard to access, if doesn’t tell the full story, you could be looking at fabrication or maintenance errors and costly downtime.
Advances in manufacturing technology – the adoption of agile workflows and additive manufacturing – actually make things worse. These processes accelerate product development and iteration, making the documentation and content bottleneck even more damaging.
Macro realities compound the problem yet further. Once upon a time a new company would start by bringing a core team together at a new premises. However, full-time, on-site work looks like a thing of the past. Studies suggest 70% of the workforce will remain working remotely five days per month by 2025 with others opting to work part-time on-site and part-time at home. And, in any case, start-ups tend to rely on a distributed ecosystem of product and service suppliers from the outset, for obvious reasons.
And according to a 2020 McKinsey report, Unlocking growth in small and medium-size enterprises, SMEs have innate productivity challenges, exacerbated by lack of access to high-cost enterprise software solutions. So, to ensure effective communication – to give themselves the best possible chance of success – start-ups today must find a way to drive effective teamwork and collaboration among a distributed workforce and ecosystem, at an affordable price point, all while driving productivity, in order to become competitive.
No pressure.
But start-ups have an advantage. Their primary strength in addressing these challenges is their capacity for continuous innovation, not just in terms of products and services but also – crucially – in terms of processes. This owes a huge amount to that optimism which got them started on the journey in the first place. According to McKinsey, “Because they are unhindered by legacy systems and outdated strategies, new market entrants are often able to rethink established practices and cut through traditional industry boundaries.”
Here’s a great example: Impossible Sensing is a CDL alumnus that develops and manufactures autonomous exploration tools designed to function in extreme environments from deep ocean to deep space. Their products are used to detect valuable minerals in off-planet environments. Prior to the pandemic, Impossible Sensing’s founder used 3D-printed models to enable prospective buyers – a Mars scientist at NASA, for example – to get a tangible sense of the firm’s products.
Restrictions on face-to-face meetings put an end to that, leaving this CEO suddenly missing a key part of his sales pitch. He overcame this by using interactive 3D communication which allows customers to play with the 3D models of his product (the closest thing to handling that 3D-printed object) wherever they were located. Video calling is great for replicating the conversation, but there are a number of critical communication experiences that it simply cannot deliver.
Many people might have focused on the frustration of being unable to continue to operate as they had before. But the start-up’s optimism will always find another way.
A start-up’s Big Idea is only as good as the extent to which it can be understood by everyone whose participation is required to make it successful. Get in front of that effective communication challenge as early as possible – solve that knowledge transfer problem across the board – and not only will you be giving yourself the best possible shot at success, you’ll be future-proofing your business against problems which can undermine you as you grow.
About the author:
Patricia Hume is Chief Executive Officer of Canvas GFX.