Building Boeing’s Future
Manufacturing Leadership Journal content and MLC resources are exclusively available to MLC members. Please sign up for an account or log in to view this content.
Lincoln Electric Tour Showcases Innovation
Get the Latest News
Get involvedA word of caution about the Manufacturing Leadership Council’s plant tours: Attending one could make you rethink your manufacturing operations.
Inspiration abounds: The MLC, the digital transformation arm of the NAM, recently hosted a plant tour of Lincoln Electric’s headquarters in Cleveland. Inspired by the innovation on display, one attendee vowed “to go back to my own company and start asking what’s stopping us from implementing similar technologies and practices.”
- The two-day Lincoln Electric event included visits to the company’s welding and training center, its machine division, its 3D printing facility and its automation-solutions center.
- Tour participants also learned how the business is overcoming workforce shortages through culture and technology solutions.
What is Lincoln Electric? Lincoln Electric was founded in 1895 as an electric-motors manufacturer. Today it is a global industry leader in welding equipment and consumables, additive manufacturing and automation solutions. The company has locations in 19 countries and serves customers in more than 160.
Welding school: The first stop on the tour was Lincoln Electric’s world-class welding school, first opened in 1917 and relaunched in 2018 as the 130,000-square-foot Welding Technology & Training Center.
- Students at this state-of-the-art facility begin their training at virtual welding stations before moving to one of 150 training booths to use the real “arc.”
- Lincoln Electric also offers virtual classes, a turnkey curriculum for customers and “train the trainer” courses for welding instructors.
3D printing: Tour participants also got a look at the company’s Additive Solutions Center, the largest platform of its kind, which boasts 18 3D printing cells. It serves customers in the automotive, aerospace, marine and energy industries.
- The equipment prints replacement parts, molds, tooling and prototypes measuring up to eight feet long and weighing more than 8,000 pounds.
- It can print in a variety of metals, including mild steel, stainless steel, nickel alloys, bronze and Inconel.
Automation solutions: The Automation Solutions Center tour stop demonstrated Lincoln Electric’s twin answers to the manufacturing skills gap: innovation and tech solutions that increase productivity.
- The technology on offer includes automated arc welding products, collaborative robots, metal fabrication and assembly line solutions.
- Demand for Lincoln Electric’s collaborative robots is up as manufacturers cope with workforce shortages, tour participants learned.
High-performance culture: Tour attendees also learned about Lincoln Electric’s high-performance culture, which rewards success and provides employees with opportunities for growth and development.
- The company’s Incentive Management System for the production workforce includes output-based pay to maximize personal earnings potential, an annual profit-sharing bonus, a no-layoffs policy and an open-door policy.
- “I found the networking time to be highly valuable and came away with several ideas on employee retention,” said a tour participant.
Future focus: Looking ahead, Lincoln Electric leadership said the company’s core focus must and will be on its people—to continue to build a pipeline of talent and attract and develop the next generation of leaders.
Key Technologies In Manufacturing
Successful manufacturers find ways to ensure that digital change leads to evolution, not disruption.
Technology advances give businesses, governments and public sector institutions more possibilities to enhance their productivity, invent and reinvent offerings, and contribute to humanity’s well-being.
Just as manufacturing executives are ready to heave a sigh of relief at the state of post-pandemic recovery, recent global challenges have forced manufacturers to change their business models — seemingly overnight in some cases — to stay competitive and prepare for growth. Manufacturers must, therefore, pivot to address not only a snap-back in demand, but also significant disruption as digital technologies are driving pervasive change. Future factories may have sensors everywhere so that predictive maintenance becomes the norm. Big data in manufacturing will intersect with evolving analytics and digital simulations to drive automation and decision-making. New and innovative business models will rise rapidly.
Manufacturers have been exploring significant initiatives around IT/OT convergence, which is primarily the integration of OT assets like MES or SCADA that control physical processes with back-end software and hardware. These are the manufacturing ecosystem elements like ERP, business finance and PLM.
The greatest minds in manufacturing and technology have been swapping strategies, tips and tricks for enabling operational technology and information technology convergence for years. For most organizations, however, that “Aha!” moment has yet to materialize.
When IT and OT work together, companies can expect benefits such as:
- Faster time to market for new products
- Less siloed IT and OT environments where the departments work together using a shared set of standards and platform
- IoT devices enabling deep evaluation of critical resources and associated downtime
- Operational and development costs reduction
- Improved visibility and auditing thereby streamlining regulatory compliance
The manufacturing industry is constantly witnessing an increased digital disruption. Demand uncertainty and rapid changes in customer preferences are challenging planning systems to unprecedented degrees. Logistics disruptions are pushing businesses to find alternatives to globalized supply chains. Demand fluctuations are calling for dramatic operational and capital cost reduction in some areas and rapid growth in others. Remote work is forcing manufacturers to reconfigure manufacturing flows and management. Here, we will consider some of the key technologies that are shaping the future of manufacturing.
Internet of Things
The capabilities of the Internet of Things (IoT) are rapidly proliferating in the industrial and manufacturing industries, enabling plant managers to increase productivity and decrease process complexity. By 2025, the number of IoT-enabled devices is expected to reach 50 billion. The Industrial Internet of Things (IIoT) is an amalgamation of various technologies such as machine learning, big data, sensor data, cloud integration, and machine automation. These technologies are being employed in areas like predictive and proactive maintenance, quality management, real-time monitoring, resource optimization, supply-chain visibility, cross-facility operations analysis, and safety, enabling plant managers to minimize downtime and enhance process efficiency.
By 2025, the number of IoT-enabled devices is expected to reach 50 billion.
For example, regular maintenance and repair are essential for smooth plant operations, but not all equipment and devices need maintenance at the same time. The IIoT allows plant managers to employ condition monitoring and predictive maintenance of the equipment. Real-time performance monitoring helps manager plan maintenance schedules based on when a particular type of maintenance is necessary, reducing the likelihood of unplanned outages and the ensuing loss of productivity. Similarly, IoT-enabled and sensor-embedded equipment can communicate data that helps the supply chain team track assets (using RFID and GPS sensors), take stock of inventory, forecast, gauge vendor relations, and schedule predictive maintenance programs.
Artificial Intelligence and Machine Learning
Manufacturers have utilized robotics, mechanization, and control systems for decades to increase productivity and minimize production costs. Artificial intelligence (AI) and machine learning will be the next wave in manufacturing. AI is helping production teams analyze data and use the insights to replace inventory, reduce operational costs, and offer seamless quality control over the entire manufacturing process. AI and machine learning enable robots and humans to collaborate, creating agile manufacturing processes that learn, improve, and make smart manufacturing decisions. Manufacturers can employ industrial robotics and smart automation to manage manual labor-intensive tasks and focus their time and resources on revenue-generating tasks such as research and development, product line extension, and creating better customer experiences.
Edge Computing
Edge computing brings computational power closer to machines. The technologies let manufacturers collect and process data faster and, in turn, run more efficiently. Existing on-premises and centralized cloud infrastructures may be able to support the vast computing needs of these powerful applications, which require low latency — or data-transfer delay — to smoothly transport and get real-time access to data. To reduce latency and bandwidth use, as well as rein in costs, computing power and processes must be closer to the physical location of the data.
Edge technology enables manufacturers to gain and apply the data-driven knowledge that will power smart factories and products.
Edge computing complements cloud computing in that edge technology enables manufacturers to both gain and apply the data-driven knowledge that will power smart factories and products. Edge devices can be sensors, IoT-enabled machines, gateways, or single-board computers. These devices offer a quick, lightweight method for streamlining digital initiatives, run on minimal power, consume low quantities of energy, and can be cost-effective. Use cases that will drive the use of edge computing include:
- Machine monitoring / Condition-based monitoring
- Predictive maintenance
- Precision monitoring and control
- AR/VR
Digital Twins
Manufacturers are eager to adopt digital twin technologies to accelerate their smart factory initiatives, but many lack the business alignment or the required prerequisites to begin. Digital twins are one of the key enablers of smart factory initiatives, with the technology having the potential to increase revenue opportunities. Digital twins are useful throughout the asset lifecycle, from design and engineering to operations, and across the value chain from demand forecasting to planning and scheduling to distribution. Plant and process manufacturing facilities are at the intersection of the asset lifecycle and value chain and as a result are the primary focus of digital twin activity.
To maximize the technology’s benefits, manufacturers must first understand the distinct types of twins, their construction, and their limitations. Once an organization recognizes the nuances of these elements, it can align its twin program with financial objectives. Manufacturers can deploy digital twins for predictive analytics, to model on critical assets, and similar uses. The energy industry has already started adopting digital twins for network optimization, offshore asset management, etc.
5G
There is increasing demand for wireless communications inside manufacturing plants driven by the need for stable connectivity between IoT devices, including those embedded in machine controls. Machine background noise and the movement of people in manufacturing sites have the potential to interfere with wireless communications, so thorough verification of the reliability and stability of any 5G technology deployed in such environments is necessary.
To maximize the technology’s benefits, manufacturers must first understand the distinct types of digital twins, their construction, and their limitations.
As the demand for parts diversifies and production cycles become shorter, production lines need to be rapidly reconfigured whenever there are changes to components. By using autonomous mobile robots (AMRs) to create production lines with flexible layouts, manufacturers will be able to quickly build these and change their layout in line with demand fluctuations. Organizations also want to enhance productivity within plants by having AMRs automatically convey components to the exact spot they are required based on communication with production line equipment.
In another potential use case, dedicated cameras may monitor production line technicians, with the system giving feedback on their performance based on an analysis of their movements transmitted to servers using 5G communication. This requires a reliable, high-bandwidth, and low-latency network connectivity. AR/VR, push-to-talk, AGVs, machine vision, video surveillance and rugged tablet usage in the factory may similarly require the latency-free wireless coverage that 5G provides.
Immersive Technologies (AR/VR)
With the manufacturing sector beginning to explore immersive technologies, there is huge potential for this technology in assembly processes, equipment maintenance and decision making. For instance, factories could use augmented reality (AR) glasses to project data such as layouts, assembly guidelines, possible malfunction sites, or serial numbers for parts, enabling faster and easier workflows. AR and virtual reality (VR) can speed the onboarding of new workers and improve worker productivity by offering more immersive on-the-job training. AR smart glasses that project video, graphics and text can visually guide a worker, step by step, through assembly or maintenance tasks. Virtual technology is also in use for factory floor planning and manufacturing trade events. In mass-production manufacturing, factory planning — where to place tools, equipment and personnel — is crucial for productivity and efficiency.
AR and VR can speed the onboarding of new workers and improve worker productivity by offering more immersive on-the-job training.
Engineering a new plant or altering an existing one involves design, testing, and trials, and any unexpected delays or a production line shutdown — even a temporary one — can be very costly. Virtual technologies can simplify and significantly shorten the process. Before changes are made in the physical world, virtual plants can be designed to evaluate production flows and how workers and robots perform tasks. The use of virtual reality allows plant managers to simulate assembly line configurations and the processes involved in production, which allows them to identify situations that may be potentially dangerous. VR may also serve as a way for employees to immerse themselves in a future workstation to capture the employee’s task proficiency, movement, and feasibility, reducing the risk of potential injuries and/or fatalities.
Blockchain
As the plants become increasingly connected, the influence of blockchain is becoming more prevalent. The Factory of the Future spans across a whole network of machines, parts, products and value chain participants, including machinery providers, suppliers and logistics companies. Now, more than ever before, manufacturers face the challenge of securely sharing data within and outside factory walls. To work out the best place for blockchain, a manufacturer must conduct a structured assessment that begins with identifying the company’s current business problems and future needs. Blockchain can scale transparency and trust through all stages of the industrial value chain, from sourcing raw materials to delivering the finished product. Pain points it could help address include:
- Supply chain monitoring for greater transparency
- Materials provenance and counterfeit detection
- Engineering design for long-duration, high-complexity products
- Identity management
- Asset tracking
- Quality assurance
- Regulatory compliance
Low-Code/No-Code Platform
A low-code or no-code platform uses a drag and drop visual software development environment to enable users to create a mobile or web app. No-code has the distinction of creating these apps without writing a single line of code. This approach enables faster development and increased agility compared with writing lines of code, resulting in quicker updates and changes to the system being developed. It offers several benefits including better utilization of IT engineers, solutions built in lockstep with business problems, the ability to iterate and improve faster. Gartner has written that no-code is a key pillar of a broader digital strategy precisely because it broadens a company’s development base. Their argument is that businesses will succeed faster if they can radically shorten the development cycle, and involve significantly more business personnel in the development process. According to the research firm, “citizen development is fundamental to digital transformation.”
Blockchain can scale transparency and trust through all stages of the industrial value chain, from sourcing raw materials to delivering the finished product.
In manufacturing, the use cases for no-code applications are numerous. Common ones include visual work instructions, inline quality assurance, machine changeover, tool tracking, and root cause analysis. The manufacturing engineers design their applications using the low-code platform’s visual editor. Within the visual editor, they embed media, add text, and drag and drop elements to match their desired layout. With advanced no-code solutions, manufacturers could program responses to specific inputs. These inputs can trigger a response if they meet certain conditions. Conditional, if-then logic allows manufacturers to create branch logic so that one set of actions occurs given a specific input, but not others. This gives manufacturers unprecedented visibility into their factory’s processes. Using a manufacturing application platform, engineers can design customized, paperless root cause analyses that automatically document root causes.
3D Printing
Already, more than two-thirds of U.S. manufacturers use additive manufacturing technology to design products using less physical material, reduce product development costs, save space, and create malleable prototypes. Additive manufacturing, so-called because it adds material in layers to create an object, uses CAD software or 3D object scanners to digitally 3D print machine parts. It deposits material in layers, in precise geometric shapes. It is then possible to store parts as design files in virtual inventories and produce them whenever needed, which is known as distributed manufacturing. Storing digital files reduces transportation distances and simplifies inventory management.
Today, additive manufacturing employs a vast range of possibilities from tooling to mass customization across industries. The future is bright for 3D printing applications across the supply chain. In fact, the average 3D printer production speed is expected to increase by 88% by 2025. And, as printer speed increases, volume capabilities also are likely to increase. New combinations of 3D printing materials, as well as improvements to existing materials, will not only enable unprecedented 3D printing applications, but also will help reduce prices. There will be an emphasis in metals that is likely to grow over the next three to five years. Advancements in printing technologies and capabilities also will spur the development of new equipment and applications, like 3D-printed electronics.
Conclusion
Digital change is inevitable. Successful manufacturers will find ways to ensure that digital change leads to digital evolution rather than digital disruption. Understanding the potential benefits of successfully adopting digital technologies and the consequences of failing to do so is the first step. M
About the authors:
Baskar Radhakrishnan is Strategic Advisor, Manufacturing Industry Solutions at NTT DATA.
Sameer Joshi is Senior Director, Manufacturing Industry Solutions at NTT DATA.
.
Prioritize to Thrive: M4.0 as Recession Antidote
Technology investments can help manufacturers fuel growth as economic headwinds build.
Manufacturers have long known about the benefits of investing in Industry 4.0 improvements. As economic headwinds build, business leaders face a difficult choice about how to prioritize capital investments. In many cases, costly, long-term projects will be put on the backburner in favor of quick wins that can deliver a rapid return on investment.
At the same time, challenges related to supply chain disruption, labor shortages and heightened customer expectations persist. Industry 4.0 initiatives can help address those challenges, but organizations will need to prioritize spending as economic uncertainty constrains investment.
Supporting strategic business goals can be a guiding principle for how to prioritize investments. Digital strategy is a component of business strategy, and Industry 4.0 projects need to align with broader business objectives. Rather than being a technology exercise, digital initiatives should be business enablers that are tied to enabling competitive advantages or addressing tactical needs.
“Rather than being a technology exercise, digital initiatives should be business enablers.”
As recessionary pressures squeeze manufacturers, many businesses respond by looking to optimize costs and scale back investment, but it’s critical to seek targeted efficiencies and not undercut key areas that support revenue generation, revenue protection and competitive advantage. Now is the time to adapt and make the strategic adjustments necessary to support the business and set it up for growth when market conditions improve.
Evaluate your current state, prioritize planned capital investments, and assess your workforce and culture to understand where organizational value comes from. Then you can plan beyond the downturn and accelerate through the turn.
Prioritize Your Industry 4.0 Initiatives
Whether a business is thriving, merely surviving, or somewhere in between, an economic downturn requires prioritization across the business. Unfortunately, manufacturers that have delayed implementing Industry 4.0 may find it more difficult in the months ahead due to recessionary pressures alongside continuing supply chain disruption and workforce challenges.
BDO’s 2022 Manufacturing CFO Outlook Survey found that 30% of manufacturers surveyed have not yet started implementing Industry 4.0, so they are behind the curve in technology adoption compared to their peers. Additionally, half of all respondents say falling behind on innovation is a significant business risk. That clearly signals the need to continue investing in innovation, but all innovation is not equal. During a time of constrained resources, businesses should prioritize projects that have a clear path to implementation and can enhance revenue, profitability, competitive advantage, and future readiness.
Amid recession concerns, there can be a tendency to pull back on spending across the board and focus on cost cutting. However, if those steps are not taken carefully, they can hamper success by disrupting key business objectives. Reducing, delaying, or halting Industry 4.0 investments can have a cascading effect across an organization that increases risk, exacerbates the impact of risk, reduces resilience, and slows recovery from a downturn. It’s important to make targeted reductions in spending and continue investing in necessary projects while eliminating redundancies to create efficiencies.
Determining What Matters
Prioritization will vary between companies depending on several factors:
- The nature of the business
- Projects currently in flight
- Areas of greatest need
Despite these variations, the process of rationalizing a business portfolio is generally similar.
First, identify the mandatory projects that must continue. You cannot stop those because they are integral to the business, whether because they support revenue enhancement or preservation, customer satisfaction, an indispensable capability or other vital areas.
Then, assess where ROI will come from and how to accelerate quick wins. This step can include conducting a scenario analysis on expected timelines, project costs and projected value. Other initiatives can be put on hold temporarily, or even scrapped entirely, depending on how they fit with broader strategic goals. Once you’ve decided what initiatives to forgo and what to proceed with, you can continue investing in the mandatory projects and prioritize among the remainder.
“During a time of constrained resources, businesses should prioritize projects that can enhance revenue, profitability, competitive advantage and future readiness.”
For example, consider a large manufacturer that conducts quality control by relying on workers to make manual inspections of its products. That process draws substantial resources that could be devoted to other high-value activities. Alternatively, the company could invest in computer vision that is trained to identify common issues and automate a substantial portion of quality control tasks. Whether or not that investment is a priority for the specific business depends on several unique factors, especially cost, but the upside is clear: It will modernize an important process, free up more internal resources, and potentially improve customer satisfaction.
Establishing a Criteria
The process of prioritizing Industry 4.0 spending goes beyond just determining what is mandatory and what is optional. It requires defining the criteria for ranking priorities.
You can evaluate each project in terms of the monetary upside, strategic fit, required investment, and ease of implementation. Bear in mind that growth typically comes from geographies, business models, customers, and products. Anything that aids short-term revenue and profitability should be supported in the face of recessionary pressures. These considerations can include initiatives that improve customer retention, margins, or deliver a clear competitive differentiator. Some investments may be low-cost and easy to implement, such as installing IoT devices on a factory floor that monitor equipment and inventory to provide real-time information. Those quick wins should be captured as soon as possible.
There may be tradeoffs among competing considerations. For example, a project with significant monetary upside and strong strategic fit may require more investment, but that could be worthwhile even during lean times, especially if it carries strong revenue potential, which begins materializing in the near-term. And in other cases, there may not be alternative options, such as if a legacy system has reached the end of its useful life. Anything broken must be repaired or replaced.
“Long-term investments can be risky during uncertainty because pausing mid-flight can prove even more costly depending on the delay.”
Any capital-intensive investments will be scrutinized closely, so the expected benefits need to be clear, as well as the timeline for realizing those benefits. By contrast, projects that do not fit well with broader business strategy or do not carry notable monetary upside should be postponed. As one example, switching to a new ERP system, while strategically useful, can be a slow and costly process. Many businesses may choose to delay switching their ERP until there is less uncertainty regarding the future outlook.
The exception would be if there is a compelling reason to proceed with a certain project. For instance, if a large company you supply to changes systems or has new system requirements that vendors must meet, then you will need to upgrade your systems to continue working with that major partner.
It is important to bear in mind that projects which have known hurdles for implementation, or a long timeline for implementation, may be difficult to devote sufficient internal resources to when the main focus is on priority areas. Long-term investments can be risky during uncertainty because pausing mid-flight can prove even more costly depending on the delay.
The Importance of Culture and People
The success of Industry 4.0 relies on your people. A strong culture that is built on shared purpose and embraces innovation is one of the greatest organizational assets a business can have.
The more end-to-end understanding of processes that exists across the entire organization and workforce, the more aligned employees will be with change. Think of the mentality between management and workers as “create change with us” as opposed to “do what we say.”
“Using technology to automate repetitive tasks and providing upskilling of employees creates greater value to the employee and to the organization.”
Working together makes the work easier. And with that mentality, the workforce can also be a valuable source of intelligence to help guide Industry 4.0 investments in areas that eliminate redundancy, clear bottlenecks, and create greater efficiency. Additionally, a siloed organization will struggle to devise alternative solutions because they lack visibility and cross-functional understanding. If an organization is not siloed, then workers can better help devise best practices for alternatives.
Overall, companies that have a strong culture and a track record of participating actively in large transformational change programs have a much better chance to thrive. That is true for any program, not just during a downturn.
Overcoming the Talent Shortage
All too often, digital transformation efforts fail or fall short of their goals. Common reasons for this include employee pushback, change fatigue, poor change management, low digital literacy, and a lack of enablement and adoption. A culture that embraces change helps set up an organization for Industry 4.0 success, but that can be undercut by a separate workforce challenge: turnover and too few skilled workers to fill open positions.
Even before the challenges of the COVID-19 pandemic — and the related supply chain disruption and talent shortage across industries — manufacturers faced a workforce crisis. A 2019 survey by the National Association of Manufacturers found that nearly a quarter of the industry’s workers were age 55 or older. Those workers have only gotten older since then, and the U.S. population as a whole is skewing older as well. The U.S. Census Bureau noted in 2020 that the number of Americans aged 65 and older increased by 34% between 2010 and 2019 as more Baby Boomers pass retirement age.
On one hand, an aging workforce is a repository of critical knowledge, but on the other it poses a significant business risk. A lack of knowledge transfer could sap revenue and impede manufacturers’ growth trajectory. Older workers may opt to retire rather than undergo upskilling or reskilling for new systems, and the talent pipeline is struggling to keep up with replacing them. By some estimates, there could be millions of unfilled positions across the U.S. manufacturing industry by 2030.
These challenges will require a mix of solutions to leverage technology, strengthen culture, improve the talent pipeline, and modernize job roles to match available skill sets. Using technology to automate repetitive tasks and providing upskilling of employees creates greater value to the employee and to the organization. Identifying and enabling the highest and best use will drive efficiency through a diminished workforce.
“It is critical to communicate clearly and consistently with the workforce to identify concerns and anticipate emerging risks.”
At the same time, recession fears and cost cutting can leave workers worried that they could lose their jobs. Whether those concerns are justified or not, even the prospect of furloughs or layoffs can negatively impact employee engagement, which saps productivity. Businesses that rely on workers as a reserve of institutional knowledge are even more vulnerable to engagement and morale issues. So, it is critical to communicate clearly and consistently with the workforce to identify their concerns and anticipate emerging risks. Conducting a voice of the employee survey can also help gain better insight into employee morale, especially during times of change and uncertainty.
Revising the Value Drivers
In addition to revenue generation, business leaders consistently seek to minimize risk and enhance future readiness. One way to help achieve that is by improving the performance of systems and processes, which helps increase the proportion of value they generate for the organization.
In many organizations, processes and knowledge reside with a company’s people, who rely on first-hand knowledge built through experience. They may frequently need to intervene and circumvent problems with systems, so most tasks cannot be done without significant involvement by workers. Systems may resemble paper forms — or work may even be done through actual paper forms. A lack of clear processes for task management, routing and prioritization can also create redundancy that saps efficiency and output. Therefore, people provide the greatest proportion of value under these circumstances, and the business faces outsize risk from turnover or other workforce disruption.
Fortunately, improving business systems and processes can reduce that overreliance on people and potentially free up internal resources for higher-value tasks. Then, people can create competitive advantage instead of solving unnecessary problems and triaging the breakdowns.
Figure 1: A rough illustration of how organizational value is distributed among systems, processes, and people, and how Industry 4.0 investments can help reduce risk by bringing added value into greater balance.
Standardization of systems and processes — in terms of real-time availability of required information, clear rules for task completion and full workflow functionality — reduces labor-intensive, customized methods that were developed ad hoc. It can also increase employee engagement by reducing a common source of frustration.
On the revenue side, more automation and Industry 4.0 maturity leads to better decision making. It enables better visibility into the business and potentially spotlight cross-silo KPIs. Your processes likely extend across multiple companies and include vendors and other partners, some of which operate in the cloud and others on-premises. Digital maturity can enable cross-company KPIs to build end-to-end visibility. Better information yields better decisions that can unlock strategic value, and Industry 4.0 is the key.
Planning Beyond the Downturn
Competitive advantage hinges on the ability to access data about your business and your customers. Companies that have a higher degree of Industry 4.0 maturity will be in a stronger position for enduring recessionary pressures and workforce challenges. They can access better insights about the business and make better decisions for the short and long terms, enabling a swifter exit from any downturn and a recovery at a higher velocity. By prioritizing Industry 4.0 investments to align with strategic business priorities, manufacturers can focus available resources on the highest value activities, maximize the short-term ROI they can achieve, and enhance future readiness. M
About the authors:
Maurice Liddell is a BDO Digital Market Leader, Manufacturing, with BDO USA LLP.
Dimitrios Vilaetis is a Managing Director, Management Advisory Services, with BDO USA LLP.
.
Laying the Foundation for Factories of the Future
Bringing together the right IT and OT systems will be key for manufacturers to realize a digital future.
To remain competitive in an increasingly digital and interconnected environment, companies across the manufacturing sector are working toward data-driven, lights-out facilities. But manufacturers cannot reach that point without having foundational information technology and operational technology infrastructures that work symbiotically to unify supply chains, cloud platforms, and other aspects of operations.
To take advantage of technologies such as artificial intelligence, machine learning, digital twins and robotics, manufacturers need to change the way they think about network infrastructure. Integrating historically siloed IT and OT infrastructures will be central in developing the factories of the future. Companies should make investments that make it easier for the OT side to make decisions using data, and that make it easier for the IT side to understand how the OT environment works.
Businesses will not be able to embrace advanced technologies if they don’t have the foundational data highway and security in place to support them. For many teams, building an integrated IT/OT infrastructure foundation will require a mindset shift. Rather than just a means of sending data from Point A to Point B, these IT and OT foundations — when integrated holistically — can enable more circular connectivity throughout operations, better security, continual improvements in efficiency and, ultimately, growth.
Shifting the Mindset
Especially with the rise of more regulatory requirements around data security, manufacturers need to determine whether their IT and OT infrastructure align with their business goals and make intentional efforts to use the infrastructure’s capabilities proactively across the organization. Leadership teams should view IT and OT foundations as visibility and containment tools in detecting viruses, performance issues and security gaps. Manufacturers will not be able to make meaningful improvements in supply chain efficiencies and elsewhere unless they prioritize such efforts.
“Businesses will not be able to embrace advanced technologies if they don’t have the foundational data highway and security in place to support them.”
For many businesses, this will mean collapsing IT and OT to be more connected to each other, which will enable faster decision-making with the use of real-time data. This will help foster the necessary mindset shift from viewing networks solely as a way to connect machines to seeing the broader scope of their functions. Developing more resilient IT and OT foundations will be especially crucial for boosting capabilities in the following three areas:
- Detection: Manufacturers can leverage symbiotic IT and OT networks to improve end-to-end visibility throughout the business, making it easier to identify everything from operational issues to security threats.
- Diagnostics: More connected infrastructure will allow companies to use tools like predictive analytics to diagnose problems and eventually automate corrective actions. This can save time by requiring less human involvement.
- Compliance: There are a host of compliance rules and implications to navigate related to information infrastructure, whether from the federal government or other parties. Once manufacturers have greater visibility across their networks, they will also have a better real-time understanding of whether their platforms and systems comply.
On the compliance front, the stakes are higher than ever; in the wake of ransomware attacks in recent years, insurers have elevated the requirements companies need to meet in order for them to be covered. Some such requirements are even more strict than rules put forth by the National Institute of Standards and Technology. That demand from insurance providers underscores why now is the time to invest in more resilient systems.
Before manufacturers can make strategic investments to upgrade their aging legacy infrastructure, however, they will need to understand how their networks currently work. This may sound obvious enough, but for platforms that have been continually running for a decade or more without being turned off, teams may not have a clear understanding about what happens to operations when things go offline.
“The impact of network outages will only become more significant as factories become more connected and automated.”
In the manufacturing space especially, this can have enormous impacts on worker safety as well — for instance, a factory floor pressure sensor going down might pose risks to physical safety. Businesses need to ensure that the IT infrastructure side of the house takes those operational factors into account and understands the crossovers between IT and OT risks. Given that it has become standard to air gap systems, companies will need to make thoughtful decisions about how to harmonize these two different aspects of technology infrastructure without opening themselves to vulnerabilities.
The impact of network outages will only become more significant as factories become more connected and automated. Because those technologies are network-based and require moving more operations to the cloud, manufacturers will need to have redundancies in place for the systems they use to move information to the cloud. In essence, that information highway needs to be tested for reliability, and teams should have clear plans in place for when outages happen.
Shop Floor to Top Floor
Much like manufacturers need to have a holistic approach to the ways their OT and IT systems work together, they should also understand the broad scope of how their network architecture connects the shop floor to the top floor — that is to say, how their data is able to move through all aspects of operations, from assembly lines up through human resources, finance, executive leadership and other functions.
Industrial machinery and devices that gather and often transmit data, for instance, should have the ability to interface with enterprise resource planning systems to inform decisions related to inventory, raw material needs, forecasting, finance and more. In an era when supply chain constraints are common across most industries, it’s crucial that all lines of the business have better visibility into disruptions that may be on the horizon. Companies should also take into account data warehouses and SCADA systems when working toward this broader connectivity.
“Manufacturers that don’t have the right system architecture in place will be limited in how they can put data to use in improving supply chains, productivity, and efficiency.”
With the rise of the IIoT introducing more and more data-driven devices and widgets to the shop floor, the ability to integrate factory data across the business will be more important than ever. Manufacturers that don’t have the right system architecture in place will be limited in terms of how they can put data they already have to use in improving supply chains, productivity, and efficiency.
The Path Forward
In assessing their current state and needs for the future, there are several specific technologies that manufacturers should ensure they have in place or are migrating toward to ensure a stable, high-performing, and highly redundant foundational network infrastructure. But beyond individual tech capabilities, companies need to educate their teams about the potential of automation, the possibilities allowed by greater IT/OT connectivity, and help them understand that time is of the essence in building more robust infrastructures. Furthermore, organizations should have training in place to help employees on the OT side feel more fluent in data, and to help those on the IT side better understand the OT environment.
The journey toward better foundational technologies will look different from business to business; manufacturers should develop a plan for how it translates to their individual operations. Only once team members understand the importance of that journey can the organization make the right investment decisions. M
About the authors:
Ron Beck is a principal at RSM US LLP.
John Chambers is a director at RSM US LLP.
Scott Hermanson is a principal at RSM US LLP.
.
MLC Announces New 2022/2023 MLC Critical Issues Agenda
The Journey to M4.0 Value
The manufacturing industry is at a pivotal point in its history.
Driven by market forces to become more agile, innovative, resilient, cost efficient, and sustainable, companies of all sizes are pursuing a future vision for business value enabled by digital technologies that will redefine the rules of competition, how work will be performed, how companies will be organized, and how leadership must lead.
We term this future state: Manufacturing 4.0.
Such a comprehensive enterprise-wide transformation requires a three-dimensional approach: mastering the challenges and opportunities of advanced digital tools and data; improving organizational structures and cultures; and developing new workforce talent and leadership skills.
While shaped by company size, sector, and level of digital maturity, all manufacturers share the need for a common set of key M4.0 competencies.
These enable them to drive value from digital investments in critical areas of business activity – from product design and innovation, to supply chains and customer relationships, to more eco-efficient manufacturing operations.
The Manufacturing Leadership Council’s new Critical Issues agenda for 2022/2023 is a specifically designed to help manufacturers align their thinking and best practices to deliver true business value from their journey to M4.0.
The MLC’s Critical Issues Process
The Manufacturing Leadership Council’s Critical Issues agenda, now in its 11th year, is the outcome of a unique, annual, member-driven process to identify the most urgent and important issues facing manufacturing companies in the year ahead. Refreshed every year, it is based on extensive consultation with over 3500 senior executives and associate members of the Manufacturing Leadership Council and Board of Governors.
The Critical Issues agenda establishes the Manufacturing Leadership Council’s strategic plan, and directly influences all major elements of the MLC’s research program, content focus, events, and services portfolio for the year ahead.
For more information contact: [email protected]
Technology and Communication for the New Workforce Generation
Two statements, from two people deeply immersed in the manufacturing sector, have been playing on loop in my head recently. The first was something said to me by Joe Chen, co-founder of one of our customers, Anduril Industries. He said that his company’s fundamental differentiator (and thus his most important KPI) is being faster to market than everybody else.
The second was an observation I read made by Paul Wellener, Vice Chairman and U.S. Industrial Products & Construction Leader at Deloitte LLP. Wellener, who also serves on the NAM Board of Directors, said, “The challenge is to really make manufacturing attractive to the next generation and to diverse populations.”
It’s hard to argue with either statement. Advances in manufacturing technology are driving dramatic acceleration in development, iteration, and production. And with supply chain problems causing drag on the entire sector, the ability to beat the competition for pace makes you far more likely to win.
Meanwhile it’s been well documented that the older part of the U.S. population is leaving work in droves. More than half of over-55s have quit the U.S. workforce, taking with them decades of knowledge and expertise and leaving a gap which must be filled by younger generations.
But those millennials, who will account for 75% of the workforce by 2025 according to some projections, have a level of choice in employment terms that we haven’t seen for decades. It’s a seller’s market and, with the U.S. manufacturing sector on track to have over two million unfilled jobs by 2030, the urgency behind Paul Wellener’s observation becomes clear.
So it is reasonable to conclude that success in manufacturing as we move forward will be heavily dependent on speed and agility, combined with the ability to attract and retain the best new talent from a pool of workers who are younger, and increasing in diversity of nationality in line with the population as a whole.
Studies suggest that technology has a crucial role to play. According to research from Comptia, 71% of millennials cite the degree to which an organization embraces technology and innovation as an influencing factor in their choice of an employer – a share of the cohort which is increasing each year. They want access to the best technology that will have the greatest impact on their skillsets.
In addition, the survey showed that 61% of millennials like to use their smartphone as part of their working life, compared to just 38% of boomers. Anecdotally, I see the same thing. They want to work as they live, with the same technology – and that means that the ways in which information is accessed, presented, and consumed must change.
Our own research into how product and process documentation is managed within the U.S. manufacturing sector revealed more generational differences in this area. We asked manufacturing professionals from middle management through to executive leadership whether they agreed that text-heavy documentation was challenging because of diverse reading skill levels and first languages. While 66% of those in the 45–54-year-old age group agreed, the number rose to 74% for those aged 35 to 44 and to 81% for those aged 25 to 34.
Where it gets interesting for me is the intersection between that need to beat competitors on time to market and the need to change how information is consumed (and to provide technology that engages and excites the workforce). The reality, of course, is that you are only as fast as your slowest process. And because effective communication of critical product and process information underpins every aspect of success, it has to be on the money.
Our survey suggests this is understood, with 75% of manufacturers reporting that they are actively trying to improve their communication processes, and 73% saying that communication is getting harder for them to manage as they grow. Most telling of all, 73% said they believe poor communication processes are undermining the investments they’ve made in other technology and process initiatives.
These issues are driving uptake of our interactive visual communication and collaboration platform, Canvas Envision because it provides that very step change in how information is delivered and consumed that chimes with the learning styles of the new generation workforce.
The challenges are not going away, but fortunately there is a solution.
About the author:
Patricia Hume is Chief Executive Officer of Canvas GFX.
Creating the Future Workforce at Lincoln Electric

Lincoln Electric has a long and storied history since its 1895 founding in Cleveland, Ohio, as a manufacturer of electric motors. Today, it is a global industry leader in welding equipment and consumables, additive manufacturing, and automation solutions, and has expanded across 19 countries worldwide and serves customers in over 160. But how does Lincoln keep a connection with its origins through a continued spirit of innovation and learning?
Lincoln Electric first opened its welding school in 1917 and a century later launched its state-of-the-art Welding Technology & Training Center, in 2018. This 130,000-square foot facility includes training stations for virtual welding, where all students start their introduction to welding, and more than 150 training booths for learning on the real ‘arc’. There are classrooms to accommodate both live and online instruction.
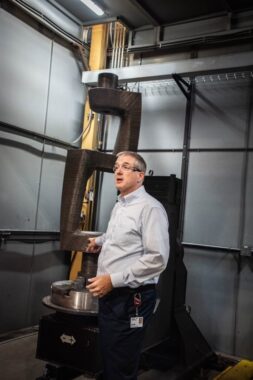
Lincoln Electric’s welding training is given to its new employees and external welding students. In addition, Lincoln also offers both turnkey and custom welding training curriculums and courses for customers to help them upskill their professional welders to achieve specific business targets and goals. They also offer a “train the trainer” course for welding instructors to ensure today’s students are getting the most up-to-date instruction to be industry-ready.
MLC members were given a first-hand look at Lincoln Electric’s headquarters in Cleveland at a recent plant tour that included visits to the welding training center in addition to the company’s machine division, where it builds welding equipment and consumables, as well as its large-scale additive business (3D printing) and their automation solutions.
Lincoln Electric is proud to have a high-performance culture that recognizes and rewards success and provides employees with opportunities for growth and development. The company’s Incentive Management System (IMS) for the production workforce includes piece work pay to maximize personal earnings potential, an annual profit-sharing bonus, a no-layoff policy, and an open-door policy including an employee-represented advisory board, who regularly meet with management to discuss various HR and operational matters. The IMS has been studied by the Harvard Business School and is one of the school’s top-selling case studies.

Lincoln Electric’s state-of-the-art, large-scale metal 3D printing solution is an extension of its automation, software development and metallurgical expertise, which has been applied to an additive process. The company’s additive solutions center is the largest platform of its kind globally with 18 3D printing cells which are used primarily to print replacement parts, molds, tooling and prototypes that measure up to eight feet in length and weigh more than 8,000 pounds – and are printed in a variety of metals including mild steel, stainless steel, nickel alloys, bronze, and Inconel. The solution serves a variety of industries including automotive, aerospace, marine, and energy. Customers provide Lincoln with CAD files or their parts and functional requirements and can expect finished parts in weeks versus months when using traditional castings or forging.
The tour stop in the Automation Solutions Center demonstrated Lincoln Electric’s portfolio of automation solutions that are aimed at increasing productivity and addressing the industry’s skills gap. The technology offered includes automated arc welding products, collaborative robots, metal fabrication, and assembly line solutions. The company has seen increased demand for its collaborative robot solutions in particular as manufacturers attempt to shore up their workforce shortages.
So what lies ahead as Lincoln Electric’s biggest challenge? Like most manufacturers, company leadership says that the core focus must be on people – to continue to build a pipeline of talent and attract, develop, and grow the next generation of leaders.
Additionally, Lincoln will focus on expanding its additive manufacturing and automation businesses in line with current trends and demand from customers in a variety of industries. But the company also intends to keep a focus on having a robust product portfolio that feeds into its bread and butter: a comprehensive and vertically integrated welding business, recognized around the world.
Transform Cybersecurity Through OT
Manufacturing Leadership Journal content and MLC resources are exclusively available to MLC members. Please sign up for an account or log in to view this content.
Manufacturers Are Getting Tough on Cybersecurity
Get the Latest News
Get involvedMore companies are taking a disciplined approach to the growing threat of cyber attacks, according to a new cybersecurity survey from the Manufacturing Leadership Council. The MLC is the digital transformation arm of the NAM.
- The survey, which included input from 160 companies, indicates a dramatic change in how seriously manufacturers consider cyber threats compared to 2018, when the MLC last conducted the same survey.
Who’s prepared: Nearly 62% of manufacturing companies say they have a formal cybersecurity plan in place, according to the survey.
- That’s up from 2018, when barely 33% of manufacturers indicated they had devised and adopted formal cybersecurity plans that encompassed their plant floors.
- Nearly 40% of respondents said they had a high level of confidence in their internal cyber expertise, compared with just 25% who expressed such certainty in 2018.
More attacks expected: Yet even as better cybersecurity strategies are put in place, nearly 79% of survey respondents said they expect more attacks in the next year.
- That figure is up from 64% in 2018.
- The most frequently cited reasons for this prediction are increased levels of cyber crime and cyber terrorism and greater connectivity in manufacturers’ operations.
The effects on digital transformation: More than half the survey respondents expressed concern that cybersecurity issues could affect the speed and scope of digital transformation.
- 14% said cybersecurity could be a major obstacle in the next five years, with another 40% describing it as “an issue of concern.”
- Close to half—43%—said they consider cyber a part of doing business in a digitally transformed world.
Proactive measures: More manufacturers are taking advantage of publicly available safeguards, such as the NIST Cybersecurity Framework, to underpin their strategies.
- Nearly 58% of respondents said they have adopted the NIST framework, up from 48% in 2018.
- 45% said they have cyber insurance, compared to the 18% that said they had it in 2018.
The coming challenge: In the past four years, manufacturers have made significant strides to combat the growing problem of cyber attacks against the industry.
- However, manufacturers will need to stay a step ahead of cyber criminals as the number and sophistication of attacks increases.
See the survey: Review the survey findings for an in-depth look at how manufacturing leaders are thinking about cybersecurity in manufacturing’s digital era.
Get help: NAM Cyber Cover was designed specifically to provide enhanced risk mitigation and protection for manufacturers and their supply chains. Find out more at www.namcybercover.com.