Resilient Supply Chains and the Digital Thread
Strengthen your supply chain by applying digital thread principles to your data.
TAKEAWAYS:
● Lean Principles Drive Performance: Implement lean principles focused on material handling, transport, and inventory management is the cornerstone of cost reduction and performance enhancement.
● Metrics Enhance Comprehensive Insight: Evolve the development of metrics enabling comprehensive reporting and insights into supply chain performance, enhancing strategic decision-making.
● Integrated Redesigns Extend Beyond Silos: Shift from isolated efficiency gains to structural redesigns that improve demand-supply alignment, production, and fulfillment processes across entire organizations, significantly transforming operations post-pandemic.
Applying lean principles to supply chains, especially to material handling, transport, and inventory management together has been the foundation for most cost and performance improvements for the last 30 years. Metrics, like return on working capital and inventory turnover, have been developed for comprehensive reporting of supply chain performance.
Advancements in data management, usage and integration over the last decade have broadened the sources of supply chain performance improvement from functionally siloed efficiency gains to structural redesigns that span organizations. Regardless of industry, demand-supply alignment, production, warehousing, and fulfillment functions operate much differently today than they did a decade ago, or even before the pandemic.
Why?
One dominant reason is the adoption of industrial digital thread principles in supply chain management. These principles have helped supply chain data become more accurate, valuable, and broadly deployed to drive business improvement.
A digital thread is the real-time, omnidirectional flow of richly contextualized data between and among networked or meshed supply chain nodes.
Digital threads have evolved from focusing on product data to including product, process, commercial, and logistical data across wider supply chain ecosystems, particularly in mesh networks.
Today’s supply chain professionals often observe that logistics, visibility, capacity, and inventory data drive greater business efficiency. Data are more fully monetized than ever before.
As companies revisit overall supply chain strategies, misalignments among supply chain network capacities, inventories, and information have led many companies and their supply chain partners to reconstitute their integrated supply chain operations, often beginning with their data architectures and models.
In response to these challenges, manufacturers today are embedding industrial digital thread principles and data characteristics in their supply chain operating models. These often include:
- Seamless flows
- Real-time access
- Structured collaboration
- Consistent formats
- Full traceability
- Case-based contextualization
Investments in these capabilities offset risks and enhance operational agility. For example, real-time data and advanced analytics together enable early identification of potential disruptions and provide better understanding of supply chain impacts before the event(s) occur. This is crucial for making informed, preemptive decisions.
Applying Digital Thread Principles to Supply Chain Management
Many companies have viewed digital transformation as a “one-stop-shop” solution to achieve more resilient supply chains. The same is true for the application of digital thread principles. Blindly adopting new technologies without a cogent strategy that focuses on the data and its secure, but fluid, movement between supply chain participants often produces less than optimal results.
Instead, for high-value operations, organizations must complete three steps for applying digital thread principles within and across the supply chain functions where the greatest opportunities for improvement in resiliency are thought to exist.
- Measure and Diagnose: Evaluate current processes and identify opportunities.
- Design and Build: Deliver results to show immediate business impact.
- Implement and Measure (Repeat): Refine solutions through continuous monitoring and optimization.
To illustrate the application of digital thread principles, we consider two high-value supply chain operations that often determine overall supply chain resiliency:
- Demand–Supply Alignment
- Inventory Management: Material and Finished Goods
Digital Threads in Demand–Supply Alignment
Even in today’s highly integrated data environments, the timely and efficient exchange of accurate, properly contextualized demand (forecast) and supply (replenishment) data between trading partners remains a primary, sometimes elusive, goal of supply chain leaders.
Optimal demand–supply alignment maximizes on-time fill rates while reducing raw material and finished goods inventories.
Safety stocks and buffers across the supply chain may be responsibly reduced, as confidence in the accuracy of demand and supply data integration and analysis improves.
How may digital thread principles be useful in achieving these goals?
Here are some questions to ask, and suggestions to consider that are connected to the three steps for applying digital thread principles.
Measure & Diagnose:
- Seamless flows: Are demand signals received from authoritative sources without delay or modification? Similarly, are supply/replenishment triggers timely, accurate, and received into the demand–supply alignment activity without need of changes to the make the data suitable for planning purposes?
- Real-time access: Even if they are aggregated later, is access to current data available in real-time?
- Consistent formats: Is the form and content of demand and supply data consistent across all sources? That is, are units of measure and product references consistent?
Now, apply these findings to the design of data connections and flows grounded in digital thread principles.
Design & Build:
- Goal-focused design: Digital thread principles in demand–supply alignment smooth the exchange of consistently formatted, properly contextualized authoritative data to leaders of production operations and material management.
- Standardized data architectures: Adopt a unified namespace (UNS) or equivalent structure. Focus on contextualization to improve collaboration efficiency between demand and supply process owners.
- Alignment between demand–supply processes: Processes using data configured to digital thread principles are more capable of accommodating disruptions, unusual events, and other irregular operating conditions.
Remember, the hallmark of a resilient supply chain is its ability to return to regular operations.
Implement & Measure:
- Demand–supply alignment processes that encourage collaboration: To provide value, IT systems leverage contextualized data from forecasts, planning systems, capacity and production plans, logistics and warehouse management systems, and other data sources. Data flows, analysis results, action recommendations, and reports become more valuable when they leverage data procured through digital thread principles.
- Data models architected with digital thread principles: These models are better able to support demand–supply alignment processes and deliver supply chain performance goals. Keep the focus on the alignment process and desired outcomes, instead of on manipulating and managing the data.
Digital Threads in Inventory Management
A well-known operations management principle posits that production capacity, inventory, and data are interchangeable. Of course, the most efficient and valuable operations are those which maximize the value and utility of data, in exchange for optimized inventories and manufacturing infrastructures.
That proposition applies to the digital thread for optimizing inventory and streamlining the management processes associated with it, especially at the bookends of raw material (RM) and finished goods (FG).
No other core contributors to supply chain resiliency have more sources or more diverse sets of data than inventory management.
How may digital thread principles contribute to optimization of raw material and finished goods inventory across the supply chain?
Using the three steps, here are some more suggestions to consider.
Measure & Diagnose:
- Inventory management metrics: Diagnose supply chain issues and quantify weaknesses or gaps in data, its form, content, or contextualization.
- Thorough root cause analyses (RCA) of inventory excursions: Identify data and IT system operating gaps to be addressed through digital thread principles like timeliness, accuracy, and contextualization.
- RCA results: Prioritize these results for changes to data models and applications of digital thread principles to available data to drive the greatest and/or most rapid improvements in RM and FG inventory performance.
Design & Build:
- Evaluation and prospective redesign of data models: Efficient integration of digital thread principles into inventory management processes and their IT applications requires evaluation and prospective redesign of data models within the capabilities of IT systems.
Experience suggests most of the new digital thread data, or additional detail for current data, will be directed toward contextualization, since inventory management performance issues often result from incomplete data models or incorrect ancillary data.
Implement & Measure:
- Complete and contextualized data architectures: Data architectures that focus on completeness and contextualization improve the performance and value of inventory management systems and processes.
- Inventory management processes and systems: These leverage large volumes of data from diverse sources, including suppliers, factories, distribution providers and customers. The rich data structures and system connectivity enabled by digital thread principles help maximize the operational value of both RM and FG inventory management tools.
- Contextualized inventory data: Contextualization of inventory data provides material managers greater situational awareness and more comprehensive data upon which to act.
Closing Recommendations
Adopting industrial digital thread principles is essential for creating a resilient supply chain network, as they enhance the accuracy and usability of data, driving significant business improvements in a dynamic marketplace.
– Consider inclusion of digital thread principles in process, solution, and technology architectures spanning your supply chains.
– Evaluate the sufficiency of your current data architectures, models, and operations against supply chain performance.
– Determine the role of data form, content, context, timeliness, and other digital thread principles in mitigating the identified deficiencies. Determine if gaps are rooted in business applications, technologies, infrastructures, or data. M
About the author:
Jeffrey Miller is Industry Principal Lead for Kalypso, a Rockwell Automation Business
Germany, Canada Push Back on U.S. Policies at Opening of Hannover Fair
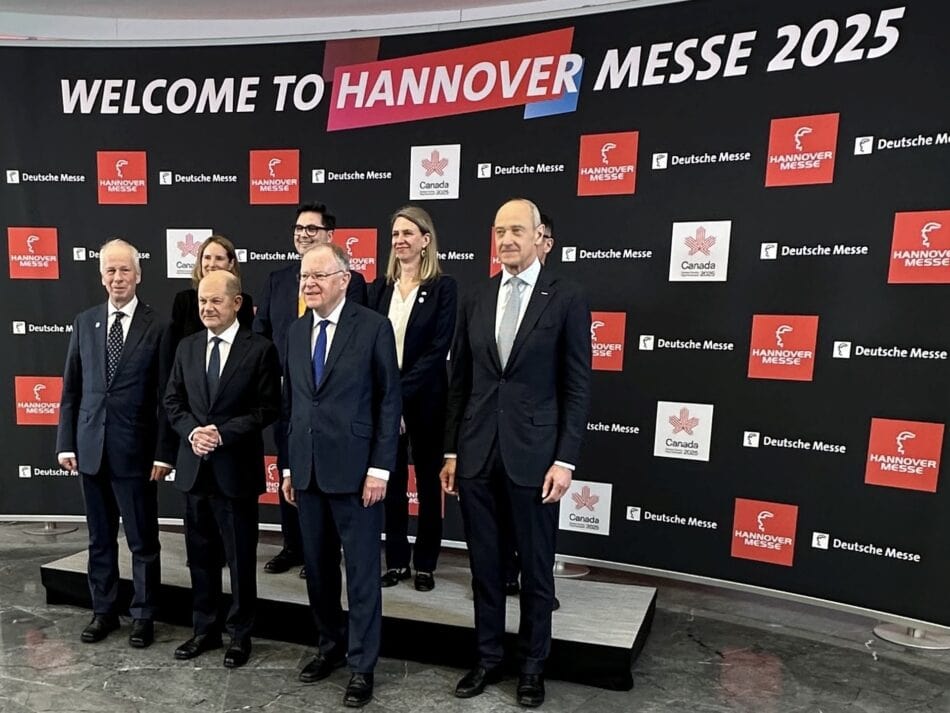
Geopolitics took center stage at the opening ceremonies of the Hannover Fair in Germany last night, as German and Canadian government and industry officials criticized U.S. policy on tariffs and trade and declared their support for the independence of Canada.
“Rarely has there been so many political messages at a Hannover Fair,” said German Chancellor Olaf Scholz. “Trade wars have no real winner, not even the U.S. Europe’s goal is cooperation. But if there is no chance of this, we will act as a unified front.”
Even though Scholz and other speakers did not mention the Trump Administration by name, their messages were clearly targeted at the tariff, trade, and defense polices of the new U.S. administration. Phrases such as “open markets”, “reliable partners”, “respect for neighbors”, and “stable environments” dominated the opening ceremony speeches.
President Donald Trump’s statements about Canada, the partner country for this year’s Hannover Fair, becoming the 51st state of the U.S. received pointed rebukes.
“Canada is not a state of any other nation,” said Scholz. “It will never be part of the U.S.”
It is customary for the Hannover Fair partner country to have its head of state or government participate in the Fair’s opening ceremonies in person. Because Canada is in the midst of a national election, the new Prime Minister, Mark Carney, could not attend. Instead, Stephane Dion, Special Envoy to the European Union and Europe, spoke at the ceremonies, emphasizing Canada’s commitment to free trade, its reliability as a partner, and its willingness to strengthen ties with friendly nations.
“Canada is an ally, a friend,” Dion said. “We believe in win/win agreements. We have respect for international law and mutual trust.” With regard to trade relations with Germany, he said: “We knew we liked each other; now, we know we need each other.
But it was also clear from the speeches at the opening ceremonies that the countries and their industrial companies are now operating in a new environment. Siemens AG CEO Roland Busch said the new geopolitical environment is an opportunity Germany must seize.
“The operating system of the world is becoming obsolete,” he said. “It is time for a new one. We must re-invent how we grow together. Germany has been held back by excessive bureaucracy. We need less and more and faster innovation.”
Busch also addressed a major focus of the Hannover Fair this year – artificial intelligence.
He said companies won’t succeed by just adding AI into what they are currently doing. They have to re-think their processes and rebuild. He also warned about the stakes of not moving aggressively to adopt and learn about AI.
“In a few years from now, there will be a divide between those that embrace AI and those that don’t,” Busch said. “This may be the last generation of managing companies with just humans.”
Last night, Siemens won the Fair’s coveted Hermes Award for its Industrial Co-Pilot generative AI tool.
On Monday, the Hannover Fair exhibition opens. There are approximately 4,000 companies showing and demonstrating their technology and industrial products. About 130,000 people are expected to attend.
About the author:
David R. Brousell is the Manufacturing Leadership Council’s Founder, Vice President and Executive Director
Digital Transformation Sees Explosive Growth
Manufacturers are increasing their investments in digital assets, according to a recent survey from the Manufacturing Leadership Council, the NAM’s digital transformation division.
What’s going on: Due in large part to expectations of economic growth, manufacturers plan to either maintain or boost their spending on smart factory investments, they told the MLC in the recently published results of the Smart Factories and Digital Production Survey.
- Respondents also said they are optimistic about continued digitization and adoption, with 69% expecting moderate growth and no recession.
- While 28% would call their current operations “smart” or “somewhat smart,” 76% expect to be there in the next two years.
- Awareness of AI is growing by leaps and bounds among manufacturers; some 34% said they see AI as very significant. (Last year, just 10% said the same.)
Key points: The survey’s top takeaways include the following:
- Digital transformation is changing the game: Most manufacturers—60%—see digital transformation as something that is redefining the industry.
- More manufacturers are going digital: Some 75% of manufacturers say they are at “midlevel” digital maturity, up significantly from 2024 and 2023.
- AI’s role is inevitable: Fully 80% of manufacturers fully or partially agree self-managing and self-learning facilities powered by AI and machine learning are coming.
Manufacturing Leadership Council Elects Four New Leaders to Board of Governors
Washington, D.C. — The Manufacturing Leadership Council, the digital transformation division of the National Association of Manufacturers, has announced the election of four leading manufacturing executives to the MLC’s Board of Governors. The MLC is the nation’s leading networking and executive leadership organization dedicated to digital transformation in manufacturing by focusing on the technological, organizational and leadership dimensions of change.
The four new MLC board members include the following:
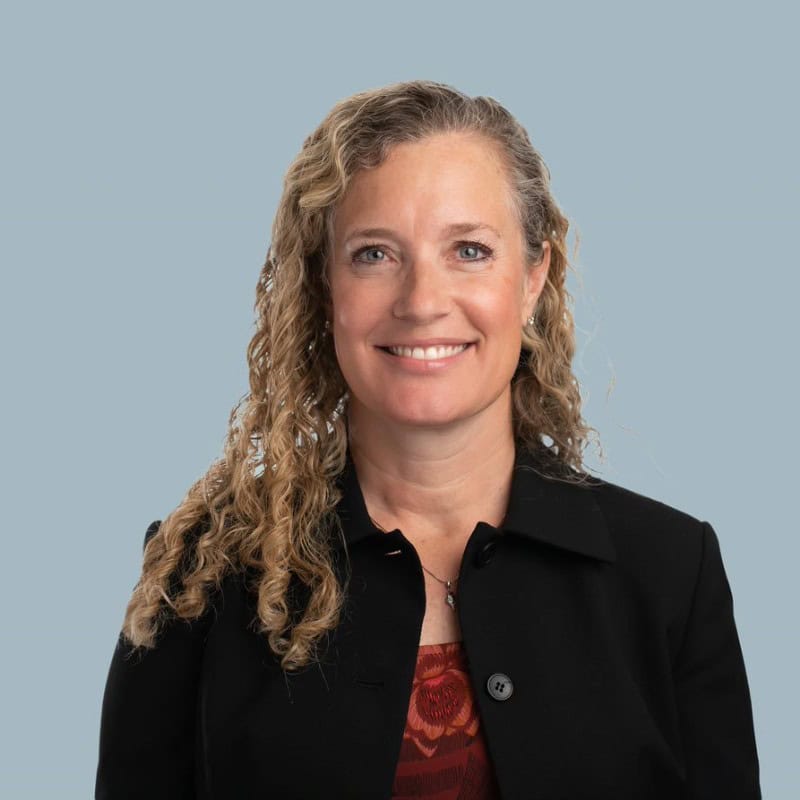
Melissa Boom, vice president, Business Excellence Systems, Winnebago Industries: In her role, Boom has designed and leads the Business Excellence Center of Excellence at Winnebago Industries, which enables the company’s businesses to partner and improve on techniques that drive value, reduce risks and increase synergies. This covers capabilities in business process, continuous improvement, industrial and manufacturing systems engineering, and quality systems.
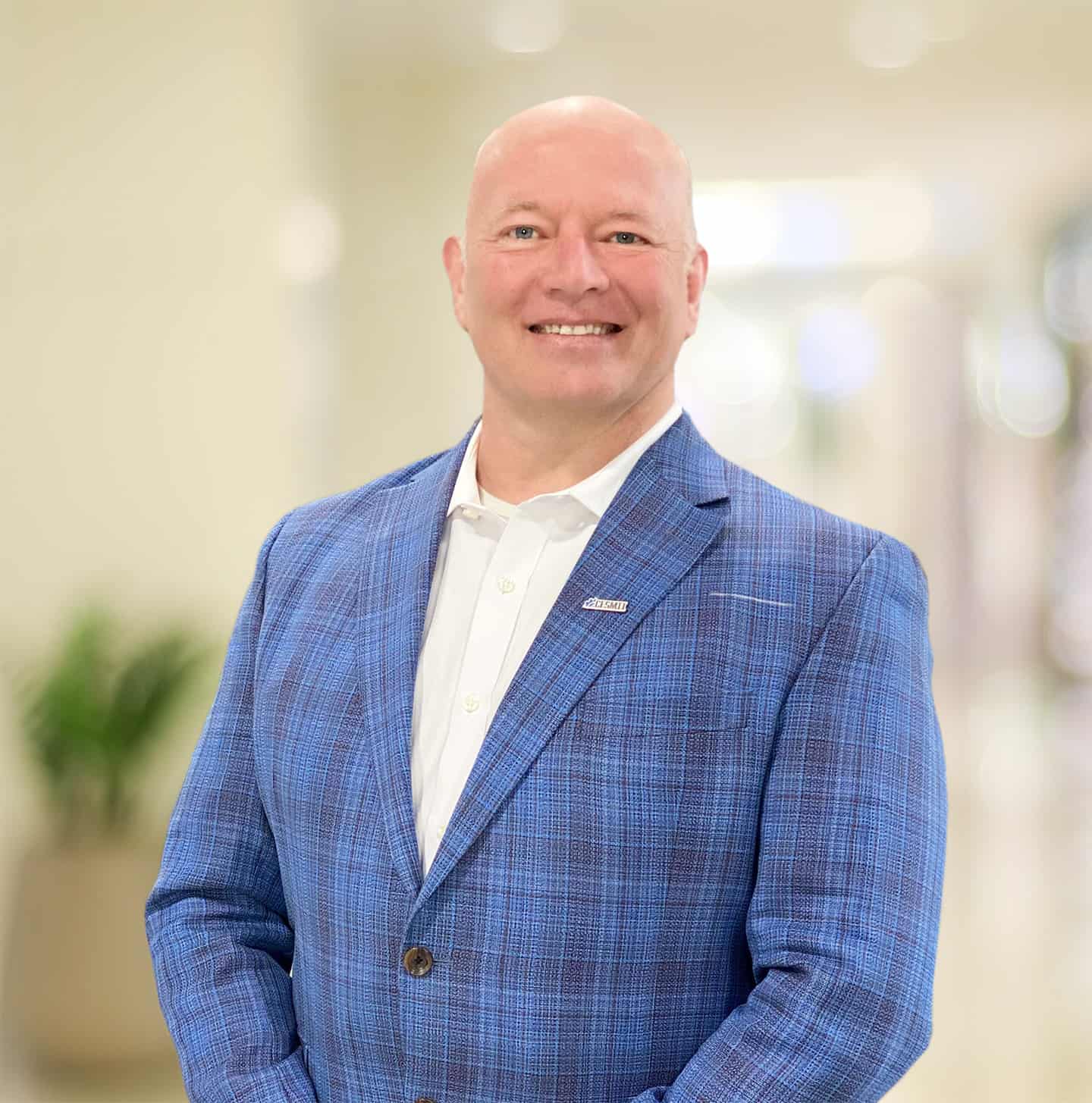
John Dyck, CEO, CESMII – The Smart Manufacturing Institute: Dyck’s leadership of CESMII focuses on outcomes that will benefit the nation’s energy and economic security by sharing existing resources and investing to accelerate development and commercial deployment of smart manufacturing capabilities. He is a renowned domain expert on both technology and business management and has pioneered the application of advanced digital technologies in manufacturing operations and supply chains.
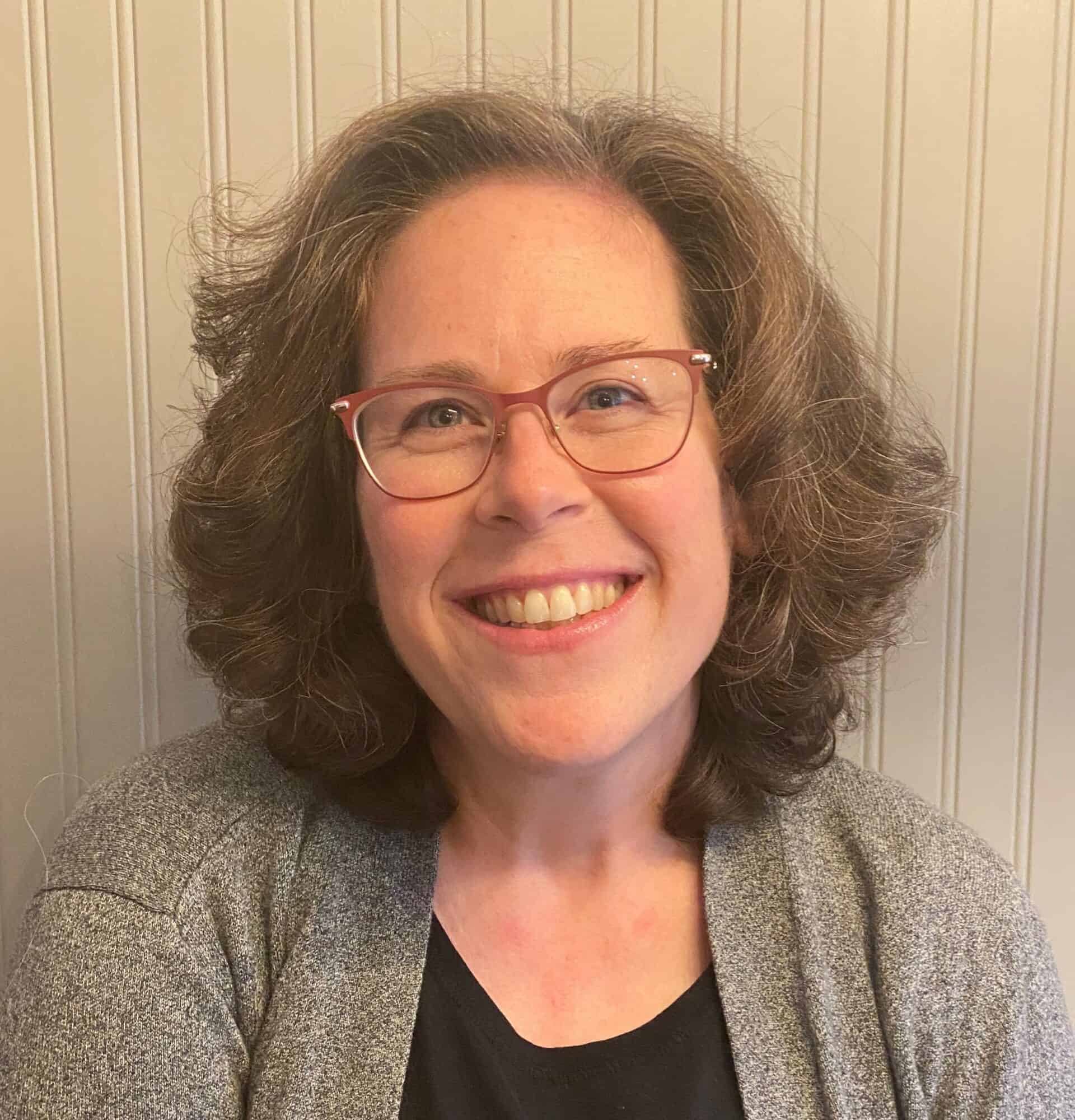
Regan Gallo, director of operations, Coated Abrasives NA, Saint-Gobain North America: Gallo has led operations for four different businesses at Saint-Gobain, in support of more than 40 manufacturing sites. She leads Saint-Gobain’s North American Operations Council, which brings together the company’s North American operations managers to share best practices and align on common operational standards in safety, HR, world-class manufacturing and Manufacturing 4.0.
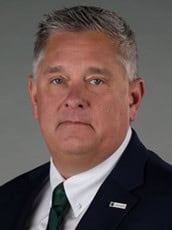
Billy Spears, senior vice president and chief product delivery officer, Lexmark International, Inc.: Spears is responsible for hardware and supplies development, supply chain, manufacturing and service delivery in his role with Lexmark. He also serves on the board for the Kentucky Chamber of Commerce and the Supply Chain Advisory Board for Eastern Kentucky University.
“Adding these distinguished manufacturing leaders to the MLC Board of Governors brings a wealth and depth of experience and knowledge that are critical to serving MLC members,” said Dan Dwight, president and CEO of Cooley Group and chairman of the MLC Board of Governors. “I am proud to welcome these new board members and look forward to collaborating with them to create a stronger future for the MLC.”
“Since its inception, the Manufacturing Leadership Council has always aspired to be at the forefront of digital operations, and to tap the industry experts who could help us meet that goal,” said David R. Brousell, founder, executive director and vice president of the MLC. “The newest additions to our board are essential to that mission and will ensure our place as the leading organization for digital manufacturing leadership.”
As an advisory body, the MLC Board of Governors provides guidance to the MLC on its annual Critical Issues agenda, research studies and programs and services for the MLC membership.
-MLC-
Founded in 2008 and now a division of the National Association of Manufacturers, the Manufacturing Leadership Council’s mission is to help manufacturing companies transition to the digital model of manufacturing by focusing on the technological, organizational and leadership dimensions of change. With more than 2,500 senior-level members from many of the world’s leading manufacturing companies, the MLC focuses on the intersection of advanced digital technologies and the business, identifying growth and improvement opportunities in the operation, organization and leadership of manufacturing enterprises as they pursue their journeys to Manufacturing 4.0.
Rethink 2025 Is Coming Up Fast
Get ready! Manufacturing’s leading annual event on accelerating digital transformation is right around the corner.
What’s going on: Rethink—held by the Manufacturing Leadership Council on Marco Island, Florida, each June—is a must-attend conference for anyone interested in Manufacturing 4.0 and where it’s headed (The MLC is the digital transformation division of the NAM.)
- This year’s event takes place June 15–18 at the JW Marriott Marco Island Beach Resort.
Why you should go: Rethink attendees will get an inside look at the cutting-edge processes and technologies transforming manufacturing today—directly from those creating and implementing them. They’ll also get a chance to:
- Consult with peers on manufacturing’s most critical initiatives, including smart factories and digital production, resilient supply networks and analytics and data mastery;
- Participate in real-time discussions and one-on-one meetings to help them understand how various solutions can solve their business problems;
- Hear from industry leaders and experts during panel discussions, executive interviews and more;
- Interact and collaborate with peers during interactive “think tank” sessions; and
- Hear from the MLC’s event partners during Rethink’s exclusive VIP Tour.
Who will be there: Scheduled speakers include Siemens USA President and CEO Barbara Humpton, Eaton Vice President of Industry 4.0 Craig Sutton, Hershey Company Vice President of Manufacturing, Operations Technology and Supply Chain Strategy Will Bonifant, Rockwell Automation Senior Vice President of Intelligent Devices Tessa Myers and many more.
The gala: Closing out the packed three-day event is the Manufacturing Leadership Awards Gala, at which the MLC will recognize award finalists and winners of the Future of Manufacturing Award, the Manufacturing Leader of the Year, the Small/Medium Enterprise Manufacturer of the Year and the Large Enterprise Manufacturer of the Year. The gala will take place on the evening of June 18.
Attend: Register online here for Rethink 2025. (NAM members get a discount at checkout.) Questions? Send them to [email protected].
The AI Glossary for Manufacturing Leaders: Key Terms You Need to Know
AI is revolutionizing manufacturing, but do you know the essential terms? This quick guide breaks down key technologies driving the future of industrial innovation.
As manufacturing leaders navigate Manufacturing 4.0’s complexities, artificial intelligence has emerged as a critical enabler of digital transformation. With AI evolving rapidly, staying on top of the latest terms and technologies can feel overwhelming.
To cut through the complexity, we’ve put together a quick guide to key AI concepts shaping manufacturing today. Whether you’re exploring predictive maintenance, product development, or human-machine collaboration, understanding these AI technologies will give you a clearer picture of their potential impact on your operations.
- Agentic AI: AI systems capable of autonomous decision-making and action-taking to accomplish goals, often integrating planning, reasoning, and adaptability to dynamic environments.
- Causal AI: AI that goes beyond correlation-based learning to understand cause-and-effect relationships, improving decision-making, diagnostics, and scientific discoveries.
- Edge AI: AI that runs on local devices rather than centralized cloud servers, enabling real-time processing and low-latency applications in areas like IoT, industrial automation, and smart devices.
- Generative AI: AI models that create new content, such as text, images, audio, or code, based on training data. Examples include ChatGPT for text and DALL·E for images.
- Large Language Models/Small Language Models: LLMs are advanced AI models trained on vast amounts of text to generate human-like language, while SLMs are smaller, more efficient models optimized for specific tasks with lower computational requirements.
- Machine Learning: A subset of AI that enables systems to learn from data, identify patterns, and make decisions with minimal human intervention. It includes supervised, unsupervised, and reinforcement learning techniques.
- Natural Language Processing: AI focused on enabling computers to understand, interpret, and generate human language, allowing for applications like chatbots, translation services, and sentiment analysis.
- Physical AI: AI integrated into physical systems, such as robots or autonomous vehicles, enabling interaction with the physical world through sensors, actuators, and adaptive control.
- Vision Systems: AI that processes and interprets visual data from the world, such as images or videos, enabling tasks like facial recognition, object detection, and quality control in manufacturing.
Scenes from MLC’s AI Conference
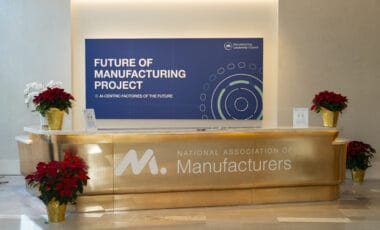
The opportunities and challenges of applying artificial intelligence in manufacturing operations were explored at MLC’s recent event in Orlando.
More than 190 manufacturing executives gathered in Orlando in early December of last year to talk about AI-Centric Factories of the Future. More than one dozen case studies, panel discussions, and presentations were delivered at the one-day conference, which was part of the Manufacturing Leadership Council’s Future of Manufacturing Project.
The goal of the Project is to help manufacturing executives understand the potential of advanced technologies to improve their operations in the years ahead.
The following are photos from the Orlando conference. MLC members can access full videos of the sessions depicted in the photos by going to the MLC Member Resource Center: https://manufacturingleadershipcouncil.com/member-dashboard/resource-center/resource_type/future-of-manufacturing-project/
Photos by David Bohrer, Senior Director, Photography, at the NAM.
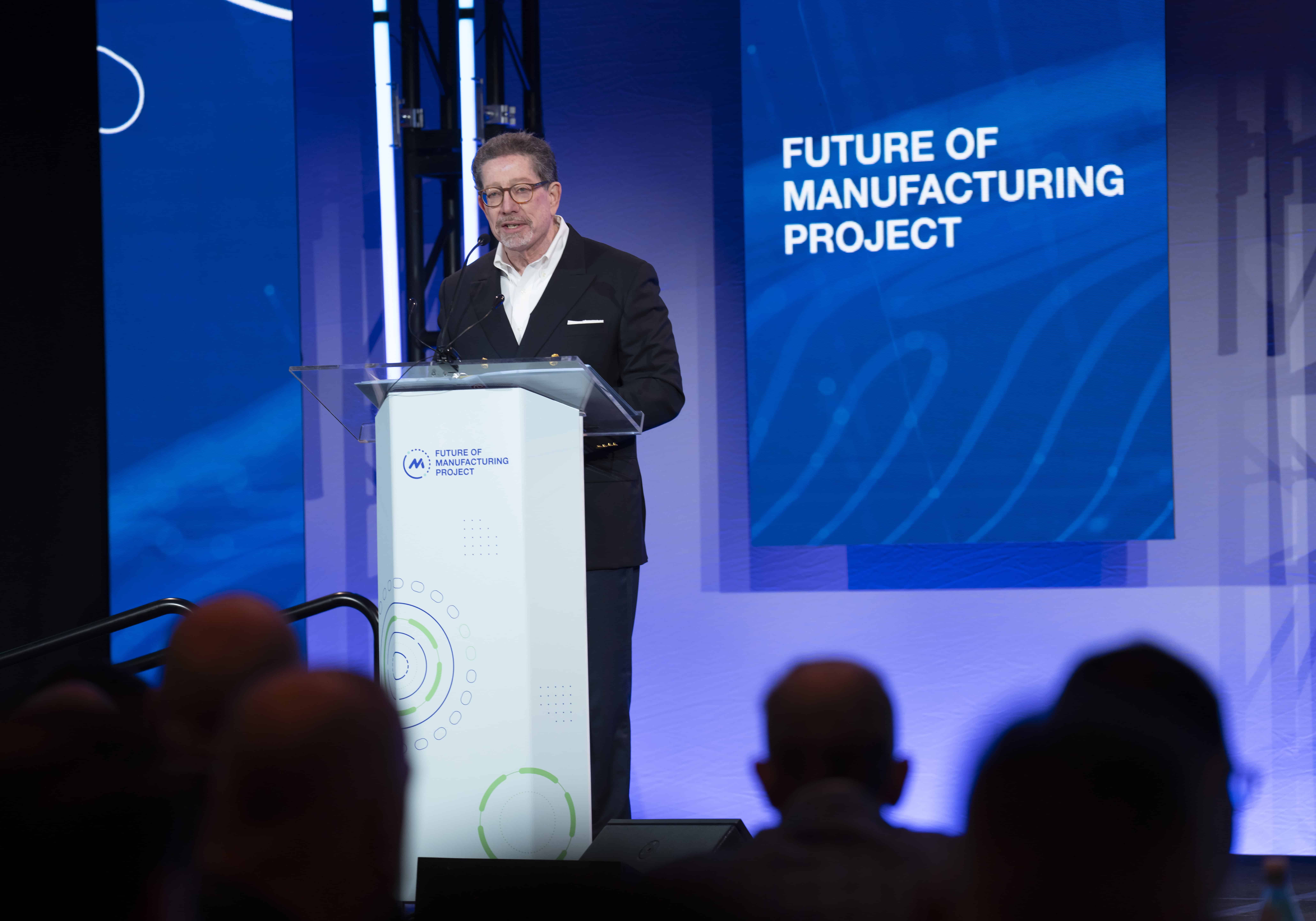
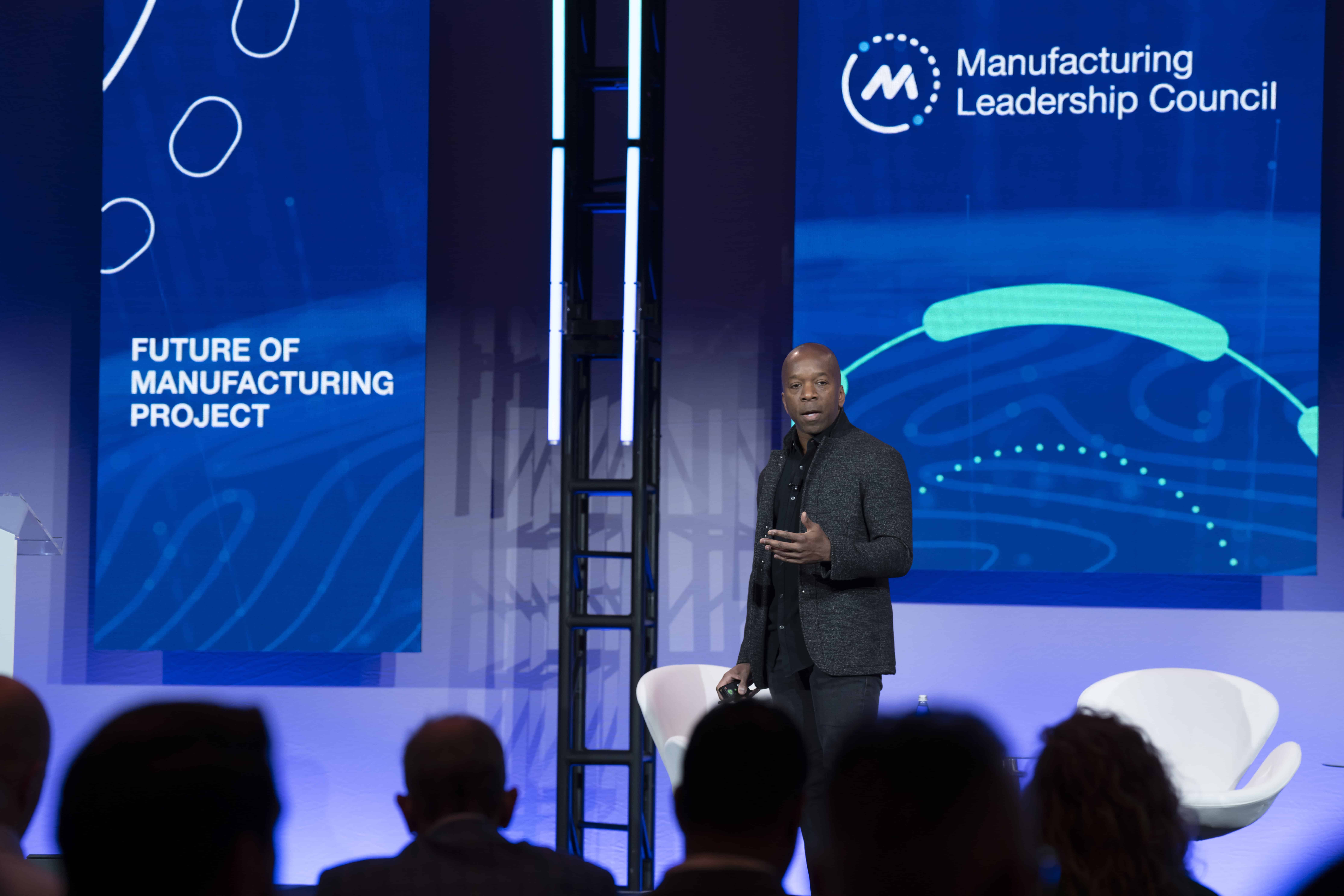
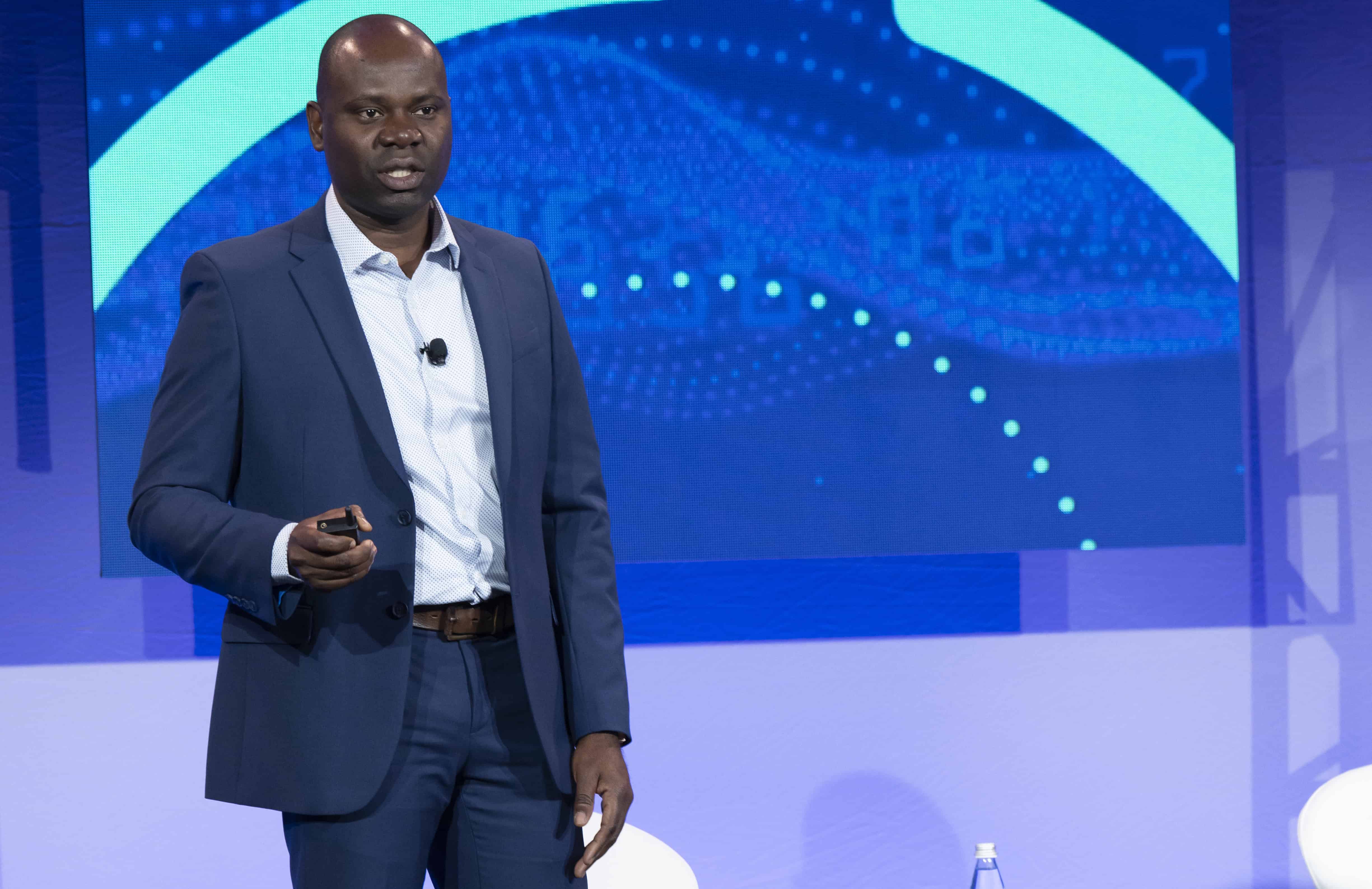
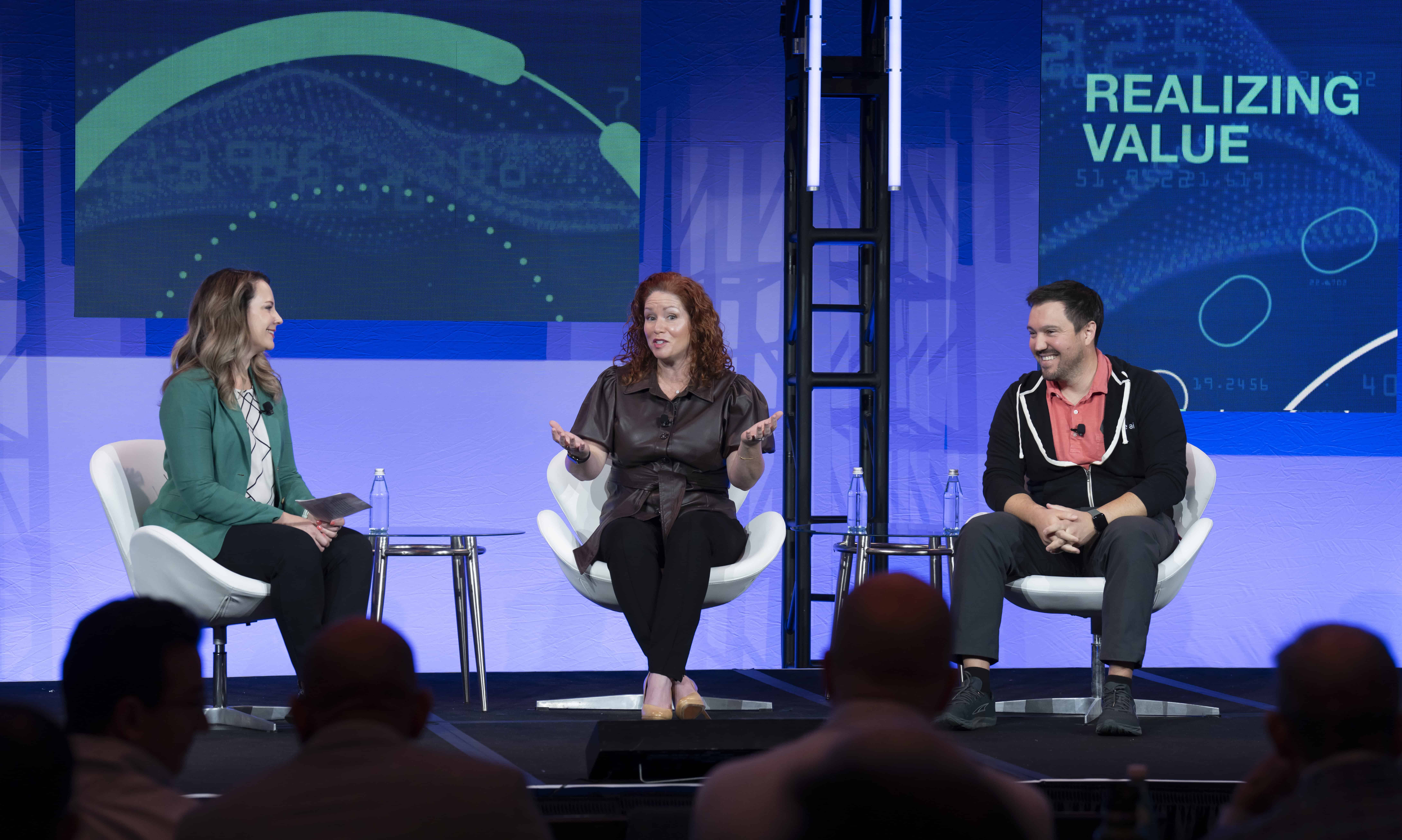
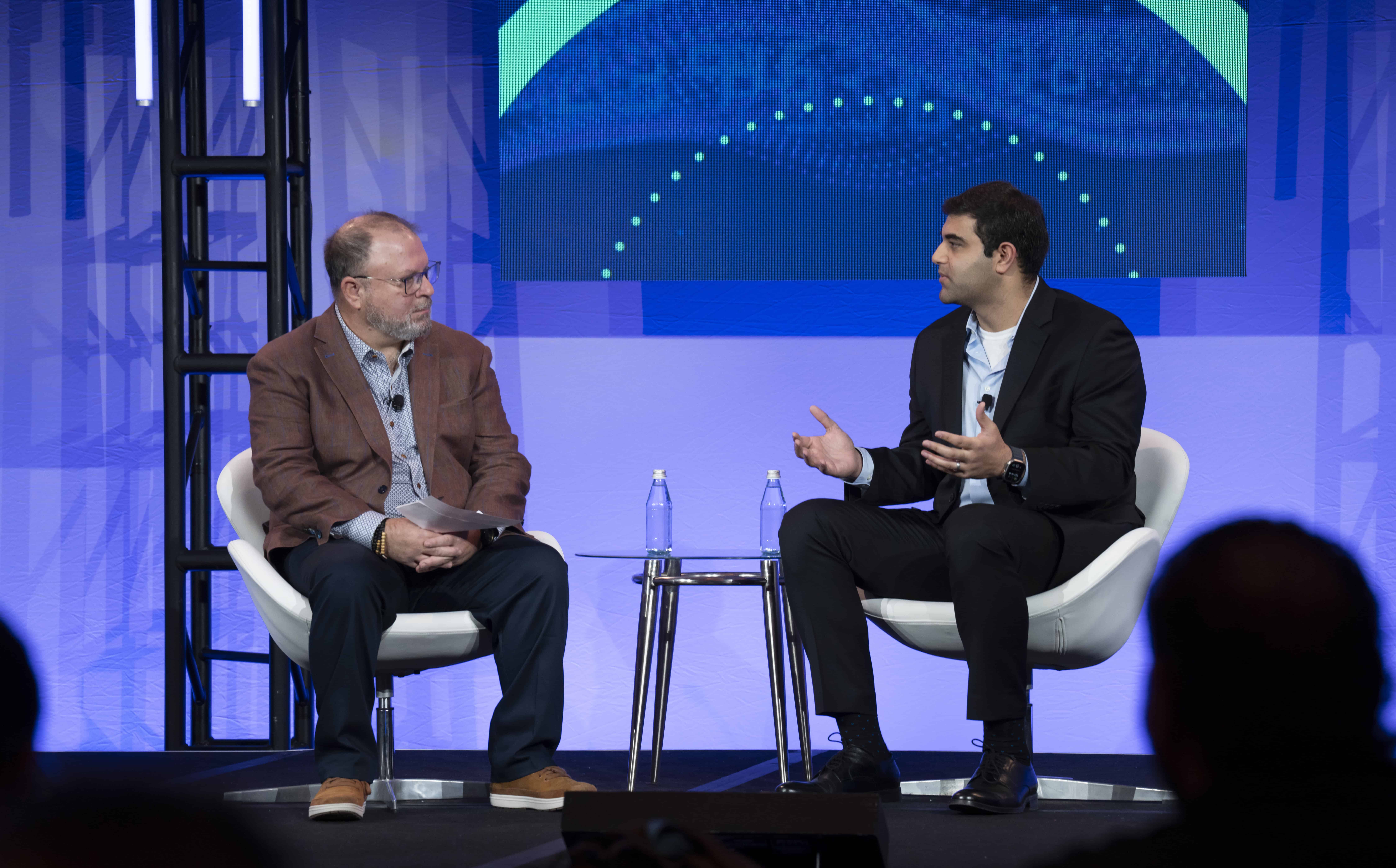
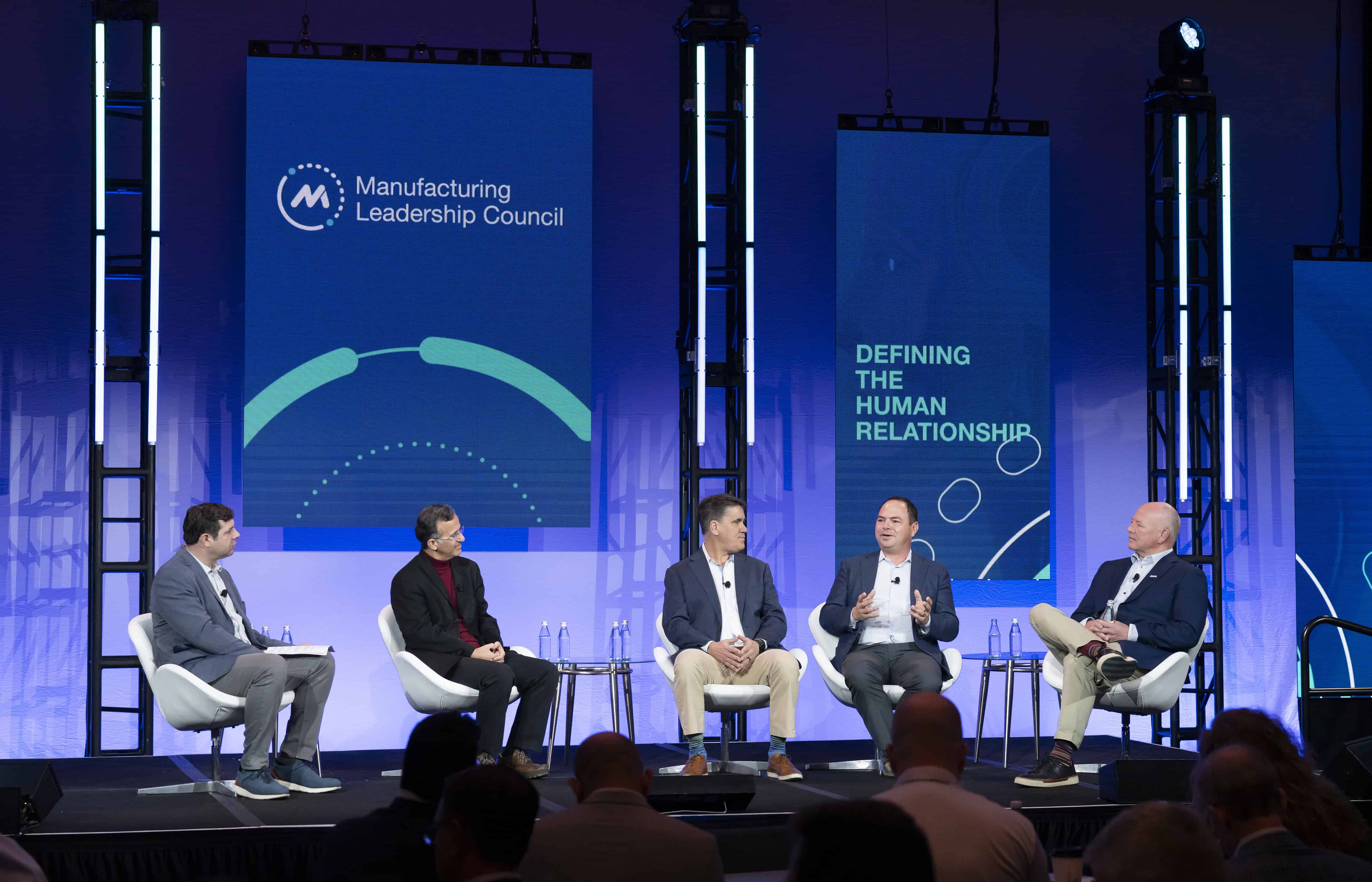
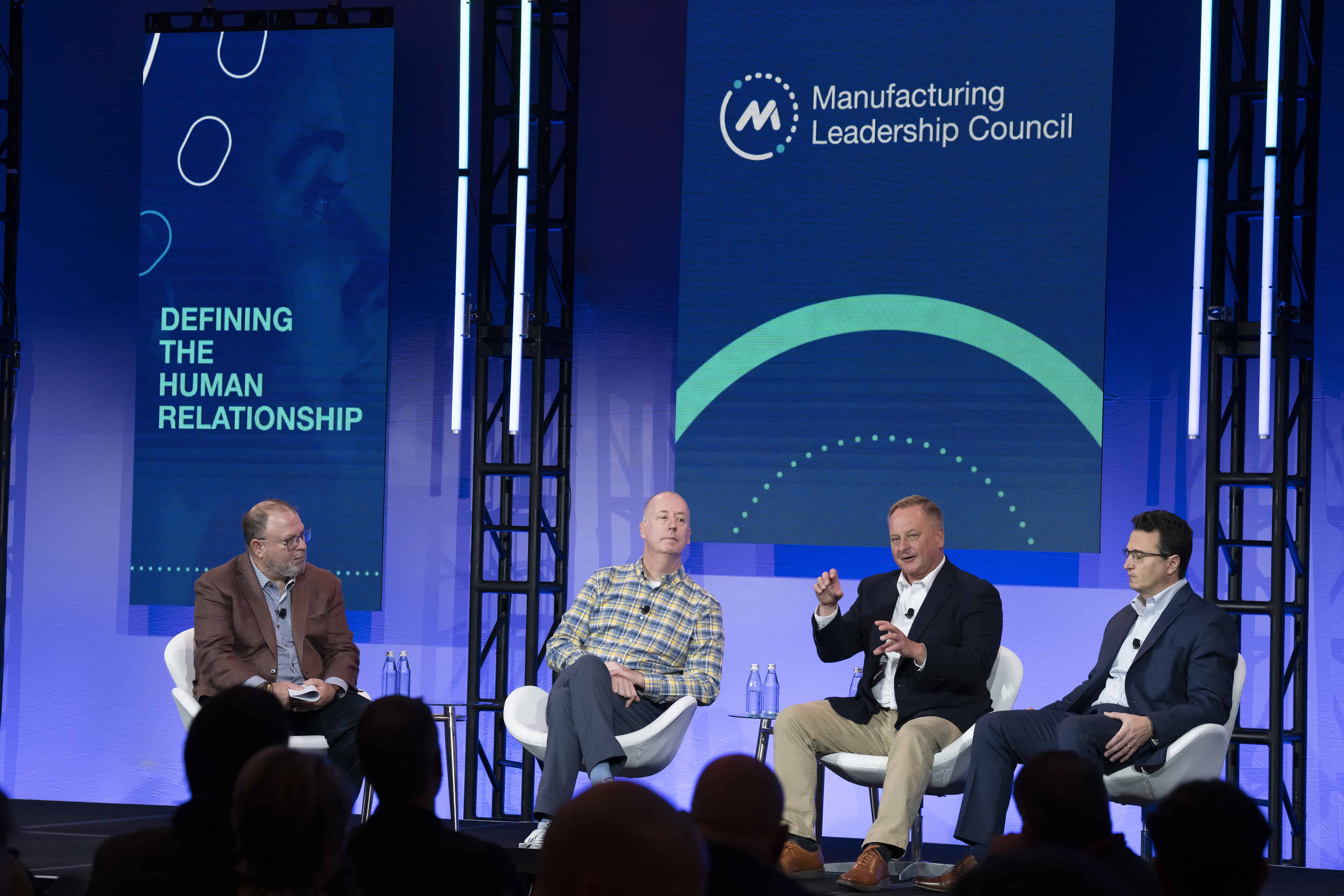
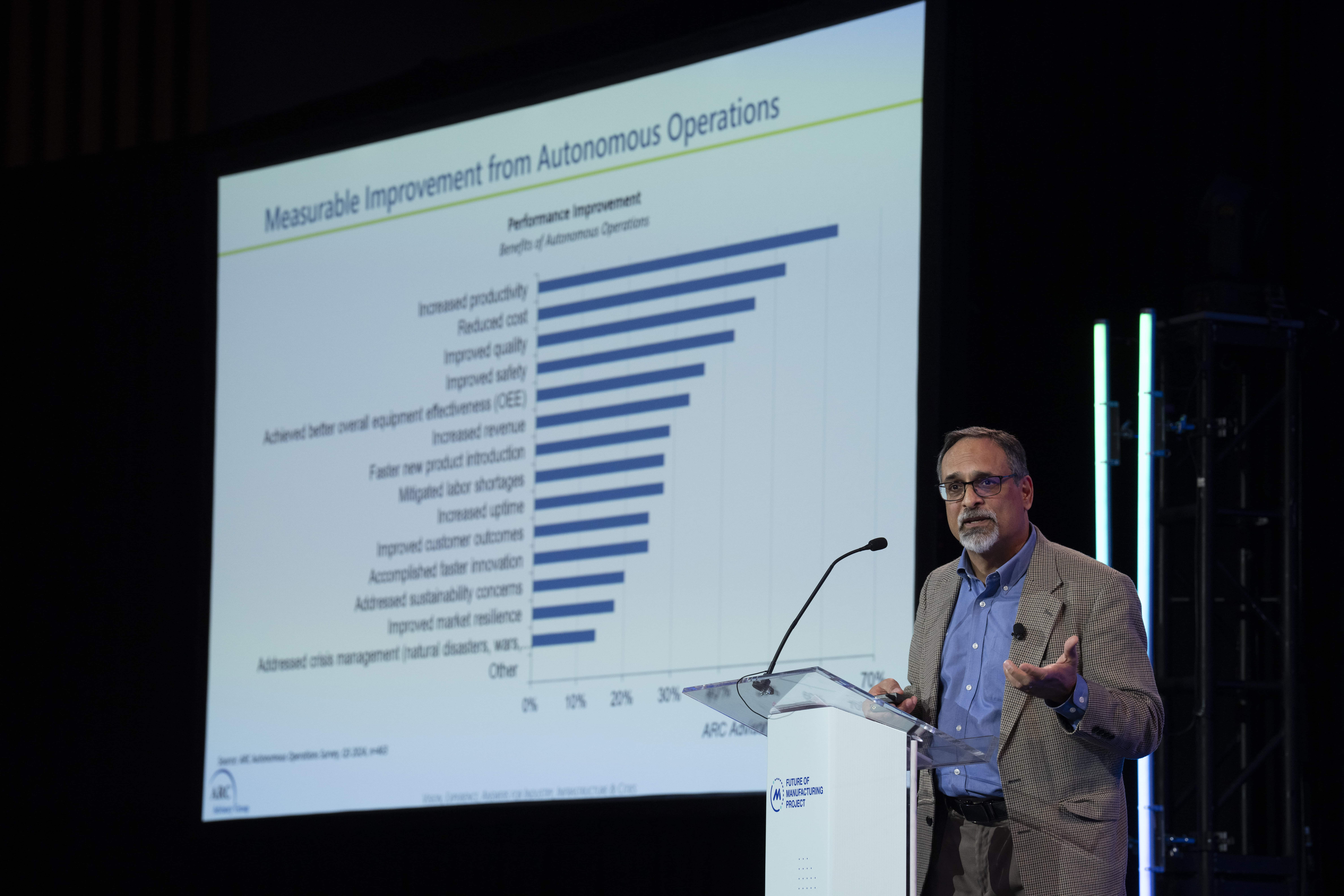
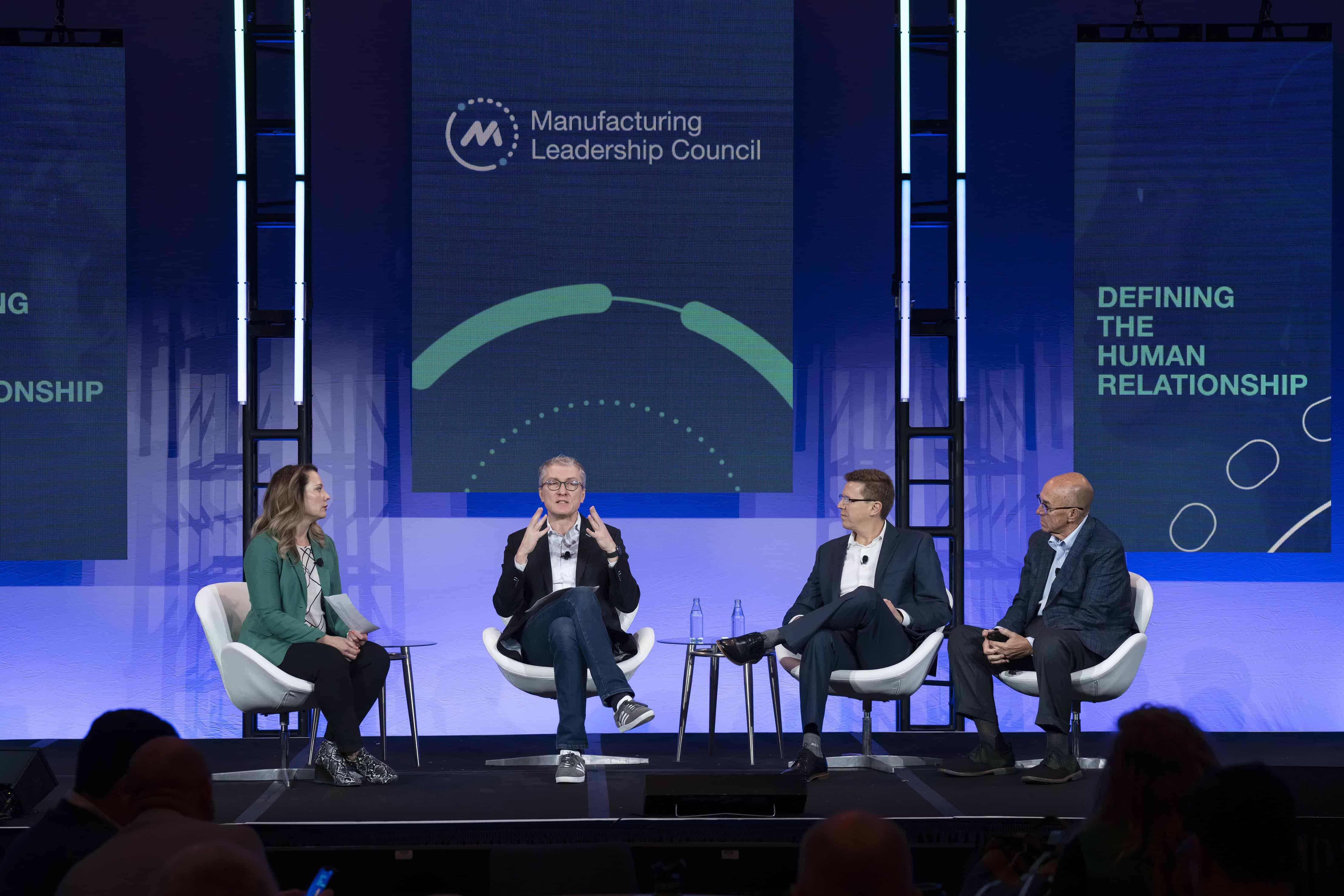
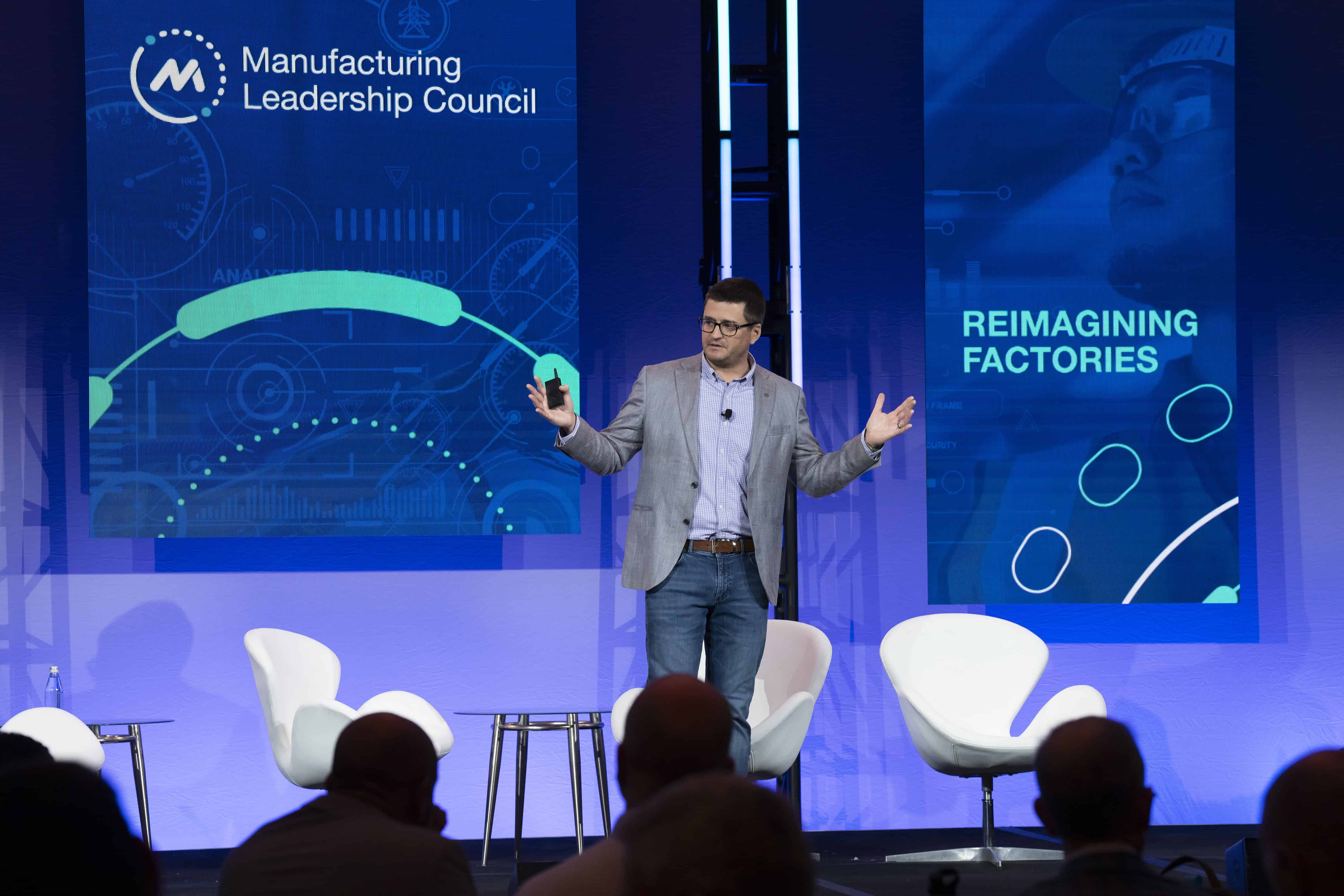
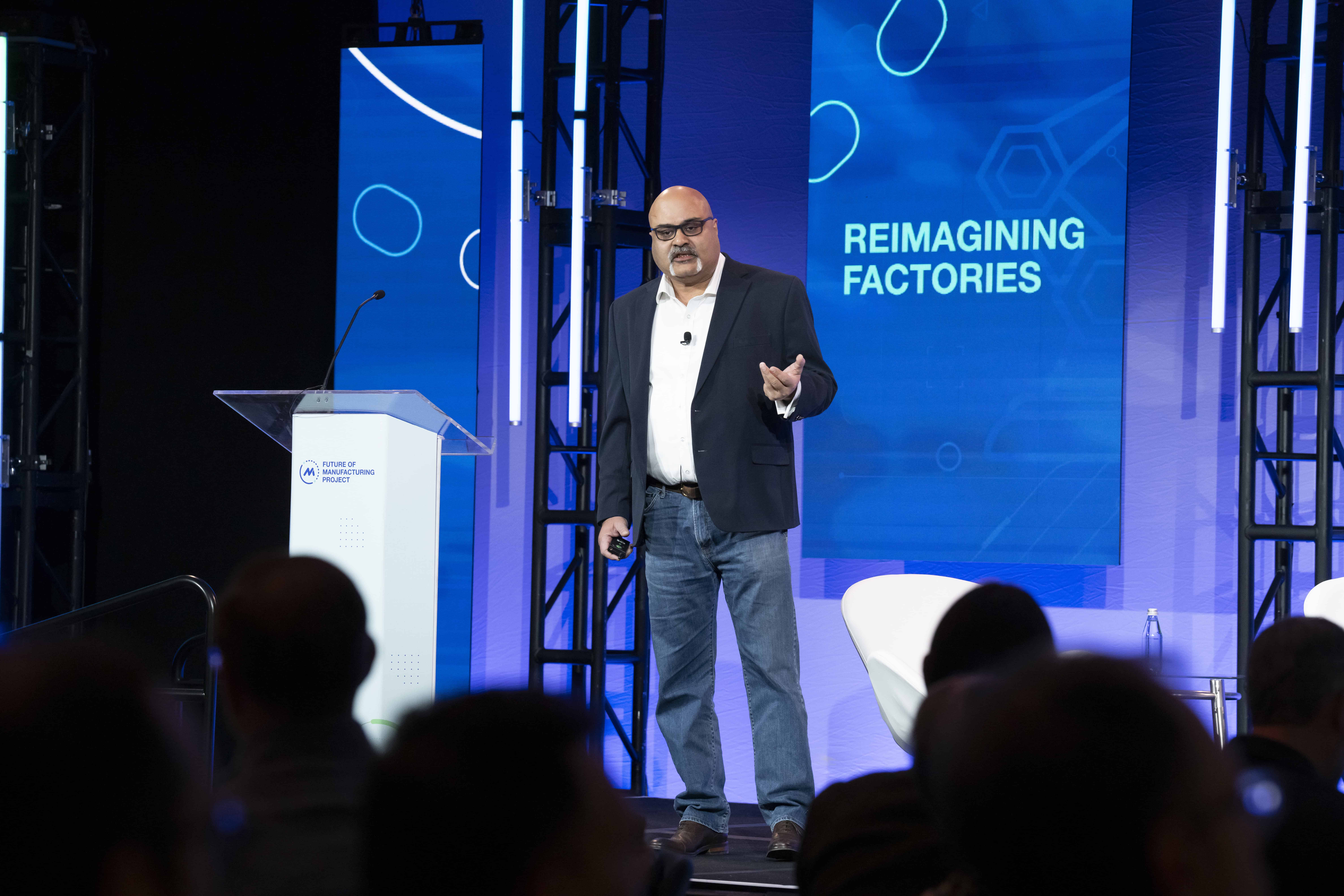
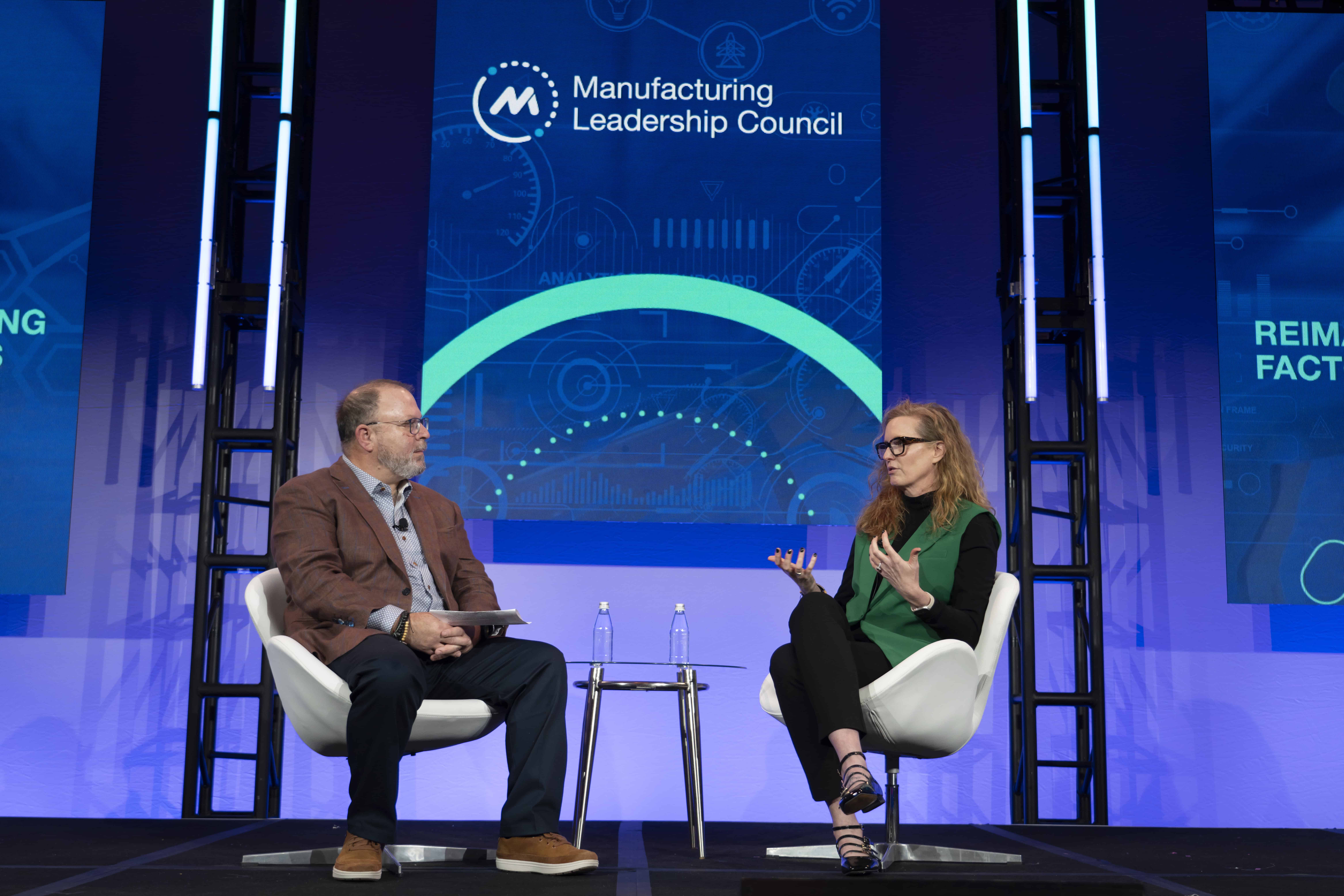
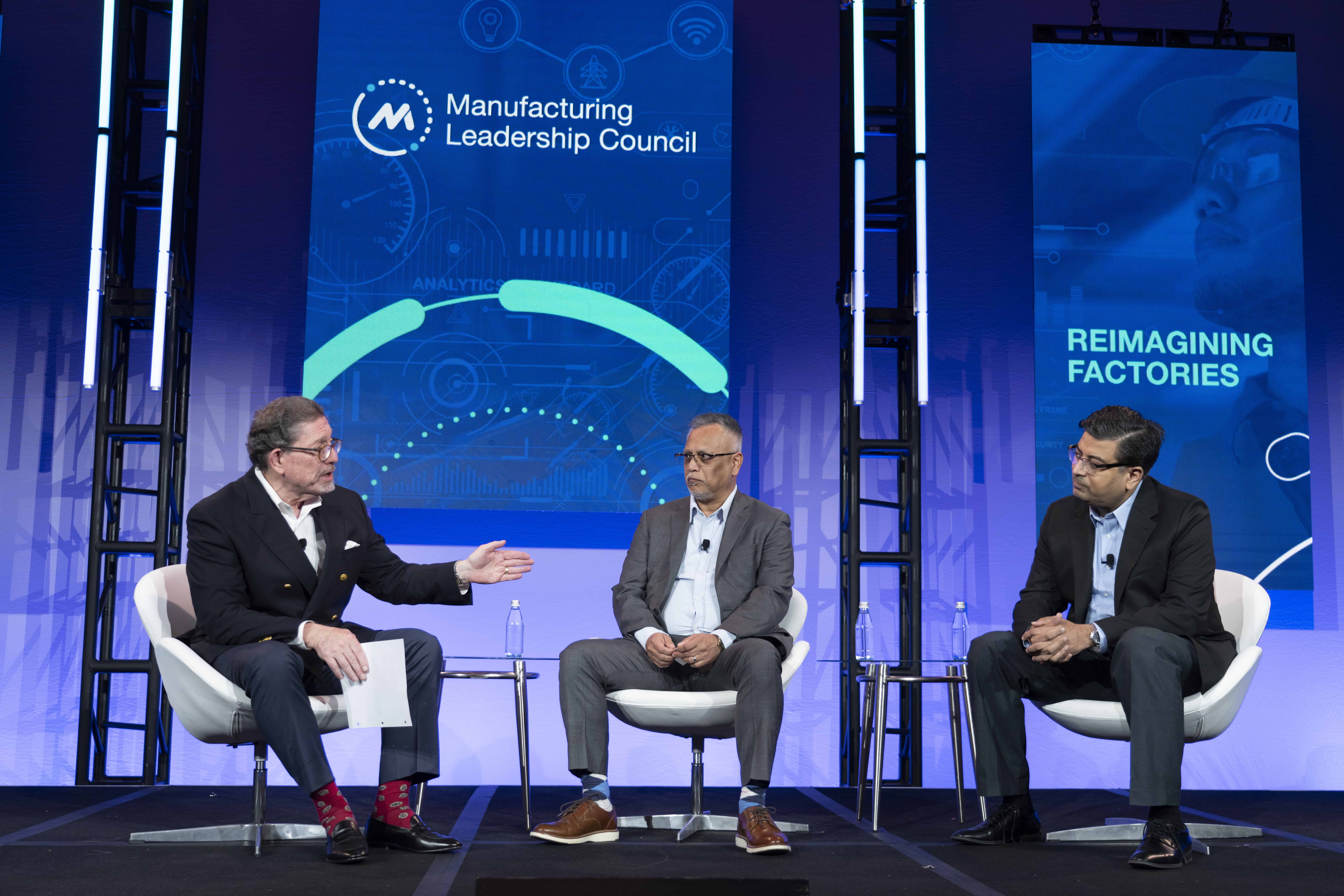
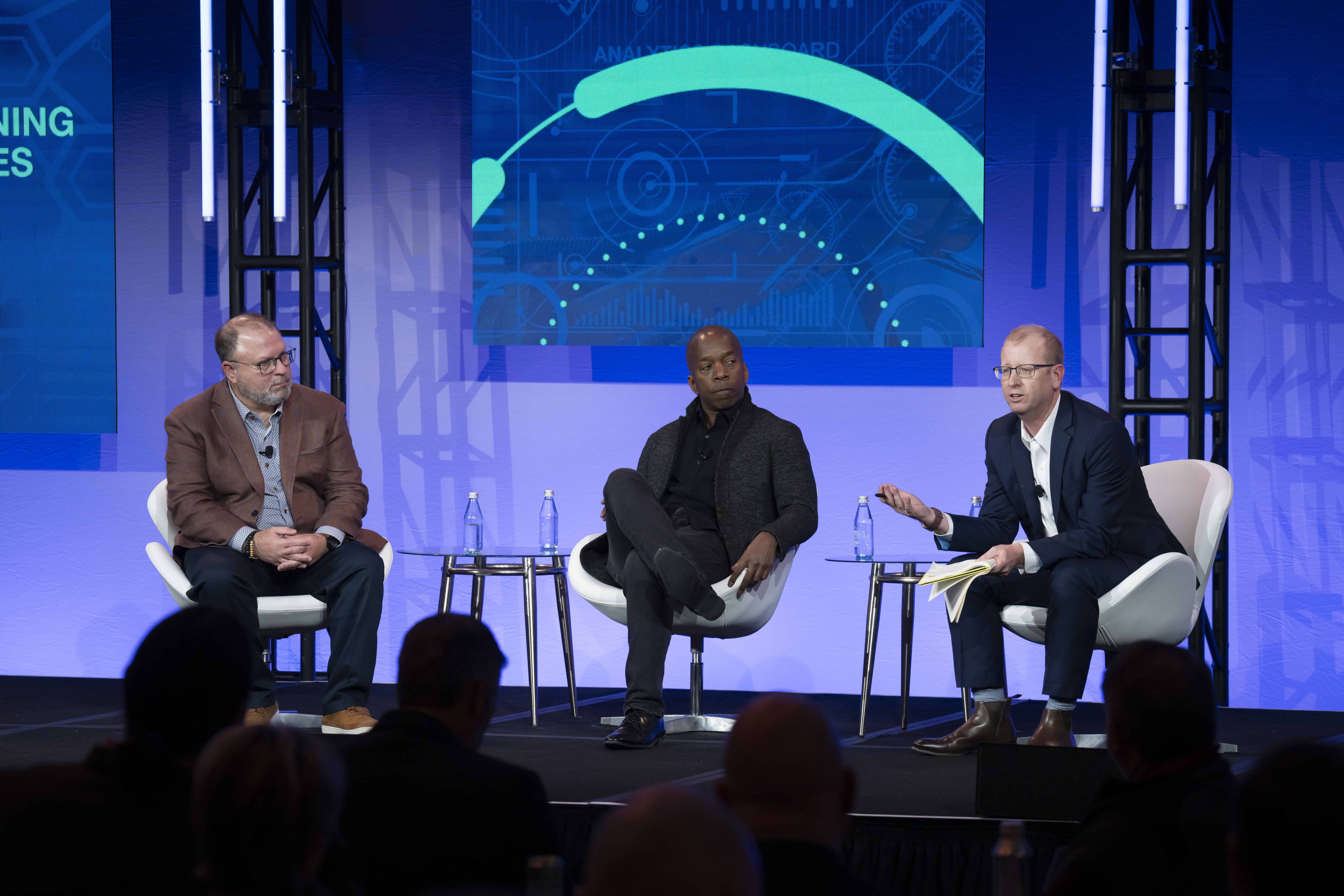
About the author:
David R. Brousell is the Founder, Vice President and Executive Director, Manufacturing Leadership Council
Welcome New Members of the MLC February 2025
Introducing the latest new members to the Manufacturing Leadership Council
Euan Anderson
VP of Manufacturing – KCNA
Kimberly-Clark
https://www.kimberly-clark.com/en-us
https://www.linkedin.com/in/euan-anderson-39316547/
Stacy Brozen
Director of Continuous Improvement NA
CNH Industrial
https://www.cnh.com/
https://www.linkedin.com/in/stacy-kelley-brozen/
Tim Windingstad
Director of Manufacturing – Fabrication
Hatco Corporation
https://www.hatcocorp.com/en
https://www.linkedin.com/in/tim-windingstad-04446b198/
Troy Youngbauer
COO
Galloway Company
https://www.gallowaycompany.com/
https://www.linkedin.com/in/troy-youngbauer-8a9012b/
Dialogue: Finding the Human Edge in Manufacturing AI
Dow’s Tim O’Neal shares how data, AI, and intentional talent placement drive operational excellence
Penelope Brown, MLC: Well, hello, everybody, and thank you for joining us for the February 2025 edition of Executive Dialogue, and today we are super excited to be talking to Tim O’Neal of Dow. He is their Global Director of Operational Excellence and Leveraged Services, and he is also one of the Manufacturing Leadership Council’s newer members of our Board of Governors. We’re really excited to have him on board and to get to know him a little bit today. So, Tim, thank you for joining us.
Tim O’Neal, Dow: Thank you for having me. I appreciate the time to talk.
PB: Let’s talk a little bit about you. Get to know you a little bit. I know you’ve been with Dow, you know, for a while. What’s your career evolution been like there? And what’s your current role? What does that entail?
TO: I’ve been with Dow 28 years. It’s going on a quick 29 years coming up soon. But I’m currently the Global Director of Operational Excellence and Leveraged Services. My role is really to support our businesses and our plant assets through best practices, like quality, continuous improvement, digital, environmental and analytical services, external manufacturing and including operations, talent management like recruiting, onboarding and with learning and talent development as well.
I began my career in 1997 in Seadrift, Texas as an environmental protection engineer. From that role I quickly moved into direct manufacturing, and I progressed through the manufacturing journey with roles in multiple technologies and production plants.
I was blessed to lead large world scale plants as well as the smaller batch facilities, where you can switch products and create different products within hours and not days. I was the site director before moving into a global environmental health safety and sustainability role to drive our corporate world leading operations, sustainability goals.
And you and I first met when I became the digital operations, IT/OT director responsible for all the manufacturing digital teams, and from that role I then joined this global director role in operational excellence.
PB: So let’s pick up a little bit. I know you just mentioned part of it is recruiting and that talent development piece. You know, really improving performance of both people and processes through that continuous learning and building those effective teams. What do you think, is the most important thing for leaders to know when it comes to encouraging team members to really perform at their best?
In operations and manufacturing, we can measure everything, but you want to make sure that you’re measuring those items that can lead to actions, whether it’s defects, outliers, and trends.
TO: To me, it’s always about placing talent and people intentionally. I see it almost like, I think, three bubbles. There’s this intersection of skills, passion in terms of what people want to do, and then what the organization needs and values. If we take the time to understand our individual team members, that intersection is where discretionary effort is born which leads to performing at our best.
PB: A few months ago you were on one of MLC’s Decision Compass calls. For those of you that may be watching this and not in the know, these are virtual working group meetings that we host.
You were discussing how Dow uses data to predict operational failure. Borrowing from that theme, how do you think the data can most easily be translated into action for manufacturers?
TO: First and foremost, I really think about measuring where it matters. In operations and manufacturing, we can measure everything, but you want to make sure that you’re measuring those items that can lead to actions, whether it’s defects, outliers, and trends. Early in my career a very experienced leader had mentioned to me one time and really gave me some great advice. He said, “Tim, manufacturing plants will whisper to you and let you know when something is not exactly right.”
And so our challenge is to really understand that and place a measurement system in place to detect the most probable failures in our facilities.
I believe in the future we will continue to see AI as a collaborative partner enhancing our capabilities and really helping us meet some of the dynamic challenges in changing marketplace in our manufacturing industry
PB: Borrowing some from that data theme, we’re hearing a lot of that from our members. It’s been an ongoing struggle to get data to a really usable format. But a lot of our members and the manufacturing community at large is really trying to get their data in shape to start using AI right? So you want to have that data in a good position to be able to feed into those algorithms and give you those actionable insights.
There’s a lot of discussion about that growing role of AI within manufacturing operations. Looking toward the future, do you see AI mostly staying in a role as strictly a digital tool? Do you see it becoming a collaborative team member? Or do you see it potentially moving into what might be considered a leadership role?
TO: First, we have a long history in our industry of AI in the early forms, if you think about machine learning, automation and optimization. However, we are in the earlier learning stages of our Generative AI journey. I see AI’s role in manufacturing and decision making as multifaceted, and it’s continuing to evolve.
We envision AI, not just as a digital tool, but an integral part of our team helping us drive efficiency and innovation. I believe in the future we will continue to see AI as a collaborative partner enhancing our capabilities and really helping us meet some of the dynamic challenges in changing marketplace in our manufacturing industry.
PB: Yeah, it’s an exciting time. And I’m really quite keenly interested to see where this all ends up going in the next 3, 5, 10 years. We’ll really see what happens there.
Talking again on that AI theme, MLC just in December, hosted our Future of Manufacturing Project event down in Orlando and we had an AI theme around that. And one of our panel discussions talked about how AI might impact decision making specifically. For example, where that decision is made such as within maybe a functional role, or why it was made based on the type of decision. What types of decisions do you think AI is going to end up influencing the most?
As long as we have reliable and governed data where folks understand that you have one source of truth, I believe that’s where we’ll have the best decision-making capabilities.
TO: I personally believe it’s limitless and I’ll go back to your statement regarding data. As long as we have reliable and governed data where folks understand that you have one source of truth, I believe that’s where we’ll have the best decision-making capabilities. And it could be structured or unstructured data, but I think where AI really will help us make decisions is to make those trends and make the data very visible and be much more quicker to analyze, so that we can make sound decisions.
For our teams, the early areas where we’re piloting this is really in plant reliability, where you can make decisions about taking equipment down and doing maintenance in a timely manner. And I think this is where AI can look at multiple pieces of data and maybe give us a quicker glance at what could potentially be a failure in our, in our manufacturing facilities.
PB: Well, Tim, thank you so much for your time today. We are, again, very happy to have you on our Board of Governors, in addition to all the other insights that you share with us and share with our members.
Thank you and we hope to see you again soon.
TO: Yes, absolutely. Thank you for the time, and I appreciate a chance to catch up.
PB: Thank you. M
About the Interviewer:
Penelope Brown is Senior Content Director for the NAM’s Manufacturing Leadership Council
Survey: M4.0 Appears Poised for A Significant Leap
Manufacturers are ramping up digital investments, with AI, automation, and smart factories reshaping the industry faster than ever.
KEY TAKEAWAYS:
● Digital transformation is a game changer. Sixty percent see it as a defining shift for the industry, marking a strong rebound in enthusiasm after a dip in 2024.
● Manufacturers digital maturity continues to increase as 75% believe they are at a mid-level maturity—up significantly from the 2024 and 2023 survey results.
● AI expectations have rebounded. A full 80% now fully or partially agree that self-managing and self-learning facilities powered by AI and machine learning are on the horizon.
Manufacturers are charging ahead with their digital transformation efforts. The Manufacturing Leadership Council’s Smart Factories and Digital Production Survey reveals an increase in smart factory maturity and optimism about continued digitization and adoption.
Fueled by an expectation of economic growth and a corresponding plan to increase or maintain smart factory investments, respondents share an outlook that includes AI adoption, end-to-end digitization, and belief that the game changing power of digital transformation is moving beyond mere table stakes.
Section 1: Economic Outlook and Investment Trends
Manufacturers are optimistic about the economy in 2025, with 69% expecting moderate growth and no recession, while only 8% anticipate an economic slowdown. Encouragingly, 11% expect inflation to ease and growth to rebound, signaling greater confidence in market stability. (Chart 1)
This optimism extends to smart factory investments, with 89% of manufacturers planning to maintain or increase spending in 2025. Within that number, it’s notable that 44% expect to ramp up investments, aligning with a broader push for digital transformation. (Chart 2) In the 2024 version of this survey, only 9% expected to increase their Manufacturing 4.0 investment.
Meanwhile, only 8% foresee a decline in spending in 2025, underscoring that despite economic fluctuations, smart factory adoption remains a strategic priority. The data suggests that as confidence in economic growth solidifies, companies are doubling down on automation and digitalization efforts to remain competitive.
1. Strong Majority See Growth on the Horizon
Q: What is your company’s outlook for the economy in 2025? (Select one)
2. 89% see smart factory investments increasing or remaining unchanged
Q: How do you expect your company’s outlook for the economy to influence M4.0 smart factory and production technology investments for 2025? (Select one)
Section 2: Smart Factory Maturity and Adoption
The digital transformation journey continues to advance, with manufacturers steadily maturing their smart factory strategies. Compared to previous years, the percentage of companies rating themselves at lower maturity levels (1-3) has declined significantly, from 57% in 2024 to just 16% in 2025. Meanwhile, those ranking their factories at a mid-level maturity (4-7) increased to 75%—up from 42% in 2024 and 58% in 2023—and 9% now place themselves in the advanced range (8-10). (Chart 3)
While progress is evident, most companies are still in experimental phases—40% are piloting small-scale projects and 6% are implementing on a single-project basis. Meanwhile, 34% are scaling these initiatives company-wide. Only 15% are just beginning their digital journey, emphasizing a strong industry-wide shift toward implementation. (Chart 4)
In fact, only 28% believe their factories are very smart or somewhat smart today. That number is expected to skyrocket to 76% by 2027. (Chart 5)
For this to happen, specific functional areas must advance. So it is a positive that manufacturers aspire to reach advanced adoption in every area included in our survey. Many find themselves in the intermediate range, with procurement/inventory management the area most ripe to move from early adoption to this stage. (Chart 6)
Despite this, full integration with business strategy remains a work in progress, with just 24% rating their integration at eight or higher on a 10-point scale, though this is an improvement from 7% in 2024. (Chart 7)
3. Smart factory journeys continue to mature
Q: How would you assess the maturity level of your smart factory journey? (Scale of 1-10, with 10 being the highest level of digital maturity)
4. Most experimenting with small-scale pilots or scaling smart factory practices
Q: Which activity best describes the primary stage of your company’s M4.0 digital efforts today? (Select one)
5. Smart factory explosion expected by 2027
Q: How “smart” do you consider your factory and plant operations to be today and what do you anticipate they will be by 2027?
6. Manufacturers still striving to reach advanced digital adoption stages
Q: At what stage of digital adoption are the following functions in your company? (Rate as early, intermediate or advanced)
7. Smart factory strategy becoming more integrated with business strategy
Q: To what extent has your smart factory strategy been integrated with the company’s overall business strategy? (Scale of 1-10, where 10 is fully integrated)
Section 3: Digitization and Automation Growth
Manufacturers anticipate a significant leap in factory-wide digitization by 2027. Today, only 2% report being extensively digitized, but this is expected to surge to 38% within the next two years. Similarly, partial digitization is set to grow from 47% to 52%, while the number of companies still in planning stages will plummet from 43% to just 5%. (Chart 8)
Production and assembly processes are on a similar trajectory. Only 6% of companies currently consider these processes extensively digitized, but this figure is projected to jump to 45% by 2027. (Chart 9)
Integration with customers and suppliers, however, remains a weak spot—just 2% report extensive digital connectivity today, though 22% expect to achieve this by 2027. (Chart 10)
Taken together, these findings highlight a growing recognition of end-to-end digital transformation as essential for operational agility and supply chain resilience, while identifying an opportunity for improved digitization between manufacturers and their customers and suppliers.
8. Significant end-to-end digitization on the horizon
Q: To what extent are your factory operations fully digitized end to end today, and what do you anticipate they will be by 2027?
9. 92% predict extensive or partial digitization of production/assembly by 2027
Q: To what extent are your production/assembly processes digitized today, and what do you anticipate they will be by 2027?
10. Digital integration with customers and suppliers lags behind in-house digitization
Q: To what extent are your production functions digitally integrated with customers and suppliers today, and what do you anticipate they will be by 2027?
Section 4: Future of Factory Models and AI-Driven Operations
Manufacturers envision a hybrid future for their factory networks, with 44% expecting a mix of small and large facilities, reflecting the need for both localized agility and economies of scale. Large-scale production remains dominant, with 40% favoring large factories or networks of large facilities, while only 10% see a shift toward smaller, more agile production models. (Chart 11)
AI-driven automation is also gaining traction. Almost one quarter (23%) of manufacturers fully agree that factories will evolve into self-managing, self-learning facilities, a dramatic increase from just 6% in 2024. Another 57% partially agree, suggesting growing confidence in AI’s ability to optimize operations. This shift reflects the industry’s increasing focus on AI-driven decision-making and predictive analytics as key enablers of the smart factory vision. (Chart 12)
11. Only 10% see small, agile factories and networks as the future
Q: What is the expected future state of your factory model?
12. Expectation of self-managing, self-learning factories increase significantly
Q: Thinking about the impact of technologies such as AI and machine learning, to what extent would you agree or disagree with the following statement: “Tomorrow’s factory will evolve to be a self-managing and self-learning facility.”
Section 5: Technology Adoption and Priorities
The 2025 survey highlights strong momentum in advanced technologies, particularly cybersecurity (73% scaling/at scale), IIoT sensor networks (46% scaling/at scale), and advanced analytics (56% scaling/at scale). AI adoption is also accelerating, with 22% of manufacturers now scaling/at scale with AI solutions, and another 42% piloting at least one AI project. Machine learning follows a similar trend, with 21% scaling/at scale and 29% planned for future deployment by 2027. (Chart 13)
AI’s perceived impact is rising sharply—34% now see it as very significant, compared to just 10% in 2024. (Chart 14) This signals a shift from experimentation to real-world application, as manufacturers increasingly leverage AI for predictive maintenance, process optimization, and adaptive automation. However, emerging technologies like the metaverse, blockchain, and exoskeletons remain niche, with over 70% of companies having no plans to adopt any of them. (Chart 13)
13. Cyber, advanced analytics, IIoT sensor networks top production operations tech list
Q: Where does your company stand in regard to the following technologies in its production operations?
14. AI’s expected significance increases
Q: Looking ahead over the next few years, how significant an impact will AI have on your production operations?
Section 6: Challenges and Benefits of Digital Transformation
Manufacturers continue to grapple with major roadblocks in their smart factory journeys. Nearly half (49%) cite outdated legacy equipment as their top challenge, up from 39% in 2024, highlighting the complexity of modernization. Workforce-related barriers are also growing—43% point to a lack of skilled employees, a sharp increase from 24% in 2024. Resistance to change remains a persistent issue, with 42% citing organizational culture as a challenge, though this has improved from 53% last year.
But it’s not all bad news. In 2024, a lack of leadership buy-in and access to adequate budget/investment both ranked among the top four roadblocks. Improvements have been seen in both these issue areas. Leadership buy-in and increasing budgets may very well prove to be leading indicators that the current issues discussed above may become lower hurdles rather than roadblocks. (Chart 15)
Despite these current roadblocks, companies recognize the benefits of transformation. Nearly two-thirds (63%) rank operational efficiency as the top expected gain, a significant jump from 40% in 2024. Better decision-making (49%) and cost reduction (44%) follow closely, demonstrating that digital adoption is increasingly seen as a performance and profitability driver. (Chart 16)
Notably, the percentage of companies expecting digital transformation to create a competitive advantage has soared from 11% in 2024 to 38% in 2025. While the majority still see digital transformation as table stakes, the dramatic increase in those who see it as a competitive advantage marks a major shift in strategic thinking. This shift suggests that as adoption accelerates, digital capabilities are becoming key differentiators rather than mere necessities for survival. (Chart 17)
15. Legacy equipment, lack of skilled employees and organizational culture are biggest smart factory roadblocks
Q: What do you feel are your company’s primary roadblocks to implementing your smart factory strategy? (Select top 3)
16. Better operational efficiency outpaces all other smart factory benefits
Q: What are the most important benefits and opportunities your company hopes to realize from embracing a smart factory strategy? (Select top 3)
17. Digital transformation still seen as table stakes for majority, but increasing number see it as a competitive advantage
Q: Do you believe that digital transformation of your company’s manufacturing operations will create a unique competitive advantage for your company or is it merely table stakes to remain in the game?
Section 7: The Strategic Value of Digital Transformation
After a dip in enthusiasm in 2024, manufacturers now overwhelmingly see digital transformation as a game-changer—60% believe it signals a new era for the industry, up from just 26% last year. Another 40% still see it as significant but not transformative, while no respondents consider it insignificant. Apart from our 2024 survey, these numbers have remained largely consistent over the past four years. (Chart 18). M
18. After dip in 2024, majority now see digital transformation as a clear game changer
Q: Ultimately, how significant an impact will digital transformation have on the manufacturing industry?
About the author:
Jeff Puma is content director at the NAM’s Manufacturing Leadership Council.