The manufacturing industry has spent a lot of time, effort and money on making its processes more efficient over time. And now the industry is investing in the Industry 4.0 philosophy to minimize wastage and downtime, leveraging technologies including 3D printing, digital twins, and predictive maintenance. Powering all of these investments is data.
Late last year I had a number of conversations with manufacturing professionals who manage products throughout their lifecycles – from the 3D CAD design phase, through review, fabrication, sales and marketing, and even further into customer usage and after-sales. They each told similar stories of breakdowns in the processes for creating, distributing, and consuming content that transfers vital knowledge about their products. In addition, they all identified significant negative impacts stemming from these problems. Errors, delays, and missed sales opportunities were frequent complaints.
I came away wanting to know more about these problems, their outcomes, and the underlying causes. What is driving ineffective product documentation workflows and processes at organizations that otherwise appear to be investing heavily in efficiency-based initiatives and cutting-edge tech?
In a bid to find out, my company, Canvas GFX, surveyed over 500 manufacturing professionals across a broad range of verticals, including automotive and electric vehicles, aerospace and defense, new space tech, industrial machinery, and more. The results showed these challenges exist widely across the manufacturing sector, suggesting an endemic and interconnected problem.
We’ve dubbed this problem Product Communication Disorder. For many companies, Product Communication Disorder is perceived, managed – and often tolerated – as a series of departmental workflow challenges. The data suggests the problem cannot be solved unless assessed and addressed with a company-wide perspective.
Where have manufacturers gone wrong?
There are three distinct stages within documentation and knowledge transfer where problems arise, the first being the creation of product content.
As it stands, creating product communication content is time-consuming and complicated, requiring input from multiple team members across an organization. Our research highlighted how critically deficient current workflows are, with clear room for improvement. The stats lay the issue bare, with over 95% of manufacturing industry professionals reporting that projects or products at their company had suffered errors or delays as a result of inefficient workflows for the creation of product communication.
But the problem runs deeper than content simply being late or too time-consuming to create. While the data says these are both true, our survey also suggested that the processes underpinning the creation of content are themselves flawed. For more than one in three respondents (36%) workflow bottlenecks stemmed from too many people being involved in content creation. Meanwhile, the lack of skills or software needed to be able to properly visualize 3D models, the basis for many documentation illustrations, was cited by one third of respondents.
Collaboration is another area fraught with challenges. In fact, 73% of respondents in our survey said they had experienced product or project errors or delays in the past two years as a result of difficulty collaborating on content.
Just as content creation at manufacturing companies is fragmented in terms of departments, skills and software, the collaborative process also appears to want for some kind of central management. According to almost three quarters of survey respondents, a primary problem appears to be too many channels (including email, Microsoft Teams, Slack, and other voice and video calling solutions) being used to manage collaboration, review and feedback on product content. The result of this vital communication happening across a range of channels according to 3 in 4 respondents is that it is easy to miss feedback on important documentation and content.
Lastly, the survey revealed serious concerns around the ability of workers to access the most up-to-date documentation materials. For many organizations this appears to be a struggle, while the problem is aggravated by managing a range of different content formats. It’s vital to remember that consuming content is what this entire process is about.
Worryingly, 85% of respondents said that outdated documentation in circulation had resulted in errors and delays over the last four years, and over a third (36%) said their company struggled to manage the rate at which content becomes outdated. More alarming still is the large proportion of respondents who conceded that their company has difficulty ensuring everyone who needs access to content is able to access the most up-to-date version of each document (54%).
Solidifying Industry 4.0 gains
The overarching issue is that manufacturers spend heavily to update their processes to reduce defects and ensure products make it to market on time, documentation issues are continually undercutting those investments.
Perhaps the starkest illustration of the problem lies in the fact that 73% of respondents felt that inefficiencies in their product communication processes were undermining gains made through other technology initiatives.
But it’s not all doom and gloom, and there is a silver lining here. The findings pointed to evidence that manufacturing companies are looking to cure the problem, rather than simply manage the pain. While the data is clear, so are the actions companies can take.
By addressing their problems in product documentation, companies can take a huge leap in realizing the full potential that Industry 4.0 offers and maximize their investments in it.
About the author:
Patricia Hume is Chief Executive Officer of Canvas GFX.
Are Your People On Board?
Cultural Transformation Is the Key to Success in Digital Transformation
Though once considered a radical concept in the eyes of some, the necessity of digital transformation is now embraced by most organizations. The question is no longer whether to digitally transform — it’s now how to do it. But often, those discussions focus myopically upon the technologies involved.
That’s a mistake.
People, after all, are the ones driving change. Technology is the tool they use to do so. If the attitudes, behaviors and goals of your organization’s people — your culture — are not on board with your digital transformation goals, your transformation will likely fail even if you have the right technology in place. Having clear alignment between your technical objectives and your company’s culture is essential for success — in fact, organizations that take a human-centric approach to digital transformation are 2.6 times more likely to see success.1
Five common business blockers to cultural change
There are several common stumbling blocks that may significantly impede your progress along the path to digital transformation. The most vexing challenges revolve around five key cultural issues:
- Organizational data isolated in functional or hierarchical silos.
- A lack of the skills needed to enable digital transformation.
- The breakdown of inter-team communication and collaboration.
- Cultural resistance to change rooted in lack of understanding of transformation goals.
- Fear and worry about job insecurity, or a lack of psychological safety, among employees.
Any one of these cultural barriers presents a significant speed bump to the transformation process. The presence of all five within a single organization — not an uncommon scenario — wreaks havoc upon an organization’s efforts to transform.
Stepping over those stumbling blocks
Transformation undeniably involves change — and change and human nature often have a stormy relationship. People tend to resist change, particularly when it makes them feel isolated or left behind. How can companies overcome these stumbling blocks to enable and encourage cultural change in support of digital transformation? The answer involves a mix of technology and people-centric management.
To eliminate data and skillset silos without disrupting your key business processes, you need to gradually build cross-functionality across teams. Consider using tools and techniques such as Kaizen (a management strategy that supports ongoing, incremental change), which many organizations have found to be crucial for success. A top-down commitment to opening silos is equally important; however, the true key to breaking down silos is about understanding, engaging and promoting collaboration across both the formal structures and the informal networks that exist across the organization.
Recently, research has found that the key to identifying and engaging these informal networks is by identifying influencers across an organization and engaging with them. Each silo represents a comfort zone for the group of employees that operates within that silo, and employees may be reluctant to move away from those comfort zones. By activating networks across the organization, company leadership can promote collaboration without incentivization.
Similarly, it’s essential to nurture teamwide collaboration and communication in ways that are nonthreatening to individuals and team cultures. While specialized skillsets and knowledge specific to a team (or even a single task) is valuable to the entire organization, individuals who hold that knowledge often consider themselves the owners of that knowledge — an ownership that they may be reluctant to surrender for fear of diminishing their own value. Commending employees for exceptional knowledge sharing and skill development creates a culture of collaboration while promoting candid communication.
Innovation culture and success factors for digital transformation
Leadership should also be sensitive to the language used in communicating transformation initiatives. Phrases such as “breaking down silos” can feel threatening to people working in those so-called silos. Functional areas with their own domains of expertise and knowledge exist for important reasons — and will continue to exist — so leaders should instead talk about “weaving silos together” to achieve cross-functional integration while preserving the benefits of domain expertise.
Adopting agile approaches serves to foster the evolution of cultural shifts across teams, enabling them to be more cross functional. Another tool that can be highly effective in breaking down a range of barriers to collaboration and communication — including differences in age, gender and ethnicity — is reverse mentoring, where younger employees are paired with executive team members to help those executives connect with a younger demographic. Creativity, too, is important when it comes to breaking down cultural cliques. Even discouraging teams from keeping to themselves in settings like company cafeterias can be effective.
Finally, executive leadership, like all other members of the organization, must also evolve. They must embrace the goals of transformation and become comfortable with the higher levels of ambiguity that characterize today’s marketplace.
That said, technology does play a major role in supporting digital transformation initiatives. The right technology can make all the difference in fostering the cultural shift necessary for successful digital transformation. Today’s digital tools can guide effective collaboration, enhance efficiencies, enable standardization and encourage innovation. For example, Hitachi designed a cross-functional 2-day Smart Manufacturing Solution Envisioning Workshop for Logan Aluminum that helped key employees better understand the benefits of specific digital transformation initiatives.
Transformation is really about people
Business organizations are often perceived as lifeless, faceless entities. But in truth, each organization is a collection of people — people who must work together to make the business successful. That’s why it’s so important that everyone in your organization is on board with both the processes and goals of transformation.
Ultimately, fostering positive cultural shifts among your people is the best way — and, realistically, the only way — to ensure that your digital transformation goals can be achieved. Because, in the end, digital transformation is all about your people; a journey begun for your people and achieved by your people.
Hitachi’s Social Innovation imperative is all about unlocking value for society through the power of technology and people. For more tips about getting ahead by thinking ahead, visit our Social Innovation page.
About the authors:
John Brinegar, Director, IoT Solution Architecture, Hitachi Vantara
John Brinegar leads the Solution Architecture team at Hitachi Vantara, and has been leading IIoT projects at Hitachi customer sites for eight years. In addition, Brinegar led the architecture, development, and launch of Lumada Manufacturing Insights, an analytics platform for optimizing performance, maintenance and quality operations. He has extensive background deploying analytics systems into a variety of manufacturing sub-verticals, including electronics, pharma/biotech, metals, automotive, and others, along with IIoT software development and integration in telecommunications, health care, and enterprise markets.
David R. Brousell, Co-Founder, Vice President and Executive Director Manufacturing Leadership Council
David R. Brousell is the Co-Founder, Vice President and Executive Director of the Manufacturing Leadership Council, the digital manufacturing arm of the National Association of Manufacturing, the largest association of manufacturers in the United States.
In his role as head of the MLC, Brousell sets the strategic direction of the organization and oversees day-to-day activities across the MLC’s portfolio of live and virtual events and thought-leadership content generation. Brousell is a member of the NAM Leadership Team and is also a member of the MLC’s Board of Governors. In his more than 40-year career, Brousell has served in numerous leadership positions in companies large and small.
1Errol Gardner, Norman Lonergan, Liz Fealy, “How transformations with humans at the center can double your success,” EY, June 24, 2022, https://www.ey.com/en_gl/consulting/how-transformations-with-humans-at-the-center-can-double-your-success.
Digital Tech is Cornerstone for Sustainability
MLC Master Class session with NTT DATA and Microsoft lays out formula for net-zero success
In his introduction to MLC’s recent Master Class session, Harnessing Digital Technology for a Sustainable Future, Paul Tate laid out the high stakes involved in sustainable manufacturing.
“This is one of the most existential challenges and sources of opportunity for the manufacturing industry over the next decade,” said Tate, MLC’s Co-Founding Executive Editor and Senior Content Director.
To get to a sustainable, net-zero future, application of both data and analytics are critical. During the Master Class, expert speakers Baskar Radhakrishnan of NTT DATA and Rebecca Christiansen of Microsoft defined the challenges and described how digital technology can help manufacturers accelerate decarbonization.
According to Christiansen, Microsoft’s Americas Azure IoT Specialist Director, nearly one-third of the world’s energy consumption and roughly 20% of CO2 emissions are attributable to the manufacturing industry. To help combat climate issues, she pointed to the 5,000 companies that have committed to net zero as part of the United Nations Race to Zero Campaign.
“While a lot of companies have made commitments, building the strategy, backing it with detailed plans and execution methodologies has been really tough,” Christiansen stated. “It’s really up to all of us, collectively, to figure out what technologies and what strategies should be implemented to go after this.”
Further, Baskar Radhakrishnan shared this must be looked at not only through the strategic lens, but also from a tactical, operational technology perspective.
“From a technology perspective, there is a lot of data available coming from the supply chain, coming from your OT systems, coming from all over your networks,” said Radhakrishnan, NTT DATA’s Strategic Advisor for Manufacturing. “But how you derive some meaningful insight out of that is a huge challenge.”
To show how sustainability investments can provide value, NTT DATA and Microsoft have partnered together to demonstrate quick return on investment for their customers. They have designed a production-level pilot that can be set up in a small-scale production environment at a customer site in less than 12 weeks. This allows the implementation team to show its organizational leaders the opportunity, value and positive ROI associated with investing in an energy management or a waste reduction system.
Beyond demonstrating ROI with this pilot, it is important to also look at sustainability from a business objectives perspective.
“There is a gamut of technologies involved,” Radhakrishnan said, “so technology is an enabler. It’s not going to solve your problem unless you have the process straightened out and unless you identify the range of possible options for transitioning towards the net-zero targets.”
In part because organizations cannot improve things they can’t measure, NTT DATA and Microsoft are using the Azure digital twin to help companies meet their sustainability goals.
“We tackle the problem of data by connecting directly to energy data sources – be it power meters, submeters on equipment, or utilizing building management systems. From there we create both real-time visibility to energy usage and provide analytics about the energy usage, trends, and patterns,” said Radhakrishnan.
According to the Master Class speakers, manufacturers shouldn’t be afraid or overwhelmed with the prospect of using digital twins in this process. While they can seem complex, they are simply virtual replicas of physical assets, or “high-fidelity digital representations of the physical world,” as Christiansen called them.
“Once you’ve got [the physical world] modeled, you can garner insights, you can look at consumption, you can look at interaction, you can think about how you can manipulate or even identify fault detection or anomalies in advance, which help you really optimize keeping your manufacturing line healthy, runtime up, and throughput maximized,” she said.
The outcomes from using digital twins are clear, including improved production capacity and inspection efficiency with reduced energy usage and CO2 emissions. Plus, the twin allows the user to look at energy management on many level: at the product, factory, or even supply chain levels. That includes progress toward net-zero goals.
“That’s extremely important because you’re completely taking the guesswork out of this,” said Radhakrishnan. “You need a systematic way of tracking, reporting, recording, and being able to model and show progress not only to your board but also to your external stakeholders as well as investors.”
In fact, he said, if you are not making progress, the digital twin in combination with artificial intelligence allows you to model and fix problems and see how you are progressing toward your vision.
Beyond the technology itself, the final piece to the puzzle is creating an organizational culture with proper funding, training, and resources.
“We’re seeing a lot of organizations hire chief sustainability officers,” said Christiansen. “That’s an incredible start, but that’s a single person. It has to come through the entire culture of a company.”
If the culture is not there, she warns, it will be a challenge to implement these changes.
As the Master Class demonstrated, net-zero goals are challenging, but they are also achievable. Digital technologies like NTT DATA and Microsoft’s production-level pilot can build a case to create sustainability programs that create substantial results. Establishing goals and a strategy, utilizing digital twins, analyzing the data and analytics, and creating an organizational culture where the entire company is behind the mission are all key to accelerating a decarbonization effort.
Visit NTT DATA’s sustainable manufacturing page to learn more about this topic.
Why Women’s Voices in Manufacturing Matter
What do women in manufacturing think about the business they’re in? It’s not something we hear a great deal about, which is perhaps not surprising. Manufacturing is a male-dominated industry, after all. For half a century women have represented around 30% of the U.S. manufacturing workforce, peaking at 33% in 1990, according to the U.S. Census Bureau (USCB).
By number, most female employees are found in production, transportation, and material moving. They are assemblers and fabricators, says the USCB, inspectors and testers, among other roles.
But, proportionately, women enjoy far greater representation in the sales and office-based roles of manufacturing companies, where they are in the majority, holding 51.7% of the roles.
So it’s important to know what they think. Earlier this year we surveyed over 500 manufacturing professionals from a range of industries, including aerospace and defense, automotive, space, electric vehicles, autonomous vehicles, to understand the challenges associated with product-related communication and knowledge transfer.
In line with the USCB data, female employees accounted for 28% of responses. And while we did not set out to measure gender distribution across industries (and so, offer no conclusive insight) there was some interesting variation by sector. For example, women accounted for just 21% of responses in the aerospace and defense sector while in the emerging SpaceTech sector they accounted for 35%, and in the automotive sector 32%.
When it comes to existing product communication workflows – the ways in which documentation describing products and processes is created, shared, and consumed – the data was clear: 71% of female employees believe there is room for improvement in these workflows, and the same proportion believe documentation challenges at their organization are getting harder to manage as the company grows. Ninety-seven percent of female respondents said they had seen products or projects hit by errors or delays as a result of documentation being late, inaccurate or unclear, or outdated.
Digging further into specific elements of the workflows, and perhaps indicating areas where female employees may have greater insight, women were more acutely concerned about bottlenecks associated with the creation of product documentation than their male counterparts. Sixty-five percent of female respondents reported that creation bottlenecks are a frequent problem at their organization compared to just 51% of male respondents.
They also felt more strongly that managing distribution of, and access to, important documentation was a problem, with 43% of women saying this was difficult for their organization to manage, compared to 36% of male respondents.
With documentation creation and consumption routinely involving collaboration between separate departments, we asked respondents how well different disciplines such as engineering and marketing professionals were able to collaborate. Here, female respondents were perhaps more optimistic than their male counterparts, with 30% saying there were no difficulties, compared to only 20% for male respondents.
In terms of the outcomes of these workflow challenges, women again registered somewhat higher levels of concern than men. Forty percent of female respondents said they had witnessed wastage through product defects as a result of product documentation being delayed, inaccurate or unclear, or outdated, compared to 38% of male respondents. And 38% of women said the same problems had led to delayed or missed sales opportunities, compared to 32% of male respondents; interesting considering the USCB data which showed higher numbers of female workers in manufacturing sales roles.
Perhaps more worryingly, one in three female manufacturing employees believe their organization is not actively seeking ways to improve documentation workflows and processes, which suggests a huge opportunity for improvement if the problems these women are identifying can be highlighted and understood at the leadership level.
So what does success look like for women in manufacturing? Well, with 37% of female respondents saying the applications used in documentation workflows are unsuited to the task, 33% saying there are too many applications involved, and 39% saying there are too many people involved, the data suggests women want to see more autonomy and efficiency in these crucial knowledge transfer workflows.
More than 2 in 3 of female respondents said it would be beneficial to use a single application for the creation of all types of product content, while 62% said it would be beneficial if all collaboration were also to happen in one application channel. Meanwhile, 66% said they believed it would be beneficial if the company was able to track and measure document access and usage.
As in any sector, women have an important role to play in manufacturing and it is essential we understand their perspective on the challenges companies face. A clear takeaway from this research is that female employees believe the manufacturing industry faces a defining challenge when it comes to poor communication and product documentation, which is intricately connected to the success of the entire organization. And when the processes in place break down, the result is self-inflicted damage that could – and should – have been avoided.
About the author:
Patricia Hume is Chief Executive Officer of Canvas GFX.
Digital Solutions Drive Sustainability in Manufacturing
It’s an interesting parallel: the global drive toward sustainability may directly improve carbon emissions and help slow climate change to the benefit of all. And correspondingly, manufacturing companies that successfully transform to contribute to global sustainability will positively enhance their own ability to thrive.
The reverse, of course, is also true — manufacturing companies that fail to meet global environmental, social and governance (ESG) benchmarks will likely find themselves falling behind competitors, being shunned by consumers and, ultimately, facing irrelevance.
It’s a stark reality and a daunting task. Manufacturers must successfully digitally transform in ways that enhance sustainability. But the potential benefits of that success are virtually unlimited.
The digital transformation question is no longer a question
A couple of decades ago, a discussion about digital transformation and sustainability in manufacturing might have involved a number of participants advocating both for and against the need for change — or at least how much things would really need to change. But now, driven by tightening regulations, pressures from global markets, the increased focus on ESG metrics and shifting customer preferences, digital innovation is no longer optional — and manufacturers know it.
According to a recent survey conducted by IndustryWeek and Hitachi, 99% of manufacturing executives consider their company to be committed to sustainability initiatives when compared to others in their industry.
Manufacturers are also beginning to recognize that the benefits of success in this transformation extend beyond the primary goals of operational efficiency, increased profitability, and productivity and safety improvements. Respondents to the survey also noted the potential for significant improvements in:
- Market share
- Influence on industry and society
- Ability to attract new talent
- Brand recognition and reputation
- Employee retention and morale
But knowing you need to transform and knowing how to do it are two different things. Most manufacturing companies are aware of the need to digitally transform, and they know that the changes involved will be substantial. These top three areas of focus emerged in the survey as the most important for meeting sustainability goals:
- Production processes. Streamlined processes that save energy, reduce waste and increase visibility all contribute to making factories more sustainable.
- Workforce training. Manufacturers can maintain and improve sustainability-based work practices and smart-work behaviors by using digital information-sharing tools to reduce the knowledge drain as skilled workers retire.
- Supply chain. More efficient supply chains can save energy, reduce warehouse storage needs and streamline logistics to reduce truck rolls — all of which help lower carbon footprints.
For enhanced sustainability, manufacturers must pursue ways to improve efficiency, lower their energy usage, integrate alternative sources and energy management systems, and lower their carbon footprint from end to end.
And it all starts with knowing where you are today.
Sustainability in manufacturing is built upon a foundation of data
Manufacturers that are exploring digital transformation initiatives know that data will form a large part of the answer to the sustainability challenge. In fact, the survey respondents consider data analytics the most important technology for managing sustainability, with a primary focus on machine learning and artificial intelligence (AI).
Unprecedented quantities of data are now available to organizations, but deriving insights from that data quickly and efficiently requires digitalization. Digital technologies that leverage that data into operational benefits and enhanced efficiencies are the key to enabling quantum improvements in manufacturing sustainability.
Leading manufacturing sustainability by example
Hitachi is a leader in providing sustainable solutions for manufacturing, having developed and operationalized many of the cutting-edge digital technologies that companies use to meet their ESG goals. For example, Lumada Manufacturing Insights helps manufacturers such as Logan Aluminum develop data-driven operations, increase supply chain visibility, run predictive models and enable smart factory solutions that use data to drive productivity, lower asset downtime, extend remaining useful life, and promote sustainability in manufacturing processes.
Hitachi is also one of the largest manufacturing companies on the planet. Its global presence in both manufacturing and technology uniquely positions it as a leader in sustainability solutions. Many technology companies offer recommendations for bolstering manufacturing sustainability, but Hitachi offers advisory services, hands-on guidance, domain and business process expertise, and more — all delivered and backed up with hundreds of use cases and successful delivery examples. Hitachi’s Omika Works factory, for example, was recognized by the World Economic Forum in 2020 as an advanced Fourth Industrial Revolution Lighthouse, an honor given to factories that are world leaders in the adoption and integration of groundbreaking technologies.
But the bottom line is Hitachi’s reputation for leading by example. The company is committed to achieving carbon-neutrality at its industrial facilities by 2030 and investing $13 billion over the next few years in green technologies research and development.
Transformation should be simpler.
Hitachi stands ready to help manufacturing companies achieve their sustainability goals. Recent sustainability-enhancing successes achieved by Hitachi manufacturing customers include:
- Improved operating rates achieved by consolidating multiple factories for automobile parts manufacturing companies
- Improvements in equipment operation rates and reduced manufacturing lead times for an agricultural machinery manufacturer
- Reduced productivity losses from equipment stoppages and improved preventative maintenance processes for a printed circuit board manufacturer
Learn more about how Hitachi can help you more effectively leverage your data and achieve your sustainable future.
About the authors:
David McKnight is Director of Digital Manufacturing Solutions, Hitachi Vantara. McKnight joined Hitachi in 2016 with an eye to broaden his work in industrial IoT and digital manufacturing. At Hitachi Vantara, he is driving manufacturing operations excellence solutions with clients across various industries. Prior to his tenure with Hitachi, McKnight has focused on providing industrial automation and SAP manufacturing solutions throughout the world. He is passionate about enabling manufacturers and their operators, supervisors and management to employ technology to maximize productivity, quality, safety and flexibility.
Shamik Mehta is the Director of Digital Services and Solutions Marketing for Hitachi Vantara. Mehta has around 25 years of experience in product and strategic marketing in IoT, data management and data analytics, semiconductors, renewable energy, and e-mobility solutions. He’s held roles in chip design, pre-sales, product management and marketing for technology products, including software applications and data platforms for industrial applications. His experiences include six years at SunEdison, once the world’s largest solar, wind and energy storage independent power producers, leading product management, operations, business development and marketing.
Mehta has experience managing global product marketing, GTM activities, thought leadership content creation and sales enablement activities for technology and software applications for the smart energy, electrified transportation and manufacturing verticals. Mehta is a Silicon Valley native, having lived, studied and worked there since the early 90s.
Enhancing and Demonstrating Environmental Stewardship
Supply Chain Control Tower Solutions for Sustainability
Nothing tests the resiliency of supply chains like a global pandemic — as everyone from CEOs to consumers desperately seeking toilet paper know all too well. And, as the COVID-19 pandemic so vividly demonstrated, organizations around the globe need help in monitoring and strengthening their supply chains.
But all organizations — and multinational corporations, in particular — must also be concerned about the sustainability standards of their supply chains. Issues such as climate change, fair labor practices and environmental impacts must be considered along with issues affecting supply chain resiliency. Yes, focusing on these issues is the right thing to do. But increasingly, ensuring supply chain sustainability standards is also essential to maintaining competitiveness and market share. A recent Deloitte survey1 found that nearly a third of consumers have abandoned a brand or product because of concerns about sustainability or ethics. Nearly half of consumers want more insights into the sourcing of products and impacts to sustainability.
So, modern consumers indeed want to find toilet paper fully stocked on the store shelves. But they also expect that product, and all products, to have been produced and sourced sustainably and ethically.
The big ask
Maintaining supply chain viability, especially in recent times, can be pretty challenging. Adding the task of ensuring and demonstrating that all the many supply and labor sources that feed into that chain meet modern sustainability standards — well, that’s a big ask. But that’s the task that’s faced by enterprises that seek to remain competitive.
It’s not an easy task. And some of the biggest brand names on the planet have made some embarrassing stumbles in attempting to ensure the sustainability and ethics of their suppliers. Some suppliers were cited for violating worker safety conventions and fair labor practices. Others were found to have dumped toxic chemicals into rivers that serve as the source of drinking water for millions of people.
Enterprises need help in successfully monitoring all of the many streams and tributaries that flow into a typical modern supply chain. They need a high-level focus that provides oversight of all supply routes and suppliers — they need a control-tower view.
A control tower solution for supply chain sustainability
Hitachi has developed supply chain control tower solutions explicitly designed for monitoring and managing the complexity of modern supply chains. Powered by Hitachi’s Lumada Manufacturing Insights, these solutions integrate process monitoring, data collection from Internet of Things (IoT) sensors and satellites, historical records and predictive algorithms to provide alerts about potential disruptions.
According to the Association for Supply Chain Management, more than half of all companies lack complete visibility into their supply chains, leaving them vulnerable to disruptions.2 Hitachi’s supply chain control tower solutions offer enterprises a paradigm shift in supply chain management: predicting the future of the supply chain rather than simply reacting to disruptions as they occur.
But Hitachi’s supply chain control tower solutions can go far beyond simply helping to keep a supply chain intact. These solutions can also be used for effectively monitoring, managing and demonstrating the sustainability of supply lines, from beginning to end — as the following ongoing Hitachi pilot project demonstrates.
Supply chain sustainability safeguards one of the seven natural wonders of the world
Australia’s Great Barrier Reef is the largest coral reef on the planet and is counted as one of the world’s seven natural wonders. But the majestic beauty of the Great Barrier Reef is sustained by a fragile ecosystem. And in just the past three decades, that delicate ecosystem has been pummeled by a combination of climate change fallout and damage from pollutants. Much of the pollution that affects the reef originates from agriculture.
Recently, Hitachi and Horticulture Innovation Australia teamed up on a project that utilizes Hitachi’s supply chain control tower technologies to help enhance the environmental stewardship of farmers in the Great Barrier Reef catchment area. The project encompasses four remotely monitored farms growing nursery, vegetable, macadamia and banana crops. The project’s goal is to use digital dashboards to enhance sustainability efforts by helping the farms produce more with less waste and increase their compliance with governmental directives.
This project will demonstrate the viability of both managing and monitoring even the most remote endpoints of a supply chain using Hitachi’s data-driven control tower technologies. The project is expected to enhance supply chain sustainability and resiliency while providing the product-source transparency that has become so vital to modern consumers.
Supply chain sustainability is now an imperative
Not so long ago, any enterprise efforts toward ensuring increased supply chain sustainability were worth a virtual pat on the head — and not much more. But that’s no longer true. Increasingly, maintaining goodwill in the eyes of stakeholders and consumers requires that supply chains be both resilient and sustainable. Enterprises that manage to do both enjoy a competitive edge that far transcends the ability to simply keep toilet paper on store shelves.
Discover how Hitachi’s supply chain control tower solutions can help you keep your supply chain intact while providing the sustainability that consumers demand.
About the author:
Owen Keates, Industry Executive, Manufacturing Practice, Hitachi Vantara
Keates leads the development of Hitachi Vantara’s digital supply chain solutions. With over 25 years of experience in supply chain management including global supply chain manager of a logistics company and vice president of a supply chain consultancy, he has led many digital transformation programs across a range of industries from beverages and agri-food to transformer, motor, construction, vehicle assembly as well as chemical and paper manufacturing. Qualified as a chemical engineer, Keates has production, project and executive management experience in manufacturing and is currently completing a part-time Ph.D. in process intelligence.
1 – “Shifting sands: Are consumers still embracing sustainability?” Deloitte, 2021, https://www2.deloitte.com/uk/en/pages/consumer-business/articles/sustainable-consumer.html
2 – “Over Half of Companies Lack Clear Picture of Their Own Supply Chain, According to New Report from ASCM and the Economist Intelligence Unit,” Association for Supply Chain Management, February 23, 2021, https://www.prnewswire.com/news-releases/over-half-of-companies-lack-clear-picture-of-their-own-supply-chain-according-to-new-report-from-ascm-and-the-economist-intelligence-unit-301233340.html
MLC Announces New 2022/2023 MLC Critical Issues Agenda
The Journey to M4.0 Value
The manufacturing industry is at a pivotal point in its history.
Driven by market forces to become more agile, innovative, resilient, cost efficient, and sustainable, companies of all sizes are pursuing a future vision for business value enabled by digital technologies that will redefine the rules of competition, how work will be performed, how companies will be organized, and how leadership must lead.
We term this future state: Manufacturing 4.0.
Such a comprehensive enterprise-wide transformation requires a three-dimensional approach: mastering the challenges and opportunities of advanced digital tools and data; improving organizational structures and cultures; and developing new workforce talent and leadership skills.
While shaped by company size, sector, and level of digital maturity, all manufacturers share the need for a common set of key M4.0 competencies.
These enable them to drive value from digital investments in critical areas of business activity – from product design and innovation, to supply chains and customer relationships, to more eco-efficient manufacturing operations.
The Manufacturing Leadership Council’s new Critical Issues agenda for 2022/2023 is a specifically designed to help manufacturers align their thinking and best practices to deliver true business value from their journey to M4.0.
The MLC’s Critical Issues Process
The Manufacturing Leadership Council’s Critical Issues agenda, now in its 11th year, is the outcome of a unique, annual, member-driven process to identify the most urgent and important issues facing manufacturing companies in the year ahead. Refreshed every year, it is based on extensive consultation with over 3500 senior executives and associate members of the Manufacturing Leadership Council and Board of Governors.
The Critical Issues agenda establishes the Manufacturing Leadership Council’s strategic plan, and directly influences all major elements of the MLC’s research program, content focus, events, and services portfolio for the year ahead.
For more information contact: [email protected]
Technology and Communication for the New Workforce Generation
Two statements, from two people deeply immersed in the manufacturing sector, have been playing on loop in my head recently. The first was something said to me by Joe Chen, co-founder of one of our customers, Anduril Industries. He said that his company’s fundamental differentiator (and thus his most important KPI) is being faster to market than everybody else.
The second was an observation I read made by Paul Wellener, Vice Chairman and U.S. Industrial Products & Construction Leader at Deloitte LLP. Wellener, who also serves on the NAM Board of Directors, said, “The challenge is to really make manufacturing attractive to the next generation and to diverse populations.”
It’s hard to argue with either statement. Advances in manufacturing technology are driving dramatic acceleration in development, iteration, and production. And with supply chain problems causing drag on the entire sector, the ability to beat the competition for pace makes you far more likely to win.
Meanwhile it’s been well documented that the older part of the U.S. population is leaving work in droves. More than half of over-55s have quit the U.S. workforce, taking with them decades of knowledge and expertise and leaving a gap which must be filled by younger generations.
But those millennials, who will account for 75% of the workforce by 2025 according to some projections, have a level of choice in employment terms that we haven’t seen for decades. It’s a seller’s market and, with the U.S. manufacturing sector on track to have over two million unfilled jobs by 2030, the urgency behind Paul Wellener’s observation becomes clear.
So it is reasonable to conclude that success in manufacturing as we move forward will be heavily dependent on speed and agility, combined with the ability to attract and retain the best new talent from a pool of workers who are younger, and increasing in diversity of nationality in line with the population as a whole.
Studies suggest that technology has a crucial role to play. According to research from Comptia, 71% of millennials cite the degree to which an organization embraces technology and innovation as an influencing factor in their choice of an employer – a share of the cohort which is increasing each year. They want access to the best technology that will have the greatest impact on their skillsets.
In addition, the survey showed that 61% of millennials like to use their smartphone as part of their working life, compared to just 38% of boomers. Anecdotally, I see the same thing. They want to work as they live, with the same technology – and that means that the ways in which information is accessed, presented, and consumed must change.
Our own research into how product and process documentation is managed within the U.S. manufacturing sector revealed more generational differences in this area. We asked manufacturing professionals from middle management through to executive leadership whether they agreed that text-heavy documentation was challenging because of diverse reading skill levels and first languages. While 66% of those in the 45–54-year-old age group agreed, the number rose to 74% for those aged 35 to 44 and to 81% for those aged 25 to 34.
Where it gets interesting for me is the intersection between that need to beat competitors on time to market and the need to change how information is consumed (and to provide technology that engages and excites the workforce). The reality, of course, is that you are only as fast as your slowest process. And because effective communication of critical product and process information underpins every aspect of success, it has to be on the money.
Our survey suggests this is understood, with 75% of manufacturers reporting that they are actively trying to improve their communication processes, and 73% saying that communication is getting harder for them to manage as they grow. Most telling of all, 73% said they believe poor communication processes are undermining the investments they’ve made in other technology and process initiatives.
These issues are driving uptake of our interactive visual communication and collaboration platform, Canvas Envision because it provides that very step change in how information is delivered and consumed that chimes with the learning styles of the new generation workforce.
The challenges are not going away, but fortunately there is a solution.
About the author:
Patricia Hume is Chief Executive Officer of Canvas GFX.
Rethink 2022: Avoiding a Digital Divide
When it comes to digital transformation, is there a way to ensure that all manufacturers have an equal opportunity to focus on digital initiatives – regardless of their size? A panel at Rethink: The Manufacturing Leadership Council Summit examined the different challenges faced by small and medium enterprises on the industry’s journey to Manufacturing 4.0.
The panel featured Val Zanchuk, President at Graphicast; Chuck Wetherington, President of BTE Technologies and SMM Chairman for the NAM Board of Directors; and Irene Petrick, Senior Director of Industrial Innovation at Intel Corporation.
The most obvious challenge comes from resources. As Zanchuk said, he is often limited by the three T’s: Time, Treasury, and Talent. “I try to keep up with the pace of understand what’s going on with the latest digital tools, and identify the opportunities that make sense for the business.”
“M4.0 is not a rote prescription, it’s a toolbox,” Wetherington said. “We are moving digital technology down to where the work is being done.”
Petrick said that the digital divide isn’t only because of size, but also because of investment choices. “If you weren’t doing a lot of investments in digital over time, then you are behind – it’s not a size issue, it’s an investment issue.” Petrick added that companies who have not been making those continuous investments are behind, especially after COVID.
Cybersecurity is also a concern, not just internal to a company but also as an ask from customers. “The customer base has to be able to look at us and say we’re in good shape, to be comfortable working with us,” Zanchuk said.
Wetherington added, “Every company needs to be worried about cyber and needs to make efforts to be secure. The problem isn’t how good your defense is, it’s whether or not the bad guys want to get at you.”
So how can a small company, or any company, keep from falling into the divide?
“You have to stay on top of understanding technologies,” Zanchuk said. “Lean mentality fits well with 4.0 mentality, but we don’t use every tool in the Lean toolbox. I’m always scanning the technologies to understand it and translate it down to my scale.”
It’s also a matter of people, not just technology. “Hiring and retaining talent will continue to be an enormous challenge,” Petrick said. “Investing there will yield much more value than ever before.”
Rethink 2022: Tomorrow’s Manufacturing Leaders Speak Up
Panelists discuss access, cross-functional teams, lessons learned and more at Rethink
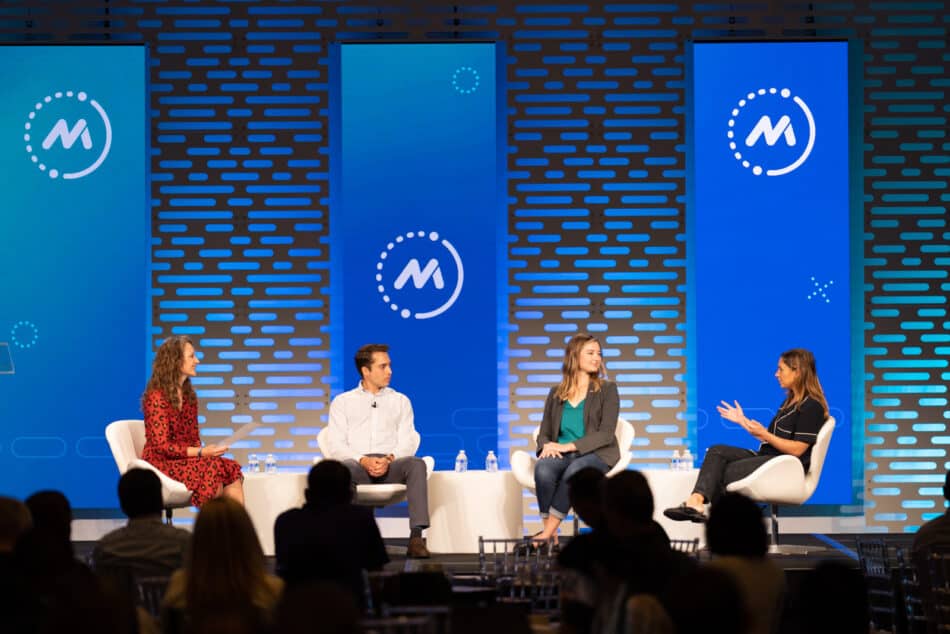
Katelyn Kelsey didn’t expect to go into manufacturing, but as an engineer, the lure of digital transformation and the opportunity to solve emerging problems was too great.
Participating in a panel discussion on next-generation leaders at MLC’s Rethink 2022 Summit, the Mobility Technology Engineer for Dow, Inc., encouraged employers to go back to the drawing board and to let young people know that manufacturing is a place where they can work with the latest technologies and solve problems that bridge information technology and operational technology.
Moderated by Penelope Brown, MLC’s Senior Content Director, the panel also included Hayley Dwight, Director, Business Architecture and Change Management for Cooley Group, and Daniel Shrives, Research Engineer for Saint-Gobain North America.
The panelists agreed that Gen Z and millennials want to work for companies with interdisciplinary teams that do not operate in silos. Further, Dwight explained that her generation also wants a culture that values information sharing between organizational levels. She shared that she’s able to direct message with people like Jack Dorsey – the co-founder and former CEO of Twitter – so she should have similar access to the leaders in her our organization.
Later Kelsey added, “It costs you nothing to offer a seat at the table.”
Meanwhile, Shrives shared that one of the most important lessons he’s learned so far is to be flexible and expect that a role and responsibilities will change over time. But it is not just about his generation’s expectation to adapt. Shrives shared that leaders should give millennials an opportunity to bring change with them.
To prepare for the future, Kelsey encouraged manufacturers to come to events like Rethink in order to have candid conversations as an industry. She also reminded the audience that manufacturers aren’t just manufacturers anymore. They are also technology companies and they need to pull talent from other industries to create cross-functional teams.
And it is not just about speaking truth to power. Each of the panelists is also working to build their own leadership skills. In fact, Dwight, Kelsey and Shrives were among those honored later in the Next-Generation Leadership category at the Manufacturing Leadership Awards Gala.
Asked to share something about her personal development journey, Dwight shared that she’s working to ask more questions instead of making declarative statements. To do this, she asks herself each day if she ended more sentences with question marks or periods. That’s a lesson for leaders regardless of their generation.
Photo by David Bohrer / National Assoc. of Manufacturers