What Got You Here, Won’t Get You There
To move into the digital future, manufacturing leaders must lead with disruption and innovation.
TAKEAWAYS:
● Transformation starts with leadership.
● Employee-wide upskilling development is needed.
● How to instill a learning culture.
The manufacturing industry continuously faces new challenges in an ever-changing landscape. Leaders must contend with increasing demands to adopt sustainable practices, the need for greater data security, rising customer expectations, and difficulties around recruiting and retaining talent as skilled workers approach retirement.
This complex landscape requires disruptive and adaptable manufacturing leaders ready to navigate uncertainty and introduce new ways of working designed to fit shifting priorities.
To do this, leaders will need to look inward to identify the behaviors that will support and empower workers, upskill current employees, and cultivate a culture of constant learning.
Transformation Starts With Leadership
The new transformative, disruptive manufacturing leader will need to pivot away from “business as usual” to a digital-first “change as usual” mindset. They must understand and embrace data, be able to role model digital behaviors, leverage the strengths and behaviors of the team and individuals to retain competitive advantage, and bridge the gap between the now and ever-changing digital future.
Contrary to popular belief, leadership is not a stand-alone, isolated activity. The new leader must be able to ideate, innovate, and create future solutions while leading, empowering, and engaging teams undergoing transformation. This leader should encourage people to think and operate outside the box. In an industry that is heavily product driven, this new paradigm will need to be applied with caution given the reduced margin of error within this sector.
“The new leader must be able to ideate, innovate, and create future solutions while leading, empowering, and engaging teams”
PA Consulting recently surveyed over 300 business leaders across the U.S., U.K., and Europe to explore the behaviors driving the new way to lead. The finding revealed that over the next five years, the following behaviors will be critical to success:
- Nurture human optimism by helping people create a positive mindset and approach, tapping into people’s innate capacity to adapt to new and complex situations with innovation and creativity.
- Empower teams to innovate by inspiring people to understand their customers’ desires and giving them the space and permission to imagine and deliver value-creating responses.
- Build evolving organizations by creating environments where rapid change is the norm, and where aware, inclusive, and responsive teams can make a success out of change.
- Seek inspiration in surprising places by applying new perspectives and a broader lens to both existing technologies and evolving challenges.
An overwhelming majority of surveyed leaders recognized the importance of those behaviors as essential to leadership now and in the future. Moreover, these behaviors are linked to 70% and 74% better outcomes in performance and societal outcomes, respectively.
Driving Economic Optimism Through Upskilling and Learning
To lead systematic change and deliver organizational transformation at pace, businesses must ensure that all employees are prepared and ready to face the challenges of the 21st century. Indeed, being disruptive isn’t just about thinking differently, it’s about having a stable and secure organizational foundation to take risks and adapt. To do so, leaders must prioritize building new talented teams, upskilling and transforming the learning capability.
The World Economic Forum’s Future of Jobs Report states that due to the growing uptake of technology and automation, half of all employees will need reskilling by 2025. This remains particularly relevant within manufacturing where operationally intensive companies begin to enter a new era of automation reliance. In Europe and the U.S., demand for physical and manual labor for repeatable and predictable tasks within the sector is predicted to decline by nearly 30% over the next decade. In contrast, the requirement for digital skills (coding analytics for example) is predicted to almost double. Finally, demand for high-level social and emotional skills will continue to increase as global partnerships and supply chain complexity expand. Such significant workplace trends present real challenges, and opportunities, to manufacturing firms.
Create a long-term vision for growth
In this context, leaders can no longer rely on a reactive and short-term people strategy but must look to develop a long-term vision for growth, which recognizes the importance of an adaptable and cognitively mobile workforce. The economic incentive remains paramount and clear: retention and training are, and will continue to be, a more sustainable and effective employee policy than hiring new employees. Moreover, shifts in societal and workplace attitudes will only strengthen this approach and the expectation that employers must do more to retain their current workforce where possible. In light of this clear momentum shift, what can leaders do to guide this skills transition and drive progress?
“Employees should be encouraged to embark on their own upskilling journey through conversations and development plans”
Companies must ensure that any upskilling forms part of a larger digital strategy. Acquiring top talent remains a common barrier to achieving digital strategies, and success in either requires a combined approach that sees upskilling as a critical cog in the wider digital wheelhouse. Here, leaders must engage with serious discussions around workforce planning and resource allocation to design effective upskilling capability.
Reward and incentivize training
Upskilling and reskilling must be widely promoted and resourced at all levels to ensure enterprise-wide adoption. Leaders must consistently communicate its value, actively endorse and support opportunities, and identify risks of reduced adoption. Where possible, employers should look to reward and incentivize upskilling activity (both compensatory and non-compensatory). At the very minimum, employees should be encouraged to embark on their own upskilling journey through regular career development conversations and bespoke development plans. Flexible learning and additional staff development products such as microlearning and flexible time off should also be reviewed in order to see a noticeable shift in this area.
Leaders should work closely with learning and development (L&D) teams who have a wealth of learning resources, training skills, and valuable workforce data on required future skills and learning needs. Leaders should also discuss emerging trends, business needs and skill requirements to inform the L&D teams’ programs and middle leadership layer. A strategic response to this upskilling challenge will inform leaders and encourage staff to take up opportunities to upskill and grow. Developing an online opportunity marketplace or talent-seeking resource hub can help to meet business needs and develop individuals and teams.
Finally, upskilling provides numerous benefits to both employees and organizations. The meaning and importance of work have changed over time and research has shown that the main motivating factor is no longer money. More people are reevaluating their priorities, looking at their work-life balance and wanting their work to be meaningful, purposeful, and in harmony with their beliefs and values. When aligned with organizational beliefs, mission, and values, the power of upskilling is even stronger.
Cultivating a Life-Long Learning Culture and Digital Mindset
Manufacturing 4.0 is primarily anchored in interconnectivity which is underpinned by insights garnered from automation, machine learning (ML), big data analytics, and real-time data. Moving into a digitally enabled era means that there is an ever-greater expectation of delivering innovative products to the market at speed. This means that success ultimately lies in how well organizations are able to move their people to become truly innovative, agile, and collaborative in order to overcome increasingly complex structures and meet future customer demands.
“It is crucial for leaders to cultivate a foundational culture of life-long learning and a digital mindset”
Organizations going through such Manufacturing 4.0 digital transformations will recognize that, alongside investing in new technologies and upskilling/reskilling employees in how to use them, it is apparent that technological advances and the unexpected changes they bring are here to stay. To be unequivocally fit for the future, therefore, it is crucial for leaders to cultivate a foundational culture of life-long learning as well as a digital mindset that will inspire their teams and enable them to find creative solutions at an unprecedented pace.
Create a psychologically safe environment
Creating a life-long learning culture and a new digital mindset requires the right platforms and resources to provide more informal, on-demand, and bite-size learning opportunities that can be accessed alongside day-to-day work, and also an environment of psychological safety. Like evolving learning approaches, performance and development conversations are now also occurring both more frequently and informally, to meet the real-time nature of new or changing demands.
For manufacturing in particular, a move to greater automation can create substantial changes physically (from the shop floor to an office setting) as well as behaviorally (towards a fail-fast agile learning mindset), and this can create psychological unease. The uncertainty presented by inevitable technological and societal developments will require leaders to be proactive in offering a leadership style that is more sensitive, adaptive, and empowering so that their teams feel heard and supported through these shifts. In turn, this authentic approach to investing in employees and providing recognition of their intrinsic value will also help to retain and attract talent in these challenging times.
Transformation is now commonly viewed as being more of a journey than an end point. The long-term capability and culture of life-long learning will need authentic leadership to generate a psychologically safe environment that motivates teams to evolve, grow, and disrupt so that businesses don’t just survive but truly thrive. M
About the authors:
Nigel Lowe is a Partner and people and change expert at PA Consulting
Nini Ali-Khan is a change management expert at PA Consulting
Shanton Wilcox is a Partner and America’s Leader in Manufacturing at PA Consulting
The Evolution of Manufacturing Jobs
Networking technology is driving transformation and empowering leaders through both growth and disruption.
TAKEAWAYS:
● Digital transformation and the evolution of manufacturing jobs rely upon enhanced connectivity.
● The workforce evolution isn’t just about how jobs are done but also who is doing the jobs.
● Business leaders can find success through employee training and digital transformation that leverages networking technology.
This is a different manufacturing industry than even a decade ago. What got the industry here today, will not get it where it needs to be tomorrow.
Manufacturing leaders are grappling with how to adapt and grow in an environment that is undergoing constant disruption by advances in technology, globalization, and shifting customer demands.
The Evolution of Manufacturing Jobs
In the past, manufacturing jobs primarily involved manual labor and repetitive tasks on assembly lines. Today, these jobs are evolving to include a higher degree of automation, digitization, and skilled labor. This same transformation is happening in other industries and even at AT&T.
What are the factors contributing to this radical sea change?
- Automation and robotics: The rise of automation and robotics in manufacturing has led to a reduction in the need for manual labor. Tasks that were once performed by humans are now being handled by machines, allowing workers to focus on higher-value tasks that require specialized skills and expertise.
- Advanced manufacturing techniques: The adoption of advanced manufacturing techniques, such as additive manufacturing (3D printing) and computer numerical control (CNC) machining, has led to a greater need for skilled workers who can operate and maintain these sophisticated technologies.
- Digital transformation: The manufacturing industry’s digital transformation has created a growing demand for workers with expertise in data analytics, machine learning, and other digital skills. As manufacturers increasingly rely on data-driven decision-making, workers must be able to interpret and analyze complex data sets.
- Globalization: As companies continue to expand their operations across borders, there is an increasing need for workers who can navigate the complexities of global supply chains and communicate effectively with colleagues and partners around the world.
This evolution is not just about how jobs are done. It is also about who is doing them. The shift toward some jobs requiring higher levels of education and less physical strain has helped create more opportunities for women in the industry.
“Although men still hold the majority (67.9%) of U.S. manufacturing jobs, the Census Bureau’s Job-to-Job (J2J) Flows Explorer shows that from 2010 until the pandemic struck in 2020, the share of women in manufacturing jobs rose in every working-age category,” according to an October 2022 U.S. Department of Commerce report. “In 2021, the data show the numbers going back up to pre-Covid levels. Certain age groups show an even higher spike than before the pandemic. For example, 8.6% of the people who went into manufacturing jobs were women ages 55 to 64 before the pandemic but increased to 9.1% in 2021.”
“Advanced connectivity is critical for driving innovation, improving efficiency, and enabling new ways of working”
While there has been progress in getting more women in the industry, there is more work to be done including taking a proactive approach to providing and seeking out opportunities for women and encouraging women to lean in to be comfortable while not placing artificial limits on others. And once a woman has her foot in the door, she should send the elevator back down for others who are waiting in the lobby for their opportunity.
The Role of Enhanced Connectivity
Enhanced connectivity, enabled by technologies like 5G and fiber-optic networks, is playing a crucial role in this manufacturing jobs evolution and the industry’s digital transformation. The increased speed, bandwidth, and reliability of these advanced networking solutions provide numerous benefits for manufacturers, including:
- Real-time data exchange
- Accelerated decision-making
- Improved collaboration
- Support for IoT and Industry 4.0
- Remote monitoring and control
- Enhanced supply chain visibility
- Support for remote work and distributed teams
- Scalability and flexibility
- Reduced latency
By embracing enhanced connectivity solutions like 5G and fiber-optic networks, manufacturers can unlock a range of benefits that help them adapt to the changing nature of manufacturing jobs and stay competitive in the digital age. This advanced connectivity is critical for driving innovation, improving efficiency, and enabling new ways of working in the manufacturing industry.
More than just 5G and Fiber
Other networking technologies, from IoT to cybersecurity, are also playing crucial roles.
IoT devices and sensors connected via networking technology collect real-time data on production processes, equipment, and environmental conditions. This data enables manufacturers to monitor their operations closely, identify potential issues, and optimize their processes for greater efficiency and productivity.
Networking technology has facilitated the widespread adoption of cloud computing in the manufacturing industry. Cloud-based platforms and services allow companies to store, process, and analyze vast amounts of data, streamline their operations, and enhance collaboration among employees and external partners.
As manufacturing operations generate massive amounts of data, edge computing has emerged as a valuable solution to process and analyze this data close to its source. Networking technology enables edge computing by connecting devices and systems at the edge of the network, reducing latency, and ensuring real-time analysis.
“Leaders must be proactive in adapting strategies and practices to this new reality and workforce”
With the increasing need for connectivity by manufacturing operations, the importance of robust cybersecurity measures has become paramount. Networking technology plays a critical role in securing data and communication channels, protecting businesses from potential cyber threats and ensuring the confidentiality, integrity, and availability of information.
Meanwhile, networking technology has revolutionized supply chain management in the manufacturing industry by facilitating real-time communication, data exchange, and collaboration between various stakeholders, such as suppliers, logistics providers, and customers. This enhanced connectivity allows companies to optimize their supply chains, minimize disruptions, and respond rapidly to changes in demand.
How Business Leaders Can Respond
That is a lot of disruption! It is exciting, but it also creates unique challenges that previous manufacturing leaders never encountered. Today’s leaders cannot be laggards. They must be proactive in adapting strategies and practices to this new reality and workforce. Here are some steps they can take:
- Invest in employee training and development: As the nature of manufacturing jobs evolves, it is essential for companies to invest in ongoing training and development programs that help workers acquire the necessary skills and expertise. This includes providing access to online courses, workshops, and industry conferences focused on networking technology, automation, and digital skills.
- Embrace digital transformation: Business leaders must recognize the importance of digital transformation and embrace the adoption of advanced technologies, such as IoT, cloud computing, and edge computing. This involves not only investing in new technologies but also developing a culture of innovation and continuous improvement within the organization.
- Foster a culture of open communication: Encouraging communication and collaboration across the organization is crucial for adapting to the evolving nature of manufacturing jobs. Leaders should provide employees with the tools and platforms they need to share ideas, ask questions, and collaborate with their peers, both internally and externally.
- Leverage data-driven decision-making: As manufacturing becomes increasingly data-driven, leaders must learn to leverage data and analytics to make more informed decisions. This involves investing in data analytics tools and platforms, as well as training employees to use them effectively.
- Prioritize cybersecurity: With the increasing reliance on networking technology and connectivity, it is crucial for business leaders to prioritize cybersecurity. This includes implementing robust security measures, such as firewalls, intrusion detection systems, and encryption, as well as educating employees about cybersecurity best practices.
- Build strong relationships with external partners: In a globalized economy, it is essential for manufacturers to build strong relationships with external partners, such as suppliers, logistics providers, and customers. Networking technology can help facilitate these relationships by enabling real-time collaboration and information sharing.
- Prepare for the future of work: The manufacturing industry is continually evolving, and business leaders must be prepared for future changes to the nature of work. This includes staying informed about emerging trends and technologies, such as advancements in networking technology, as well as being open to new ways of working and managing talent.
In conclusion, the evolution of manufacturing jobs – driven by technological advancements, globalization, and changing customer demands – is significantly impacting the industry. Networking technology is at the heart of this transformation, enabling businesses to adapt and thrive in this new environment.
By investing in employee training and development, embracing digital transformation, and leveraging the many benefits of networking technology, business leaders can position their organizations for success in manufacturing’s future. It is essential for leaders to stay informed about emerging trends and technologies, be prepared to adapt their strategies and practices, and seize the opportunities presented by this rapidly changing landscape. M
About the author:
Andrea (Ande) Hazard is Vice President, Manufacturing and Transportation Solutions for AT&T Business where she leads a team of sales professionals, technical architects and engineers delivering AT&T products, services and global solutions to enterprise clients. Her organization focuses on the manufacturing, transportation, logistics and consumer packaged goods industries, ensuring an integrated, enterprise-wide customer experience for their clients.
The Best Tool for Employee Retention? Listening to Them
Soliciting feedback is key to bridging the gap between what workers want and what employees offer.
TAKEAWAYS:
● Compensation, health care and retirement perks are typically the top priorities of what employees want most, regardless of industry.
● Giving employees a clear framework for defining their career paths could be one area ripe for improvement.
● Employees want opportunities to be heard, and for their employers to take their feedback into consideration.
Manufacturers have been grappling for years with how best to fill thousands of job openings on factory floors and white-collar positions, and economic headwinds are only adding more challenges to hiring within the sector.
As of March, the manufacturing sector contracted for the fourth consecutive month, according to data from the Institute for Supply Management. Also in late March, the RSM US Manufacturing Outlook Index—a composite index based on surveys of business sentiment conducted by six regional Federal Reserve banks—showed manufacturing activity was 1.8 standard deviations below normal. RSM’s index can be considered representative of the general direction of national manufacturing activity.
“That slowing leads us to think that firms will do their best to hold onto their workforce, minimizing the loss of employment in the coming quarters even if there were to be a recession,” RSM Chief Economist Joe Brusuelas wrote in an article that month.
“A recent survey reveals where employee priorities lie and generational nuances within the workforce — valuable insights that can help manufacturers boost retention.”
One aspect of addressing recent hiring challenges may seem obvious: Companies should listen to what employees say about their priorities and what they want most from their jobs. Proprietary data collected by advertising, technology and data company Big Village on behalf of RSM US LLP in 2022 reveals where those priorities lie and generational nuances within the workforce — valuable insights that can help manufacturers develop strategies that can boost retention for the increasingly digital factories of the future.
Understanding Employee Priorities
Compensation, health care and retirement perks are typically the top priorities of what employees want most from their employers, regardless of industry. But data from the Big Village and RSM survey shows how manufacturing sector respondents value the benefits their organization currently offers, compared to the importance of various benefits if respondents could create their ideal benefits package.
For instance, 29% of manufacturing sector respondents said above-market compensation would be critically important in their ideal benefits package, but only 13% of respondents said their employer offered such compensation. (The online survey was conducted among a sample of adults ages 18 and older in the United States who reported having at least one job.)
In numerous categories, the number of respondents who said their organization currently offered a given benefit was comparable with the number who said that benefit would be part of their ideal compensation package (Figure 1).
Figure 1: Manufacturing Sector Respondent Answers, RSM US Survey
For some categories, though, the gap between what the employer currently offered and what would be in the ideal benefits package was wider (Figure 2).
Figure 2: Manufacturing Sector Respondent Answers, RSM US Survey
Along with competitive compensation packages, the data seems to indicate that giving employees a clear framework for defining their career paths could be one area ripe for improvement. Responses to other parts of the survey underscore this further; manufacturing sector respondents said that if they could have the ideal job, the three most important factors would be work-life balance, support from their supervisor/boss, and the potential for advancement/promotion (Figure 3).
Figure 3: If you could have the ideal job, how important of a role would each of the following play?*
For an accurate assessment of employee priorities and desires, manufacturers might consider conducting a similar survey among their teams. Leadership teams can then use the resulting data to develop or adjust employee compensation and benefits packages, rather than guess what workers want.
Generational Shifts
Understanding millennial and Gen Z perspectives on their jobs and employers will also become increasingly important as the presence of those cohorts rises in the labor force. Among all respondents — including those in the consumer products, technology, business and professional services, construction, financial services, and other sectors — significantly more members of the Gen Z and millennial cohorts wanted flexibility compared to their older counterparts.
Figure 4: To what extent do you agree with the following statements?*
Millennials were also significantly more likely than others to report:
- They would recommend their current organization to a friend (52% vs. 37% Gen Z, 43% Gen X, 37% boomers)
- Employee recognition programs are a critical benefit (32% vs. 24% Gen Z, 25% Gen X, 13% boomers)
- Consistent feedback on their performance is critical (36% vs. 27% Gen Z, 26% Gen X, 16% boomers)
- Collaboration with co-workers is critical (39% vs, 30% Gen Z, 28% Gen X, 21% boomers)
- Gen Z and millennials are significantly more likely than Gen X and boomers to report that they were actively applying for a new job/role, with 24% of Gen Z respondents, 30% of millennials, 14% of Gen X respondents and 6% of respondents in the baby boomer generation.
Those figures—even though they are respondents from all industries, not just manufacturing—should make clear just how important retention efforts are for any business.
Workforce Ownership in the Factory of the Future
Manufacturers need to respond to what workers want and give them a clear path for success if they aim to build a workforce that has longevity and adaptability for the future. Here are some of the most important areas we believe companies should zero in on:
- Flexibility: The pandemic may have thrust flexibility into the spotlight, but it is now table stakes for manufacturers that want to draw top talent. Flexibility isn’t just about remote work or adjustable schedules; workers also want to have the ability to navigate childcare and other obligations of daily life in a way that meshes well with their job. Manufacturers should assess where they may be able to improve options for workplace flexibility, for both factory floor and white-collar workers.
“Manufacturing sector respondents said the three most important factors in an ideal job would be work-life balance, support from their supervisor/boss, and the potential for advancement/promotion.”
- Compensation: Salary or wage considerations have always been one of the most important considerations for workers seeking employment, but two factors in particular right now require companies to provide competitive pay; inflation putting stress on consumer wallets and the manufacturing sector competing more and more with other industries (such as technology) for talent. Leadership teams should review compensation packages and adjust to align with the market and competitors.
- Career path: Employees do not want to remain stagnant in any position, and our survey results above indicate the importance of organizations offering employees defined career paths. For manufacturers, this might include intentional digital skills development, clear frameworks for improvement, continuing education to understand the implications of the factories of the future, and mentorship programs. Manufacturing companies should help employees chart their future within the organization based on their goals and talents.
Perhaps one of the clearest takeaways from the workforce shifts of the last three years is that employees want opportunities to be heard, and for their employers to take their feedback into consideration. Manufacturers that take a strategic approach to gathering and addressing employee feedback will have a competitive edge as the sector continues to evolve. M
Survey Methodology
The online CARAVAN® survey was conducted by Big Village among a sample of 2,017 U.S. adults ages 18 and older who are employed. Of these, 175 reported working in the manufacturing sector. Data collection occurred from Sept. 23 through Oct. 6, 2022.
About the authors:
Marni Rozen is a management consulting director at RSM US LLP.
Jason Alexander is a partner and national manufacturing sector leader at RSM US LLP.
Welcome New Members of the MLC June 2023
Introducing the latest new members to the Manufacturing Leadership Council.
Introducing the latest new members to the Manufacturing Leadership Council.
Anupam (Anu) Khare
Global Chief Information and Digital Officer
Oshkosh Corporation
www.oshkoshcorp.com
www.linkedin.com/in/anupamkhare/
Kevin Goering
Partner, North American Manufacturing Lead
McKinsey & Co.
www.mckinsey.com
www.linkedin.com/in/kevin-goering/
Holly Becker
Director, Commercialization
ATS Global
www.ats-global.com
www.linkedin.com/in/holly-elyse/
Frank Hopkins
Project Manager
Faith Technologies
www.faithtechnologies.com
www.linkedin.com/in/frank-hopkins-01625490/
Suresh Palanisamy
Professor and Director, Manufacturing Futures Research Platform
Swinburne University of Technology
www.swinburne.edu.au
www.linkedin.com/in/suresh-palanisamy-6b4a3250/?originalSubdomain=au
Ergun Hepvar
Director, Corporate Innovation
International Paper
www.ip.com
https://www.linkedin.com/in/ergun-hepvar-0a447a/
Fernando Garcia
Director, Sales
Ubisense
https://ubisense.com/
https://www.linkedin.com/in/fernando-a-garcia-74581612/
MLC Members can view the full MLC Member Directory here.
How ALOM Triumphs in a Tight Labor Market
How can manufacturers recruit and retain employees amid a skills gap that leaves hundreds of thousands of manufacturing jobs unfilled every month? ALOM Technologies Corporation—a global supply chain management services and solutions provider based in Fremont, California—has an answer: focus aggressively on company culture.
The results are in and ALOM’s program is a remarkable success, leading to workforce and revenue growth for the company over the past few years. This achievement led ALOM to be named a finalist for the Manufacturing Leadership Awards, given every year by the Manufacturing Leadership Council (the NAM’s digital transformation division). Here’s a sneak peek into how they did it.
The program: After being named an essential business in 2020 due to its medical supply chain infrastructure, ALOM turbocharged its existing culture program, called DOING—which stands for Development, Opportunity, INclusion and Growth—to support staff recruitment and retention in a challenging labor market.
- The program had existed since 2018 and was based on ALOM’s longstanding cultivation of values-driven purpose. When the company expanded it during the pandemic, it enabled ALOM to build a higher performing team across multiple locations.
The details: ALOM has employed several strategies for reinforcing its cultural values, aiming to instill a sense of purpose and belonging in job candidates and veteran staff alike. These include:
- Showcasing their commitment to diversity, inclusion and sustainability both inside the organization and in recruitment efforts;
- Redefining the ALOM People Team mission and structure to emphasize staff development over compliance;
- Working to address employee wellness through stress and mental health education and resources; and
- Instituting a staff development online portal called ALOM University that empowers rapid onboarding, training and advancement.
The results: The program has been an extraordinary success, helping to increase ALOM’s workforce and strengthen the company’s bottom line at the same time. In 2021 alone, the company achieved:
- 70% workforce growth;
- 60% revenue growth;
- A 6% decrease in employee attrition for 2021, as compared to 2018; and
- A 65% reduction in recruitment days to fill open positions.
Looking ahead: ALOM isn’t done yet. This year, the company is working on a digital transformation effort, called DOING DX, designed to make all of ALOM’s tech systems and business processes more efficient and effective.
- It will focus on staff recruiting, performance management, supplier management and evaluation, team building, mentoring and much more.
The last word: “When I started ALOM 26 years ago, I was determined to build a supply chain company that did right by everyone,” said President and CEO Hannah Kain.
- “This has become the foundation of ALOM’s corporate culture. We believe in using the supply chain to help the world be a better place—for the environment and for every person, supplier and company. Experiencing our values in action instills a sense of pride and belonging in our staff that helps us attract, build and retain an exceptionally talented team.”
Get involved: Want to learn more about this successful workforce effort, as well as a whole host of other innovations by leading manufacturers? Join the MLC for its Rethink summit in Marco Island, Florida, on June 26–28. Sign up here.
At Hershey, a Sweet History and Saltier Future Powered by Digital
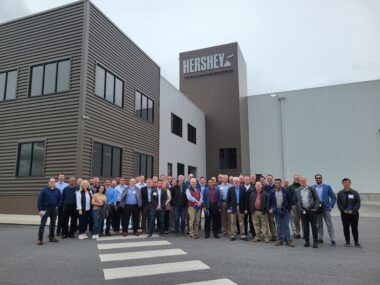
From its namesake chocolate bars to the immensely popular Reese’s Cups, The Hershey Company has been a maker of beloved confections for many decades. But no matter which variety is your personal favorite, Hershey’s powerhouse combination of manufacturing, fulfillment and distribution keeps those famous brands coming to store shelves and to the consumers who love them, generation after generation.
Nearly 100 Manufacturing Leadership Council members took part in a tour encompassing two Hershey facilities: the West Hershey plant in Hershey, Pa., and their nearby Annville Fulfillment Center in Annville, Pa., which is also Hershey’s first fully digital facility.
As a $10 billion publicly traded company, Hershey is perhaps most famous for its chocolate brands and other confections, but it also has expansion goals to evolve into a leading snacking powerhouse. To that end, it has acquired several brands of salty snacks, including Skinny Pop Popcorn, Pirate’s Booty puffs and straws, and Dot’s Pretzels. Its nearly 4,000 SKU brand portfolio is carried out through 21 plants (14 in the United States, seven internationally), roughly 950 global ingredient and packaging suppliers, 60 contract manufacturing and contract packaging partners, 34 distribution centers, and 143 freight carriers.

One thing that leadership emphasized on the tour was Hershey’s move from “best in cost” to “best in class.” Fulfilling Hershey’s vision as a snacking powerhouse means focusing on people-first manufacturing, which includes skill development, career advancement and teambuilding; innovating through technology, including through its digital factory strategy; and a focus on reliability. But in addition to its future aspirations, Hershey also needed to respond to evolving market and operational conditions – the company saw more volume growth during the pandemic, but retirements meant that its mean labor tenure decreased significantly, while lead times for packaging and capital equipment lengthened. Those shifts means that the company was left with a need to respond faster.
Investment in transformation capabilities has been essential. The company has moved away from conventional lines with single-purpose assets and focused SKU portfolios with complex line changeover requirements to advanced technology lines that can handle diverse SKUs with faster cleaning and changeover capabilities. Overall, Hershey’s digital factory strategy is focused on four areas: data capture and analysis to facilitate rapid problem identification and resolution; physical automation; a digital backbone (encompassing universal data architecture), and digital quality to bring forth a paperless shop floor. The company performs mass customization at scale through robotics and digital integration.
During the visit to the West Hershey production plant, which originally opened in 1990, attendees got an inside look at some of the production lines in the world’s largest and most technologically advanced chocolate manufacturing plant (750,000 square feet). It takes 26,000 cows to supply the milk needed to produce the Hershey’s Kisses (70 million a day), chocolate bars and syrup made here – one million pounds each of milk chocolate and Hershey’s Syrup each day. There is no storage for intermediaries at this facility – as soon as products are made, they are put onto a truck.
The 800,000-square feet Annville Fulfillment Center started production in October 2021, going from its groundbreaking to operation in just 16 months. It includes 62 trucking bays and 18 packing cells with flexibility to handle packages anywhere between two ounces and six pounds. Some of its advanced features include a cloud-based technology stack, digital work instructions for operators, and environmentally friendly battery-powered forklifts. The company will continue to scale up operations there as they leverage the facility’s full capacity.
The Annville facility is a joint operation between Hershey and its logistics partner, DHL. While Hershey owns the facility and its capital equipment, the majority of the workforce there are DHL employees. The Annville leadership team says that the partnership capitalizes on the strengths of both organizations, such as Hershey’s digital production know-how and DHL’s warehousing and logistics expertise. The facility utilizes a flex labor setup with cross-training between machine operators, palletizing operators and other functions to ensure that operations are adequately staffed at all times.
During the tour’s panel discussion at the end of the day, leadership emphasized that one important aspect of Hershey’s success is the company culture, originated by founder Milton Hershey more than 100 years ago. Bringing the workforce on board has allowed them to accelerate past “pilot purgatory” for the company’s digital aspirations. Panelists described what they call “Hershey nice” – a mix of collaboration and consensus-building where everyone treats each other with respect. The culture is vested in the company’s success, which therefore means that there is passion to share success and continually strive for improvements.
For that reason and many more, the company behind “the sweetest place on earth” might also be one of the sweetest places to work, and why Hershey is positioned to grow successfully toward its future aspirations – starting on the factory floor and branching out to snack lovers everywhere.
Crystal Ball: A Futuristic Workforce Odyssey
For humans and machines to work together by 2030, the workforce evolution must start now
Extrapolating from the results of NTT DATA’s recent research report, Innovation Index: Shifting from Disruption to Growth, Kim Curley, NTT DATA’s Digital Evolution Leader and Vice President of People & Organization, shares her insights about the future of the manufacturing workforce in the first of our Manufacturing in 2030: Crystal Ball series.
Picture this: the year is 2030. Across the U.S., the manufacturing workforce has evolved into a symphony of humans and machines working in harmony. This dramatic transformation has made the workforce a technology-enabled powerhouse. Artificial intelligence, robotics, and virtual reality lead the charge, transforming the factory floor into a buzzing and orchestrated hub of activity.
Workers use advanced technologies to perform their tasks more efficiently and safely, collaborating seamlessly with their robotic counterparts. The shop floor thrums with the smooth whirr of precise machinery and the hum of advanced systems. Augmented reality displays guide workers through complex tasks. And to make this possible, the workforce has become a melting pot of diverse talents and skills that is continuously learning and developing
It is a rosy view of the future, but realistic based on current data and trends that illuminate a path to this future state.
Changing Skillsets for 2030
The 2030 manufacturing workforce will be doing things quite differently than they do today. Four in 10 manufacturers have already begun leveraging augmented or virtual reality devices, and that will only increase. That usage will expand to support workforce instruction and training. One example of this could be teaching workers to switch over a production line. Providing that training in a virtual reality environment would mean the company doesn’t need to shut down real-world production.
As the usage of advanced technologies rapidly expands, the skillsets of the manufacturing workforce must expand, too. In addition to physical technical skills, workers will need to strengthen their understanding of technologies as well as problem solving, critical thinking and leadership skills. To build that workforce over time, you must start by expanding the skillsets of managers and leaders now. Starting today is critical to being successful in 2030, indeed, 39% of manufacturers report that they have already increased their investment in leadership development.
A More Resilient Enterprise
The evolved workforce will enable significant benefits. The big one is resilience. An augmented workforce better enables the company to respond to changes in the marketplace. With such a workforce, companies can train faster, reset the lines, and change worker skillsets more rapidly. Paving the way for this evolution, upskilling and reskilling programs for new and/or existing workers are underway today at 54% of manufacturers. More broadly, making your workforce future-ready entails steps such as improving safety, productivity and talent; incentivizing workforce agility; teaching new leadership skills; engaging the workforce; and maintaining a future-focused mindset. We’ll look at each in turn.
Improving Safety, Productivity, and Talent
The NTT DATA 2023 Innovation Index survey showed that businesses are increasingly addressing potential disruptions in strategic plans because these events present opportunities for those businesses that can act with resilience and speed.
So, it is not surprising that manufacturers are placing increased importance on their workforce and the workforce’s ability to adapt and move quickly. The more connected and engaged the workforce is, the better it can shift and flex when the unexpected happens.
Three vital areas come immediately to mind when considering how these coming changes address the problems facing today’s manufacturing industry. The first is safety. As noted earlier, one of the best commercial applications of virtual technologies is training. Training workers to complete physically demanding or potentially hazardous tasks in a completely safe environment — without the cost of physically constructing such simulated environments — is a game changer. Fully 77% of manufacturers report plans to use these technologies within the next two years. That’s well ahead of the cross-industry average of 64%. Using these tools for ongoing training programs helps ensure that workers know exactly what they need to do and how to do it. And it does that while protecting their safety and the safety of the products they manufacture.
A second area of lift is in productivity — specifically, decreasing production errors and downtime. The proliferation of sensors enabled by 5G, advanced computing and machine learning technologies gives us better insights than ever before. These insights enable us to better plan and use scarce resources, another game changer.
The third area is talent. Emerging technologies in the factory call for a new-collar workforce that understands both manufacturing and Manufacturing 4.0. As the industry increases its use of and innovation with advanced technologies, more visionaries will be attracted to manufacturing. At the same time, advocacy initiatives like the Manufacturing Institute’s Creators Wanted program help spread information about this shift in manufacturing work so the next generation of young talent is aware of these opportunities to work with technology. This shift in the reputation of the industry overall can help bring the best and the brightest talent into manufacturing. The workforce will transform from the outside in as it changes from the inside as well.
Incentivizing Workforce Agility
For people and technology to align more closely, it will be important that the workforce sees the benefits of change. Many additional technologies come into play with a technology-enabled workforce. Remote collaboration tools and digital twins can allow manufacturers to assess and optimize processes virtually. These tools may require their users to have specific skills, such as a familiarity with the way data is used to create digital twins, to realize their full value. An agile and augmented workforce will be prepared with those skills or will be readily able to develop them.
The heightened importance of the workforce will call for momentous changes. Historically, manufacturing has considered the human as a component of the manufacturing line. The concept of human capital itself came from the manufacturing industry. Shifting our thinking changes how we develop people and give them desirable career progressions. It also impacts how we pay and incentivize people.
Adopting practices for compensation, rewards, and training from other industries to attract and keep the best and brightest can be beneficial. In high tech, for example, companies such as Google, Apple, and Facebook prioritize employee development and learning opportunities. They offer training programs, mentorships, and career advancement pathways. Some 84% of manufacturers have at least piloted investments in training for employees in areas such as factoring customer behavior into decision-making. To date, though, just three in 10 manufacturers report adjusting total rewards packages to increase their competitiveness when searching for new talent or retaining existing workers.
New Leadership Skills
The path to a future-ready workforce will include overcoming hurdles. One of the biggest is the need for a radically new style of leadership. Leaders in-house today often have massive institutional knowledge and a long history of viewing the workforce in a particular way. Having such leadership has often led to success. But going forward, that will need to change. That is a challenge. You have to teach the most senior leaders to see the workforce — both its potential and its needs—differently. But even incremental change comes slowly. Presently, for example, only 13% of manufacturers report being highly effective at delivering on worker-centric policies such as flexible working options and schedules.
Certainly, you cannot change a whole company’s culture unless you’re working from the top down as well as the bottom up. But once you do, you are positioned to develop and sustain a culture of innovation, experimentation, and resilience.
Engaging the Workforce
The workforce can and should be an active part of its own evolution. First, engage with your workforce – truly engage. Understand who your people are and what is important to them. Find ways to connect them to your company’s purpose and the impact you want to have on the world around you. The stronger those connections are, the more powerful a force your workforce can be in driving the transformation you’ll need over the coming years.
Second, expose more of the workforce to technologies and how these tools can help them and the business. Manufacturers are slightly behind the cross-industry average at the use of updated tools and technologies, with only 29% considering it important to employee satisfaction and engagement. Our Innovation Index shows that the best ideas to advance the business most often come from the individuals who already know the most — your workforce.
A Future-Focused Mindset
Mindset is everything. Without a growth mindset at every level of your organization, you will struggle to accomplish a transformation that will drive success between now and 2030. This mindset must be pervasive, encompassing everything from policies to hiring practices, investment decisions and the employee value proposition you put into the marketplace. When you embrace a mindset that says we are going to try new things and grow, and your workforce embodies it every day, you will create a resilient organization that is comfortable pushing boundaries to create the future.
About the author
Kim Curley is Digital Evolution Leader and Vice President of People & Organization at NTT DATA.
Hannover Fair 2023: It’s Not Technology Anymore. It’s All About Data, Data, Data.
Whatever advanced technologies manufacturers adopt, future transformational success will ultimately depend on data, from powering the latest digital tools to deliver more value, to creating entirely new industry-wide data ecosystems, to the foundation of enticing new Industrial Metaverse applications for the future, reveals this year’s Hannover Fair in Germany.
Emerging from three years of COVID disruption, the world’s largest industrial fair in Hannover, Germany, began to bounce back this year with a renewed sense of optimism about the future of digitally enabled manufacturing, hosting more than 4,000 exhibitors from 62 countries showcasing their latest innovations, and over 130,000 visitors from around the world.
Many of the impressive and varied transformational solutions on display, however, also revealed a fundamental change of emphasis from years gone by. This year, Hannover was a lot less about promoting individual products and technologies, and much more about the underlying power of data to fuel those advanced digital tools in order to drive greater efficiencies, resiliency, value, and sustainability, for both internal operations and entire manufacturing value chains.
“Without data, we will never take manufacturing to the next level and scale,” declared Rainer Brehm, CEO of Factory Automation at Siemens, launching the company’s new Industrial Operations X approach, which is based on the three pillars of software-defined automation, data-driven production, and access to an open, industry-wide data ecosystem.
Manufacturing X
The use of the letter X in the Siemens’ nomenclature is highly significant. It echoes a new and rapidly emerging industrial data sharing initiative in Europe called “Manufacturing X”, an approach showcased by multiple companies throughout the 17 busy exhibition halls at this year’s event.
Manufacturing X aims to create a safe and agile next generation data infrastructure for manufacturing industry players to network, share, and exchange key product and other information with approved partners and customers in a compliant, standardized way, solving many of the current issues companies face in creating end-to-end real-time visibility across supply chains and making it easier for manufacturers to drive and scale transformational change.
The concept envisages a federated cloud-based “data space” where companies can upload dedicated “data containers” housing fully detailed, standardized information on any manufactured product or service, whether that is a factory machine tool or a wind turbine. Each data container can include key information ranging from authenticated product documentation (sometimes known as a Product Passport) to full maintenance and service manuals, compliance details, lifecycle frameworks, performance data, CAD files, ready-made digital twins, and even details of the carbon footprint of each unit or component.
In the same way that standardized freight containers revolutionized the freight transport industry, explained the team at German automation company Phoenix Connect, Manufacturing X aims to create an industry-wide data ecosystem where standardized containers of data can be easily accessed and securely shared across qualified partners and customers within a manufacturing value chain.
Easy access to the digital twin of each manufacturing asset, for example, can make it far simpler for companies to build plant-wide virtual digital twins, or train service engineers to troubleshoot equipment issues, and detailed production specifications can be instantly shared with key manufacturing partners to help cut time to market for new products or mitigate sudden supply chain disruptions.
Based on open standards and interoperability, Manufacturing X also aims to break industry dependency on today’s proprietary systems and networks by building an open and trusted framework that allows all industrial companies, automation providers and manufacturing customers alike greater control and sovereignty over their data in the future.
Many examples of this new X data space concept were already in action at the Fair, including the advanced Production Level 4 ecosystem created by German research group SmartFactory KL, in which a rapidly reconfigurable, modular, shared production line harnesses interconnected machines and technologies from multiple suppliers, combining advanced digital process tools, AI, collaborative robotics, its own implementation of the data space concept called SmartMA-X, and the Asset Administration Shell (AAS) specification, which creates detailed standardized descriptions of each individual asset.
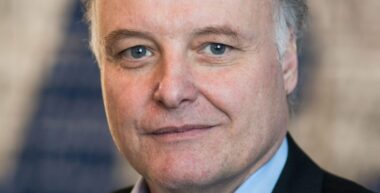
“Manufacturing X represents the next stage of Industry 4.0,” Dr. Gunther Kegel, President of the German Electronics and Digital Industry Association, ZVEI, told German Chancellor Olaf Scholz and the packed audience of senior industry leaders and dignitaries at the Hannover Fair’s high-profile Opening Ceremony on the eve of this year’s Fair. Manufacturing X, he continued, is an important element in the creation of a safe and secure industrial data economy of the future that fosters increased networking, resiliency, sustainability, and climate protection among all industry players.
Foundations of a Future Data Economy
Manufacturing X is only one implementation of a much broader data ecosystem concept called Gaia-X, initially conceived as a European initiative in 2019 but now with evolving global ambitions.
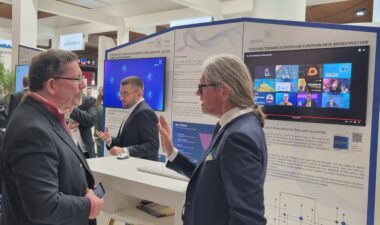
Gaia-X aims to build the foundation of a future data economy across multiple industry sectors based on the same idea of a shared and secure data ecosystem, explained Gaia-X CEO Francesco Bonfiglio, in an interview with MLC.
Other implementations include Catena-X, designed to support auto industry companies to share data on products and parts across their value chains. It has already attracted many leading auto industry partners, including BMW, Mercedes Benz, Volkswagen, Ford, Volvo, Renault, and tire maker Continental, plus technology innovators including Microsoft, IBM, SAP, Siemens, Fujitsu, Hewlett Packard, and many more. A health industry X-version for the pharmaceutical and medical devices sector is also preparing to launch in the near future, with future plans for similar data ecosystems covering other sectors including aerospace, agriculture, energy, logistics, and more.
Ecosystem Challenges
Such next generation industrial data ecosystem initiatives are both innovative and ambitious, but they are still in their early stages and there are many challenges yet to be overcome, from political infighting among European members, to the practicalities of sector-wide implementation.
In a panel discussion entitled “Towards a Federated Industry Data Ecosystem”, representatives from the Industrial Digital Twin Association (IDTA), Gaia-X, BMW, and German automation company Festo were candid about a host of challenges ahead for companies, as well as the industry as a whole, in building data ecosystems.
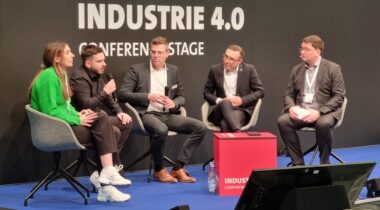
Chief among the challenges the group identified were establishing trust among participants; assembling a critical mass of participants to make an ecosystem work properly; understanding and adopting a common legal framework to enable intellectual property protection, an important foundational element of trust; and dealing with the technological complexities of such elements as data spaces and data containers.
But perhaps the most significant challenge voiced by the panel was bringing along small and medium size manufacturers, a group that often doesn’t have the focus, expertise, and financial wherewithal to undertake what by any measure will be a significant effort to adopt and operate data ecosystems.
To help bring the small manufacturers along, the panel recommended the development of technology tool kits to simplify the development of new business models based on the data ecosystem idea. One such example already exists within the Catena-X group.
The other emerging consideration for any manufacturers adopting the data ecosystem idea is how it will affect their competitive profile as well as the competitive landscape of the markets in which they do business. Will participation in such ecosystems, should they take hold in a substantial way, become essentially a requirement in order to remain competitive? By establishing a common data playing field, will manufacturers then be able to compete on higher level factors such as more targeted products and services?
And what of potential legal issues? Will such data ecosystems be viewed in some countries in an antitrust light, prompting challenges by non-participants and government bodies? There will clearly be more developments to come in the months ahead.
Inspiring Innovations
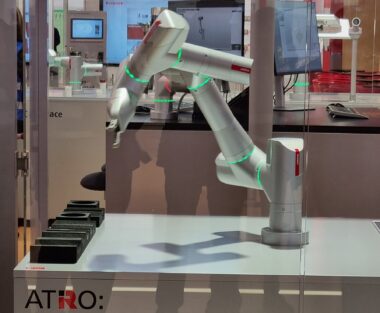
There was certainly no shortage of inspirational technologies on the stands at this year’s Hannover Fair, of course. Advanced digital twins were everywhere; AI is being embedded into almost every kind of offering; 5G is now the connecting technology of choice; and systems specifically designed to support sustainable operations – from advanced energy efficiency algorithms and on-site hydrogen production units to digital threads and twins supporting full circular economy strategies from initial product design to end of life reclamation.
AI Everywhere: Now It’s Time to Scale
The critical importance of data to drive these ever-advancing digital tools is perhaps most evident with AI systems, which were extensively showcased across the Fair this year.
While a decade of adoption of M4.0 technologies has made data better organized and more available than ever before, “An estimated 80% of data in industry remains unused,” noted Philippe Rambach, Chief AI Officer at Schneider Electric. “So, the time for AI in industry is now,” he continued, “and the next stage is to scale.”
A number of suppliers admit, of course, that overcoming the challenges of adopting and scaling AI is still a learning journey for many manufacturing companies, so products like Altair’s RapidMIner or Festo’s Automation Experience (AX) AI platform for predictive maintenance, among others, are designed to provide easier entry points for companies new to the AI arena.
Schneider Electric, meanwhile, is already applying AI in multiple ways across the company, explained Rambach, from energy optimization to driving an increasingly self-healing supply chain that supports a network of around 14,000 suppliers and 150,000 order lines a day. He identified three key areas of business focus for AI the company – to enhance customer facing services, to improve internal process efficiencies, and as an advisory tool to provide monetized consulting services in areas such as energy management and industrial automation.
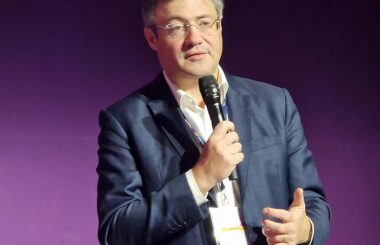
Based on his experience, Rambach advises manufacturers to approach AI adoption with three key considerations in mind. First, don’t start with AI; start with a use case that can deliver value and then ask if AI can help. Secondly, build a joint AI team made up of data specialists merged with people who have real front-line domain knowledge. In fact, Schneider’s AI team is not allowed to launch any new product in the company until it has been tested and verified by workshops of domain experts and frontline workers. Finally, to help build trust and support in AI adoption, socialize successes within the company to get all levels of employees engaged.
And to help companies ensure the AI systems they develop deliver meaningful and unbiased results, the Fraunhofer Institute was also showcasing its “Trustworthy AI” toolset on a nearby stand. This provides companies with a framework to test the quality and worthiness of their AI solutions, especially in human-dependent applications such as plant safety, medical advice, chemical processing, or even traffic management. Such formal testing and approval criteria will become increasingly essential, says Fraunhofer, with the rapid emergence of popular new generative AI tools like ChatGPT.
Omnipresent Digital Twins
While AI permeated many areas of activity, there is also little doubt that digital twins have become a primary foundational technology in driving the future of digital manufacturing across multiple application areas. Almost every digital solutions provider at the event had one or more digital twins on show, from digital versions of individual products or factory assets to full plant floor planning and monitoring systems, to end-to-end lifecycle process and circular economy applications.
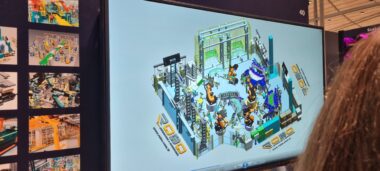
Many of those digital twin examples were built around the rapidly dominating Asset Administration Shell standard, which allows greater compatibility and interoperability between different digital twins and is backed by a collaboration between the OPC Foundation’s Open Architecture standard and the IDTA. In fact, digital twins are now so commonplace that many suppliers are proactively including digital twins of their products with every purchase so customers can more easily integrate them into their own systems for maintenance, plant floor planning, and other key use cases. These include companies like Siemens, Festo, or Harting with its product life-cycle digital twin.
The Sustainability Imperative
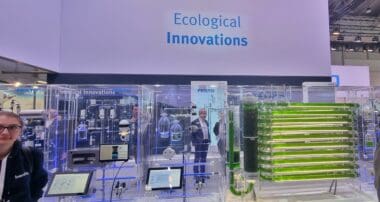
With Germany’s ambition to become the world’s first climate neutral industrial economy in the world by 2045, the presence of digitally enabled green industrial solutions was also far more in evidence than at any other previous Hannover Fair. Every company either had an explicit focus on energy reduction or showcased green energy production and infrastructure innovations – from improved plant-scale energy management applications to digitally supported processes for battery production and on-site energy storage, new low-scale green hydrogen production systems, systems for easier monitoring and reporting of Scope 3 supply chain partner emissions, and circular economy lifecycle digital twins with precise details of reclaimable content and dismantling procedures for recycling key materials and components.
One other innovative green-energy focused display was SEW Eurodrive, which has developed a family of automated guided vehicles (AGVs) that know when their power is low and can autonomously replace their own power packs with new hydrogen fuel cells as needed.
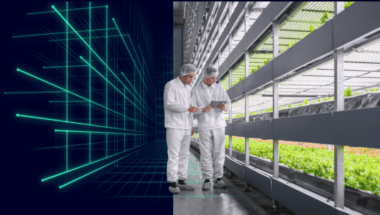
Siemens, meanwhile, showed an impressive example of how combining multiple digital technologies including AI, robotics, and visual inspection can autonomously manage vertical farms capable of delivered 300 times more fresh food yield on a comparable area of ground, using 95% less water than traditional farming methods, but without the need for any harmful pesticides or fertilizer run off.
The Dawn of an Industrial Metaverse
But perhaps the most forward-looking and engaging displays at this year’s Fair, and there were many of them, were multiple examples of emerging Industrial Metaverse applications in action. These combine multiple technologies including advanced digital twins, embedded AI, VR/AR visors, and rapid 5G communication to show how early Metaverse use cases could create collaborative virtual spaces for training, e-commerce, remote operations, factory design, product maintenance, and troubleshooting.
Once again, it is data that will drive this latest digital evolution, believes Charlie Sheridan, Technical Director of Industry Solutions/Manufacturing at Google Cloud. “Data is the foundation of the Industrial Metaverse journey”, he believes.
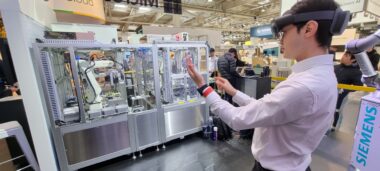
On Microsoft’s stand, for example, partner Kawasaki was using an advanced digital twin, combined with embedded AI and engineers wearing HoloLens mixed reality headsets, to show how they could work together remotely from anywhere in the world using a collaborative mixed real world/virtual environment to exchange expertise in real time to troubleshoot and fix equipment problems. “It’s the beginning of a new era,” predicts Kawasaki.
Early Industrial Metaverse applications are not all just pilots either. Real life projects are already in place at auto companies such as BMW and Renault where they are being used to create virtual factory and plant floor environments, while global chemical giant BASF is reported to have 20 Metaverse projects underway, and Norwegian battery maker Freyer is now using Siemens Metaverse technologies to help scale production capacity at both existing and new plants in rapid time to meet the predicted 700-fold increase in global demand by 2030. “We are already paving the way into the Industrial Metaverse of the future,” asserted Siemen’s Brehm.
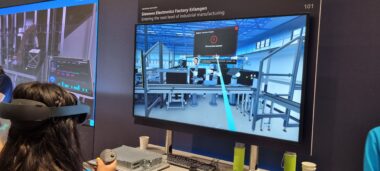
The momentum around Metaverse developments is certainly growing fast. The recently launched Metaverse Standards Forum, noted Dietmar Laß, senior researcher manager at the Fraunhofer Institute, already has over 4,000 members and is expanding fast. “We are only getting a glimpse of what may be possible now with the Industrial Metaverse, but the basics are already in place”, said Laß.
Perhaps the promise of an immersive world for future production operations, where virtual and augmented realities take digital twins and collaborative cultures to a new level, is closer than many industry leaders may think.
The Future of Data
When Stephan Weil, Minister of Lower Saxony, officially began the opening of the Fair on the Sunday evening, he hoped that the 2023 event would reveal how the power of innovation can help solve some of the world’s toughest problems, help companies balance sustainability with growth, and help foster an equitable balance between people and machines working together.
Yet, as the days went by, there was clearly more to the event than just a series of high aims this year in Hannover. There was also a fundamental sea change of emphasis across the Halls that revealed a new focus on data and perhaps a more mature ecosystem direction for future innovation and adoption to enable industrial companies to truly accelerate transformation and drive greater value.
As German industry 4.0 pioneer, founder of the German SmartFactoryKL research initiative, and former MLC Board member Detlef Zülkhe reflected: “Hannover is not about technology anymore. Today, it’s all about data, data, data.”
About the authors
Paul Tate is Co-Founding Executive Editor and Senior Content Director at the NAM’s Manufacturing Leadership Council.
David R. Brousell is Co-Founder, Vice President, and Executive Director at the NAM’s Manufacturing Leadership Council.
How a Nearly Century-Old Textile Maker Went Digital
It’s no easy feat to transform a struggling family business into a thriving digital enterprise, but that’s exactly what Cooley Group President and CEO Dan Dwight is doing.
Change for the better: Cooley Group was formed in 1926 as a family-run textile manufacturer in Rhode Island. In 2011, Dwight, a member of the NAM Board of Directors, joined the company as president and CEO to navigate the ship through a new age of manufacturing and market demands.
- Today, the private equity-backed extrusion and textile manufacturer is the leading global maker of polymer-coated textiles. Applications range from single-use blood-pressure-cuff materials, to proprietary urethane combat raiding crafts for U.S. special forces, to liners and covers for some of the world’s largest water reservoirs.
How they did it: “As a family-run business, Cooley inherited aging equipment and an aging workforce,” said Dwight, who also serves as vice chairman of the Manufacturing Leadership Council’s Board of Governors. (The MLC is the NAM’s digital transformation arm.)
- “We not only modernized our equipment and infrastructure to compete in the digital age, but also revolutionized our culture. Hierarchies slowed us down.”
- “Digital transformation isn’t only beneficial for the advancement of our physical technologies; it’s also critical to develop a more collaborative company culture that empowers employees at all levels to take action.”
Starting small: “Digital transformation—the integration of digital technology into all facets of an organization—can seem daunting at first,” Dwight said. “But that can’t deter an organization from jumping in.”
- “I advise companies, particularly mid-sized manufacturers like Cooley Group, to approach digital transformation incrementally,” he said. “Don’t expect the cultural, institutional or technological benefits of digital transformation to manifest overnight as some mega-solution.”
- “Think strategically about the areas of your business that are the first movers. Once one aspect of the business is modernized, the digital insights and team’s enthusiasm for change will build momentum to push the remaining pieces into place.”
Gaining momentum: The transformation of this firm of 300 people is ongoing. “Ten years ago, we had trouble keeping our equipment operating for any period of time,” Dwight said. “Now everything in all our factories is digitally [Manufacturing 4.0]-driven across a single operating platform.”
- The company plans to do the pilot phase of an artificial intelligence implementation later this year.
Figuring it out: The MLC was key in Cooley Group’s remarkable transformation, according to Dwight.
- “I’m not sure we would have figured it out on our own,” he admits. “I’m an avid reader; I was born excited to build things. I read a lot about manufacturing and leadership. But even if I could have figured out M4.0 strategy, actually implementing it on the plant floor would have been difficult without the support of MLC members to share best practices and to encourage the Cooley team to embrace transformation.”
Get involved: Companies can jumpstart their own digital transformation by attending Rethink, the MLC’s premier event for manufacturing executives, in Florida on June 26–28. Check it out here.
Small Manufacturers Win Big with Digital Transformation
For small and medium-sized manufacturers, digital transformation can seem like an especially harrowing task. But smaller organizations can be uniquely positioned for success in implementing firmwide digital strategies.
Small but mighty: Just look at Graphicast, a 25-person precision metal parts company in Jaffrey, New Hampshire.
- “Because the cost of data collection and analytics is getting lower and lower, even as a small company we can collect data at a rate that gives us meaningful information we can act upon,” said Graphicast President Val Zanchuk. “For example, we created a linear programming model of our business. If we’re growing at a certain rate, I can use it to determine the most economical next steps, such as whether we should hire more people, work overtime or purchase more equipment.”
A workforce solution: Graphicast, which counts Fortune 100 companies among its clientele, has used cloud computing, AI-based systems and more to help it succeed, according to Zanchuk.
- The manufacturer is also looking into the use of collaborative robots as a potential solution to the labor force shortage.
- “When it comes to Manufacturing 4.0, we think about what our customers will be looking for from us in terms of digital collaboration,” said Zanchuk, adding that some of the business’s larger customers are “transforming at a different rate than we are.” That means it’s up to Graphicast to consider client expectations and see how best to meet them given “what’s financially and operationally feasible” for the company.
The MLC helps out: To aid in Graphicast’s digital transformation, Zanchuk joined the Manufacturing Leadership Council, the NAM’s digital transformation division.
- “The MLC is the only place I know where I can discuss broad industry trends in an open fashion, where small companies like mine and large companies like Ford or GM can all be involved in the discussion,” said Zanchuk, who serves on the MLC Board of Governors.
- “Being part of the MLC lets us know if we’re on the right track and how we can make adjustments,” he continued. “It connects us to a group of incredibly talented, intelligent and experienced people who are focused on many of the same operational challenges we face.”