The Foundations of Enabling an M4.0 Supply Network
Today’s competitive supply networks are digitalized, responsive and flexible enough to adapt rapidly to changing markets, challenges and opportunities.
TAKEAWAYS:
● Looking at your supply network as an extension of your business provides an opportunity to significantly improve results.
● The goal is to reduce latency and enable agility across all aspects of the supply chain decision process.
● Increased collaboration, visibility and improved execution across the supply chain are now the keys to success.
Properly managed supply chains have long been instrumental in the success of manufacturers, with the leaders continually adapting as capabilities have evolved. Walmart was an early pioneer in driving costs out of the supply chain through automation, technology, global sourcing and creative logistics. Amazon added additional speed, transparency and visibility to give rapid deliveries and almost real-time order and delivery status, even expanding to support third-party manufacturers and sellers — which currently represent more than 60% of their retail business. Success in supply chain management combined with organizational scale has given both companies significant control over the market and the manufacturers that supply them. They set a new bar for how supply chains should be managed.
Conversely, many manufacturers have been negatively impacted by their inability to effectively manage their supply networks. There have been stories of companies that outsourced their supply chains without providing proper oversight that resulted in issues with quality, deliveries, customer satisfaction and margins. During the Covid pandemic, in addition to supplier challenges, an overreliance on the just-in-time replenishment model compounded shortage issues, leading to missed opportunities for many manufacturers. With the complexity of the global supply chain, it took years to bring supply chains back to a “normal” state.
Manufacturing 4.0 supply networks are digitalized, responsive and flexible enough to adapt rapidly to changing markets, challenges and opportunities.
Now, with increasing nationalistic pressures, constantly changing regulations, new tariff challenges and the introduction of rapidly evolving transformative technologies, it is even more critical that manufacturers manage their supply chains to the most optimal level possible. Increased collaboration, visibility and improved execution are now the keys to success. Manufacturing 4.0 supply networks are digitalized, responsive and flexible enough to adapt rapidly to changing markets, challenges and opportunities. The following ideas can help optimize and positively transform your supply chain.
Make the Supply Network an Extension of Your Business
Looking at your supply network as an extension of your business vs. treating suppliers like traditional vendors can significantly improve results. Using a unified system that offers full visibility into the supply chain while integrating the supply network with shared systems can help standardize processes, maintain quality standards and ensure delivery commitments are met. Integrated feedback loops to ensure process and quality compliance enables the business to improve performance, reduce costs and bring about better execution. Automated business processes throughout operations and the extended supply network enables better efficiencies.
One company that has found success with this is Cohu, a global technology leader in semiconductor test equipment. As a high-tech manufacturing company, they are heavily reliant on outsourcing to build and supply their products. Their success is dependent on integrating their suppliers into their manufacturing business to ensure high-quality and on-time deliveries.
The earlier that a problem or opportunity is identified, the greater the manufacturer’s chance of achieving a quick and optimal resolution.
“One system and one process means that production managers in Malaysia don’t have to work with three or four different processes and workflows when engineering change orders come through,” said Cohu CIO Craig Halterman. “As we extended our supply chain solution to our suppliers, we now capture information about the components they make early, so we don’t find out that a piece didn’t pass inspection or was made outside of a certain control limit when we’re putting our machines together. Any time we can reduce the quality issues coming in our door that we have to pass back to the supplier is a major improvement.”
A critical element of success is closed-loop feedback that enables quality processes and validates that the processes were followed. As Ronald Reagan famously said, “Trust but verify.”
Enable Rapid and Improved Decisions
As manufacturers deal with increased turbulence across the supply chain, the goal is to reduce latency and enable agility across all aspects of the supply chain decision process. This includes time to identify problems, determine resolutions and execute the best solution.
The earlier that a problem or opportunity is identified, the greater the manufacturer’s chance of achieving a quick and optimal resolution. Clear visibility across the supply chain and business operations is essential. Best-in-class processes like Sales and Operations Planning (S&OP) and Integrated Business Planning (IBP) provide a strong foundation for making faster, more informed decisions. However, disconnected, spreadsheet-based processes often hinder the timely flow of critical information. Some manufacturers run monthly S&OP cycles that take more than a month to complete. This can lead to missing the critical feedback loop that is essential for success.
IBP enhances these capabilities by integrating financial planning more effectively. For instance, incorporating financial planning tools with supply chain scenario planning enables rapid analysis of tariff impacts, improving adaptability. Additionally, including the supply network in collaborative forecasting and capacity planning further strengthens the overall process, leading to better outcomes.
Leverage New Technologies for Optimization
Manufacturers have long leveraged technology to enhance supply chain capabilities. Initially, computer systems evolved from material requirements planning (MRP) to enterprise requirements planning (ERP) to optimize processes across the business. Demand planning was an early adopter of AI, utilizing advanced techniques like Bayesian Markov forecasting to improve forecast reliability. AI-driven anomaly detection has enhanced quality control, predicted deviations and improved supply chain data. Meanwhile, IoT has improved machine connectivity and business processes, enabling early warnings and automating execution.
In recent years, AI has emerged as a major disruptive force in supply chain management. Both traditional and generative AI are becoming embedded across organizations, increasing agility, enhancing performance and boosting employee productivity. This is especially crucial as the National Association of Manufacturers’ annual surveys consistently highlight a persistent shortage of skilled workers.
AI now offers even greater advantages, such as more accurate transit time predictions, improved supply chain risk identification, and enhanced demand forecasting through the integration of external data. AI-powered planning advisors help supply chain professionals analyze supply and demand data more efficiently, while AI-driven supplier onboarding accelerates quality assessment and data validation. With AI increasingly embedded in business processes, the potential for improvement is vast. Generative AI, in particular, will initially serve as an intelligent advisor — offering insights, feedback, first drafts, and fast, accurate responses — enabling better, faster decision-making. These advancements will make supply chains and their supporting networks more agile and responsive.
Build a Skilled Workforce
For years, surveys from the National Association of Manufacturers have highlighted a persistent shortage of skilled workers — a challenge that will become even more critical as AI adoption accelerates. To keep pace, employees will need to continuously develop new skill sets to enhance efficiency and adapt to evolving roles. While some may fear that AI will replace highly skilled supply chain professionals, the reality is that AI will likely raise the bar, requiring manufacturers to become even more agile and responsive.
Rather than replacing workers, AI will serve as an enabler — automating repetitive and mundane tasks so employees can focus on creative, strategic and complex problem-solving. A key skill for the future workforce will be understanding how to effectively integrate AI into business operations. Concepts such as digitalization and Manufacturing 4.0 will be essential for driving process connectivity and business transformation.
Beyond traditional skills like communication, supply chain management and data analysis, employees will need to develop expertise in leveraging AI to enhance decision-making and optimize supply networks. By mastering these new capabilities, they will play a vital role in transforming manufacturing operations, addressing future challenges and opportunities and ensuring they remain indispensable to the success of their organizations. M
About the author:
John Barcus is Group Vice President, Manufacturing Industries & Emerging Technologies at Oracle.
Smart Factories and Supply Chains Thrive with Connectivity
Unlock agility, visibility, and efficiency with smart manufacturing and connected supply chains powered by IoT, AI and advanced wireless tech.
TAKEAWAYS:
● Next-gen manufacturing thrives on IoT, Video Intelligence, and 5G—discover how these technologies drive real-time data insights and smarter decisions.
● AI, analytics, and digital twin solutions are revolutionizing smart factories—see why they’re essential for operational agility and efficiency.
● Legacy systems, labor shortages, and supply chain disruptions pose major hurdles—learn how manufacturers are overcoming these challenges.
Revolutionizing Manufacturing: Preparing for Manufacturing 4.0
In today’s dynamic manufacturing landscape, the creation and operation of smart factories require strategic, intelligent decision-making. The transition to Manufacturing 4.0 is more than just implementing new technology—it’s about leveraging connectivity, data, and advanced analytics to build resilient and efficient operations. Agility, visibility, and planning have become essential pillars for success in this evolving environment.
Envisioning the Ideal Smart Factory
The ideal smart factory is built on a foundation of connectivity and intelligence. A connected factory provides valuable data that empowers manufacturers to make informed decisions in response to market changes. With technologies such as IoT, Video Intelligence, and 5G, manufacturers can deploy predictive analytics to forecast demand, prevent downtime, and optimize overall efficiency.
A robust cybersecurity strategy is another critical component that must be approached with a layered mindset. Effective cybersecurity needs to extend beyond the factory floor, encompassing network-based defenses, premise-based protections, and cloud security considerations. This comprehensive approach ensures that remote workers, third-party vendors, and suppliers are safeguarded against vulnerabilities that hackers may exploit. As factories become more connected, security measures must evolve in tandem to include multiple layers of defense, ensuring data integrity and operational resilience at every level of the network infrastructure.
Addressing Challenges in Legacy Manufacturing
Transitioning from legacy manufacturing processes to smart factories presents several challenges, primarily in three areas: equipment, labor, and supply chain management.
Maintaining the efficiency and consistency of legacy equipment remains a top concern. Many manufacturers operate aging machinery that wasn’t originally designed for digital integration, making retrofitting with IoT sensors and analytics tools a necessary step.
Labor shortages also present a significant hurdle. The manufacturing sector is facing an increasing gap in skilled workers, particularly in North America. Digital transformation initiatives must include workforce development strategies to equip employees with the skills needed to operate and maintain smart factory technologies and the implementation of automaton to augment the workforce.
Finally, supply chain disruptions continue to create uncertainty. Fluctuations in material availability, transportation delays, and geopolitical risks highlight the need for better visibility and predictive planning. Leveraging digital tools to monitor and anticipate supply chain issues is crucial for maintaining smooth operations.
Prioritizing Technologies for Digital Transformation
For manufacturers looking to build the smart factory of the future, certain technologies must be prioritized to drive efficiency and resilience.
IoT is foundational to smart factory capabilities. By integrating IoT technology, manufacturers can collect and analyze machine data to reduce unplanned outages, extend equipment life, and optimize production workflows. These data-driven insights are key to enhancing operational agility.
Advanced analytics and big data also play a critical role. The ability to analyze IoT data alongside AI-powered video intelligence enables real-time, actionable insights. This enhances visibility across operations, allowing manufacturers to proactively adjust to changes in demand, supply chain disruptions, and equipment performance variations.
Innovative IoT Implementations in Manufacturing
Manufacturers are already embracing IoT solutions to enhance both factory operations and broader supply chain management. A significant portion of manufacturers use IoT technology in their logistics and supply chain processes, paving the way for AI and digital twin applications.
These innovations support safety and compliance monitoring, asset condition tracking, and sustainability initiatives such as reducing carbon emissions. Other notable implementations include fleet and vehicle management, smart IoT analytics powered by AI and machine learning, and video-as-a-sensor technology. AI-powered video analytics can identify risks, track asset activity, and improve inventory management—all contributing to greater visibility and operational agility.
The Role of Advanced Wireless Connectivity
Advanced wireless connectivity is pivotal in realizing the full potential of a smart factory, and it thrives on an evolution rather than a complete overhaul. Existing Wi-Fi infrastructure can be strategically augmented where cellular technology complements and enhances overall coverage, rather than replacing the current systems. This layered approach ensures that both indoor and outdoor connectivity needs are met efficiently.
Technologies such as 5G, edge computing, and advanced Wi-Fi work together to maximize flexibility and coverage in connecting data collection endpoints. By integrating these technologies with high-speed internet solutions like business fiber, factories can achieve real-time decision-making and seamless data exchange between machines, systems, and personnel. This harmonious blend not only optimizes connectivity but also drives the factory towards greater operational efficiency and innovation. More importantly, enhanced connectivity extends beyond the factory floor. It enables remote monitoring, facilitates collaboration between global teams, and strengthens coordination across supply networks. A strong digital infrastructure ensures that manufacturers can build agile, responsive operations that are prepared for future challenges.
Navigating the Smart Factory Journey
Manufacturers are at different stages of their digital transformation journey. Some are in the early phases, assessing their current capabilities and mapping out their strategy. Others have integrated IoT and analytics but are working to improve supply chain visibility. Some are further along, scaling smart factory initiatives with AI-driven automation and predictive analytics.
Regardless of the starting point, success in Manufacturing 4.0 comes down to a clear vision, strategic technology investments, and a commitment to continuous improvement. By focusing on agility, visibility, and planning, manufacturers can build smarter, more resilient operations that are ready for whatever comes next. M
About the author:
Ande Hazard is Vice President, Global Enterprise Solutions, Manufacturing & Transportation, AT&T Business
Resilient Supply Chains and the Digital Thread
Strengthen your supply chain by applying digital thread principles to your data.
TAKEAWAYS:
● Lean Principles Drive Performance: Implement lean principles focused on material handling, transport, and inventory management is the cornerstone of cost reduction and performance enhancement.
● Metrics Enhance Comprehensive Insight: Evolve the development of metrics enabling comprehensive reporting and insights into supply chain performance, enhancing strategic decision-making.
● Integrated Redesigns Extend Beyond Silos: Shift from isolated efficiency gains to structural redesigns that improve demand-supply alignment, production, and fulfillment processes across entire organizations, significantly transforming operations post-pandemic.
Applying lean principles to supply chains, especially to material handling, transport, and inventory management together has been the foundation for most cost and performance improvements for the last 30 years. Metrics, like return on working capital and inventory turnover, have been developed for comprehensive reporting of supply chain performance.
Advancements in data management, usage and integration over the last decade have broadened the sources of supply chain performance improvement from functionally siloed efficiency gains to structural redesigns that span organizations. Regardless of industry, demand-supply alignment, production, warehousing, and fulfillment functions operate much differently today than they did a decade ago, or even before the pandemic.
Why?
One dominant reason is the adoption of industrial digital thread principles in supply chain management. These principles have helped supply chain data become more accurate, valuable, and broadly deployed to drive business improvement.
A digital thread is the real-time, omnidirectional flow of richly contextualized data between and among networked or meshed supply chain nodes.
Digital threads have evolved from focusing on product data to including product, process, commercial, and logistical data across wider supply chain ecosystems, particularly in mesh networks.
Today’s supply chain professionals often observe that logistics, visibility, capacity, and inventory data drive greater business efficiency. Data are more fully monetized than ever before.
As companies revisit overall supply chain strategies, misalignments among supply chain network capacities, inventories, and information have led many companies and their supply chain partners to reconstitute their integrated supply chain operations, often beginning with their data architectures and models.
In response to these challenges, manufacturers today are embedding industrial digital thread principles and data characteristics in their supply chain operating models. These often include:
- Seamless flows
- Real-time access
- Structured collaboration
- Consistent formats
- Full traceability
- Case-based contextualization
Investments in these capabilities offset risks and enhance operational agility. For example, real-time data and advanced analytics together enable early identification of potential disruptions and provide better understanding of supply chain impacts before the event(s) occur. This is crucial for making informed, preemptive decisions.
Applying Digital Thread Principles to Supply Chain Management
Many companies have viewed digital transformation as a “one-stop-shop” solution to achieve more resilient supply chains. The same is true for the application of digital thread principles. Blindly adopting new technologies without a cogent strategy that focuses on the data and its secure, but fluid, movement between supply chain participants often produces less than optimal results.
Instead, for high-value operations, organizations must complete three steps for applying digital thread principles within and across the supply chain functions where the greatest opportunities for improvement in resiliency are thought to exist.
- Measure and Diagnose: Evaluate current processes and identify opportunities.
- Design and Build: Deliver results to show immediate business impact.
- Implement and Measure (Repeat): Refine solutions through continuous monitoring and optimization.
To illustrate the application of digital thread principles, we consider two high-value supply chain operations that often determine overall supply chain resiliency:
- Demand–Supply Alignment
- Inventory Management: Material and Finished Goods
Digital Threads in Demand–Supply Alignment
Even in today’s highly integrated data environments, the timely and efficient exchange of accurate, properly contextualized demand (forecast) and supply (replenishment) data between trading partners remains a primary, sometimes elusive, goal of supply chain leaders.
Optimal demand–supply alignment maximizes on-time fill rates while reducing raw material and finished goods inventories.
Safety stocks and buffers across the supply chain may be responsibly reduced, as confidence in the accuracy of demand and supply data integration and analysis improves.
How may digital thread principles be useful in achieving these goals?
Here are some questions to ask, and suggestions to consider that are connected to the three steps for applying digital thread principles.
Measure & Diagnose:
- Seamless flows: Are demand signals received from authoritative sources without delay or modification? Similarly, are supply/replenishment triggers timely, accurate, and received into the demand–supply alignment activity without need of changes to the make the data suitable for planning purposes?
- Real-time access: Even if they are aggregated later, is access to current data available in real-time?
- Consistent formats: Is the form and content of demand and supply data consistent across all sources? That is, are units of measure and product references consistent?
Now, apply these findings to the design of data connections and flows grounded in digital thread principles.
Design & Build:
- Goal-focused design: Digital thread principles in demand–supply alignment smooth the exchange of consistently formatted, properly contextualized authoritative data to leaders of production operations and material management.
- Standardized data architectures: Adopt a unified namespace (UNS) or equivalent structure. Focus on contextualization to improve collaboration efficiency between demand and supply process owners.
- Alignment between demand–supply processes: Processes using data configured to digital thread principles are more capable of accommodating disruptions, unusual events, and other irregular operating conditions.
Remember, the hallmark of a resilient supply chain is its ability to return to regular operations.
Implement & Measure:
- Demand–supply alignment processes that encourage collaboration: To provide value, IT systems leverage contextualized data from forecasts, planning systems, capacity and production plans, logistics and warehouse management systems, and other data sources. Data flows, analysis results, action recommendations, and reports become more valuable when they leverage data procured through digital thread principles.
- Data models architected with digital thread principles: These models are better able to support demand–supply alignment processes and deliver supply chain performance goals. Keep the focus on the alignment process and desired outcomes, instead of on manipulating and managing the data.
Digital Threads in Inventory Management
A well-known operations management principle posits that production capacity, inventory, and data are interchangeable. Of course, the most efficient and valuable operations are those which maximize the value and utility of data, in exchange for optimized inventories and manufacturing infrastructures.
That proposition applies to the digital thread for optimizing inventory and streamlining the management processes associated with it, especially at the bookends of raw material (RM) and finished goods (FG).
No other core contributors to supply chain resiliency have more sources or more diverse sets of data than inventory management.
How may digital thread principles contribute to optimization of raw material and finished goods inventory across the supply chain?
Using the three steps, here are some more suggestions to consider.
Measure & Diagnose:
- Inventory management metrics: Diagnose supply chain issues and quantify weaknesses or gaps in data, its form, content, or contextualization.
- Thorough root cause analyses (RCA) of inventory excursions: Identify data and IT system operating gaps to be addressed through digital thread principles like timeliness, accuracy, and contextualization.
- RCA results: Prioritize these results for changes to data models and applications of digital thread principles to available data to drive the greatest and/or most rapid improvements in RM and FG inventory performance.
Design & Build:
- Evaluation and prospective redesign of data models: Efficient integration of digital thread principles into inventory management processes and their IT applications requires evaluation and prospective redesign of data models within the capabilities of IT systems.
Experience suggests most of the new digital thread data, or additional detail for current data, will be directed toward contextualization, since inventory management performance issues often result from incomplete data models or incorrect ancillary data.
Implement & Measure:
- Complete and contextualized data architectures: Data architectures that focus on completeness and contextualization improve the performance and value of inventory management systems and processes.
- Inventory management processes and systems: These leverage large volumes of data from diverse sources, including suppliers, factories, distribution providers and customers. The rich data structures and system connectivity enabled by digital thread principles help maximize the operational value of both RM and FG inventory management tools.
- Contextualized inventory data: Contextualization of inventory data provides material managers greater situational awareness and more comprehensive data upon which to act.
Closing Recommendations
Adopting industrial digital thread principles is essential for creating a resilient supply chain network, as they enhance the accuracy and usability of data, driving significant business improvements in a dynamic marketplace.
– Consider inclusion of digital thread principles in process, solution, and technology architectures spanning your supply chains.
– Evaluate the sufficiency of your current data architectures, models, and operations against supply chain performance.
– Determine the role of data form, content, context, timeliness, and other digital thread principles in mitigating the identified deficiencies. Determine if gaps are rooted in business applications, technologies, infrastructures, or data. M
About the author:
Jeffrey Miller is Industry Principal Lead for Kalypso, a Rockwell Automation Business
Germany, Canada Push Back on U.S. Policies at Opening of Hannover Fair
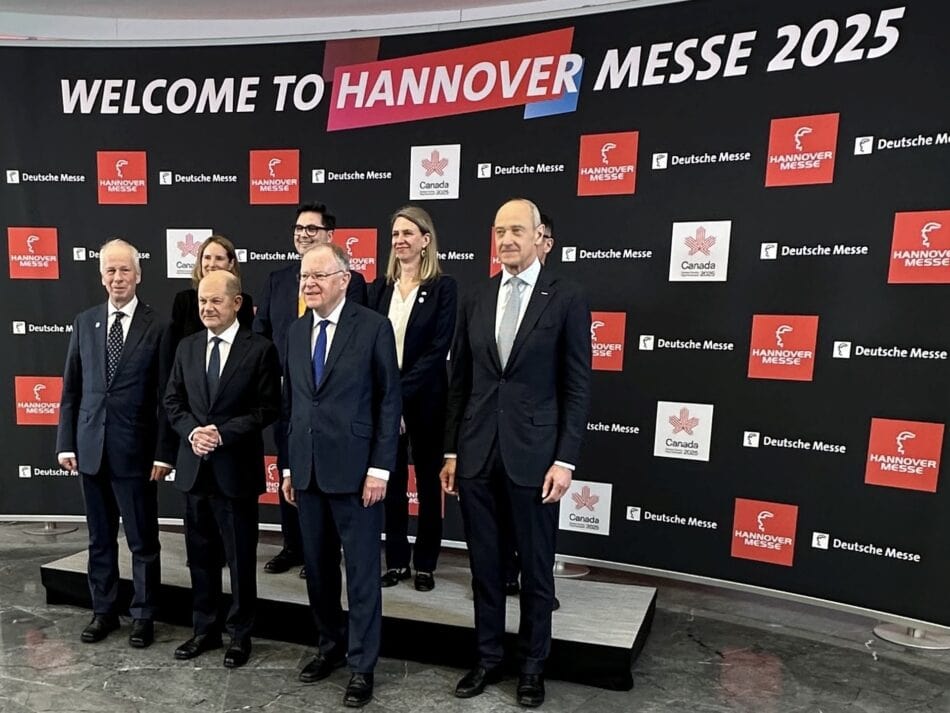
Geopolitics took center stage at the opening ceremonies of the Hannover Fair in Germany last night, as German and Canadian government and industry officials criticized U.S. policy on tariffs and trade and declared their support for the independence of Canada.
“Rarely has there been so many political messages at a Hannover Fair,” said German Chancellor Olaf Scholz. “Trade wars have no real winner, not even the U.S. Europe’s goal is cooperation. But if there is no chance of this, we will act as a unified front.”
Even though Scholz and other speakers did not mention the Trump Administration by name, their messages were clearly targeted at the tariff, trade, and defense polices of the new U.S. administration. Phrases such as “open markets”, “reliable partners”, “respect for neighbors”, and “stable environments” dominated the opening ceremony speeches.
President Donald Trump’s statements about Canada, the partner country for this year’s Hannover Fair, becoming the 51st state of the U.S. received pointed rebukes.
“Canada is not a state of any other nation,” said Scholz. “It will never be part of the U.S.”
It is customary for the Hannover Fair partner country to have its head of state or government participate in the Fair’s opening ceremonies in person. Because Canada is in the midst of a national election, the new Prime Minister, Mark Carney, could not attend. Instead, Stephane Dion, Special Envoy to the European Union and Europe, spoke at the ceremonies, emphasizing Canada’s commitment to free trade, its reliability as a partner, and its willingness to strengthen ties with friendly nations.
“Canada is an ally, a friend,” Dion said. “We believe in win/win agreements. We have respect for international law and mutual trust.” With regard to trade relations with Germany, he said: “We knew we liked each other; now, we know we need each other.
But it was also clear from the speeches at the opening ceremonies that the countries and their industrial companies are now operating in a new environment. Siemens AG CEO Roland Busch said the new geopolitical environment is an opportunity Germany must seize.
“The operating system of the world is becoming obsolete,” he said. “It is time for a new one. We must re-invent how we grow together. Germany has been held back by excessive bureaucracy. We need less and more and faster innovation.”
Busch also addressed a major focus of the Hannover Fair this year – artificial intelligence.
He said companies won’t succeed by just adding AI into what they are currently doing. They have to re-think their processes and rebuild. He also warned about the stakes of not moving aggressively to adopt and learn about AI.
“In a few years from now, there will be a divide between those that embrace AI and those that don’t,” Busch said. “This may be the last generation of managing companies with just humans.”
Last night, Siemens won the Fair’s coveted Hermes Award for its Industrial Co-Pilot generative AI tool.
On Monday, the Hannover Fair exhibition opens. There are approximately 4,000 companies showing and demonstrating their technology and industrial products. About 130,000 people are expected to attend.
About the author:
David R. Brousell is the Manufacturing Leadership Council’s Founder, Vice President and Executive Director
Digital Transformation Sees Explosive Growth
Manufacturers are increasing their investments in digital assets, according to a recent survey from the Manufacturing Leadership Council, the NAM’s digital transformation division.
What’s going on: Due in large part to expectations of economic growth, manufacturers plan to either maintain or boost their spending on smart factory investments, they told the MLC in the recently published results of the Smart Factories and Digital Production Survey.
- Respondents also said they are optimistic about continued digitization and adoption, with 69% expecting moderate growth and no recession.
- While 28% would call their current operations “smart” or “somewhat smart,” 76% expect to be there in the next two years.
- Awareness of AI is growing by leaps and bounds among manufacturers; some 34% said they see AI as very significant. (Last year, just 10% said the same.)
Key points: The survey’s top takeaways include the following:
- Digital transformation is changing the game: Most manufacturers—60%—see digital transformation as something that is redefining the industry.
- More manufacturers are going digital: Some 75% of manufacturers say they are at “midlevel” digital maturity, up significantly from 2024 and 2023.
- AI’s role is inevitable: Fully 80% of manufacturers fully or partially agree self-managing and self-learning facilities powered by AI and machine learning are coming.
Manufacturing Leadership Council Elects Four New Leaders to Board of Governors
Washington, D.C. — The Manufacturing Leadership Council, the digital transformation division of the National Association of Manufacturers, has announced the election of four leading manufacturing executives to the MLC’s Board of Governors. The MLC is the nation’s leading networking and executive leadership organization dedicated to digital transformation in manufacturing by focusing on the technological, organizational and leadership dimensions of change.
The four new MLC board members include the following:
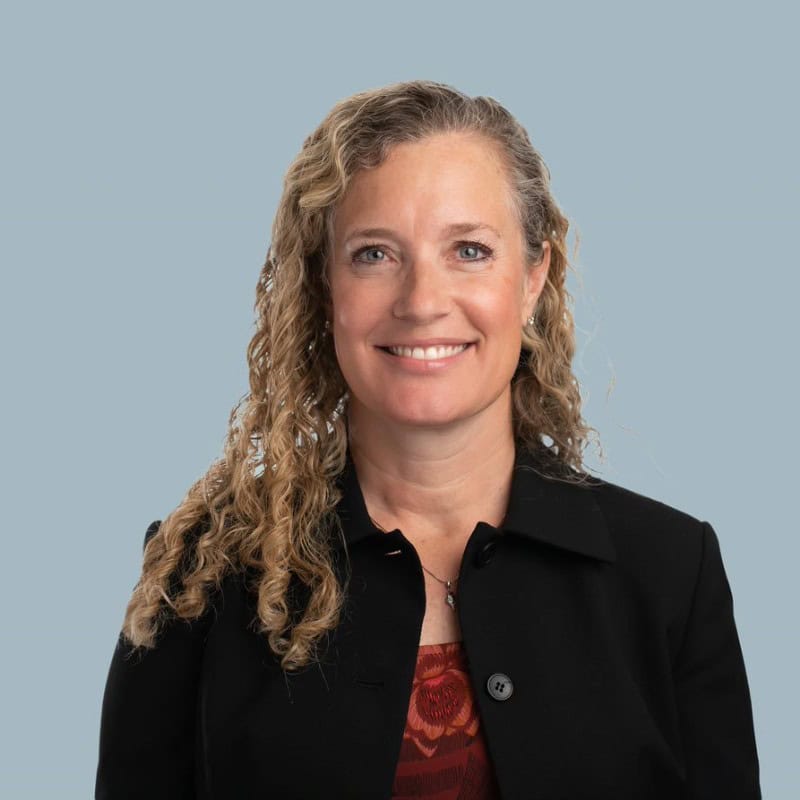
Melissa Boom, vice president, Business Excellence Systems, Winnebago Industries: In her role, Boom has designed and leads the Business Excellence Center of Excellence at Winnebago Industries, which enables the company’s businesses to partner and improve on techniques that drive value, reduce risks and increase synergies. This covers capabilities in business process, continuous improvement, industrial and manufacturing systems engineering, and quality systems.
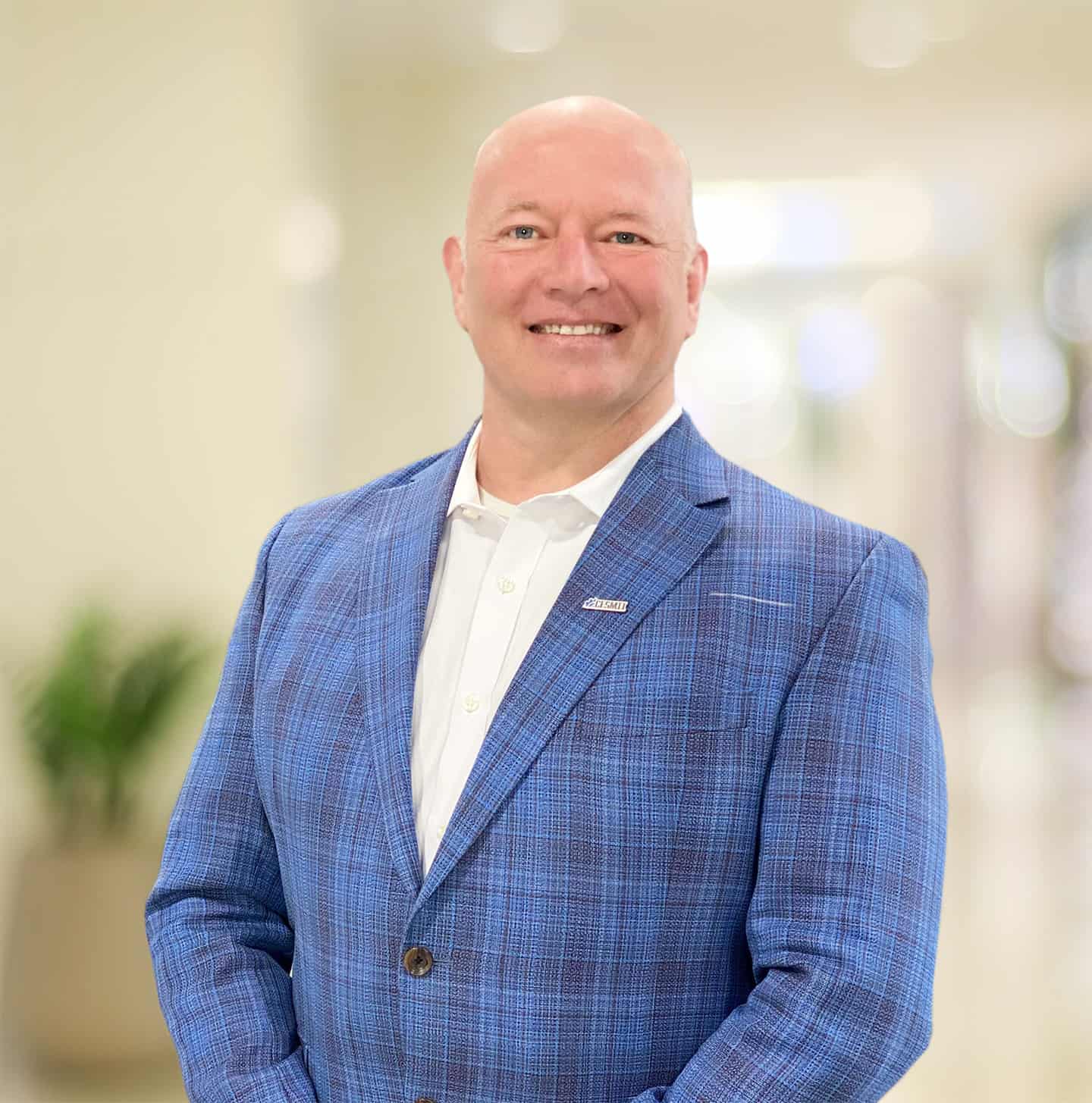
John Dyck, CEO, CESMII – The Smart Manufacturing Institute: Dyck’s leadership of CESMII focuses on outcomes that will benefit the nation’s energy and economic security by sharing existing resources and investing to accelerate development and commercial deployment of smart manufacturing capabilities. He is a renowned domain expert on both technology and business management and has pioneered the application of advanced digital technologies in manufacturing operations and supply chains.
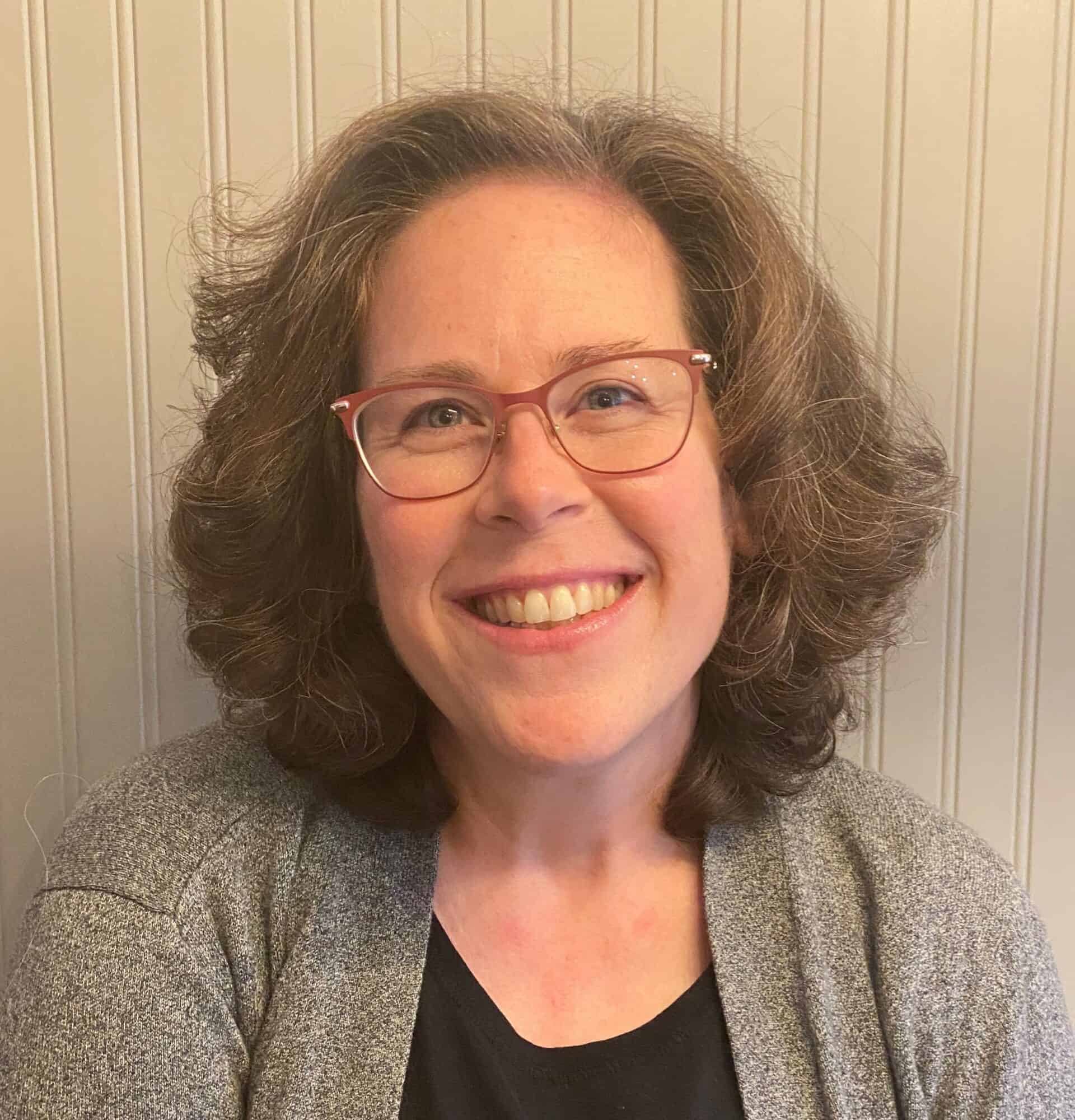
Regan Gallo, director of operations, Coated Abrasives NA, Saint-Gobain North America: Gallo has led operations for four different businesses at Saint-Gobain, in support of more than 40 manufacturing sites. She leads Saint-Gobain’s North American Operations Council, which brings together the company’s North American operations managers to share best practices and align on common operational standards in safety, HR, world-class manufacturing and Manufacturing 4.0.
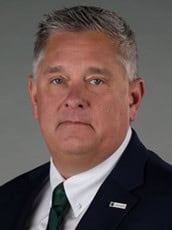
Billy Spears, senior vice president and chief product delivery officer, Lexmark International, Inc.: Spears is responsible for hardware and supplies development, supply chain, manufacturing and service delivery in his role with Lexmark. He also serves on the board for the Kentucky Chamber of Commerce and the Supply Chain Advisory Board for Eastern Kentucky University.
“Adding these distinguished manufacturing leaders to the MLC Board of Governors brings a wealth and depth of experience and knowledge that are critical to serving MLC members,” said Dan Dwight, president and CEO of Cooley Group and chairman of the MLC Board of Governors. “I am proud to welcome these new board members and look forward to collaborating with them to create a stronger future for the MLC.”
“Since its inception, the Manufacturing Leadership Council has always aspired to be at the forefront of digital operations, and to tap the industry experts who could help us meet that goal,” said David R. Brousell, founder, executive director and vice president of the MLC. “The newest additions to our board are essential to that mission and will ensure our place as the leading organization for digital manufacturing leadership.”
As an advisory body, the MLC Board of Governors provides guidance to the MLC on its annual Critical Issues agenda, research studies and programs and services for the MLC membership.
-MLC-
Founded in 2008 and now a division of the National Association of Manufacturers, the Manufacturing Leadership Council’s mission is to help manufacturing companies transition to the digital model of manufacturing by focusing on the technological, organizational and leadership dimensions of change. With more than 2,500 senior-level members from many of the world’s leading manufacturing companies, the MLC focuses on the intersection of advanced digital technologies and the business, identifying growth and improvement opportunities in the operation, organization and leadership of manufacturing enterprises as they pursue their journeys to Manufacturing 4.0.
Rethink 2025 Is Coming Up Fast
Get ready! Manufacturing’s leading annual event on accelerating digital transformation is right around the corner.
What’s going on: Rethink—held by the Manufacturing Leadership Council on Marco Island, Florida, each June—is a must-attend conference for anyone interested in Manufacturing 4.0 and where it’s headed (The MLC is the digital transformation division of the NAM.)
- This year’s event takes place June 15–18 at the JW Marriott Marco Island Beach Resort.
Why you should go: Rethink attendees will get an inside look at the cutting-edge processes and technologies transforming manufacturing today—directly from those creating and implementing them. They’ll also get a chance to:
- Consult with peers on manufacturing’s most critical initiatives, including smart factories and digital production, resilient supply networks and analytics and data mastery;
- Participate in real-time discussions and one-on-one meetings to help them understand how various solutions can solve their business problems;
- Hear from industry leaders and experts during panel discussions, executive interviews and more;
- Interact and collaborate with peers during interactive “think tank” sessions; and
- Hear from the MLC’s event partners during Rethink’s exclusive VIP Tour.
Who will be there: Scheduled speakers include Siemens USA President and CEO Barbara Humpton, Eaton Vice President of Industry 4.0 Craig Sutton, Hershey Company Vice President of Manufacturing, Operations Technology and Supply Chain Strategy Will Bonifant, Rockwell Automation Senior Vice President of Intelligent Devices Tessa Myers and many more.
The gala: Closing out the packed three-day event is the Manufacturing Leadership Awards Gala, at which the MLC will recognize award finalists and winners of the Future of Manufacturing Award, the Manufacturing Leader of the Year, the Small/Medium Enterprise Manufacturer of the Year and the Large Enterprise Manufacturer of the Year. The gala will take place on the evening of June 18.
Attend: Register online here for Rethink 2025. (NAM members get a discount at checkout.) Questions? Send them to [email protected].
The AI Glossary for Manufacturing Leaders: Key Terms You Need to Know
AI is revolutionizing manufacturing, but do you know the essential terms? This quick guide breaks down key technologies driving the future of industrial innovation.
As manufacturing leaders navigate Manufacturing 4.0’s complexities, artificial intelligence has emerged as a critical enabler of digital transformation. With AI evolving rapidly, staying on top of the latest terms and technologies can feel overwhelming.
To cut through the complexity, we’ve put together a quick guide to key AI concepts shaping manufacturing today. Whether you’re exploring predictive maintenance, product development, or human-machine collaboration, understanding these AI technologies will give you a clearer picture of their potential impact on your operations.
- Agentic AI: AI systems capable of autonomous decision-making and action-taking to accomplish goals, often integrating planning, reasoning, and adaptability to dynamic environments.
- Causal AI: AI that goes beyond correlation-based learning to understand cause-and-effect relationships, improving decision-making, diagnostics, and scientific discoveries.
- Edge AI: AI that runs on local devices rather than centralized cloud servers, enabling real-time processing and low-latency applications in areas like IoT, industrial automation, and smart devices.
- Generative AI: AI models that create new content, such as text, images, audio, or code, based on training data. Examples include ChatGPT for text and DALL·E for images.
- Large Language Models/Small Language Models: LLMs are advanced AI models trained on vast amounts of text to generate human-like language, while SLMs are smaller, more efficient models optimized for specific tasks with lower computational requirements.
- Machine Learning: A subset of AI that enables systems to learn from data, identify patterns, and make decisions with minimal human intervention. It includes supervised, unsupervised, and reinforcement learning techniques.
- Natural Language Processing: AI focused on enabling computers to understand, interpret, and generate human language, allowing for applications like chatbots, translation services, and sentiment analysis.
- Physical AI: AI integrated into physical systems, such as robots or autonomous vehicles, enabling interaction with the physical world through sensors, actuators, and adaptive control.
- Vision Systems: AI that processes and interprets visual data from the world, such as images or videos, enabling tasks like facial recognition, object detection, and quality control in manufacturing.
Scenes from MLC’s AI Conference
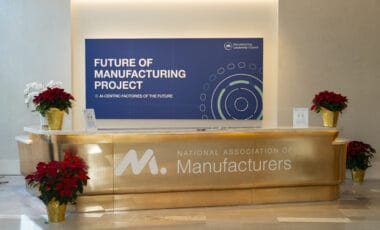
The opportunities and challenges of applying artificial intelligence in manufacturing operations were explored at MLC’s recent event in Orlando.
More than 190 manufacturing executives gathered in Orlando in early December of last year to talk about AI-Centric Factories of the Future. More than one dozen case studies, panel discussions, and presentations were delivered at the one-day conference, which was part of the Manufacturing Leadership Council’s Future of Manufacturing Project.
The goal of the Project is to help manufacturing executives understand the potential of advanced technologies to improve their operations in the years ahead.
The following are photos from the Orlando conference. MLC members can access full videos of the sessions depicted in the photos by going to the MLC Member Resource Center: https://manufacturingleadershipcouncil.com/member-dashboard/resource-center/resource_type/future-of-manufacturing-project/
Photos by David Bohrer, Senior Director, Photography, at the NAM.
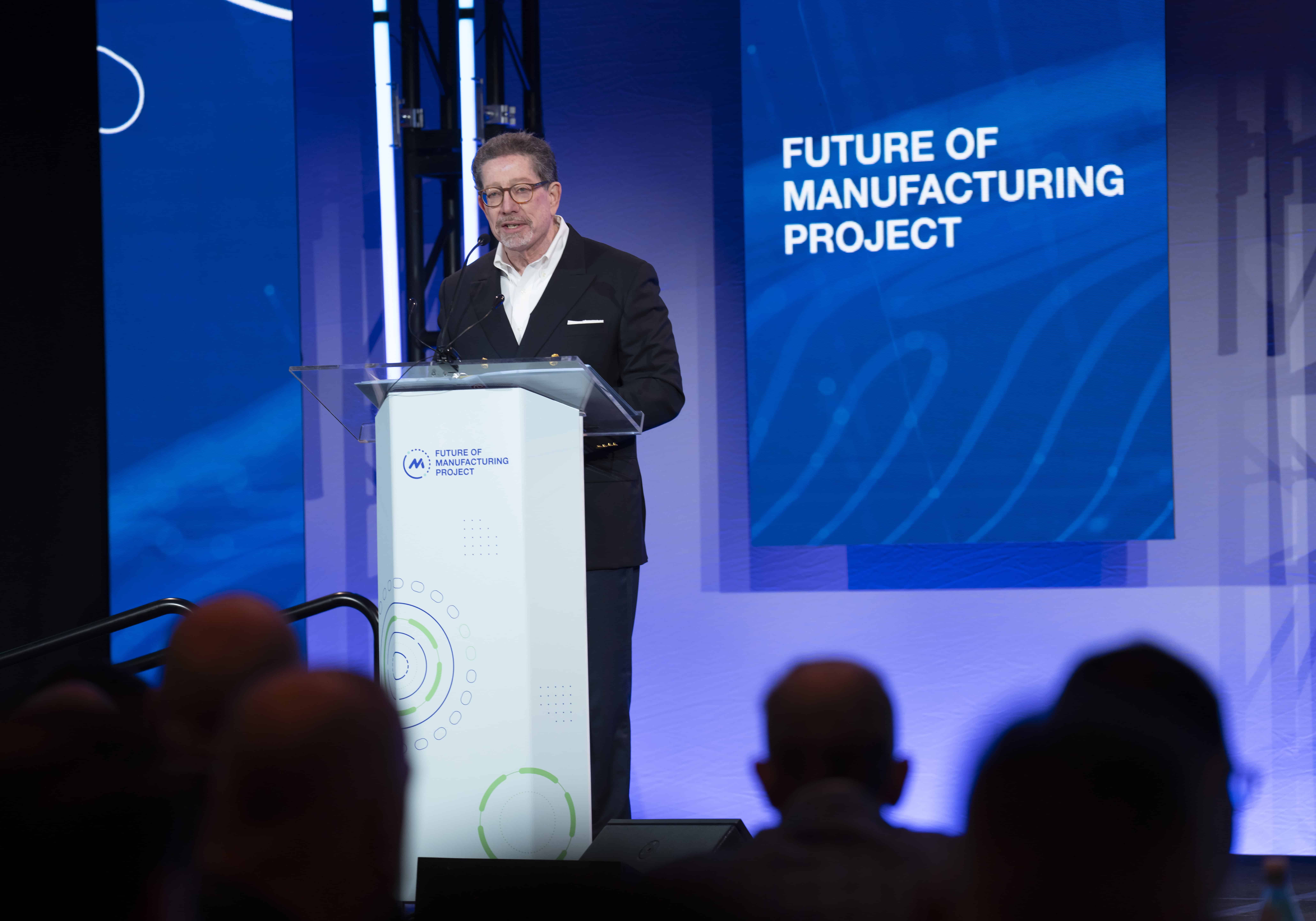
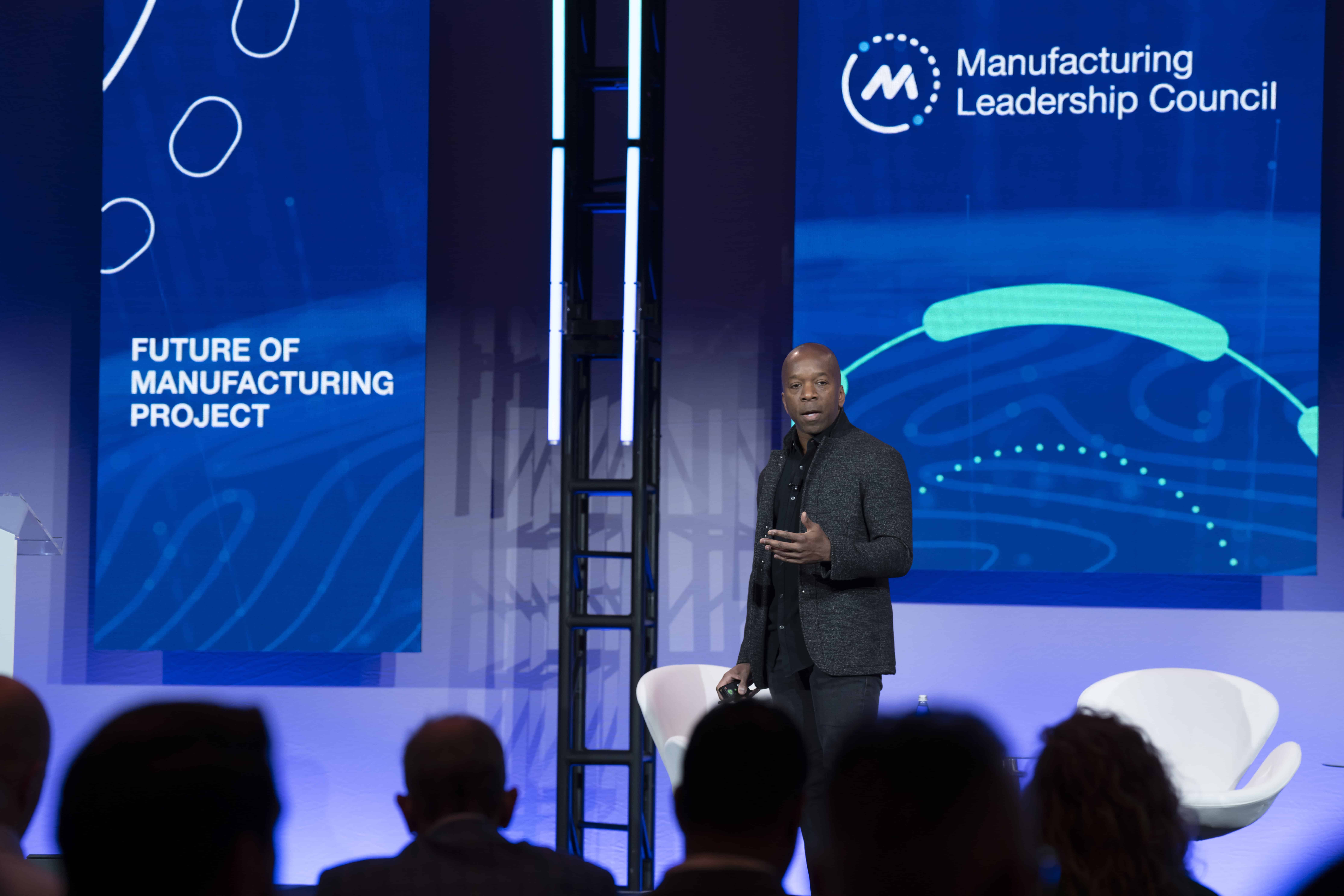
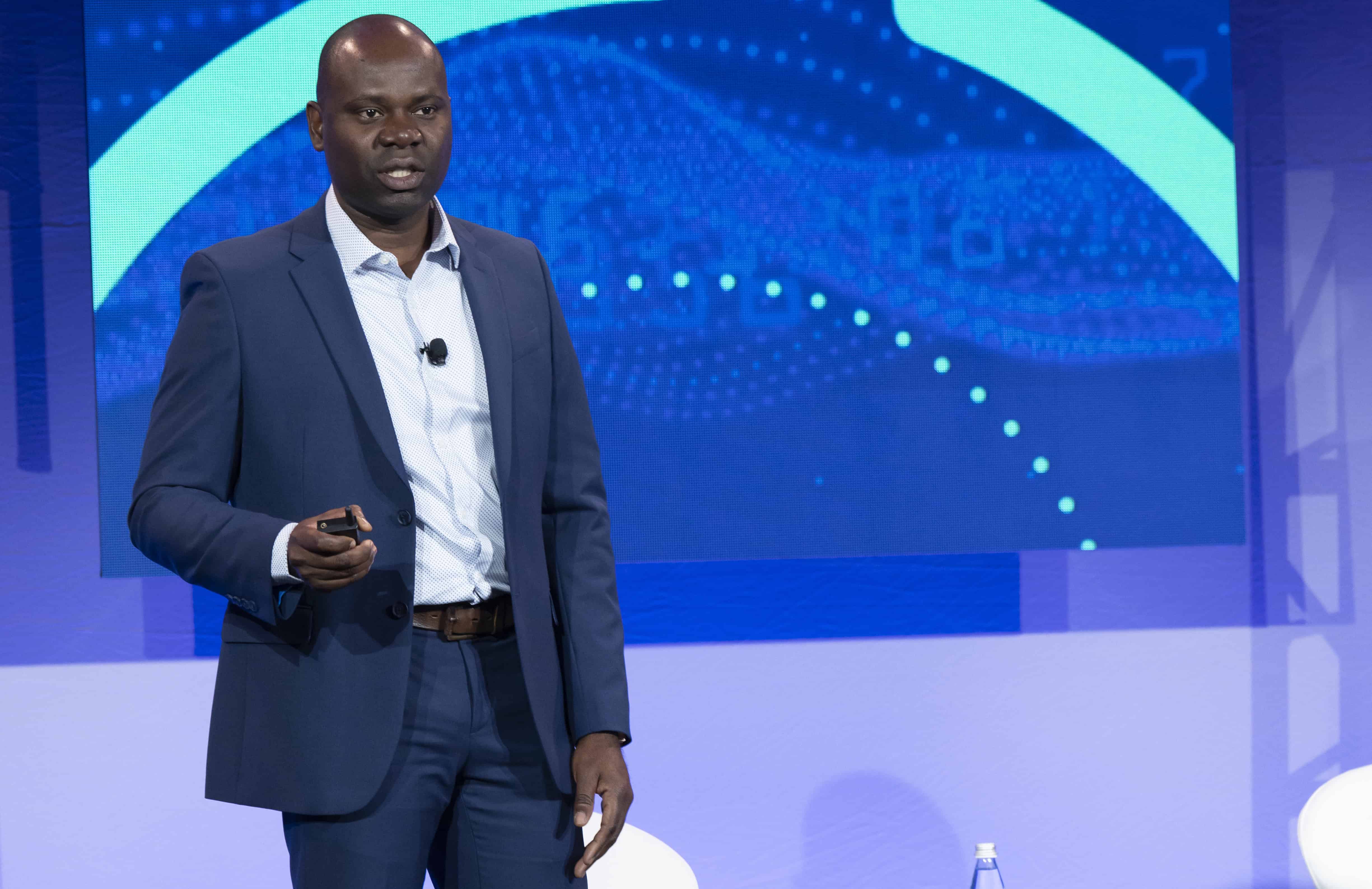
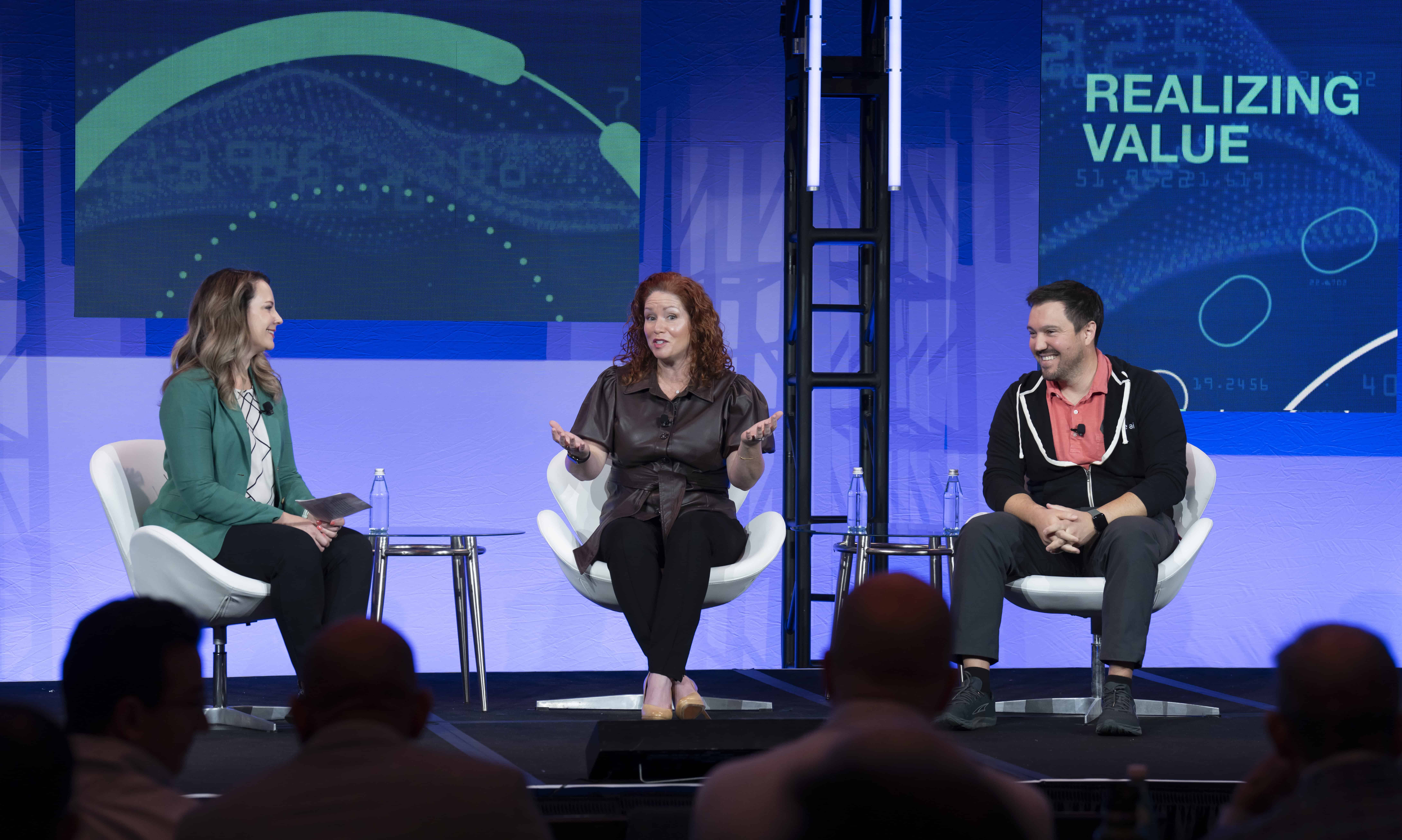
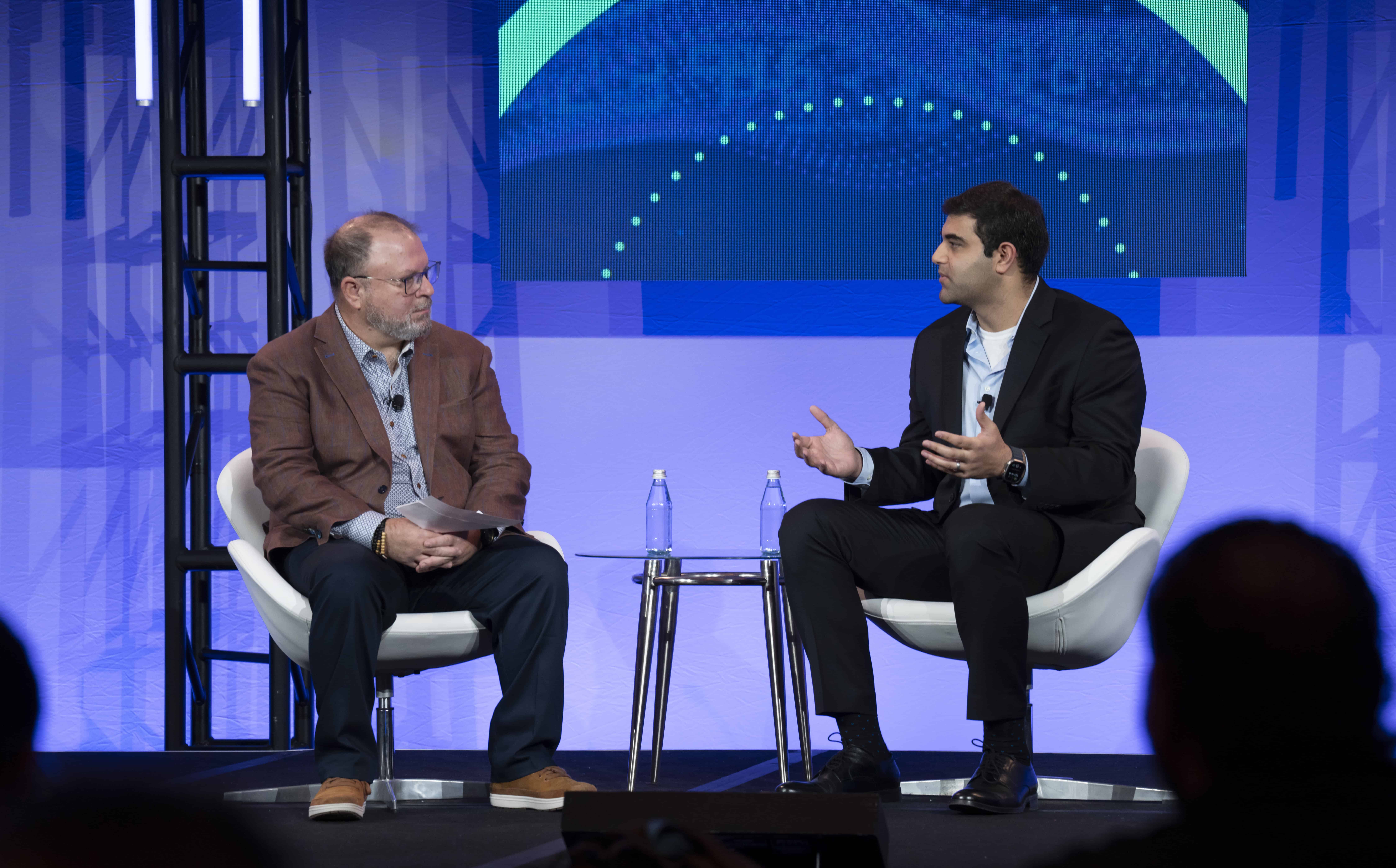
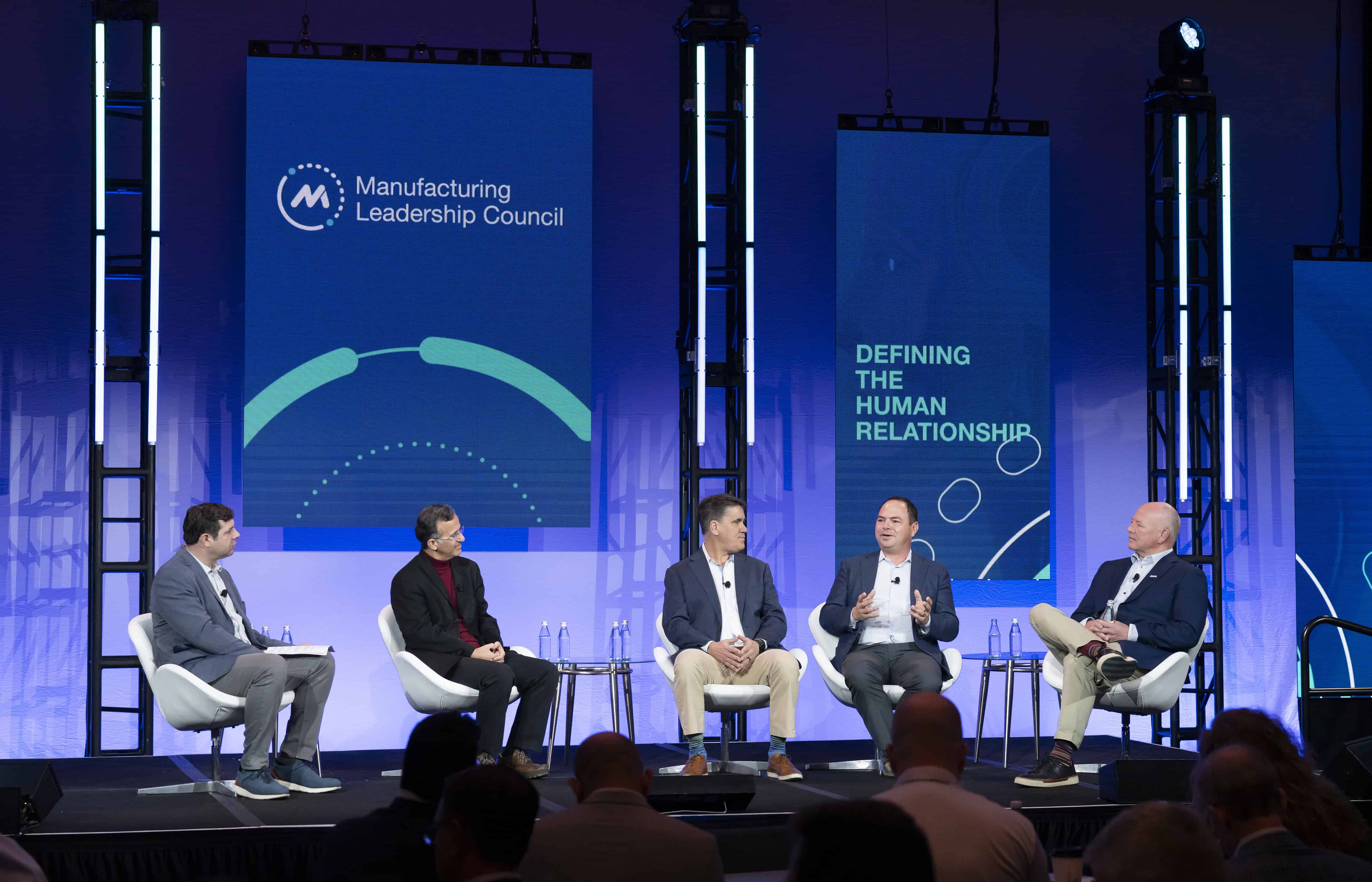
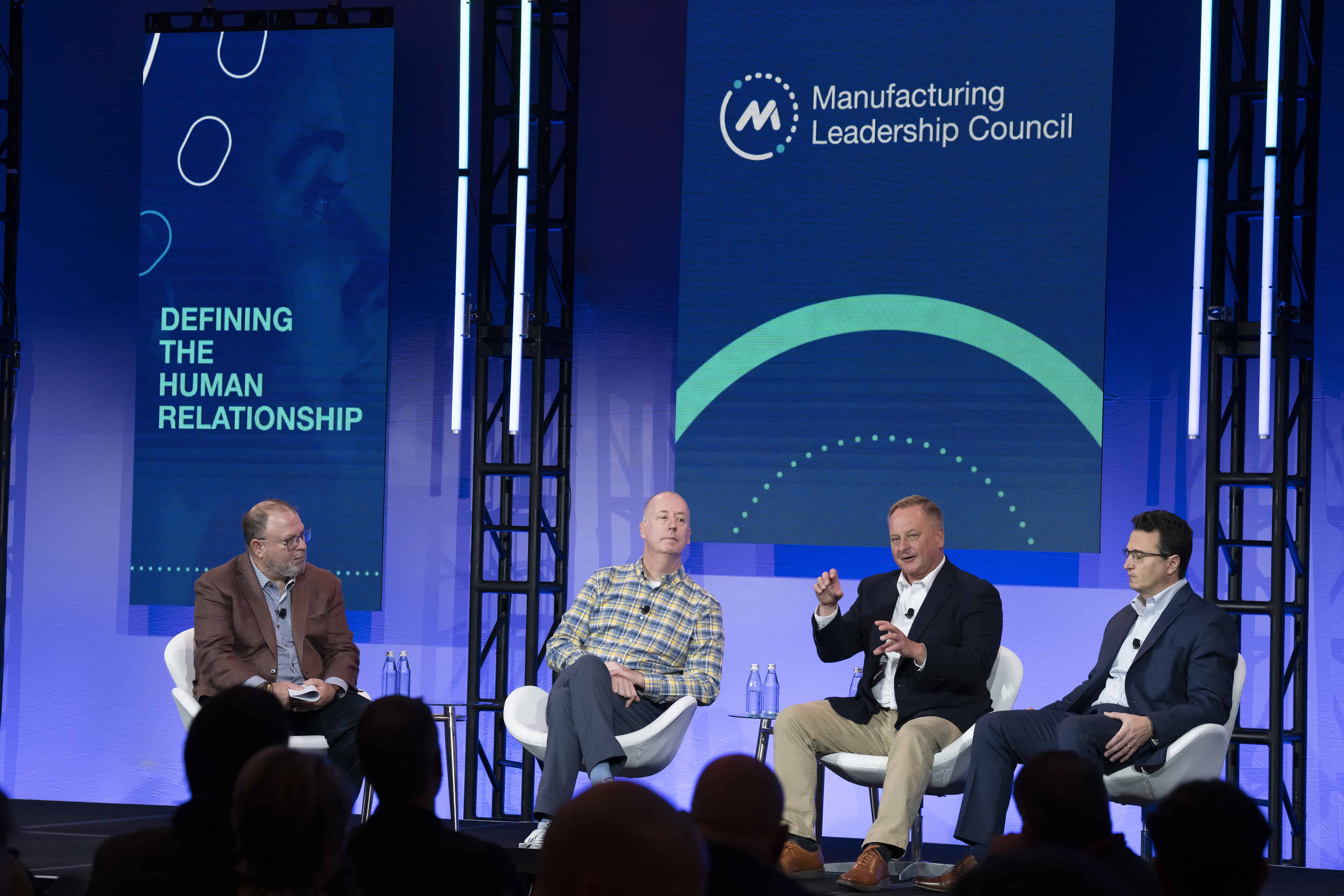
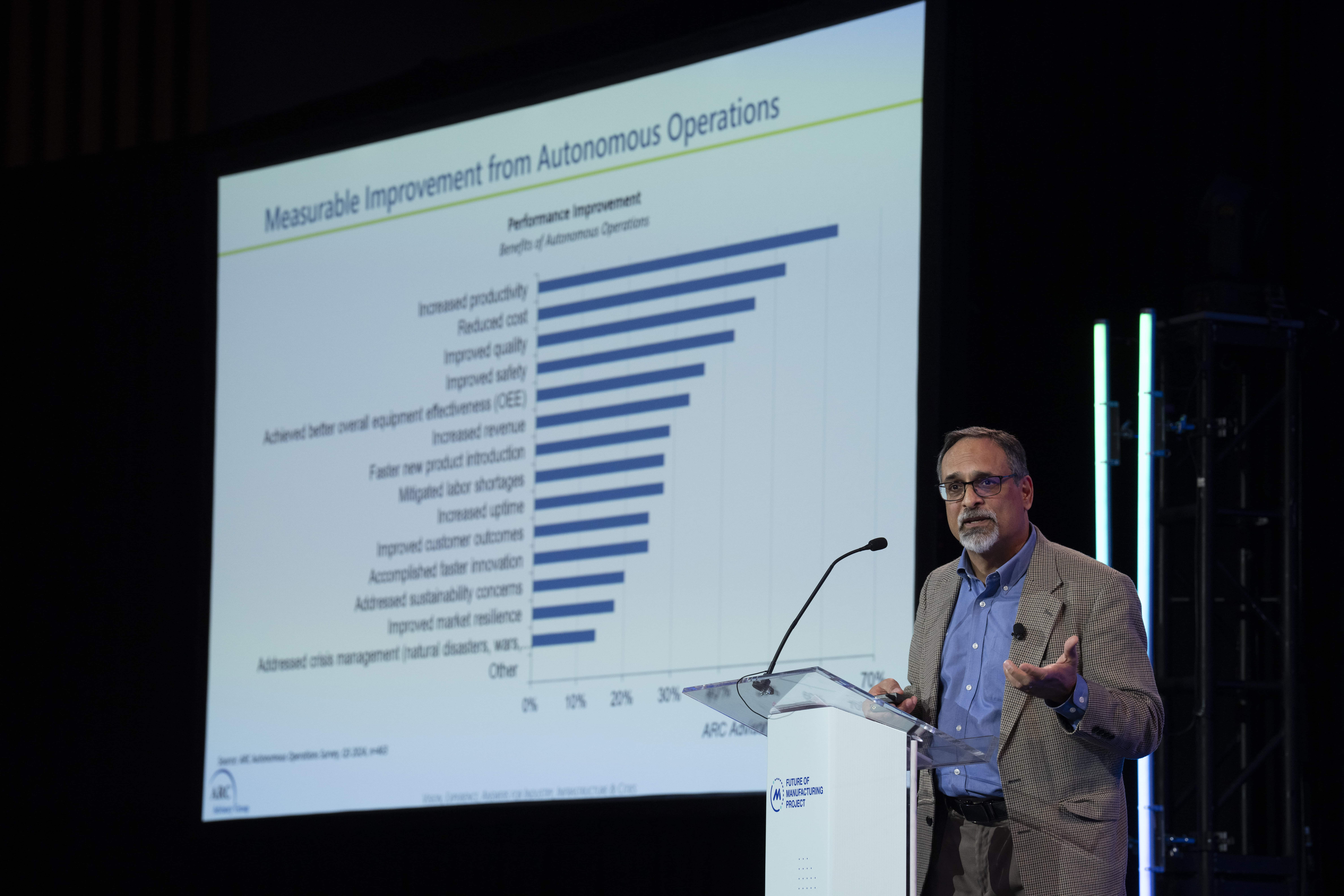
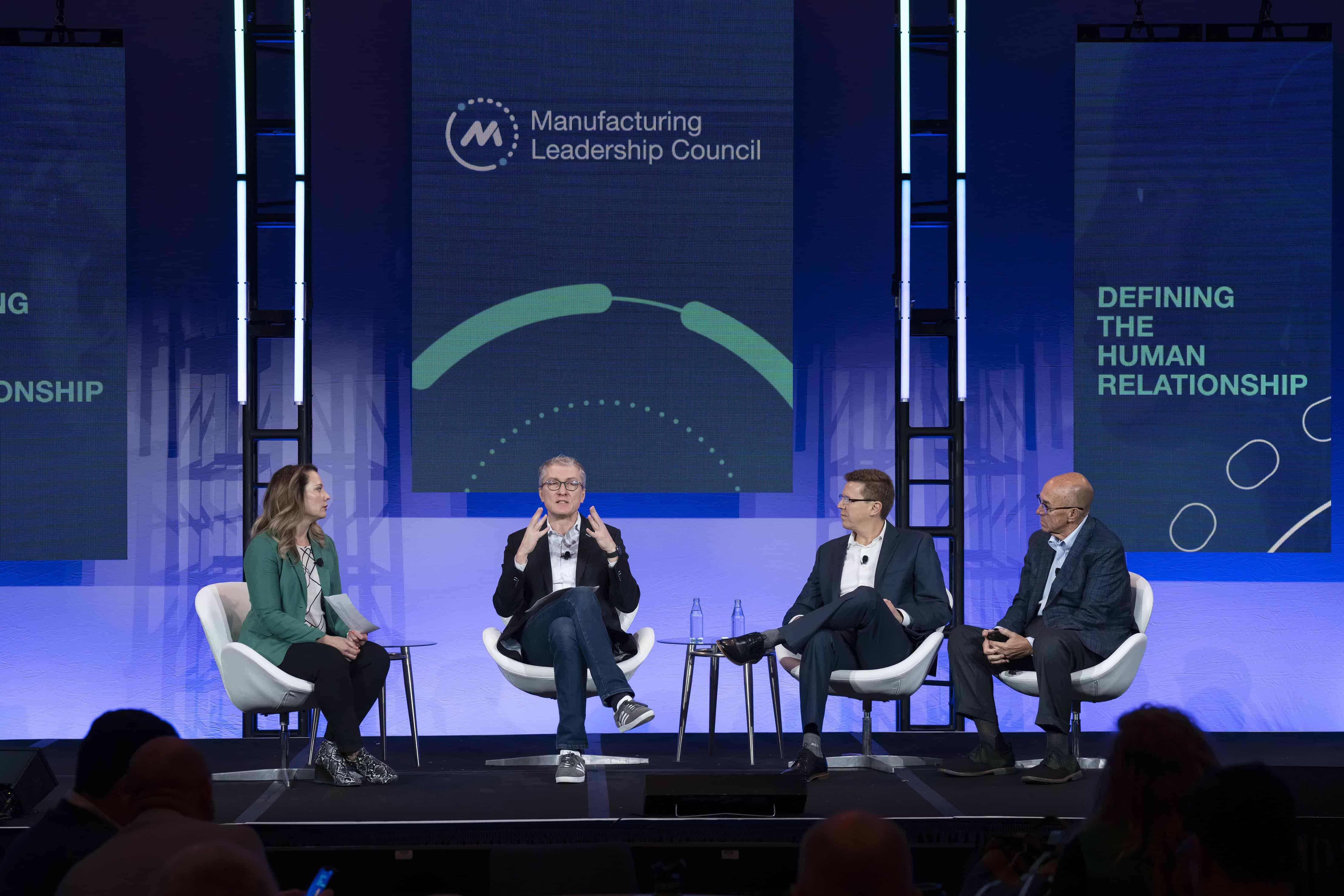
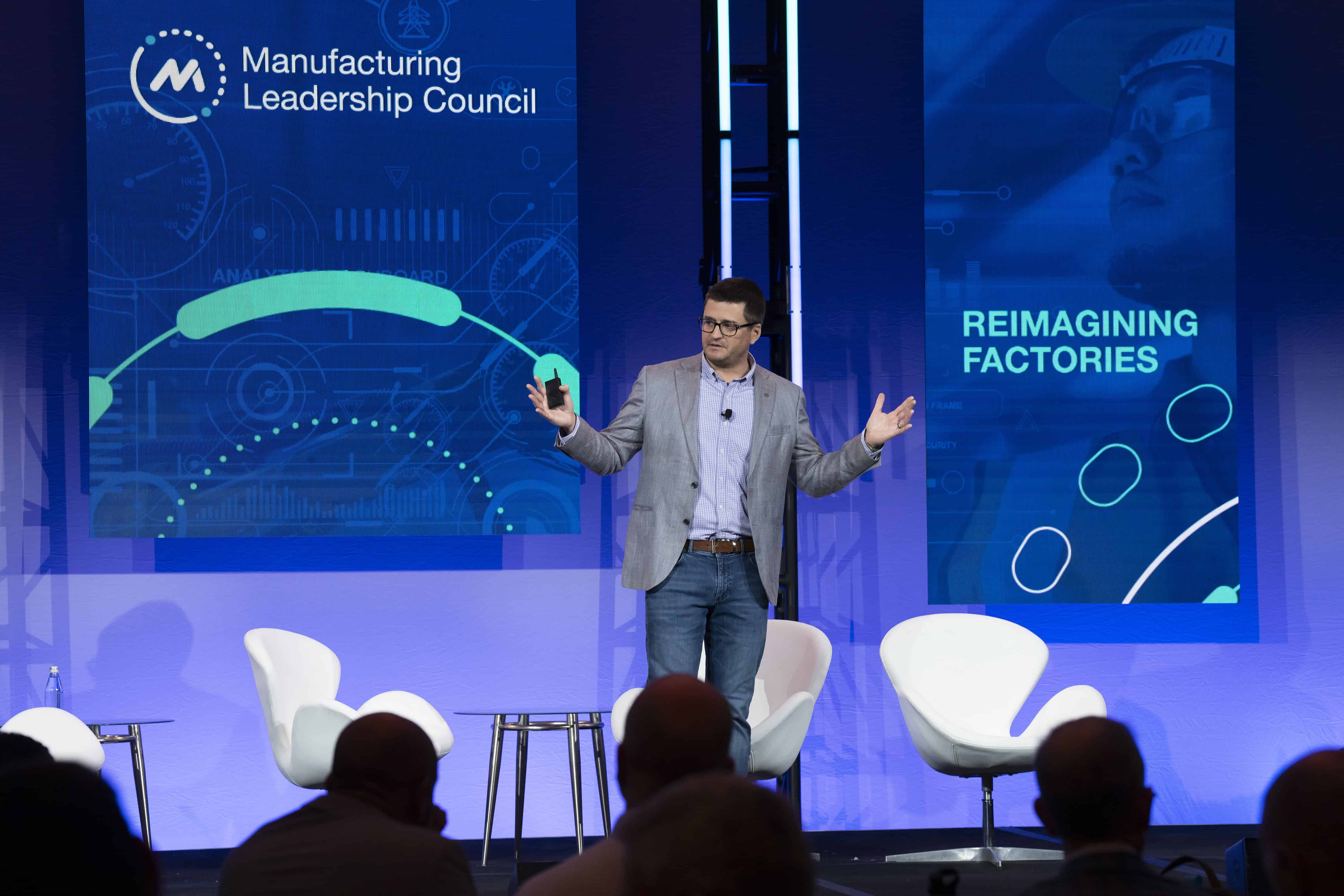
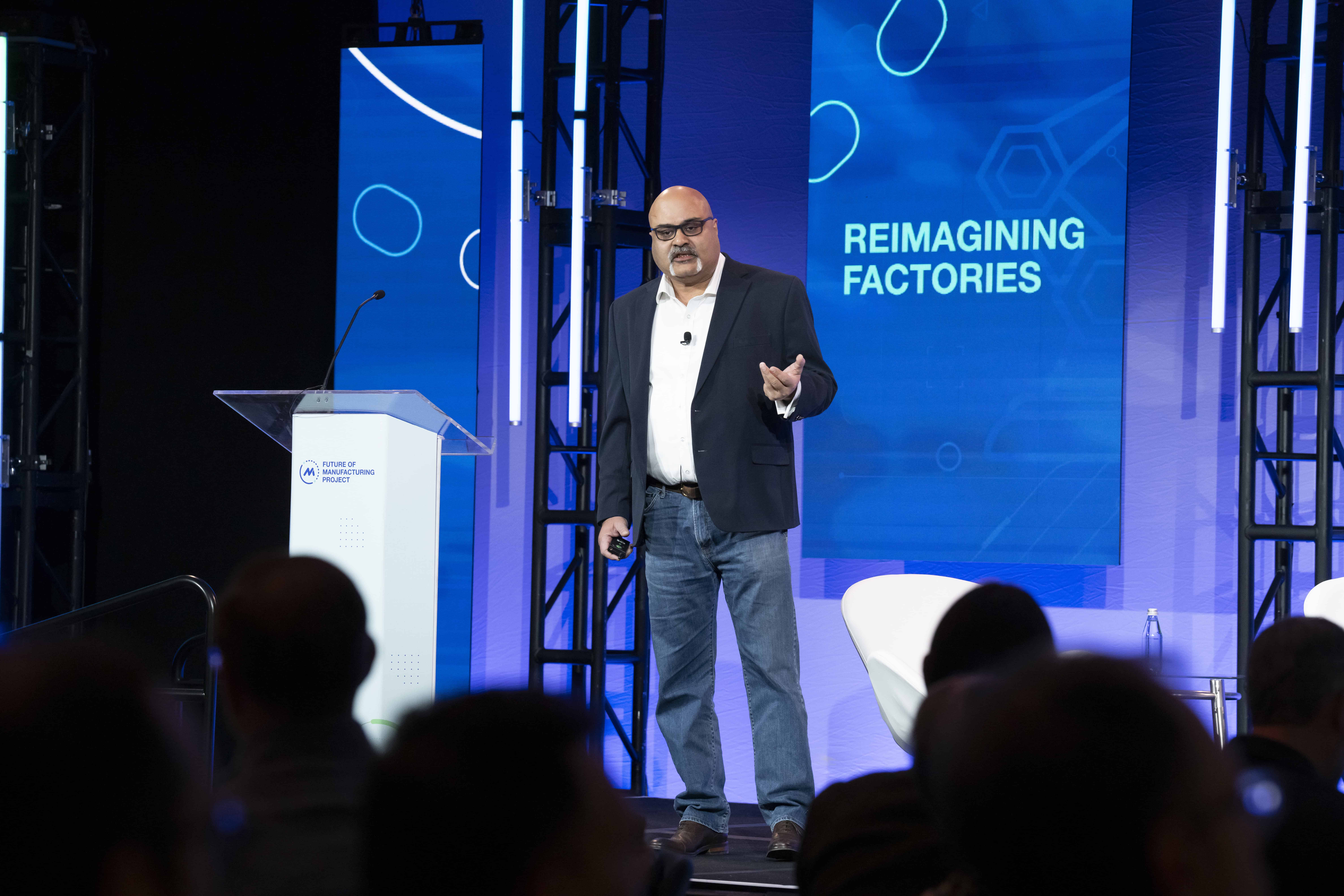
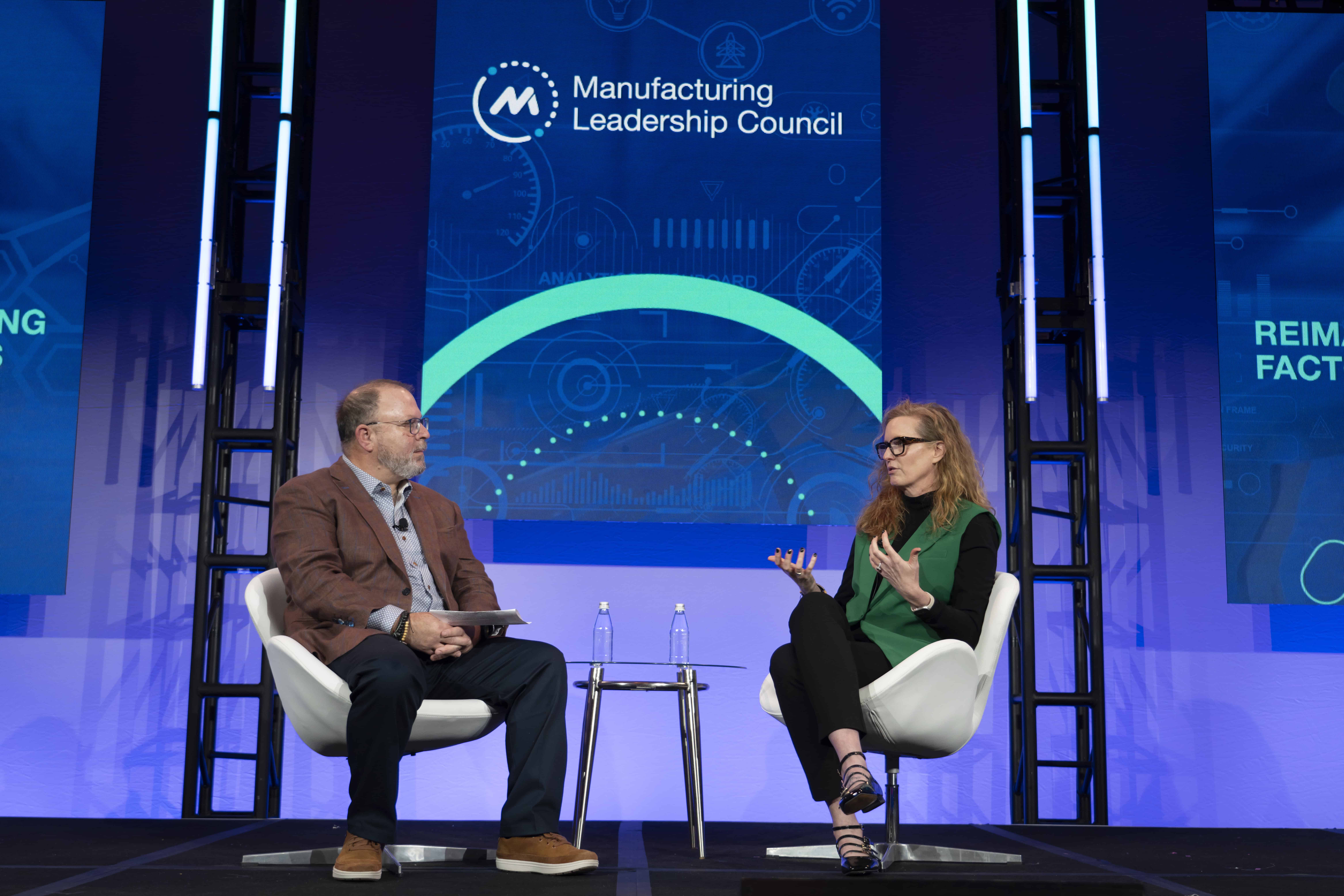
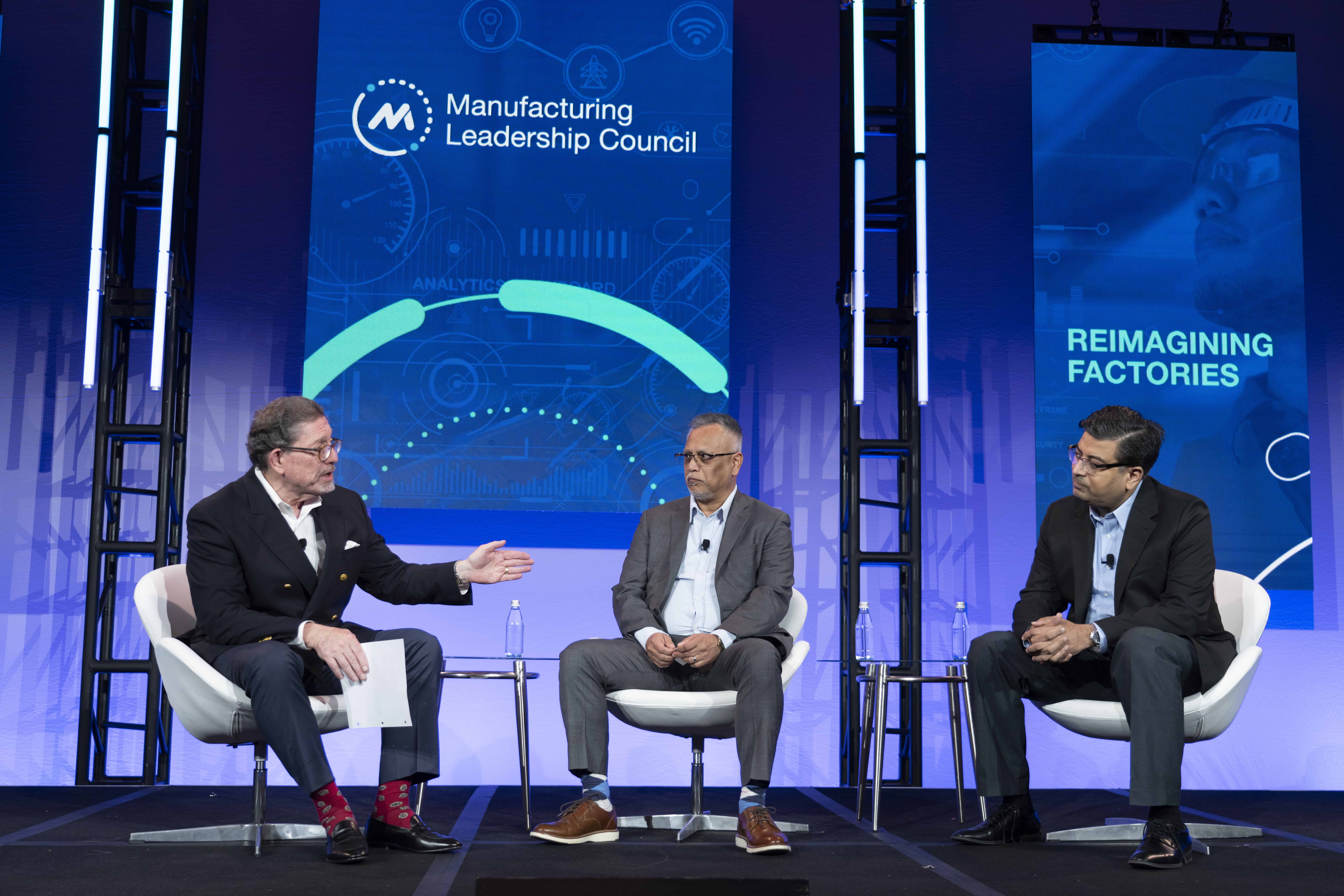
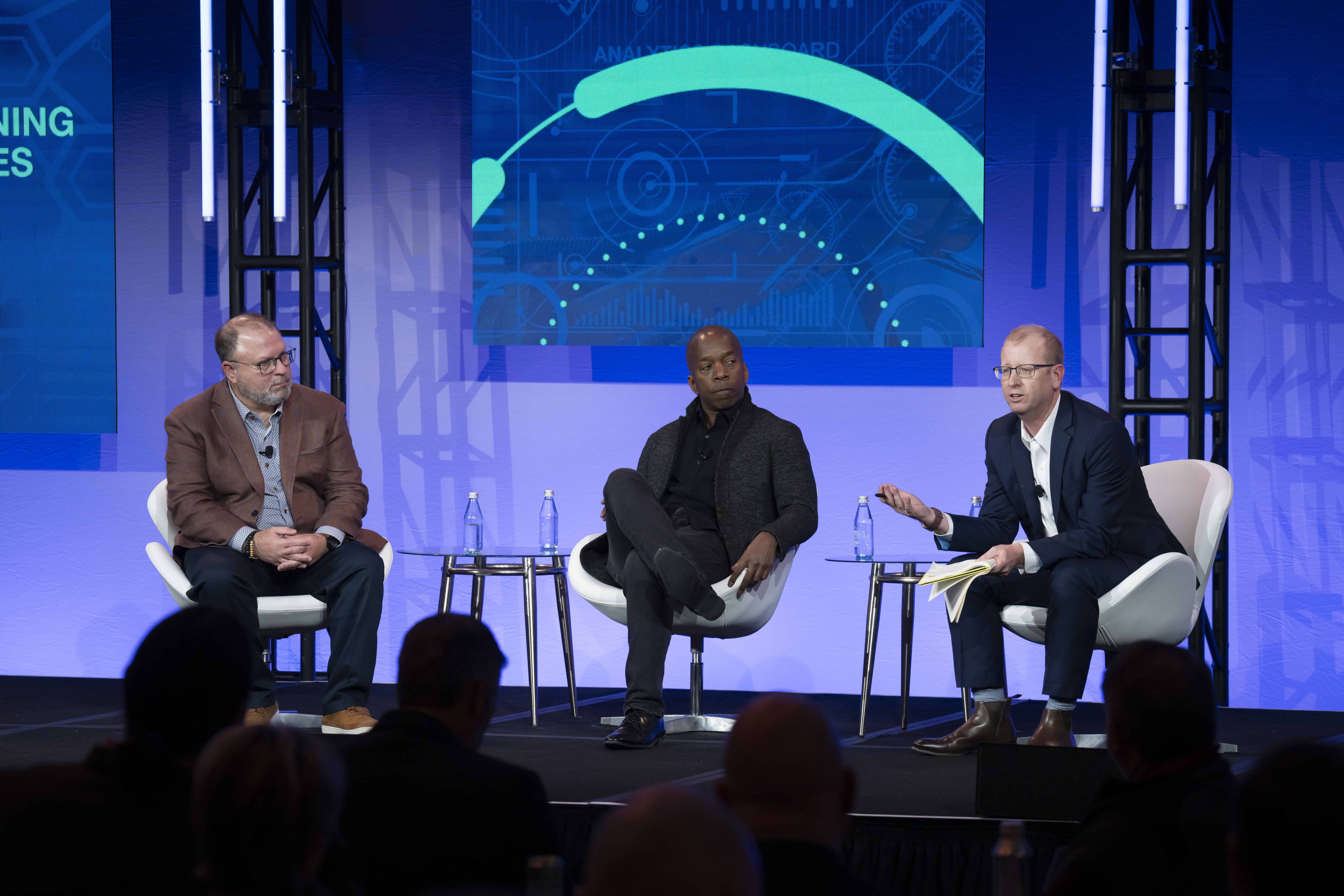
About the author:
David R. Brousell is the Founder, Vice President and Executive Director, Manufacturing Leadership Council
Welcome New Members of the MLC February 2025
Introducing the latest new members to the Manufacturing Leadership Council
Euan Anderson
VP of Manufacturing – KCNA
Kimberly-Clark
https://www.kimberly-clark.com/en-us
https://www.linkedin.com/in/euan-anderson-39316547/
Stacy Brozen
Director of Continuous Improvement NA
CNH Industrial
https://www.cnh.com/
https://www.linkedin.com/in/stacy-kelley-brozen/
Tim Windingstad
Director of Manufacturing – Fabrication
Hatco Corporation
https://www.hatcocorp.com/en
https://www.linkedin.com/in/tim-windingstad-04446b198/
Troy Youngbauer
COO
Galloway Company
https://www.gallowaycompany.com/
https://www.linkedin.com/in/troy-youngbauer-8a9012b/