Digital Transformation Sees Explosive Growth
Manufacturers are increasing their investments in digital assets, according to a recent survey from the Manufacturing Leadership Council, the NAM’s digital transformation division.
What’s going on: Due in large part to expectations of economic growth, manufacturers plan to either maintain or boost their spending on smart factory investments, they told the MLC in the recently published results of the Smart Factories and Digital Production Survey.
- Respondents also said they are optimistic about continued digitization and adoption, with 69% expecting moderate growth and no recession.
- While 28% would call their current operations “smart” or “somewhat smart,” 76% expect to be there in the next two years.
- Awareness of AI is growing by leaps and bounds among manufacturers; some 34% said they see AI as very significant. (Last year, just 10% said the same.)
Key points: The survey’s top takeaways include the following:
- Digital transformation is changing the game: Most manufacturers—60%—see digital transformation as something that is redefining the industry.
- More manufacturers are going digital: Some 75% of manufacturers say they are at “midlevel” digital maturity, up significantly from 2024 and 2023.
- AI’s role is inevitable: Fully 80% of manufacturers fully or partially agree self-managing and self-learning facilities powered by AI and machine learning are coming.
Manufacturing Leadership Council Elects Four New Leaders to Board of Governors
Washington, D.C. — The Manufacturing Leadership Council, the digital transformation division of the National Association of Manufacturers, has announced the election of four leading manufacturing executives to the MLC’s Board of Governors. The MLC is the nation’s leading networking and executive leadership organization dedicated to digital transformation in manufacturing by focusing on the technological, organizational and leadership dimensions of change.
The four new MLC board members include the following:
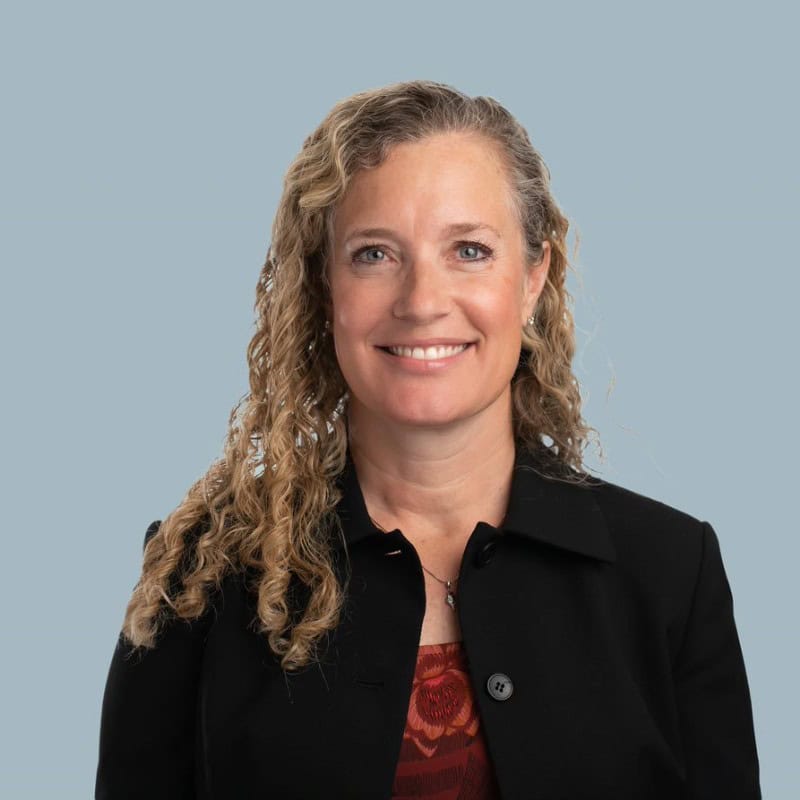
Melissa Boom, vice president, Business Excellence Systems, Winnebago Industries: In her role, Boom has designed and leads the Business Excellence Center of Excellence at Winnebago Industries, which enables the company’s businesses to partner and improve on techniques that drive value, reduce risks and increase synergies. This covers capabilities in business process, continuous improvement, industrial and manufacturing systems engineering, and quality systems.
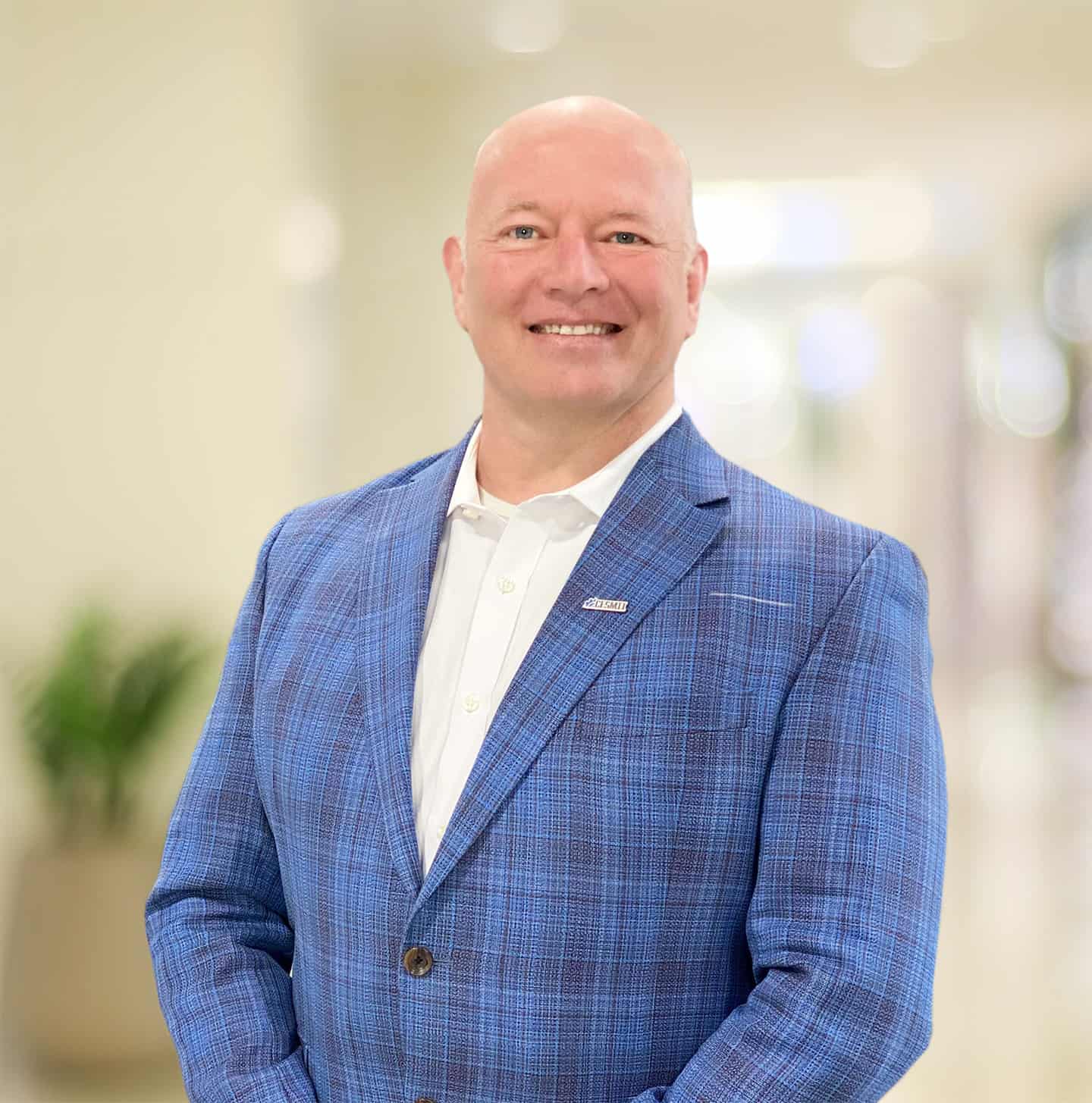
John Dyck, CEO, CESMII – The Smart Manufacturing Institute: Dyck’s leadership of CESMII focuses on outcomes that will benefit the nation’s energy and economic security by sharing existing resources and investing to accelerate development and commercial deployment of smart manufacturing capabilities. He is a renowned domain expert on both technology and business management and has pioneered the application of advanced digital technologies in manufacturing operations and supply chains.
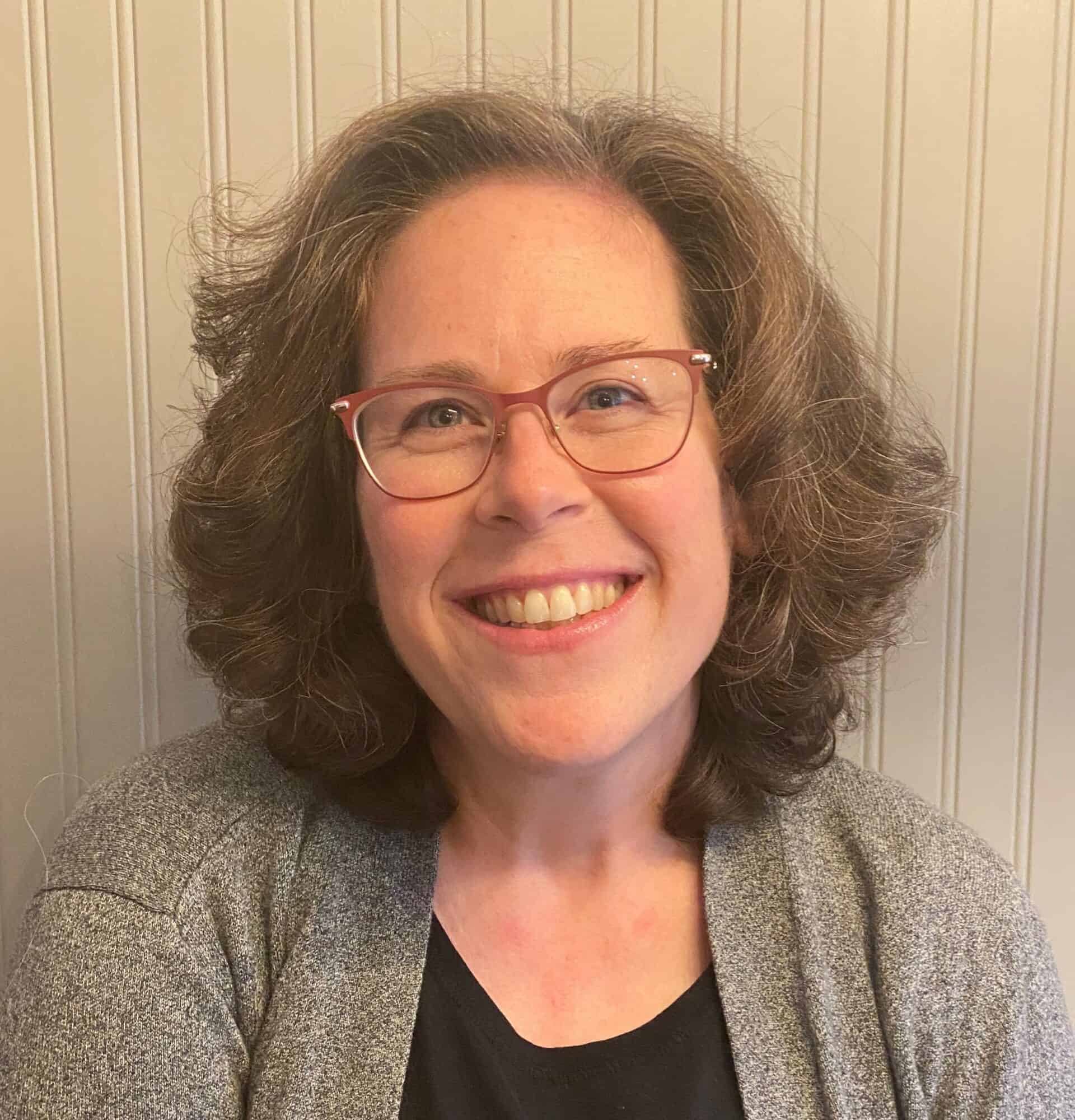
Regan Gallo, director of operations, Coated Abrasives NA, Saint-Gobain North America: Gallo has led operations for four different businesses at Saint-Gobain, in support of more than 40 manufacturing sites. She leads Saint-Gobain’s North American Operations Council, which brings together the company’s North American operations managers to share best practices and align on common operational standards in safety, HR, world-class manufacturing and Manufacturing 4.0.
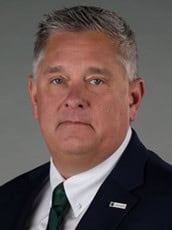
Billy Spears, senior vice president and chief product delivery officer, Lexmark International, Inc.: Spears is responsible for hardware and supplies development, supply chain, manufacturing and service delivery in his role with Lexmark. He also serves on the board for the Kentucky Chamber of Commerce and the Supply Chain Advisory Board for Eastern Kentucky University.
“Adding these distinguished manufacturing leaders to the MLC Board of Governors brings a wealth and depth of experience and knowledge that are critical to serving MLC members,” said Dan Dwight, president and CEO of Cooley Group and chairman of the MLC Board of Governors. “I am proud to welcome these new board members and look forward to collaborating with them to create a stronger future for the MLC.”
“Since its inception, the Manufacturing Leadership Council has always aspired to be at the forefront of digital operations, and to tap the industry experts who could help us meet that goal,” said David R. Brousell, founder, executive director and vice president of the MLC. “The newest additions to our board are essential to that mission and will ensure our place as the leading organization for digital manufacturing leadership.”
As an advisory body, the MLC Board of Governors provides guidance to the MLC on its annual Critical Issues agenda, research studies and programs and services for the MLC membership.
-MLC-
Founded in 2008 and now a division of the National Association of Manufacturers, the Manufacturing Leadership Council’s mission is to help manufacturing companies transition to the digital model of manufacturing by focusing on the technological, organizational and leadership dimensions of change. With more than 2,500 senior-level members from many of the world’s leading manufacturing companies, the MLC focuses on the intersection of advanced digital technologies and the business, identifying growth and improvement opportunities in the operation, organization and leadership of manufacturing enterprises as they pursue their journeys to Manufacturing 4.0.
Rethink 2025 Is Coming Up Fast
Get ready! Manufacturing’s leading annual event on accelerating digital transformation is right around the corner.
What’s going on: Rethink—held by the Manufacturing Leadership Council on Marco Island, Florida, each June—is a must-attend conference for anyone interested in Manufacturing 4.0 and where it’s headed (The MLC is the digital transformation division of the NAM.)
- This year’s event takes place June 15–18 at the JW Marriott Marco Island Beach Resort.
Why you should go: Rethink attendees will get an inside look at the cutting-edge processes and technologies transforming manufacturing today—directly from those creating and implementing them. They’ll also get a chance to:
- Consult with peers on manufacturing’s most critical initiatives, including smart factories and digital production, resilient supply networks and analytics and data mastery;
- Participate in real-time discussions and one-on-one meetings to help them understand how various solutions can solve their business problems;
- Hear from industry leaders and experts during panel discussions, executive interviews and more;
- Interact and collaborate with peers during interactive “think tank” sessions; and
- Hear from the MLC’s event partners during Rethink’s exclusive VIP Tour.
Who will be there: Scheduled speakers include Siemens USA President and CEO Barbara Humpton, Eaton Vice President of Industry 4.0 Craig Sutton, Hershey Company Vice President of Manufacturing, Operations Technology and Supply Chain Strategy Will Bonifant, Rockwell Automation Senior Vice President of Intelligent Devices Tessa Myers and many more.
The gala: Closing out the packed three-day event is the Manufacturing Leadership Awards Gala, at which the MLC will recognize award finalists and winners of the Future of Manufacturing Award, the Manufacturing Leader of the Year, the Small/Medium Enterprise Manufacturer of the Year and the Large Enterprise Manufacturer of the Year. The gala will take place on the evening of June 18.
Attend: Register online here for Rethink 2025. (NAM members get a discount at checkout.) Questions? Send them to [email protected].
The AI Glossary for Manufacturing Leaders: Key Terms You Need to Know
AI is revolutionizing manufacturing, but do you know the essential terms? This quick guide breaks down key technologies driving the future of industrial innovation.
As manufacturing leaders navigate Manufacturing 4.0’s complexities, artificial intelligence has emerged as a critical enabler of digital transformation. With AI evolving rapidly, staying on top of the latest terms and technologies can feel overwhelming.
To cut through the complexity, we’ve put together a quick guide to key AI concepts shaping manufacturing today. Whether you’re exploring predictive maintenance, product development, or human-machine collaboration, understanding these AI technologies will give you a clearer picture of their potential impact on your operations.
- Agentic AI – AI systems capable of autonomous decision-making and action-taking to accomplish goals, often integrating planning, reasoning, and adaptability to dynamic environments.
- Causal AI – AI that goes beyond correlation-based learning to understand cause-and-effect relationships, improving decision-making, diagnostics, and scientific discoveries.
- Edge AI – AI that runs on local devices rather than centralized cloud servers, enabling real-time processing and low-latency applications in areas like IoT, industrial automation, and smart devices.
- Generative AI (GenAI) – AI models that create new content, such as text, images, audio, or code, based on training data. Examples include ChatGPT for text and DALL·E for images.
- Large Language Models (LLM) / Small Language Models (SLM) – LLMs are advanced AI models trained on vast amounts of text to generate human-like language, while SLMs are smaller, more efficient models optimized for specific tasks with lower computational requirements.
- Machine Learning (ML) – A subset of AI that enables systems to learn from data, identify patterns, and make decisions with minimal human intervention. It includes supervised, unsupervised, and reinforcement learning techniques.
- Natural Language Processing (NLP) – AI focused on enabling computers to understand, interpret, and generate human language, allowing for applications like chatbots, translation services, and sentiment analysis.
- Physical AI – AI integrated into physical systems, such as robots or autonomous vehicles, enabling interaction with the physical world through sensors, actuators, and adaptive control.
- Vision Systems – AI that processes and interprets visual data from the world, such as images or videos, enabling tasks like facial recognition, object detection, and quality control in manufacturing.
Scenes from MLC’s AI Conference
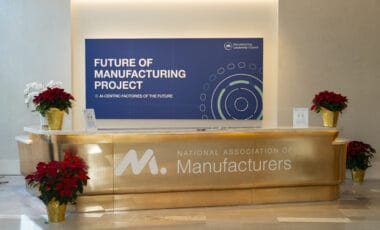
The opportunities and challenges of applying artificial intelligence in manufacturing operations were explored at MLC’s recent event in Orlando.
More than 190 manufacturing executives gathered in Orlando in early December of last year to talk about AI-Centric Factories of the Future. More than one dozen case studies, panel discussions, and presentations were delivered at the one-day conference, which was part of the Manufacturing Leadership Council’s Future of Manufacturing Project.
The goal of the Project is to help manufacturing executives understand the potential of advanced technologies to improve their operations in the years ahead.
The following are photos from the Orlando conference. MLC members can access full videos of the sessions depicted in the photos by going to the MLC Member Resource Center: https://manufacturingleadershipcouncil.com/member-dashboard/resource-center/resource_type/future-of-manufacturing-project/
Photos by David Bohrer, Senior Director, Photography, at the NAM.
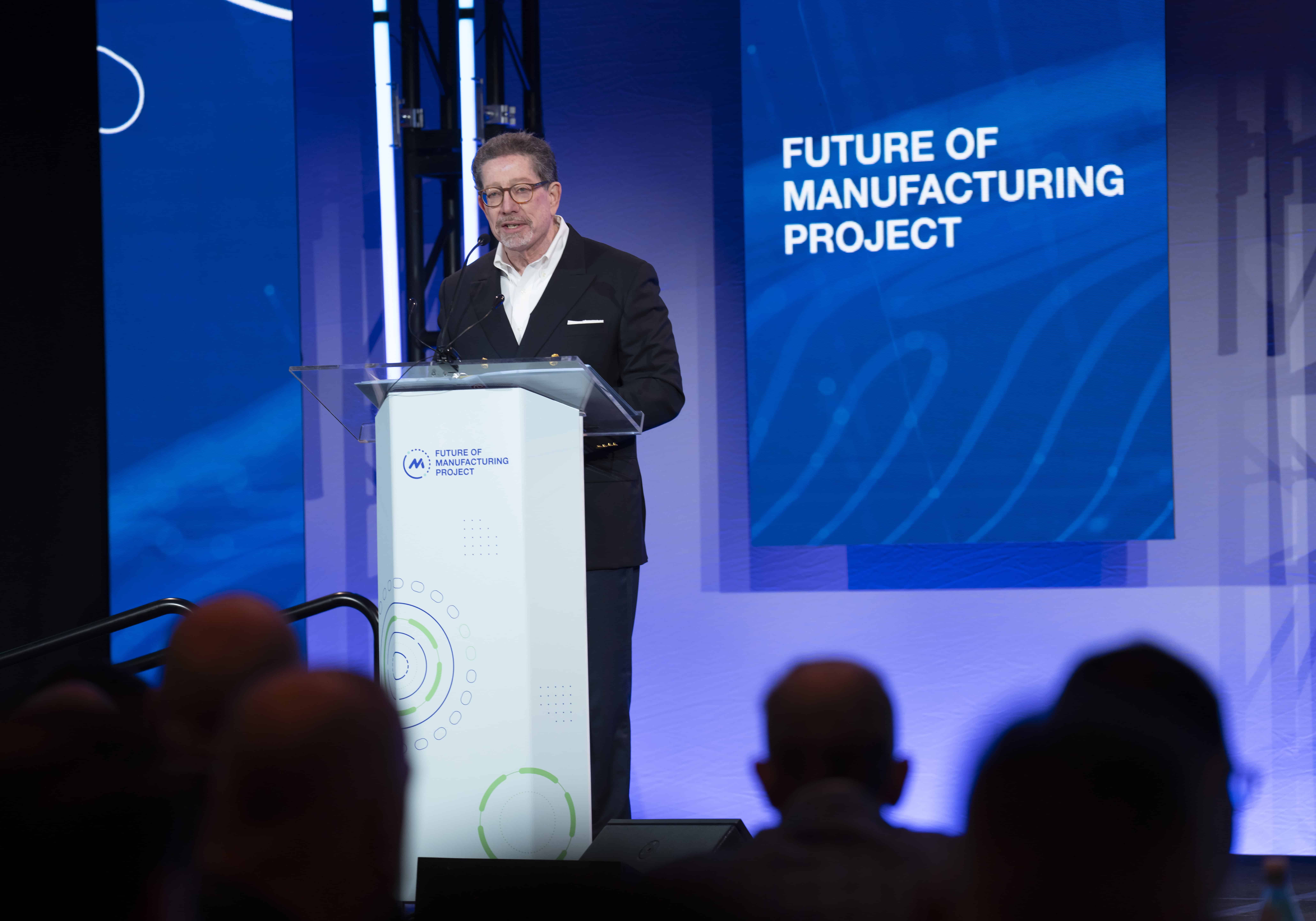
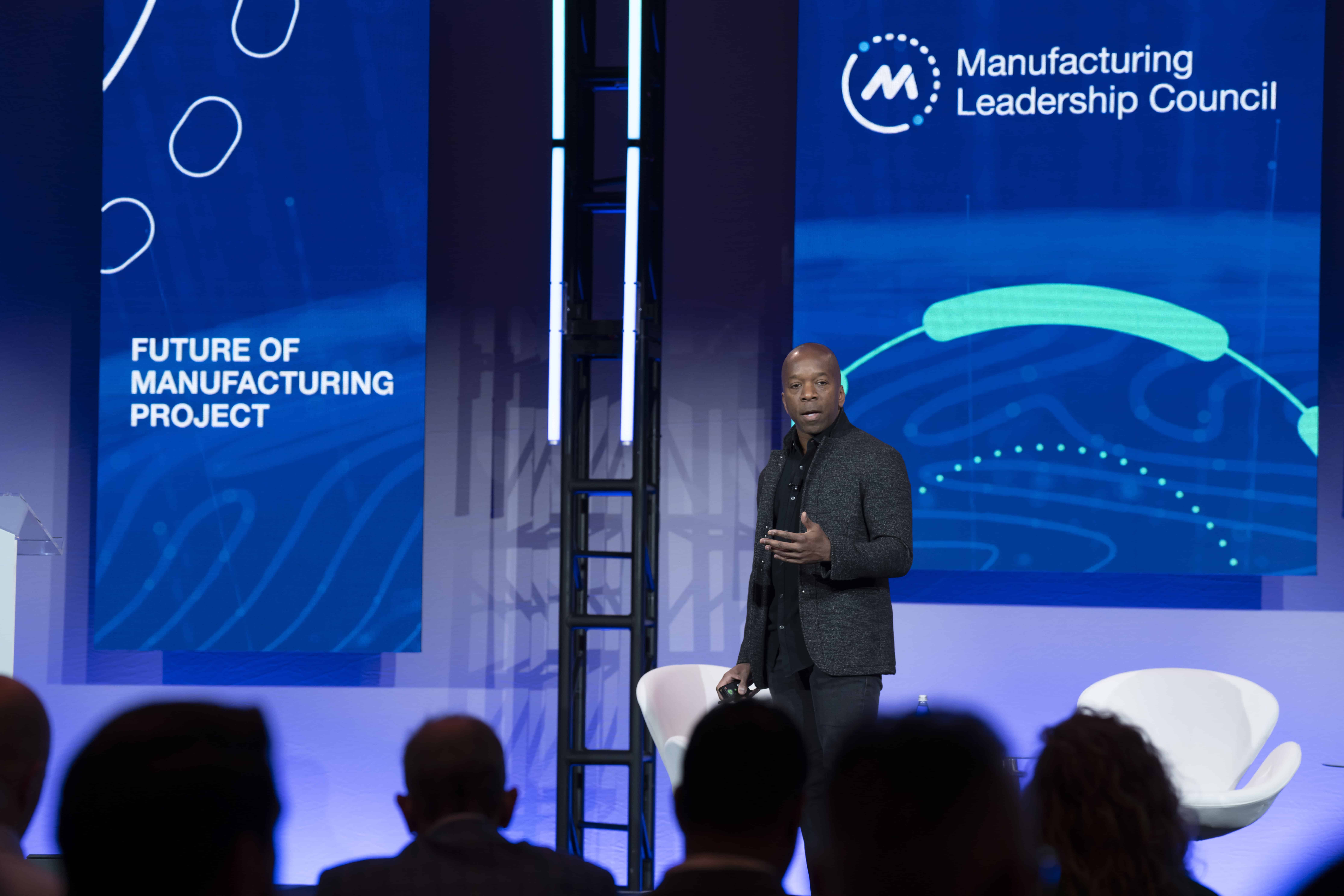
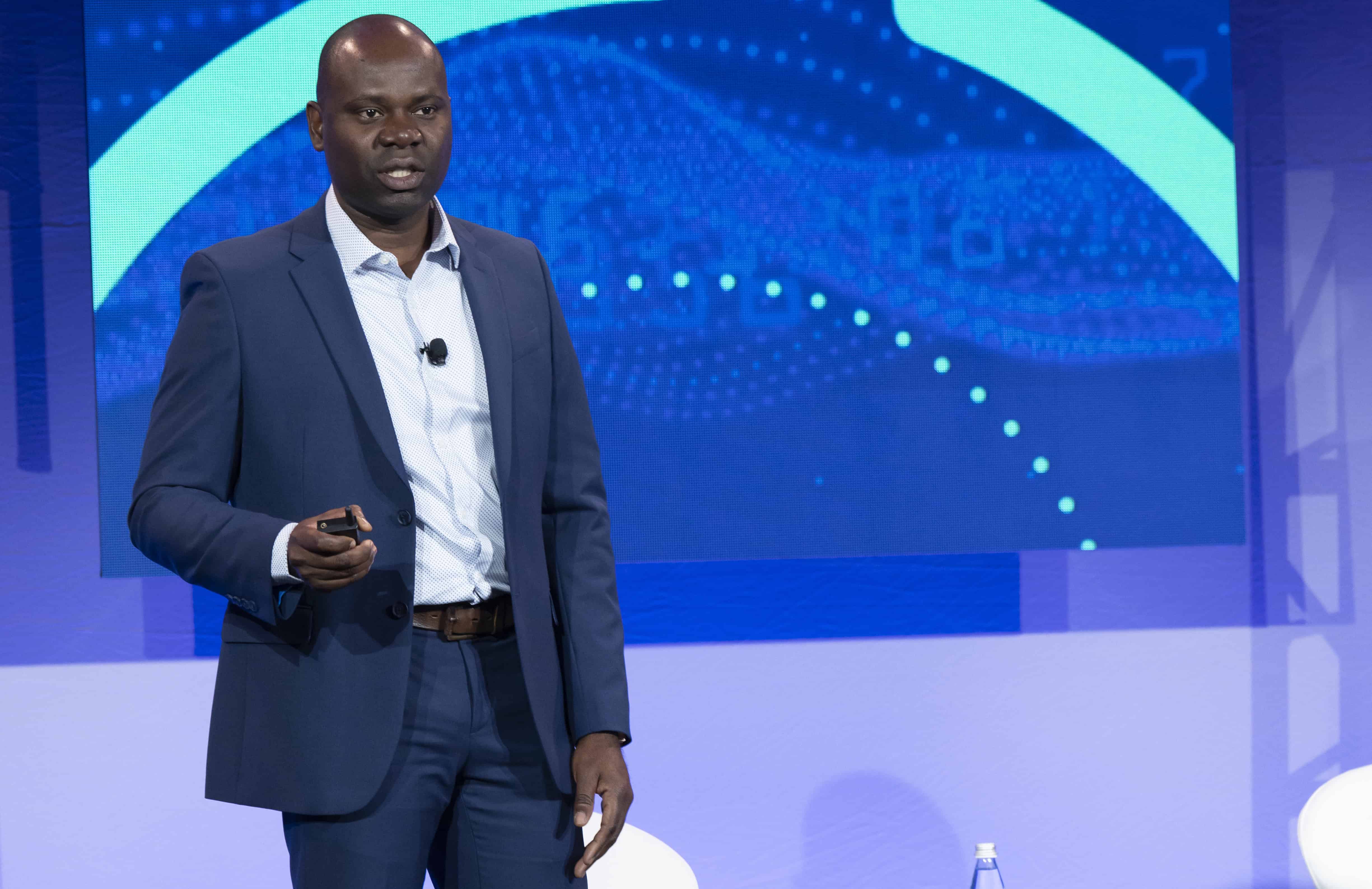
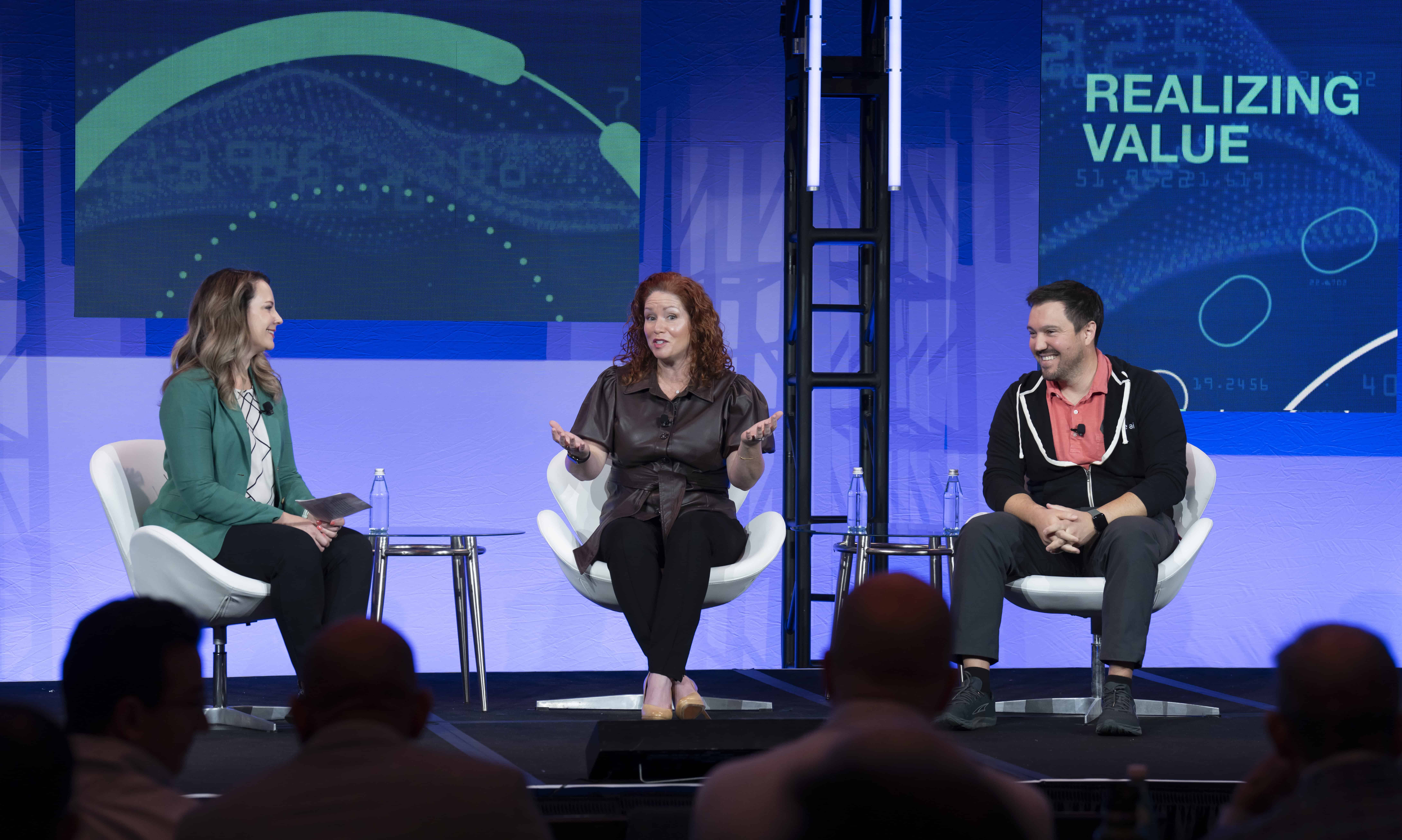
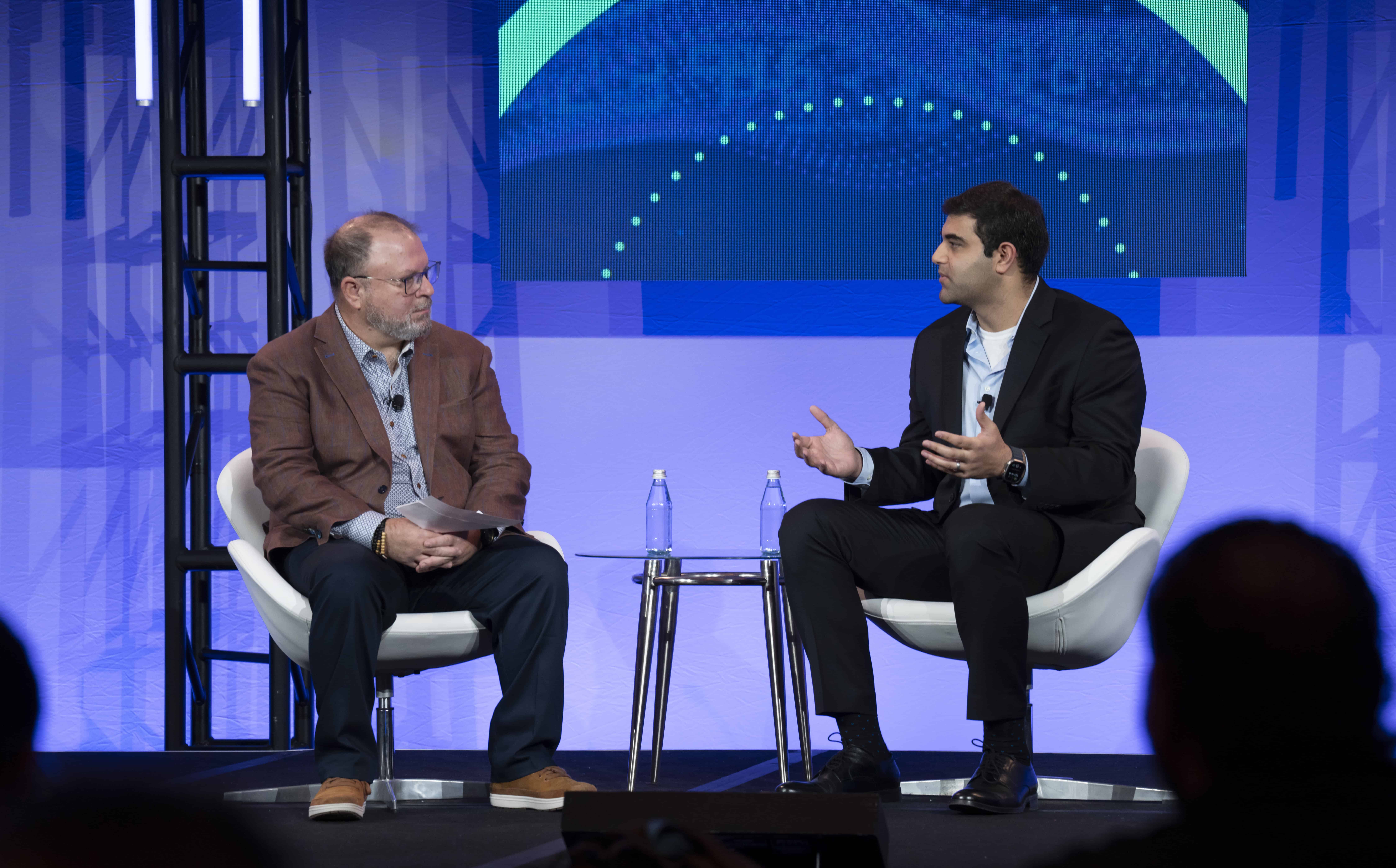
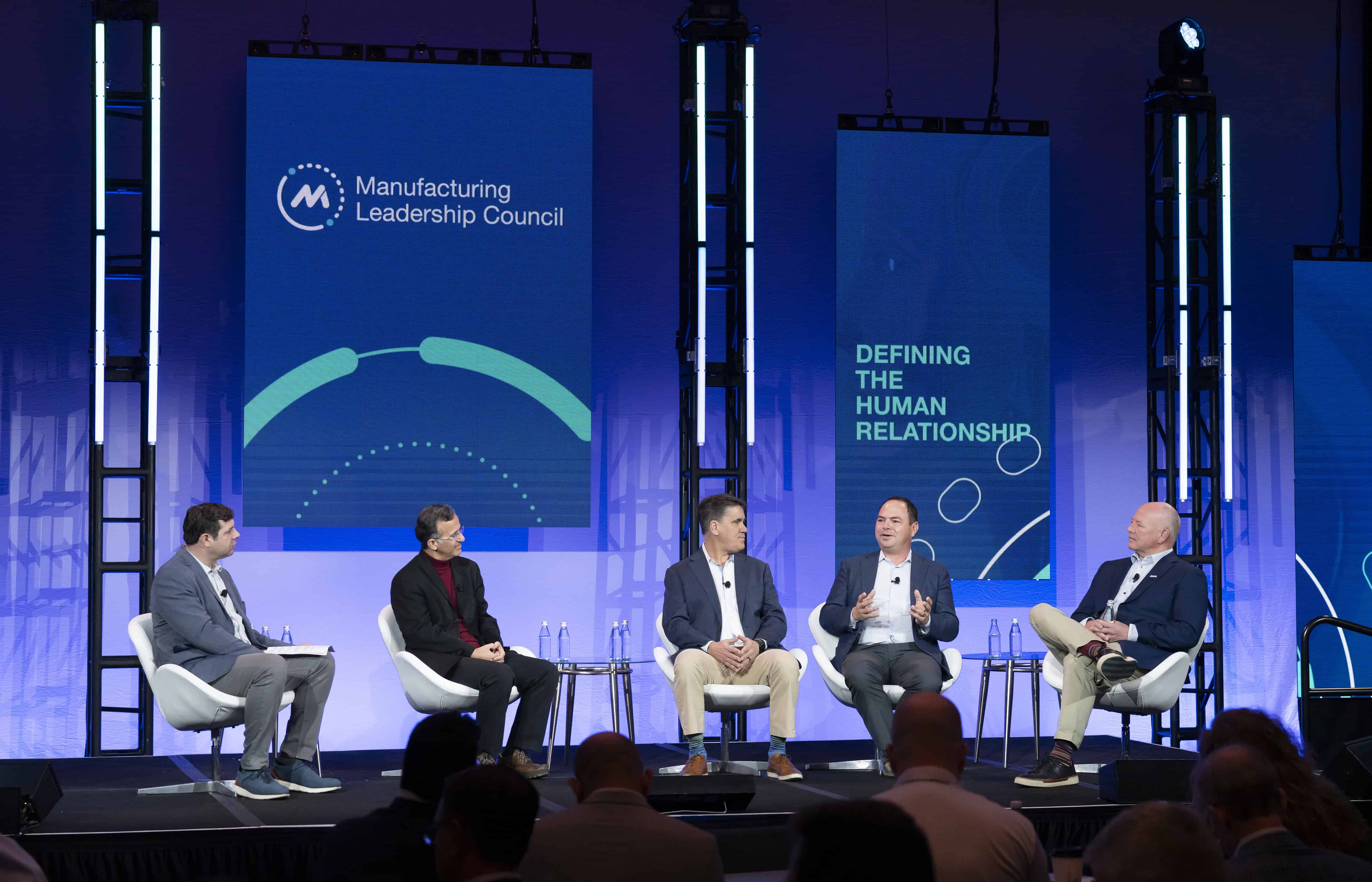
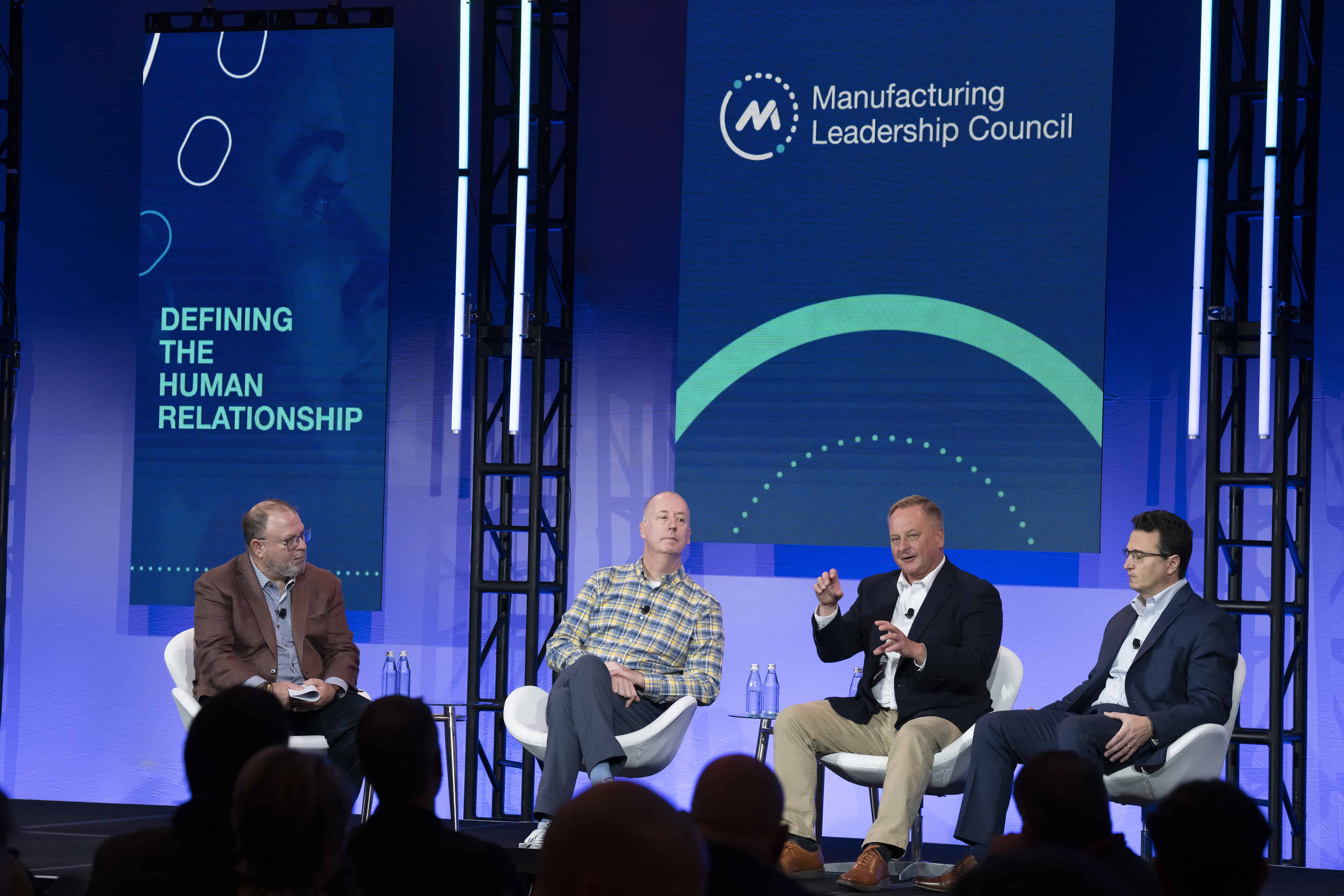
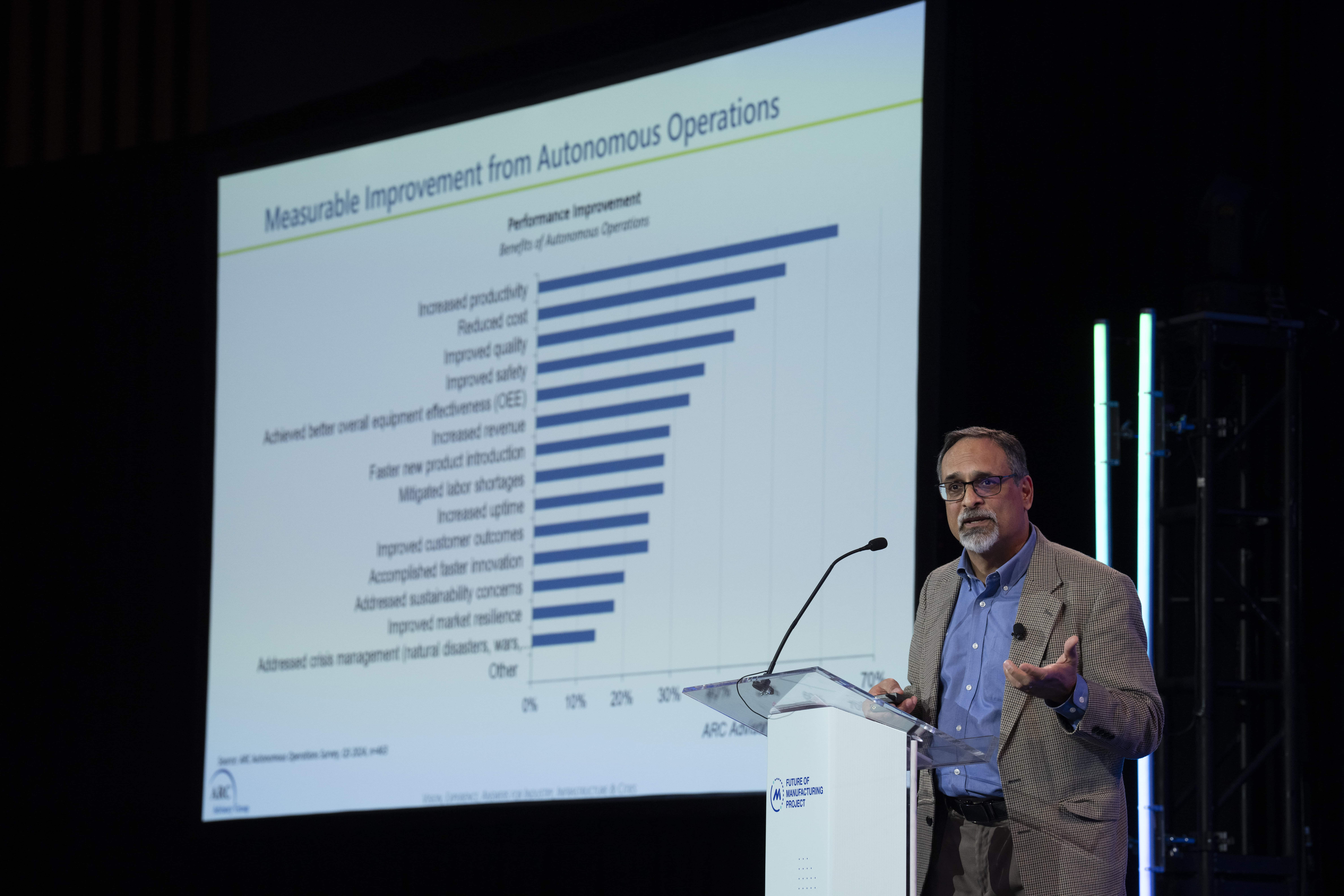
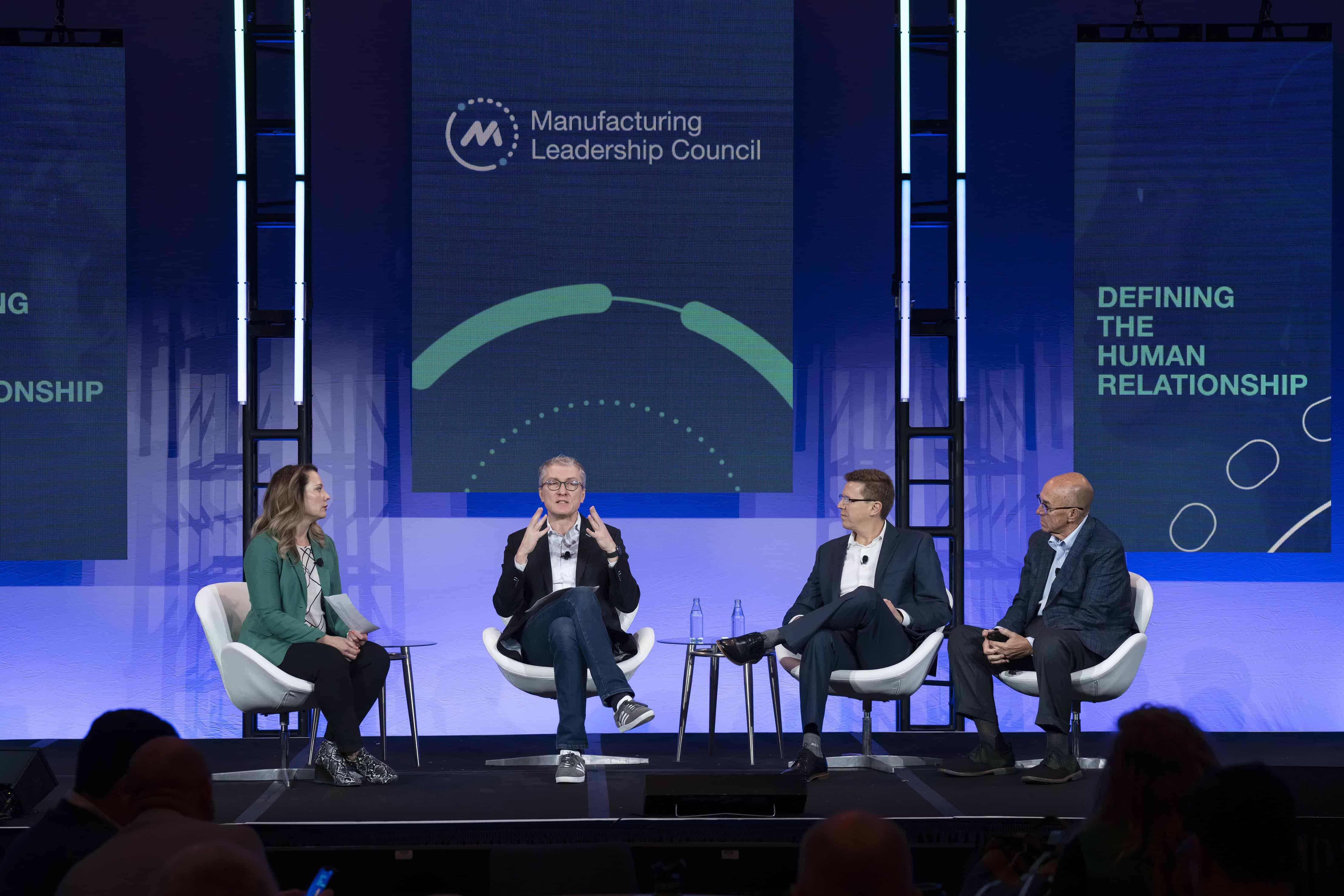
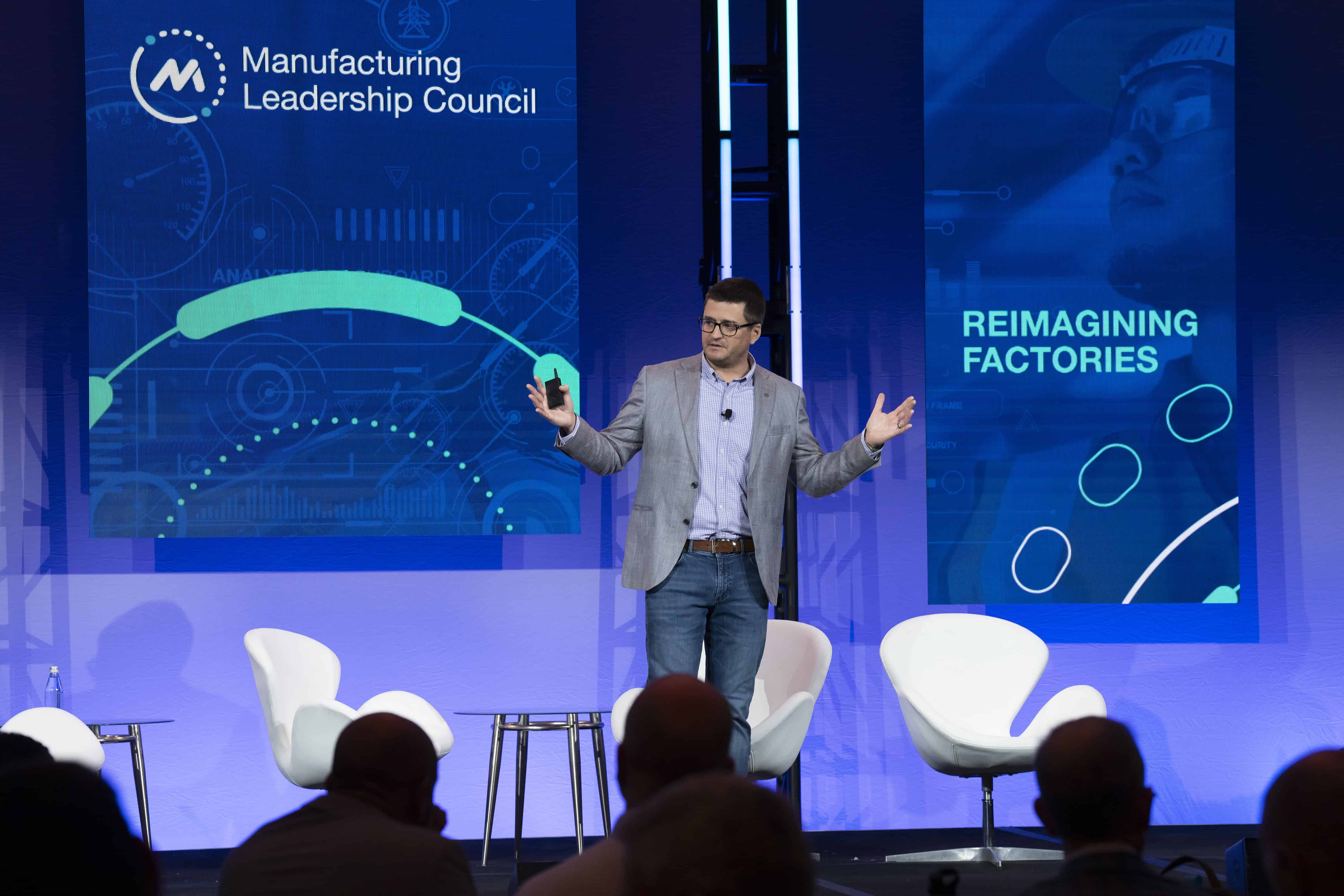
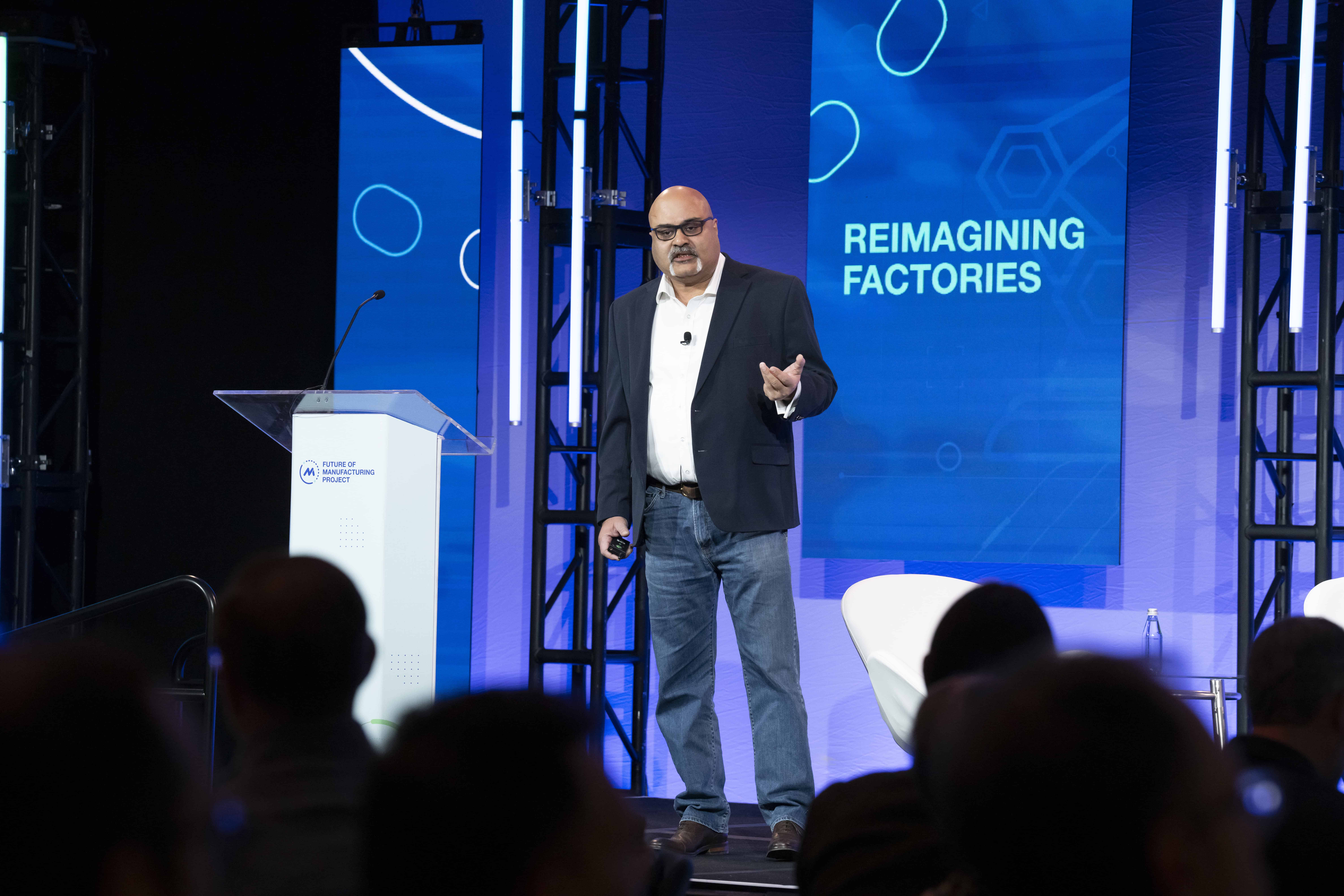
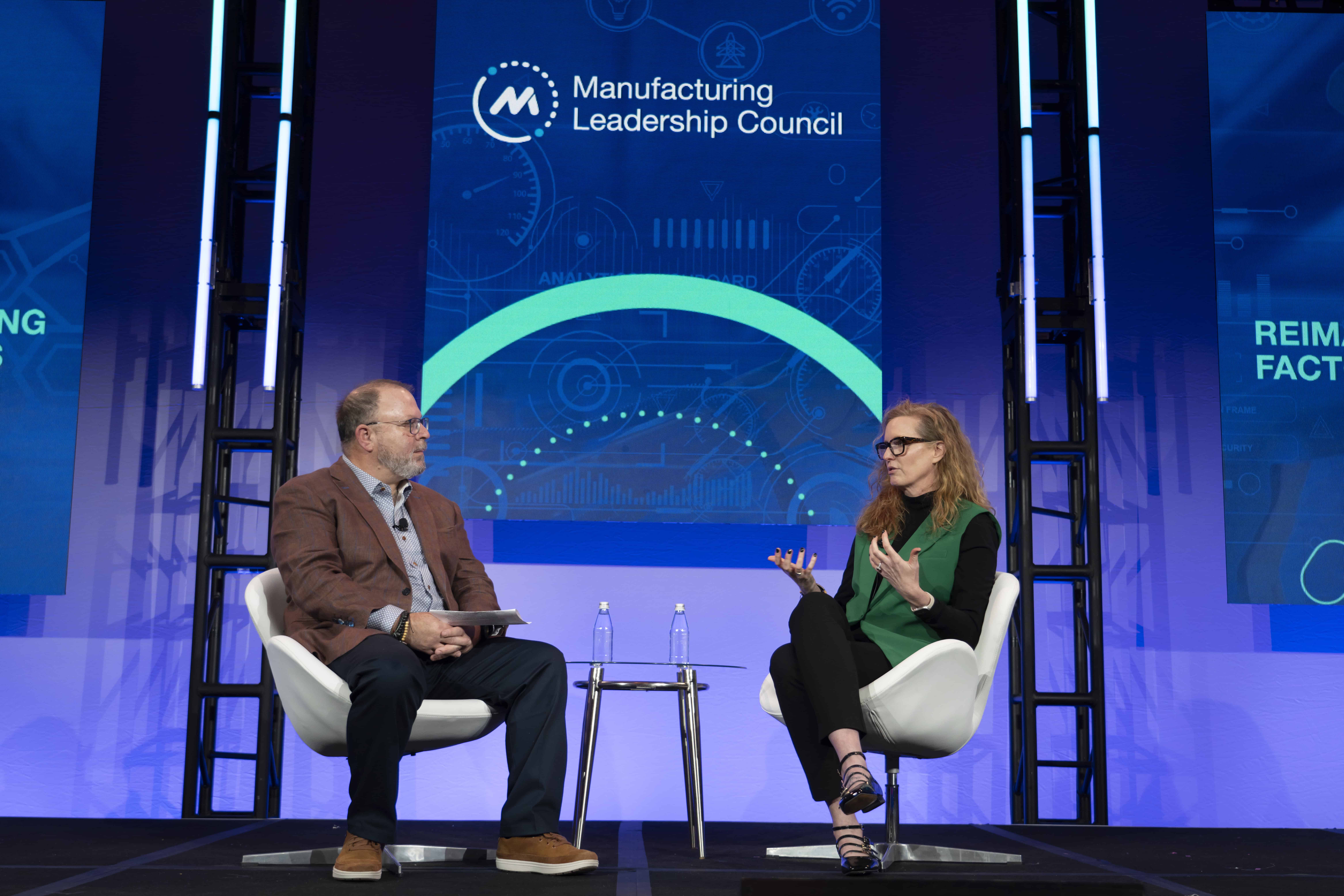
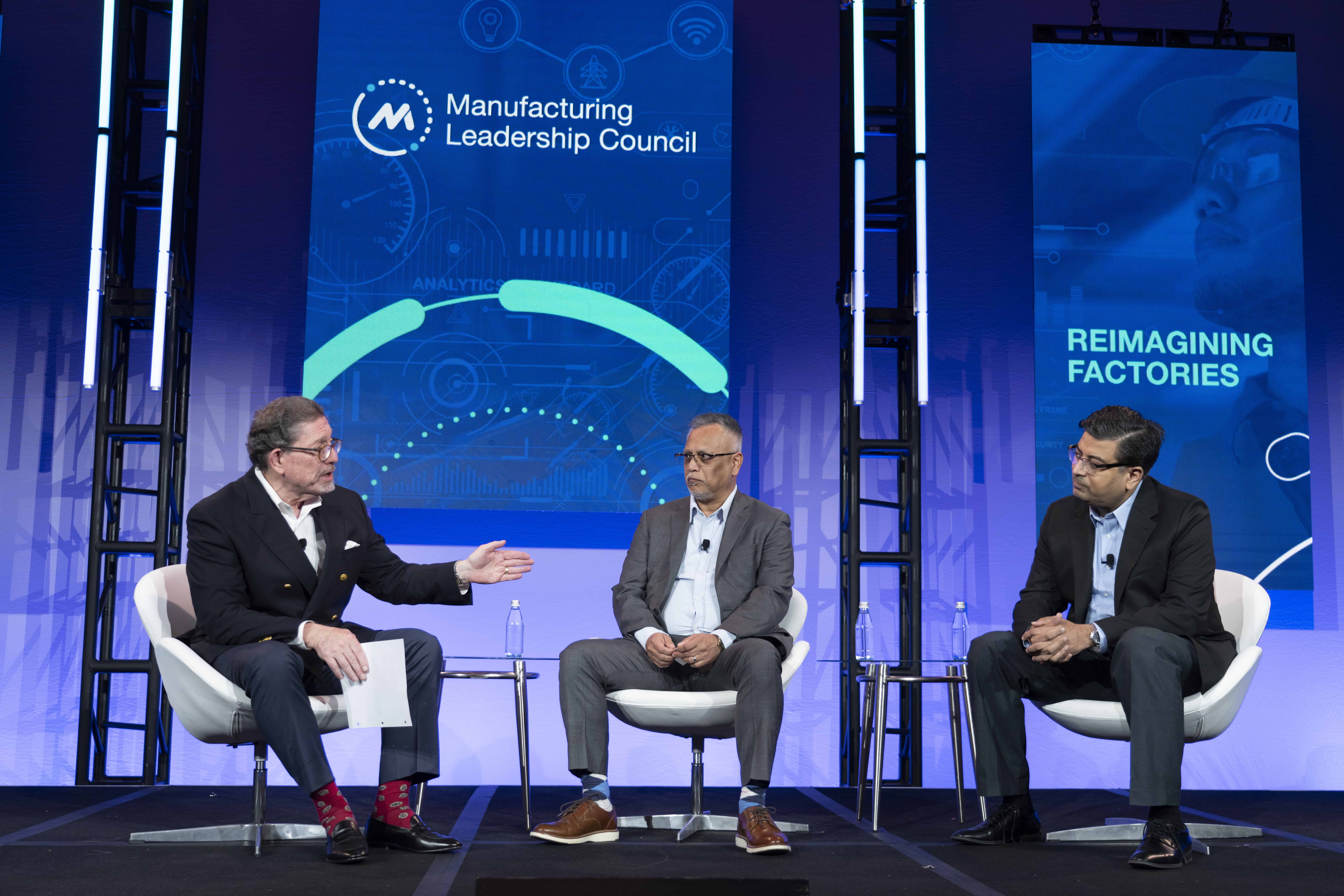
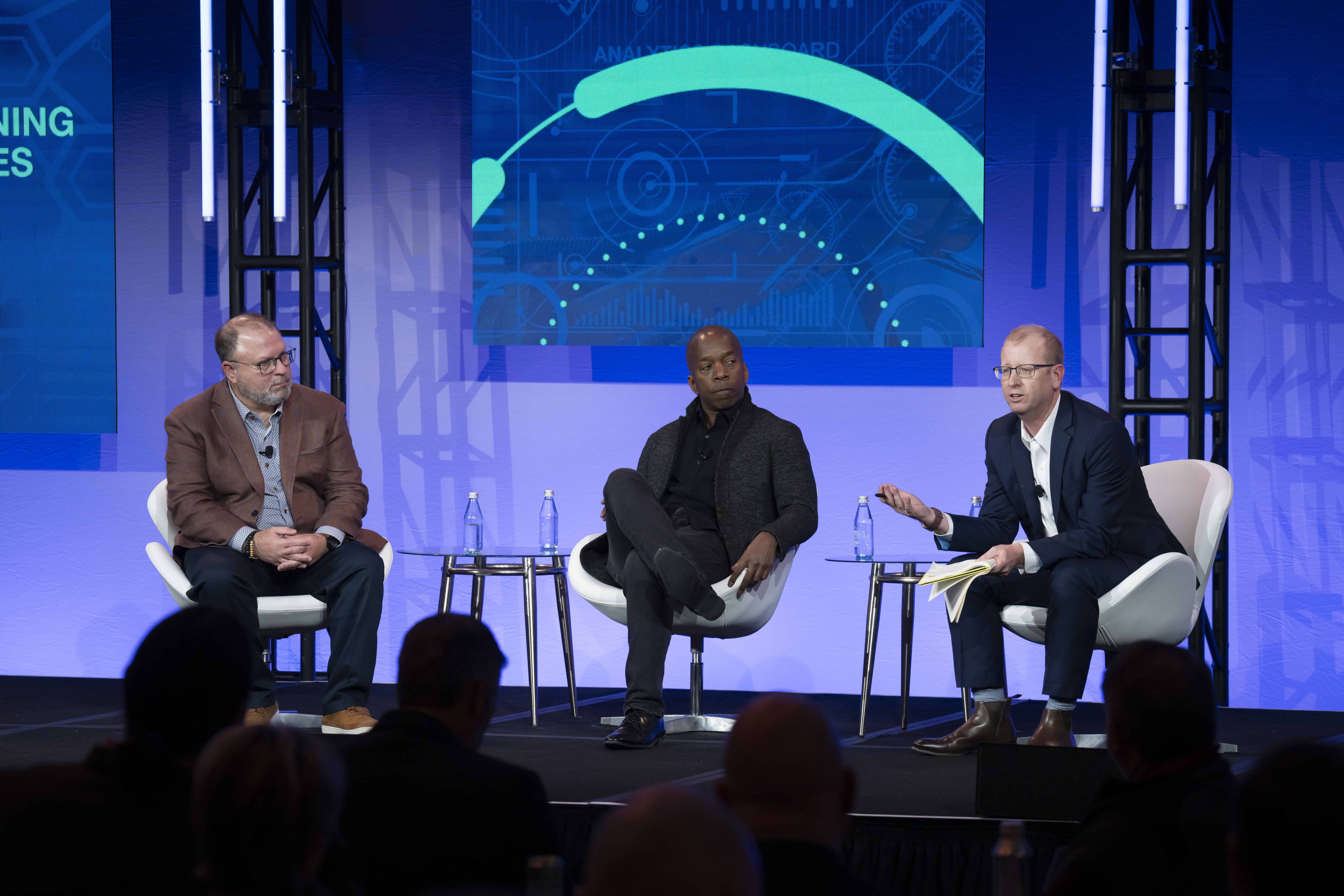
About the author:
David R. Brousell is the Founder, Vice President and Executive Director, Manufacturing Leadership Council
Welcome New Members of the MLC February 2025
Introducing the latest new members to the Manufacturing Leadership Council
Euan Anderson
VP of Manufacturing – KCNA
Kimberly-Clark
https://www.kimberly-clark.com/en-us
https://www.linkedin.com/in/euan-anderson-39316547/
Stacy Brozen
Director of Continuous Improvement NA
CNH Industrial
https://www.cnh.com/
https://www.linkedin.com/in/stacy-kelley-brozen/
Tim Windingstad
Director of Manufacturing – Fabrication
Hatco Corporation
https://www.hatcocorp.com/en
https://www.linkedin.com/in/tim-windingstad-04446b198/
Troy Youngbauer
COO
Galloway Company
https://www.gallowaycompany.com/
https://www.linkedin.com/in/troy-youngbauer-8a9012b/
Dialogue: Finding the Human Edge in Manufacturing AI
Dow’s Tim O’Neal shares how data, AI, and intentional talent placement drive operational excellence
Penelope Brown, MLC: Well, hello, everybody, and thank you for joining us for the February 2025 edition of Executive Dialogue, and today we are super excited to be talking to Tim O’Neal of Dow. He is their Global Director of Operational Excellence and Leveraged Services, and he is also one of the Manufacturing Leadership Council’s newer members of our Board of Governors. We’re really excited to have him on board and to get to know him a little bit today. So, Tim, thank you for joining us.
Tim O’Neal, Dow: Thank you for having me. I appreciate the time to talk.
PB: Let’s talk a little bit about you. Get to know you a little bit. I know you’ve been with Dow, you know, for a while. What’s your career evolution been like there? And what’s your current role? What does that entail?
TO: I’ve been with Dow 28 years. It’s going on a quick 29 years coming up soon. But I’m currently the Global Director of Operational Excellence and Leveraged Services. My role is really to support our businesses and our plant assets through best practices, like quality, continuous improvement, digital, environmental and analytical services, external manufacturing and including operations, talent management like recruiting, onboarding and with learning and talent development as well.
I began my career in 1997 in Seadrift, Texas as an environmental protection engineer. From that role I quickly moved into direct manufacturing, and I progressed through the manufacturing journey with roles in multiple technologies and production plants.
I was blessed to lead large world scale plants as well as the smaller batch facilities, where you can switch products and create different products within hours and not days. I was the site director before moving into a global environmental health safety and sustainability role to drive our corporate world leading operations, sustainability goals.
And you and I first met when I became the digital operations, IT/OT director responsible for all the manufacturing digital teams, and from that role I then joined this global director role in operational excellence.
PB: So let’s pick up a little bit. I know you just mentioned part of it is recruiting and that talent development piece. You know, really improving performance of both people and processes through that continuous learning and building those effective teams. What do you think, is the most important thing for leaders to know when it comes to encouraging team members to really perform at their best?
In operations and manufacturing, we can measure everything, but you want to make sure that you’re measuring those items that can lead to actions, whether it’s defects, outliers, and trends.
TO: To me, it’s always about placing talent and people intentionally. I see it almost like, I think, three bubbles. There’s this intersection of skills, passion in terms of what people want to do, and then what the organization needs and values. If we take the time to understand our individual team members, that intersection is where discretionary effort is born which leads to performing at our best.
PB: A few months ago you were on one of MLC’s Decision Compass calls. For those of you that may be watching this and not in the know, these are virtual working group meetings that we host.
You were discussing how Dow uses data to predict operational failure. Borrowing from that theme, how do you think the data can most easily be translated into action for manufacturers?
TO: First and foremost, I really think about measuring where it matters. In operations and manufacturing, we can measure everything, but you want to make sure that you’re measuring those items that can lead to actions, whether it’s defects, outliers, and trends. Early in my career a very experienced leader had mentioned to me one time and really gave me some great advice. He said, “Tim, manufacturing plants will whisper to you and let you know when something is not exactly right.”
And so our challenge is to really understand that and place a measurement system in place to detect the most probable failures in our facilities.
I believe in the future we will continue to see AI as a collaborative partner enhancing our capabilities and really helping us meet some of the dynamic challenges in changing marketplace in our manufacturing industry
PB: Borrowing some from that data theme, we’re hearing a lot of that from our members. It’s been an ongoing struggle to get data to a really usable format. But a lot of our members and the manufacturing community at large is really trying to get their data in shape to start using AI right? So you want to have that data in a good position to be able to feed into those algorithms and give you those actionable insights.
There’s a lot of discussion about that growing role of AI within manufacturing operations. Looking toward the future, do you see AI mostly staying in a role as strictly a digital tool? Do you see it becoming a collaborative team member? Or do you see it potentially moving into what might be considered a leadership role?
TO: First, we have a long history in our industry of AI in the early forms, if you think about machine learning, automation and optimization. However, we are in the earlier learning stages of our Generative AI journey. I see AI’s role in manufacturing and decision making as multifaceted, and it’s continuing to evolve.
We envision AI, not just as a digital tool, but an integral part of our team helping us drive efficiency and innovation. I believe in the future we will continue to see AI as a collaborative partner enhancing our capabilities and really helping us meet some of the dynamic challenges in changing marketplace in our manufacturing industry.
PB: Yeah, it’s an exciting time. And I’m really quite keenly interested to see where this all ends up going in the next 3, 5, 10 years. We’ll really see what happens there.
Talking again on that AI theme, MLC just in December, hosted our Future of Manufacturing Project event down in Orlando and we had an AI theme around that. And one of our panel discussions talked about how AI might impact decision making specifically. For example, where that decision is made such as within maybe a functional role, or why it was made based on the type of decision. What types of decisions do you think AI is going to end up influencing the most?
As long as we have reliable and governed data where folks understand that you have one source of truth, I believe that’s where we’ll have the best decision-making capabilities.
TO: I personally believe it’s limitless and I’ll go back to your statement regarding data. As long as we have reliable and governed data where folks understand that you have one source of truth, I believe that’s where we’ll have the best decision-making capabilities. And it could be structured or unstructured data, but I think where AI really will help us make decisions is to make those trends and make the data very visible and be much more quicker to analyze, so that we can make sound decisions.
For our teams, the early areas where we’re piloting this is really in plant reliability, where you can make decisions about taking equipment down and doing maintenance in a timely manner. And I think this is where AI can look at multiple pieces of data and maybe give us a quicker glance at what could potentially be a failure in our, in our manufacturing facilities.
PB: Well, Tim, thank you so much for your time today. We are, again, very happy to have you on our Board of Governors, in addition to all the other insights that you share with us and share with our members.
Thank you and we hope to see you again soon.
TO: Yes, absolutely. Thank you for the time, and I appreciate a chance to catch up.
PB: Thank you. M
About the Interviewer:
Penelope Brown is Senior Content Director for the NAM’s Manufacturing Leadership Council
Survey: M4.0 Appears Poised for A Significant Leap
Manufacturers are ramping up digital investments, with AI, automation, and smart factories reshaping the industry faster than ever.
KEY TAKEAWAYS:
● Digital transformation is a game changer. Sixty percent see it as a defining shift for the industry, marking a strong rebound in enthusiasm after a dip in 2024.
● Manufacturers digital maturity continues to increase as 75% believe they are at a mid-level maturity—up significantly from the 2024 and 2023 survey results.
● AI expectations have rebounded. A full 80% now fully or partially agree that self-managing and self-learning facilities powered by AI and machine learning are on the horizon.
Manufacturers are charging ahead with their digital transformation efforts. The Manufacturing Leadership Council’s Smart Factories and Digital Production Survey reveals an increase in smart factory maturity and optimism about continued digitization and adoption.
Fueled by an expectation of economic growth and a corresponding plan to increase or maintain smart factory investments, respondents share an outlook that includes AI adoption, end-to-end digitization, and belief that the game changing power of digital transformation is moving beyond mere table stakes.
Section 1: Economic Outlook and Investment Trends
Manufacturers are optimistic about the economy in 2025, with 69% expecting moderate growth and no recession, while only 8% anticipate an economic slowdown. Encouragingly, 11% expect inflation to ease and growth to rebound, signaling greater confidence in market stability. (Chart 1)
This optimism extends to smart factory investments, with 89% of manufacturers planning to maintain or increase spending in 2025. Within that number, it’s notable that 44% expect to ramp up investments, aligning with a broader push for digital transformation. (Chart 2) In the 2024 version of this survey, only 9% expected to increase their Manufacturing 4.0 investment.
Meanwhile, only 8% foresee a decline in spending in 2025, underscoring that despite economic fluctuations, smart factory adoption remains a strategic priority. The data suggests that as confidence in economic growth solidifies, companies are doubling down on automation and digitalization efforts to remain competitive.
1. Strong Majority See Growth on the Horizon
Q: What is your company’s outlook for the economy in 2025? (Select one)
2. 89% see smart factory investments increasing or remaining unchanged
Q: How do you expect your company’s outlook for the economy to influence M4.0 smart factory and production technology investments for 2025? (Select one)
Section 2: Smart Factory Maturity and Adoption
The digital transformation journey continues to advance, with manufacturers steadily maturing their smart factory strategies. Compared to previous years, the percentage of companies rating themselves at lower maturity levels (1-3) has declined significantly, from 57% in 2024 to just 16% in 2025. Meanwhile, those ranking their factories at a mid-level maturity (4-7) increased to 75%—up from 42% in 2024 and 58% in 2023—and 9% now place themselves in the advanced range (8-10). (Chart 3)
While progress is evident, most companies are still in experimental phases—40% are piloting small-scale projects and 6% are implementing on a single-project basis. Meanwhile, 34% are scaling these initiatives company-wide. Only 15% are just beginning their digital journey, emphasizing a strong industry-wide shift toward implementation. (Chart 4)
In fact, only 28% believe their factories are very smart or somewhat smart today. That number is expected to skyrocket to 76% by 2027. (Chart 5)
For this to happen, specific functional areas must advance. So it is a positive that manufacturers aspire to reach advanced adoption in every area included in our survey. Many find themselves in the intermediate range, with procurement/inventory management the area most ripe to move from early adoption to this stage. (Chart 6)
Despite this, full integration with business strategy remains a work in progress, with just 24% rating their integration at eight or higher on a 10-point scale, though this is an improvement from 7% in 2024. (Chart 7)
3. Smart factory journeys continue to mature
Q: How would you assess the maturity level of your smart factory journey? (Scale of 1-10, with 10 being the highest level of digital maturity)
4. Most experimenting with small-scale pilots or scaling smart factory practices
Q: Which activity best describes the primary stage of your company’s M4.0 digital efforts today? (Select one)
5. Smart factory explosion expected by 2027
Q: How “smart” do you consider your factory and plant operations to be today and what do you anticipate they will be by 2027?
6. Manufacturers still striving to reach advanced digital adoption stages
Q: At what stage of digital adoption are the following functions in your company? (Rate as early, intermediate or advanced)
7. Smart factory strategy becoming more integrated with business strategy
Q: To what extent has your smart factory strategy been integrated with the company’s overall business strategy? (Scale of 1-10, where 10 is fully integrated)
Section 3: Digitization and Automation Growth
Manufacturers anticipate a significant leap in factory-wide digitization by 2027. Today, only 2% report being extensively digitized, but this is expected to surge to 38% within the next two years. Similarly, partial digitization is set to grow from 47% to 52%, while the number of companies still in planning stages will plummet from 43% to just 5%. (Chart 8)
Production and assembly processes are on a similar trajectory. Only 6% of companies currently consider these processes extensively digitized, but this figure is projected to jump to 45% by 2027. (Chart 9)
Integration with customers and suppliers, however, remains a weak spot—just 2% report extensive digital connectivity today, though 22% expect to achieve this by 2027. (Chart 10)
Taken together, these findings highlight a growing recognition of end-to-end digital transformation as essential for operational agility and supply chain resilience, while identifying an opportunity for improved digitization between manufacturers and their customers and suppliers.
8. Significant end-to-end digitization on the horizon
Q: To what extent are your factory operations fully digitized end to end today, and what do you anticipate they will be by 2027?
9. 92% predict extensive or partial digitization of production/assembly by 2027
Q: To what extent are your production/assembly processes digitized today, and what do you anticipate they will be by 2027?
10. Digital integration with customers and suppliers lags behind in-house digitization
Q: To what extent are your production functions digitally integrated with customers and suppliers today, and what do you anticipate they will be by 2027?
Section 4: Future of Factory Models and AI-Driven Operations
Manufacturers envision a hybrid future for their factory networks, with 44% expecting a mix of small and large facilities, reflecting the need for both localized agility and economies of scale. Large-scale production remains dominant, with 40% favoring large factories or networks of large facilities, while only 10% see a shift toward smaller, more agile production models. (Chart 11)
AI-driven automation is also gaining traction. Almost one quarter (23%) of manufacturers fully agree that factories will evolve into self-managing, self-learning facilities, a dramatic increase from just 6% in 2024. Another 57% partially agree, suggesting growing confidence in AI’s ability to optimize operations. This shift reflects the industry’s increasing focus on AI-driven decision-making and predictive analytics as key enablers of the smart factory vision. (Chart 12)
11. Only 10% see small, agile factories and networks as the future
Q: What is the expected future state of your factory model?
12. Expectation of self-managing, self-learning factories increase significantly
Q: Thinking about the impact of technologies such as AI and machine learning, to what extent would you agree or disagree with the following statement: “Tomorrow’s factory will evolve to be a self-managing and self-learning facility.”
Section 5: Technology Adoption and Priorities
The 2025 survey highlights strong momentum in advanced technologies, particularly cybersecurity (73% scaling/at scale), IIoT sensor networks (46% scaling/at scale), and advanced analytics (56% scaling/at scale). AI adoption is also accelerating, with 22% of manufacturers now scaling/at scale with AI solutions, and another 42% piloting at least one AI project. Machine learning follows a similar trend, with 21% scaling/at scale and 29% planned for future deployment by 2027. (Chart 13)
AI’s perceived impact is rising sharply—34% now see it as very significant, compared to just 10% in 2024. (Chart 14) This signals a shift from experimentation to real-world application, as manufacturers increasingly leverage AI for predictive maintenance, process optimization, and adaptive automation. However, emerging technologies like the metaverse, blockchain, and exoskeletons remain niche, with over 70% of companies having no plans to adopt any of them. (Chart 13)
13. Cyber, advanced analytics, IIoT sensor networks top production operations tech list
Q: Where does your company stand in regard to the following technologies in its production operations?
14. AI’s expected significance increases
Q: Looking ahead over the next few years, how significant an impact will AI have on your production operations?
Section 6: Challenges and Benefits of Digital Transformation
Manufacturers continue to grapple with major roadblocks in their smart factory journeys. Nearly half (49%) cite outdated legacy equipment as their top challenge, up from 39% in 2024, highlighting the complexity of modernization. Workforce-related barriers are also growing—43% point to a lack of skilled employees, a sharp increase from 24% in 2024. Resistance to change remains a persistent issue, with 42% citing organizational culture as a challenge, though this has improved from 53% last year.
But it’s not all bad news. In 2024, a lack of leadership buy-in and access to adequate budget/investment both ranked among the top four roadblocks. Improvements have been seen in both these issue areas. Leadership buy-in and increasing budgets may very well prove to be leading indicators that the current issues discussed above may become lower hurdles rather than roadblocks. (Chart 15)
Despite these current roadblocks, companies recognize the benefits of transformation. Nearly two-thirds (63%) rank operational efficiency as the top expected gain, a significant jump from 40% in 2024. Better decision-making (49%) and cost reduction (44%) follow closely, demonstrating that digital adoption is increasingly seen as a performance and profitability driver. (Chart 16)
Notably, the percentage of companies expecting digital transformation to create a competitive advantage has soared from 11% in 2024 to 38% in 2025. While the majority still see digital transformation as table stakes, the dramatic increase in those who see it as a competitive advantage marks a major shift in strategic thinking. This shift suggests that as adoption accelerates, digital capabilities are becoming key differentiators rather than mere necessities for survival. (Chart 17)
15. Legacy equipment, lack of skilled employees and organizational culture are biggest smart factory roadblocks
Q: What do you feel are your company’s primary roadblocks to implementing your smart factory strategy? (Select top 3)
16. Better operational efficiency outpaces all other smart factory benefits
Q: What are the most important benefits and opportunities your company hopes to realize from embracing a smart factory strategy? (Select top 3)
17. Digital transformation still seen as table stakes for majority, but increasing number see it as a competitive advantage
Q: Do you believe that digital transformation of your company’s manufacturing operations will create a unique competitive advantage for your company or is it merely table stakes to remain in the game?
Section 7: The Strategic Value of Digital Transformation
After a dip in enthusiasm in 2024, manufacturers now overwhelmingly see digital transformation as a game-changer—60% believe it signals a new era for the industry, up from just 26% last year. Another 40% still see it as significant but not transformative, while no respondents consider it insignificant. Apart from our 2024 survey, these numbers have remained largely consistent over the past four years. (Chart 18). M
18. After dip in 2024, majority now see digital transformation as a clear game changer
Q: Ultimately, how significant an impact will digital transformation have on the manufacturing industry?
About the author:
Jeff Puma is content director at the NAM’s Manufacturing Leadership Council.
Autonomy’s Path: Operations Transformed with Production Logistics
Seamless material and data flow is unlocking the next frontier of digital transformation and empowering autonomous operations.
TAKEAWAYS:
● Manufacturers have focused automation efforts on primary manufacturing processes but not as often for material movement.
● Automating and optimizing material flow is essential to improved competitiveness and a gateway to autonomous operations.
● Success requires a deliberate plan and committed leadership in addition to awareness about commonly encountered challenges.
The fourth industrial revolution promises that advancements in technologies like IoT and AI will bring new levels of intelligence to manufacturing, ultimately reducing the need for human intervention in operations. Decades of investment in automation, along with the growth of digital technologies, has advanced this vision.
While manufacturers have adopted significant levels of automation in their primary manufacturing processes, material movement has mostly missed the Industry 4.0 treatment. Many sophisticated manufacturers rely on people to move material around their automated processes. Even Amazon, a leader in robotics, recently opened its most automated warehouse yet, which includes 2,500 people to support non-automated tasks, such as picking product and loading trailers.
To achieve more autonomous operations, the manual production logistics activities that exist today need to be automated and optimized, just like primary manufacturing tasks. Current market conditions are ushering in this next wave of automation and digital transformation. Rising labor costs, labor shortages, new economic policies, and worker safety concerns are accelerating investments in technologies like autonomous mobile robots, automated guided vehicles, and other automated material movement and storage systems, many of which are seeing double digit CAGRs. A recent survey of over 5,000 global manufacturers shows that the adoption of robotics, specifically AMRs and AGVs, as a top 3 investment area among manufacturers embracing digital technologies.
The end goal of this new wave of automation is to reduce labor cost, improve efficiency, and increase operational resiliency, resulting in a competitive advantage in production. Leading digital transformation roadmaps and I4.0 strategies include plans for automating and optimizing material flow – it’s directly on the path to more autonomous operations.
Defining Integrated Production Logistics
A strong production logistics capability goes beyond automating manual workflows. The automation is foundational, but it also involves orchestrating the flow of material movements and informing it with a touchless stream of data. At its core, integrated production logistics is the autonomous end-to-end flow and coordination of material movement throughout all operational functions, informed and optimized by data and insights.
- Autonomous: This implies a level of foundational automation and includes the integration of human activities with robot-supported movements, a tenet of Industry 5.0.
- End-to-end and throughout operational functions: This value is best realized when viewed holistically. The entire logistics process should be considered: planning, scheduling, receiving, unloading, staging, inbound put away, picking, prep, line delivery, line takeaway, and loading. Disruptions in one area can ripple throughout the process, destroying productivity.
- Informed by data and insights: The data generated in and around material movement systems should be digitized and treated with the same value as production data. It is a necessary input to dynamically coordinate and control flow.
Overcoming Common Challenges
Systems-level and holistic thinking is an essential step to making progress with integrated production logistics. The following challenges must also be overcome to achieve success:
- Fragmentation: The market for material movement solutions is extremely fragmented. In the Americas, the top 8 AGV and AMR vendors hold less than 50% market share collectively. This means businesses are unlikely to find one vendor to provide all the necessary hardware and software to automate and coordinate their material moves. For most, this means multi-vendor fleets and solutions, leading to complexity and at worst, process and technology silos.
- Technology limitations: MIT roboticist Daniela Rus said, “robots are still primitive compared to humans. Working on these technologies has only amplified my appreciation for the mental and physical marvel that is the human being.” The technology has greatly improved in the past three to five years, accelerated by advancements in AI, but it has limitations, including the tasks it can perform, the environments it can navigate, the loads it can move, and the speed it can operate. Companies still won’t find a single robot that can do it all. Humans and robots will continue to share space and the whole ecosystem needs to work together to achieve productivity targets.
- Cost: Production logistics investments are significant. Until relatively recently, the return on investment hasn’t always justified the automation. Today, blend high labor cost and labor scarcity with significantly improved and more affordable technology, and the investment calculus is attractive.
- Integration: Processes or facilities may not be set up for optimal flow, and the goal is not to automate a bad process. Islands of automation may have been created over the years, meaning parts of the process may be automated but those automation islands don’t communicate. Systems also may not speak the same language. Standards are progressing but challenges remain in creating an integrated solution.
To illustrate the importance of integration and interconnectedness in production logistics, consider the following scenario, which existed at a leading consumer goods company.
Before, a lack of integration between production orders and material ordering caused several inefficiencies including:
- Inefficient timing of orders
- Overordering
- Unnecessary staffing
- Excess Rework
Leveraging data the operation had available, two points of integration were implemented to drive a higher level of optimization into the process. The manufacturer not only realized labor savings with AMRs, but unlocked additional value and potential by leveraging data to better integrate the operation.
Elements of a Successful Integrated Production Logistics Solution
Manufacturing leaders face numerous challenges in achieving integrated production logistics. Here are the essential building blocks to overcome these challenges and realize the benefits:
- Production Logistics Integration and Orchestration Layer: Connects and coordinates work between multiple material movement solutions, enterprise systems, and people. It serves as the integration point between automated and manual operations and can provide key functions like scheduling optimization, traffic management, and act as a data broker.
- Enterprise Service Bus: Provides a consistent interface to core enterprise systems (e.g., MES, ERP), avoiding the need for point integrations.
- Enterprise Systems (WES, WMS, MES, CMMS): Manage orders, inventory, production schedules, tracking, and maintenance plans.
- Digital Twin or Simulation: Continuously optimize and test new processes before implementation with this digital representation of material flows. This twin can serve as a foundation for building AI models.
- Material Movement Hardware: Includes robots, conveyance systems, pickers, stackers, or storage and handling equipment that moves material within the facility.
- Fleet Managers: Coordinate and optimize the operations of a group of robots, handling tasks like deployment, configuration, task scheduling, and performance monitoring.
- Operational Technology Connectivity Solution: Connects to multiple hardware sources and translates or interprets various protocols, ensuring seamless communication between different systems.
- User Interfaces: Allow humans to manage operations with interfaces such as industrial HMIs and web applications. Middleware can provide a “single pane of glass” view, reducing the need for multiple interfaces.
- Enterprise and Data Analytics Layer: Logistics data should be captured, historized, and contextualized in the same spirit as production data. Includes tools for processing data, building analytical models, and visualizing performance.
Each of these elements has a role to play and should be considered in a successful integrated production logistics architecture or roadmap.
How to Get Started
Successful programs involve strategic planning, organizational change management, leadership commitment, and demonstrating success prior to rollouts.
To achieve transformational integrated production logistics, take a holistic view of operations. Begin with an assessment that considers multiple lead sites and benchmarks potential benefits. This initial strategic assessment should:
- Prioritize material moves based on feasibility and operational value.
- Identify lead sites that can serve as models for scaling.
- Articulate the value proposition to the organization.
- Define the delivery structure, governance, and partnerships needed for scaling.
- Benchmark sites and assess their readiness.
- Advance lead sites to pre-spend stage for capital requests.
- Define the implementation roadmap.
- Present the target state architecture to achieve integration, coordination, and optimization of automation equipment.
The result of this initial strategic assessment will provide the required guidelines, technical recommendations, and actionable insights to align stakeholders, secure funding, and ensure a successful implementation of transformational integrated production logistics.
The Opportunities for Success
Early adopters of integrated production logistics have an opportunity to outpace their competition. Advancements in material movement technology, combined with the right market dynamics, are creating a new wave of automation investment. Establishing a sustained competitive advantage requires scale and deeply integrated solutions. Digital executives should assess their readiness for this new wave of automation and prioritize integrated production logistics as one of the most transformational opportunities for I4.0 advancement. M
About the authors:
Austin Locke is Principal – Global Lead of Data Science and AI at Rockwell Automation Digital
Braun Brennecke is Senior Manager, Data Science and AI at Rockwell Automation Digital
Enabling Transformation with Smart Operations
Increasing visibility and speed of execution through Manufacturing 4.0 and connected systems are critical to meet manufacturers’ needs.
TAKEAWAYS:
● Manufacturers need digital tools and capabilities to address the increased business volatility that may impact their success.
● The key to success is how quickly manufacturers can identify and address the array of problems and opportunities that arise.
● Software systems that once enabled business transformation may now be a constraint, so manufacturers need updated technologies.
Manufacturing companies are continually balancing capability with opportunity. At the highest level, the challenges that manufacturers face today are the same as they’ve always faced—namely, how to deliver the best product or service at a cost that allows them to make a profit and invest in future opportunities. The new challenge manufacturers are now facing is how to address the significantly increased business volatility that can impact their success. Rapidly changing market dynamics, regulatory changes, technology advances, resource constraints, nationalism, and competitive pressures are forcing companies to react faster than ever before just to stay competitive. While many of these factors are not new problems, and every problem can be solved, developing an effective solution for addressing them simultaneously can seem like an unsurmountable challenge.
The key for success is how quickly manufacturers can identify and address the array of problems and opportunities that arise. Companies need to mitigate quality problems discovered in the field before they impact customers, margin, and future sales. They also need to identify potential shortages before they affect production. Manufacturers need to identify customer opportunities with material sourced before they lose out to the competition. They need to mitigate potential machine failures before they impact production. Moving too slowly can often make the solution worse than the problem. For example, building up too much inventory to address a shortage as the market starts to cool adds inventory and potential obsolescence costs.
Manufacturers may struggle to have the visibility they need to identify opportunities and challenges quickly. Manual processes and disconnected systems not only make visibility difficult, they can also make the rapid analysis and remediation required painfully slow. In such instances “heroes” are born: they make a phone call, call in a favor, work endless overtime hours, pay expediting costs, or throw additional resources at the problem to get to a resolution. These workarounds can be costly, cause disruption, and are normally not sustainable for long periods of time.
“Connectivity enabled through modern technology, strong organization, and innovative leadership enables a manufacturer to respond faster and more efficiently.”
Manufacturing 4.0 promises to help address these issues. Connectivity enabled through modern technology, strong organization, and innovative leadership allows a manufacturer to respond faster and more efficiently. Digitalization of the business provides the path to minimize the lag between the discovery of problems and execution of solutions. Optimizing the entire business requires a connected enterprise. This connection enables the visibility required to execute faster. Connecting engineering to manufacturing with a common product master enables faster and more accurate execution. Enabling a seamless flow between product engineering, manufacturing, quality, suppliers, supply chain, sales, and service enables digital execution between business processes. Looking at the business holistically as a connected enterprise enables smart operations.
With the advent of artificial intelligence (AI) and the dependency on data for better results, data availability and quality are becoming ever more critical. While manufacturers have been using predictive AI for years to predict machine failure and optimize production, they’re now using generative AI to improve quality and manufacturing efficiencies. To maximize the benefits and opportunities of AI for manufacturing, the next step will be to bring the operational technology data (OT) and back office/information systems (IT) data together so that correlations, predictions, and recommendations can be more accurate. Having a common platform that brings these data together enables an operator, supervisor, or maintenance technician to have visibility of their business and make better decisions faster. Persona-based workbenches enable the user to obtain the exact information required at the time required. The objective is to provide the information and tools necessary to better understand “their business” and be able to execute as required. The result will be users that are more productive, capable, and accountable to the business.
For many, software systems have served as a critical enabler of this business transformation, but they can also sometimes impede further progress on the journey. This has been the case for manufacturers that have selected systems that optimize specific areas of the business without taking into consideration the holistic need for a complete business transformation. Disconnected systems and complex integrations that once enabled a business may not have the capabilities and functionality needed to support new business models or adapt to rapidly evolving business requirements. With the immense effort required to make changes, IT and the systems that support them have often become a business constraint rather than an enabler. Modern cloud native enterprise applications have helped to address these issues by providing integrated platforms that are also updated continually. Manufacturers can take advantage of newly embedded capabilities and technologies such as AI as they evolve without requiring a reimplementation.
While most rightfully see Manufacturing 4.0 or Industry 4.0 as a journey vs. a destination, many companies feel as though they have not progressed as much as they would like. The World Economic Forum found that more than 70 percent of companies that invested in Industry 4.0 projects failed to get the benefits anticipated. Why is this so difficult? What can be done to increase success?
“Success is determined by how much time and what level of resources manufacturers need to identify any problems or opportunities and be able to adequately address them.”
The challenge for many companies is that their Industry 4.0/digitization projects are managed in silos. Similar to an assembly line or manufacturing constraints shared in Eliyahu Goldratt’s book The Goal, only optimizing a part of the business implies that the business is still constrained. The real value comes with connectivity between the lines of business. A manufacturer may find it useful to use real-time machine data to help predict machine failures and production progress to then manually create a maintenance order. However, using that data to have the system automatically order maintenance parts, plan a maintenance order, and adjust production schedules is even better. Being able to simultaneously and automatically notify the machine supplier so that they can improve their quality takes it even further.
How companies measure their Manufacturing 4.0 progress is another challenge. A snapshot in time is not necessarily the best indicator of digital transformation success. A successful transformation is really about the ability for a manufacturer to support constant innovation, continual improvement, and the capability to effectively address whatever challenges or opportunities that arise now or in the future. For these manufacturers, the better measurement is their ability to act, not just their performance improvement at any point in time. If they have transformed effectively, they have the visibility necessary across the organization, access to tools to analyze data quickly, and the capability to execute on that information. Success is determined by how much time and what level of resources manufacturers need to identify any problems or opportunities and be able to adequately address them. The ability to do so in the best way possible is a part of the Manufacturing 4.0 journey leading to smart operations and the ability for manufacturers to successfully address the ever-evolving business volatility. M
About the authors:
John Barcus is GVP Manufacturing Industries Strategy and Advanced Technologies at Oracle Corporation.