Creating the Future Workforce at Lincoln Electric

Lincoln Electric has a long and storied history since its 1895 founding in Cleveland, Ohio, as a manufacturer of electric motors. Today, it is a global industry leader in welding equipment and consumables, additive manufacturing, and automation solutions, and has expanded across 19 countries worldwide and serves customers in over 160. But how does Lincoln keep a connection with its origins through a continued spirit of innovation and learning?
Lincoln Electric first opened its welding school in 1917 and a century later launched its state-of-the-art Welding Technology & Training Center, in 2018. This 130,000-square foot facility includes training stations for virtual welding, where all students start their introduction to welding, and more than 150 training booths for learning on the real ‘arc’. There are classrooms to accommodate both live and online instruction.
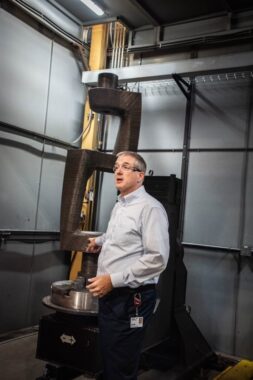
Lincoln Electric’s welding training is given to its new employees and external welding students. In addition, Lincoln also offers both turnkey and custom welding training curriculums and courses for customers to help them upskill their professional welders to achieve specific business targets and goals. They also offer a “train the trainer” course for welding instructors to ensure today’s students are getting the most up-to-date instruction to be industry-ready.
MLC members were given a first-hand look at Lincoln Electric’s headquarters in Cleveland at a recent plant tour that included visits to the welding training center in addition to the company’s machine division, where it builds welding equipment and consumables, as well as its large-scale additive business (3D printing) and their automation solutions.
Lincoln Electric is proud to have a high-performance culture that recognizes and rewards success and provides employees with opportunities for growth and development. The company’s Incentive Management System (IMS) for the production workforce includes piece work pay to maximize personal earnings potential, an annual profit-sharing bonus, a no-layoff policy, and an open-door policy including an employee-represented advisory board, who regularly meet with management to discuss various HR and operational matters. The IMS has been studied by the Harvard Business School and is one of the school’s top-selling case studies.

Lincoln Electric’s state-of-the-art, large-scale metal 3D printing solution is an extension of its automation, software development and metallurgical expertise, which has been applied to an additive process. The company’s additive solutions center is the largest platform of its kind globally with 18 3D printing cells which are used primarily to print replacement parts, molds, tooling and prototypes that measure up to eight feet in length and weigh more than 8,000 pounds – and are printed in a variety of metals including mild steel, stainless steel, nickel alloys, bronze, and Inconel. The solution serves a variety of industries including automotive, aerospace, marine, and energy. Customers provide Lincoln with CAD files or their parts and functional requirements and can expect finished parts in weeks versus months when using traditional castings or forging.
The tour stop in the Automation Solutions Center demonstrated Lincoln Electric’s portfolio of automation solutions that are aimed at increasing productivity and addressing the industry’s skills gap. The technology offered includes automated arc welding products, collaborative robots, metal fabrication, and assembly line solutions. The company has seen increased demand for its collaborative robot solutions in particular as manufacturers attempt to shore up their workforce shortages.
So what lies ahead as Lincoln Electric’s biggest challenge? Like most manufacturers, company leadership says that the core focus must be on people – to continue to build a pipeline of talent and attract, develop, and grow the next generation of leaders.
Additionally, Lincoln will focus on expanding its additive manufacturing and automation businesses in line with current trends and demand from customers in a variety of industries. But the company also intends to keep a focus on having a robust product portfolio that feeds into its bread and butter: a comprehensive and vertically integrated welding business, recognized around the world.