A Digital First Mindset for Manufacturers
Follow these five steps to enable planning, collaboration and investments in talent and technology that are vital to digital transformation.
TAKEAWAYS:
● Manufacturing companies must invest now in digital infrastructure to collect and analyze data for insights, optimization and quality improvement.
● Embracing automation will enhance efficiency and free up employees for more complex tasks.
● Collaborate with partners and invest in talent development while prioritizing cybersecurity to protect your organization’s digital assets.
The Challenge
Digital operations and data analysis are transforming the future of manufacturing. We are already seeing examples of the power of digital and data to inform, automate, and improve manufacturing processes from strategic planning to execution. Companies incorporating digital capabilities have proven efficiency gains (think constraint management, overall equipment effectiveness (OEE), quality, predictive maintenance, compliance), but will also see strategic advantage in becoming more formidable in on-going battles related to the dwindling manufacturing labor pool, demand and supply volatilities, and the overarching pervasive need to find levers to support growth or maintain already tight margins. But for most manufacturing companies, delving into digital is easier said than done with common hurdles including technical debt, reluctance to change and ineffective data management.
Operating in a digital age starts with letting go of legacy systems, processes and ways of working. But even the biggest manufacturing companies are burdened by technical debt, with outmoded systems that are incompatible with modern digital technologies. This can make it difficult to integrate new solutions into existing data, workflows and processes.
Beyond technical debt, employees can be wary of adopting new digital technologies due to a lack of understanding or fear of job loss. This can slow the adoption of digital solutions and hinder organizations’ ability to innovate.
Another complication is data management. Manufacturing companies generate vast amounts of data from machines, products and customers. However, this data is often siloed and not easily accessible or usable. This can make it difficult to gain insights into customer needs and preferences, optimize production processes, and improve product quality.
So, how do manufacturers prepare for the digital future?
Five Steps for Digital Success in Manufacturing
To shed legacy systems, bring employees on board and do more with data, it is important to invest in digital infrastructure supporting digital information systems. This will enable the collection and analysis of data from machines, products and customers to gain insight into customer needs and preferences, optimize production processes and improve product quality.
Alongside this, embracing automation will reduce costs, improve efficiency and increase productivity. By automating repetitive tasks, manufacturers can free up their employees to focus on more complex tasks that require human skills. But doing this requires careful planning, collaboration and targeted investment in talent and technology.
1. Assess the current state of digital readiness
To achieve digital success, it is vital for manufacturing companies to assess their current state of digital readiness. This all-important gap assessment helps organizations’ leadership teams to identify areas and opportunities for improvement. With this knowledge in mind, leaders can begin to prioritize their efforts and allocate resources more effectively. When selecting the most critical areas for improvement, success will be more likely when these improvement areas align with business goals and customer needs. This will help them focus their efforts on initiatives that have the greatest impact.
“Even the biggest manufacturing companies are burdened by technical debt, with outmoded systems that are incompatible with modern digital technologies”
2. Develop a roadmap for digital transformation
Having assessed their organization’s current state of digital readiness, manufacturing leaders can develop a roadmap for digital transformation that sets goals, priorities and timelines for deploying digital initiatives. This roadmap, with timebound tasks and responsible owners, focuses on objectives and avoids wasting resources on initiatives that do not align with business goals.
It is often the case that organizations throw themselves into adopting new technology and systems without necessarily considering how it supports the overall business strategy. A shiny new digital system powered by artificial intelligence might seem like a worthwhile investment but is unlikely to deliver a return on investment if it does not address a key operational need or challenge.
3. Collaborate with partners across the value chain
Customers, suppliers and service providers should be collaborators – looking at what other organizations are doing to become more digital can provide useful insight and experience. Manufacturing companies can collaborate with partners across the value chain to share data, expertise, and best practices to help them identify new opportunities for growth and innovation. They can also look beyond their own industry for inspiration and knowledge.
4. Invest in talent development
One of the key reasons firms can struggle to adopt digital is because their teams are not ready to do so. Much of this comes down to attitude, and feeling safe experimenting with new systems without worrying that they will be replaced. Helping employees to feel confident about digital systems and emergent technologies is part of the battle. A company that has had great success with digital adoption on the shop floor has worked to shift roles from operators to optimizers. It is essential to ensure employees have the right skills and knowledge to succeed in a digital environment. This starts with leaders who demonstrate the behaviors and skills required, and with digital champions who help their colleagues to build familiarity. Providing training programs, hiring new talent with digital skills, and partnering with educational institutions to develop new curricula can help to drive towards a digitally savvy workforce.
“By automating repetitive tasks, manufacturers can free up their employees to focus on more complex tasks that require human skills”
5. Prioritize cyber security
More digital assets mean a greater threat of compromise (malicious or unintentional) of IT/OT systems leading to potential to manufacturing disruptions, faulty planning and management decisions, quality issues, compliance violations or damaged business partner relationships. Conducting regular cyber security audits can flag any potential risks before they become issues and inform proactive measures to limit the negative impact. Manufacturing companies can also partner with cyber security experts to develop a comprehensive strategy.
Manufacturing organizations face myriad strategic and operational challenges; however, charting a path to digital is critical to remaining competitive and thriving in the future. Technical debt and resistance to change must be tackled head on to achieve a successful digital future. Additionally, recognizing and addressing the expanded exposure to IT/cyber risk via digital and accelerated dynamics of talent development is critical to a sustainable digital future. M
About the Authors:
Michael Platz is a Supply Chain and Manufacturing Operations Expert at PA Consulting
Shanton Wilcox is a Partner and America’s Leader in Manufacturing at PA Consulting
Winning the ‘Product Innovation Game’: The 2030 Mandate for Manufacturers
To win at product innovation, manufacturers will need to make their NPD processes more robust by integrating Operations staff earlier and by using AI and other Industry 4.0 technologies.
TAKEAWAYS:
● To survive and prosper, manufacturers must strive to excel at product innovation.
● Manufacturers can use build-and-test iterations to validate new products technically and with customers. Build-and-test iterations can be done early, often, quickly, and cheaply.
● Artificial intelligence can be a game-changer in the new product development process.
Innovation propels companies to greatness! Consider the transformation in the list of top 10 companies in America over the past three decades. In 1990, all top 10 US firms were in traditional physical products industries (Table 1). Half were in oil and gas or petrochemicals. By 2020, only two of the 1990 top ten—IBM and GE—remain on the list, but further down.
Table 1: Top 10 US companies, 1990 vs. 2020
Two fundamental factors underlie this 30-year shift:
- A transition from manufacturing: Only half of the top 10 US firms in 2020 are manufacturers, while the product offerings of the top 10 firms has shifted from older technologies, such as oil and gas or traditional autos, to newer ones, such as IT and electric vehicles (EVs). Even individual companies like IBM, once renown for making computers, now predominantly offer software and services.
- An emphasis on successful product innovation: The newer entrants on the 2020 list, such as Apple, Microsoft, and Tesla, surged primarily due to successful product innovation. In contrast, companies that failed to innovate effectively were replaced. For instance, Kodak’s inability to adapt to disruptive innovation—namely, digital cameras—led to its downfall. Innovators like Tesla surged ahead with EVs, while GM fell behind, no longer on the top 10 list.
Innovation will remain the disruptive force moving forward to 2030, even more so than in the past. We now live in the Fourth Industrial Revolution driven by technologies such as artificial intelligence (AI) and machine learning, blockchain, and robotics and automation, which will create huge changes in industry, particularly in manufacturing.
Strategically, manufacturers must adopt some or all of these new technologies, and build them into their products and processes. A less visible but equally vital message is that manufacturers must strive to excel at product innovation in order to grow and prosper. Ironically, Kodak developed the first ever digital camera, but the company’s failure to successfully commercialize it ultimately led to its demise.
“Many firms’ NP processes are cumbersome and bulky—there’s too much bureaucracy and ‘non-value-added work.’”
Many manufacturers have a long way to go when it comes to successfully commercializing new products. New-product project success rates for physical product firms are now at 25–30 percent1,2—that is, less than one-third of new-product projects succeed commercially!
The Role of Operations in New Product Development (NPD)
How can Operations make a difference to the business’s pace of product innovation and its new product success rate?
Here are four ways:
1 Play new-product football*: A best practice—consistently found to be key to success—is that NPD is a cross-functional team effort.3 Operations/Manufacturing have often been left out of the new-product process. If included, they’re not on the field until near the end of the project, just before the final commercialization stage (Figure 1). This flawed process moves the ball down the field department by department—from Marketing to RD&E and finally to Operations and Sales. The term “transfer to the plant” too often typifies the final play from development to commercialization; a disconnect occurs. This process resembles a relay race, with the baton being passed from person to person (or department to department) with many dropped batons. And it is not the way to win at new products.
A truly cross-functional project team includes staff from all key departments—Marketing, RD&E, Operations, and Sales—and the project advances thanks to a team effort, much like a football team moves the ball, play by play, to the goal line. The process is typically a stage-and-gate new-product process like in Figure 1, where stages are the “plays” and gates are the Go/No Go decisions point or “huddles on the field.”4
Although there is often little work for the Operations members of the project team early in the project, they are still key contributors because their input, knowledge, and experience are crucial to success. They provide insights into
- Manufacturing feasibility (Can it be made?);
- Existence of core competencies (Can we make it?);
- Need for capital equipment, costs, and timing; and
- Likely manufacturing cost, source of supply risks, and resolution.
This information is vital to building a robust business case for a project, for making the right project selection decisions, and for ensuring a smoother, faster production startup in the commercialization stage.
Figure 1: Typical Stage-and-Gate New-Product Process
2 Making the right Go/Kill decisions: One way to improve new product success rates is picking the winners by making the best go/kill decisions. Besides being project team members early on and sharing important information, an important role for Operations senior management is to be at the Go/No Go meetings for projects (the gates). Gates are where NPD investment decisions are made, and where management decides which projects move forward. Project innovation is a business endeavor, not just the domain of Marketing and RD&E. Operations must have a clear voice at the investment decision table.
3 Accelerate the game—remove the waste: Today’s fast-paced world demands accelerated development. Many firms’ NP processes are cumbersome and bulky—there’s too much bureaucracy and “non-value-added work.” As a result, projects move at a crawl. Lean principles (Lean Six Sigma) were widely applied on the factory floor in the early part of this century, and Operations staff know the methodology well.
Operations can lead by example, helping the other business functions streamline the innovation process. Typically, value stream analysis is used to map the entire new-product process, idea to launch.4 Bottlenecks and time wasters get identified, and a root cause analysis is undertaken to determine why. Then time wasters are removed or reduced. It’s an effective method, used often in Operations, but it is not so well known by other functions. Some firms have applied this Lean methodology to NPD with quite dramatic results—up to 40–50 percent savings in time to market.4
“AI can also be used to facilitate portfolio management and project management. Within five years, predictive analytics may be making the Go/No Go decisions at gates.”
4 Be Agile in NPD: Everything changes quickly today: What was true in the early stages of the project is no longer true by the latter stages. A major unexpected challenge in NPD is that things have changed by the time the project reaches commercialization: the customers’ needs have shifted, a competitive product has been introduced, or product requirements are no longer valid. Instead of moving into production quickly, the project grinds to a halt, and it’s back to the drawing board. Late-stage changes in product design create huge costs and time delays.
A key principle of Agile development5 is being flexible and being able to pivot quickly—the product design is allowed to evolve as the project moves forward. Frozen design specs from the beginning of the development stage are a thing of the past. The goal is to get the get the product right pre-production. This agility concept is borrowed from Agile software development.
How? The project team undertakes a series of build-and-test iterations beginning before development, all the way to production startup.6 These build-and-test iterations validate the product both technically and with customers, early, often, fast, and cheaply. Built into each iteration are tests—technical tests as well as a demo to stakeholders (both customers and management). Negative feedback usually calls for a pivot in the project. If these iterations and pivots happen early and often, the cost and time of making changes is far less, and the product will be fully validated by the time it get to commercialization.
Some project teams fail to build these iterations into the process, especially the customer demos. Demos take time and money, and often involve a physical visit. (By contrast, in software development where Agile originated, demos can be done online.) Other teams wait until the product is almost developed before showing it to a customer. Smart teams, however, devise ways to test and demo non-existent products much earlier, and also undertake technical testing. Digital products, virtual products, computer animations, simulations, and AI tools are available to enable teams to show what the product will be, do, and look like long before a real prototype is ready to test.7 Regular build-and-test validations are much more feasible today thanks to new AI technology.
Operations people must be proactive on NPD projects, pushing hard to ensure that these build-and-text iterations are done; otherwise, odds are high that the product won’t be right when it gets to production startup. When that happens and product changes are needed as the project moves into commercialization, it becomes an “Operations problem.”
Build AI into your NPD System
Operations people have more experience with AI than RD&E, Marketing and Sales staff have. AI has impacted manufacturing in huge and very visible ways—for instance, optimizing the production process, process simulations, quality management, or managing the supply chain.8,9 Except for a handful of leading early-adopter firms like Siemens, Nestlé, and GE, AI has been much slower to penetrate the NPD process, however. As an early-AI-adopter, Operations can model the way and require that AI be pushed further upstream in the NPD process from the commercialization stage (Figure 1). Here are some examples:10,11
- AI in the Validation Stage: Digital twins mimic the product and can be used to monitor the real prototype product operating remotely during customer field trials. This dramatically improves test data quality, as well as reducing the time it takes for trials.12,13
- In Development: Development times can be cut in half by doing design and optimization iterations of product components digitally, as GE does in turbine design.14
- In the front end of the NPD process: AI can be used to scan many information sources looking for unmet needs and opportunities for new products, and can even generate new ideas and concepts.15 With simple verbal prompts, AI can create concepts and make concept drawings.16
AI can facilitate portfolio management and project management and thereby improve both on-time performance and success rates. Within five years, predictive analytics may be making the Go/No Go decisions at gates.
The Path Forward
Making product innovation work better and faster in your business this decade is imperative. But this is not a piece-meal effort—rather it should be an organization-wide initiative led by the leadership team. Operations must play a major role as you reshape your innovation process and methods in order to get it right—making it Lean and Agile, building in iterations for getting the product right, making the process truly cross-functional, and driving AI through the entire process. After all, it’s only the future of your company. M
References:
- Knudsen, M. P., von Pedowitz, M., Griffin, A., and Barczak, G. Best practices in new product development and innovation: Results from PDMA’s 2021 global survey. Journal of Product Innovation Management 2023;40;257–275.
- Barczak, G., Griffin, A., and Kahn, K. B. Trends and Drivers of success in NPD practices: Results of the 2003 PDMA Best Practices Study. Journal of Product Innovation Management 2009;26:93–23.
- Cooper, R. G. New Products: What Separates the Winners from the Losers and What Drives Success. In The PDMA Handbook of Innovation and New Product Development, 4th, edited by Ludwig Bstieler and Charles H. Noble, 3–43. Hoboken, NJ: Wiley. 2023.
- Cooper, R. G. The 5-th generation Stage-Gate idea-to-launch process. IEEE Engineering Management Review. 2022; 41(1):43–55.
- Beck, K., Beedle, M., van Bennekum, A. et al. Manifesto for Agile Software Development.
- Cooper, R. G., and Fürst, P. Agile Development for Manufacturers: The Emergent Gating Model. InnovationManagemenSE, Nov 10, 2020.
- Bilgram, V., and Laarmann, F. Generating Innovation with Generative AI: AI Augmented Digital Prototyping and Innovation Methods. IEEE Engineering Management Review. June 2023;51(2):18–25.
- Marr, B. The Future Of Manufacturing: Generative AI And Beyond. Forbes, July 25, 2023.
- D’Silva, V.,and Lawler, B. What Makes a Company Successful at Using AI? Harvard Business Review, Feb. 28, 2022.
- Cooper, R. G. The Artificial Intelligence Revolution in New-Product Development. [PDF] 2023.
- Cooper, R. G. The Artificial Intelligence Revolution in New-Product Development. YouTube video, 18:37.
- Huang, S., Wang, G., Lei, D., and Yan, Y. Toward digital validation for rapid product development based on Digital Twins: A framework.The International Journal Advanced Manufacturing Technology 2022;119:2509–2523.
- Nieto-Rodriguez, A., and Vargas, R. V. How AI Will Transform Project Management. Harvard Business Review, Feb. 2, 2023. https://hbr.org/2023/02/how-ai-will-transform-project-management
- Bogaisky, J. GE Says It’s Leveraging Artificial Intelligence To Cut Product Design Times In Half. Forbes, March 6, 2019.
- Applied Marketing Science. Our Solutions: Your Insights Partner. 2023.
- Roch, J. From Hot Wheels to handling content: How brands are using Microsoft AI to be more productive and imaginative. Microsoft News, Oct. 12, 2022.
About the author:
Robert G. Cooper is ISBM Distinguished Research Fellow at Pennsylvania State University’s Smeal College of Business Administration, Professor Emeritus at McMaster University’s DeGroote School of Business (Canada), and a Crawford Fellow of the Product Development and Management Association.
* North American football.
AI, Autonomous Operations Seen as Having Major Impacts by 2030
In a roundtable discussion, MLC Board members also opine on the evolution of supply chains, sustainability, and leadership requirements in the years ahead.
TAKEAWAYS:
● Artificial intelligence technology will have a substantial impact on operations and supply chains well before 2030.
● Autonomous factory and plant operations will happen but it will not make sense for every type of operation.
● Leaders will need to be able to manage the interface between the AI world and human world.
In October, six members of the Manufacturing Leadership Council’s Board of Governors gathered virtually to talk about what manufacturing might look like in 2030. The Board members discussed the potential impact of AI, autonomous operations, how supply chains may be architected, what status sustainability will have by the next decade, and the leadership behaviors and skills executives will need to lead digital businesses. The following are excerpts from that roundtable.
Q: How significant do you think AI is going to be in manufacturing operations by 2030?
Dan Dwight: I think AI is going to be core for us by 2025. I’m thinking of AI in the more traditional sense, making algorithms self-correcting to the point where you no longer have your operators having to do anything on the line. It’s going to empower the people.
Ron Castro: I think Dan is absolutely right that by 2025 we’ll see a lot of this. We’re already seeing quite a bit of an acceleration after ChatGPT and now the focus on AI for business. AI for the enterprise is accelerating as well. AI will be at the core of the any end-to-end supply chain, any end-to-end manufacturing process. But I also think there will be drastic changes on the human machine collaboration. How we interact with machines that are enabled by AI will be much more intuitive than it is today.
What’s coming as well is how we mentor the capabilities of more junior members of our teams. With AI, you’re able to capture a lot of knowledge, experience, and know-how from people who will be leaving the industry in the next few years. I think we’re starting to see it already in the last couple of years, but it just doesn’t seem to be a trend that’s going to slow down given the demographics.
There will have to be significant governance as we go forward. As we go into the future unstructured data will become much more critical as well. Having the capability to absorb and be able to optimize and understand what unstructured data is telling us will be key.
Rebecca Teeters: I hope to use it to really augment the great talent that I already have. And it’s interesting, sometimes humans are a little bit too close to a problem that we don’t think about it rationally. Sometimes we have assumptions, and we do all kinds of interesting calculations almost subconsciously that might lead us down the wrong path, where AI might not do that.
It’s actually a good checking mechanism on our scientific rigor in some of the decisions we’re making. So I see it as a technology that can augment the power of our people versus a replacement technology.
The key will be how we’re able to prioritize and focus on a few key opportunities and not try to apply these technologies to everything at one time, because then we’ll just overwhelm our ability to manage the change.
Q: Does anyone see a pushback coming from the workforce on AI or overreach by government to try to govern the technology?
Dan Dwight: At least to date, with Cooley becoming more data oriented and now having more sophisticated operator screens available to the folks on the line, our workforce has been gobbling it up. They love it because in some ways it makes their job easier. They’re no longer guessing, and when they’re guessing in my world, it’s going to result in a mistake. We don’t want to make a bad product, so the fact is we can optimize the facility, make their life easier and create better products.
But workers are still playing a role looking at that operator board, still making manual adjustments because we’re not yet there on complete AI. When we do get there, a person’s role is going to be very different. We’re still not sure exactly what that might look like for them.
Jim Davis: I do not see pushback from the existing workforce. There is generally high interest in engaging, as Dan says. I will add, though, that workers need to be aware, see leadership interest, and have access to the capabilities. We still see the gap widening between the larger companies that have the resources and those that don’t, and we still don’t see that manufacturing is viewed as a particularly high-tech profession from a future workforce standpoint. I did want to mention there can be workforce concerns with privacy and personal intrusion if AI is used to monitor individuals. I really like this new term of “co-piloting” that has emerged. It better communicates the value of using AI to support the worker to do his or her job better.
Q: Do you expect a loss of jobs in in the industry as a result of widespread AI adoption?
Dan Dwight: I don’t.
Jai Sundararaman: This is like a watershed moment. For the last seven decades, we were just talking about lean, nothing else. So now it’s AI. It’s going to be the AI generation for the foreseeable future. We can just say from our own experience, we thought we were operating best-in-class, but we raised our bar significantly beyond what we thought was possible with AI now.
In the future, factories without AI will struggle to attract top talent. Candidates will demand, ‘Do you have AI?’ If the answer is no, they’ll simply walk away.
Ron Castro: My view is the cost of entry of leveraging AI has been going down and will most likely continue to go down. This will make it less prohibitive for smaller and medium sized companies to start to play in in AI. By 2030 the cost of entry will be much lower than it is today, enabling smaller and medium sized companies to really play in this space as well.
Q: What other technologies will have a significant impact on manufacturing by 2030?
Ron Castro: A key point is the exponential value of having technologies interact with each other. For example, with 5G and IoT talking to each other and the more data they generate, the more insights we can get out of the data. So I think the aggregate of technologies will continue to grow.
And quantum. What quantum computers do extremely well is very complex optimization exercises. I really think by 2030 we will see some breakthroughs in quantum computing. Imagine AI interacting with quantum, simulating millions of possible scenarios which cannot be done by conventional computers and AI picking up on that ‘training’ data generating real time insights which we can only dream of today.
Jai Sundararaman: 3D printing continues to be an exciting frontier, with evolving technologies unlocking a multitude of possibilities. The integration of technology traceability and sustainability through digital twin concepts holds immense promise, poised to reshape the landscape in a truly transformative way.
John D. Gagel: I’ll just chime in on what Jay said. It’s that whole concept of a digital passport. So imagine having all the information about where your product came from, where it was manufactured, down multiple layers in the supply chain — a digital passport at your fingertips.
Rebecca Teeters: Well, in in my world, in the chemical world, the digital twin concept is just huge. The ability to model chemical reactions under certain situations to understand how, for example, a reactor system going to behave. That’s a big focus point for us because it saves us a lot of time and a lot of energy if we can do some digital twinning and understanding where things are working and where things aren’t working.
Other key technologies include being able to supplement human talent with digital goggles and additive manufacturing is just really taking hold.
Q: How do you see the architecting of supply chains playing out by 2030?
Ron Castro: Designing supply chains for resiliency versus just for cost will have more weight, although I suspect at some point cost will continue to be a key factor. But we will need to have the right tools in place to manage that resiliency. The continued expansion of digitally-enabled supply chains will continue to grow, in my view, exponentially. We’re just on the tip of the iceberg here with generative AI — and that’s going to continue to accelerate. In the future there will not be a process or a task or a supply chain operation that will not be augmented in some way by AI. This will create a faster evolution that will force companies to really rethink their processes.
Rebecca Teeters: My view is a very simple. Operational excellence. Architecting supply chains to get them as close to the point of consumption as possible. One, they’re more resilient that way, but two, just less inventory in the system, right? You have less material in the system at any given time that allows you to just flow material faster and you gain significant productivity. It’s fundamental cycle time math.
And honestly, we’re also seeing the fact that the world is flattening. There’s less variation in labor costs and utility costs and all these variables that have historically encouraged us to offshore and kind of move things around and chase all of these variables. I think the time has come to stop chasing the sweet spot and really design and architect supply chains for optimum flow. Not only material flow, but financial flow. That will gain us huge productivity advantages from my perspective.
Dan Dwight: But what I think is really interesting is, if you look at manufacturing to date, at least from the Cooley perspective, it’s been very internal focused within the walls of our factory — how we are digitizing, how we are driving AI, how we are becoming more resilient within the manufacturing process. We now have to go external and bring that resiliency model to our external partners, which will require us to open up and be even more transparent with our vendors and our customers. That is a lot more challenging.
Jim Davis: Ten years ago the manufacturing focus was largely about what happens within “my” company. No one was seriously thinking about supply chains as factories and end-to-end supply chains interoperating. If you fast forward to today, this industry and factory view has come into play with industry (and government) emphasizing importance. The implementation and needed scaling have not been worked out, however. Data are needed in factories, but also throughout supply chains for operational interoperability and for the materials and products visibility that addresses supply chain resilience. Data are also needed to address a significant increase in complexity. Demand dynamics, product customization, tighter specifications, faster setups, etc., have all increased while at the same time, economic, environmental, and social sustainability requirements are increasing, converging, and impacting factories and supply chains. You have to manage this complexity with increasing automation and autonomy that underpin simpler interfaces for higher level decision making.
Q: How close do you think the industry will come to autonomous factory operations by 2030?
Rebecca Teeters: I think there will be scenarios where we get there by 2030, for sure, and scenarios where we don’t, and part of that will just be the sheer capacity to change that much over the course of the next six years or so. For example, we are installing currently state of the art water treatment facilities at our chemical factories around the world. And as I look at these facilities, they’re very complex but I think these can be autonomous operations.
I should be able to operate these water treatment facilities lights out 100% autonomous and I should be able to do that in the next five or six years.
I think it’s going to depend on us making some very clear prioritization decisions and driving a few of them to the end point. This is absolutely possible and necessary in my opinion.
Dan Dwight: So having our extruders run autonomously through algorithms and AI, but it’s not complete lights out because you’re still going to have material handling issues. So I guess it’s how far down the spectrum you’re going toward ultimately being fully lights out?
Jai Sundararaman: In Taiwan, some companies in our industry have already embraced lights-out manufacturing for the past decade. With labor costs on the rise and a scarcity of available workers, it’s becoming increasingly clear that by 2030, many plants will be on the verge of lights-out operations. As we strive for cost-effectiveness, our industry is maturing in automation and digital process adoption, suggesting that we may soon achieve near lights-out capabilities.
John D. Gagel: I think it will depend on the process or the industry that you’re talking about. How far down the path they can go with lights out? Some of your more chemically intensive processes due to regulatory pressure may not. I don’t think you’ll see them go very far just because there’s a whole host of regulatory oversight requirements for heavy chemical processing or what you would consider high risk.
Ron Castro: It might not be lights out, but as I mentioned before, every single task will be enabled with technology, most likely AI. We’ll clearly be more intelligent and more optimized, either directly by AI or by humans being assisted by AI. By now we transformed approximately 80% of our internal processes to either be automated through AI or our supply chain professionals being augmented by AI. There is still a lot of work ahead of us in cross-company processes across the value chain. We as supply chain leaders need to push further digitization and automation across the value chain with our suppliers and our partners.
Jim Davis: There will be some situations where lights out will make sense. However, I see this more as automation and autonomy needing to increase to address the economics of competitiveness, increasing requirements, increasing complexity, and using the workforce in better ways (AI is critical). There’s a lot of economic headroom to drive a progression of human involvement, control, automation, and autonomy, but it is expensive. When we talk across companies and industries, economics remains the key driver. Importantly, there is a process in building the maturity that comes from using data and gaining a deeper understanding of the operation so automation and autonomy can be implemented and sustained with trust. This mindset about data and a maturity process with staged benefit and investment is not accounted for very well yet.
Q: How do you see the industry’s current focus on sustainability playing out by 2030?
John D. Gagel: I think I’ll go back to something that Ron said. This is a material science issue in my opinion. Sustainability is well established in the market. We all know the increasing regulatory requirements for reporting. So there is going to be a need for a lot of data now coming off of manufacturing and that’s where I think all the things we talked about will help. But the material science issue is the one that that it is getting increasingly challenging. For example, one of the most recent topics is PFAS (polyfluoroalkyl substances) compounds. If you have those in your products, how do you replace them?
So as you look at what we make our products out of, you can’t use what you used to use. For example, you all those PFAS compounds. If you have those, how do you replace them?
On the product sustainability side, we’re not talking about climate impacts at the start. We’re talking about what raw materials are you using to make those products and what is the impact of that material in its entire life cycle on the planet and on people. And I think that’s where sustainability will continue to be top of mind.
Rebecca Teeters: Gone are the days when industry can say I have a right to discharge because I have a permit. The world expects industry to move towards a pollution prevention, environmental stewardship mindset, period, and it’s time that we, as industry, accept that our job is to not impact our environment while we make the specialty materials we need to make to empower the world, we need to accept that reality and we need to get after it.
We’re a little comfortable with this idea, though. Many feel we have a regulatory regime and all I have to do is be in compliance with my regulatory regime. That’s antiquated thinking. I’ve been involved in round table debates globally around environmental stewardship and the chemical industry, and this is a very tough mindset shift for the chemical industry.
Q: What skills and behaviors will manufacturing leaders need by 2030?
Rebecca Teeters: So I’ve been thinking about this recently with respect to our plant managers. First of all, we need to acknowledge the fact that the scientific first principles of manufacturing are operational excellence. You still have to know them.
Then you need to have what I call floor presence. You need to be able to actually talk to people. You need to be able to engage with people to have really good conversations and that won’t change even in the face of all this digital stuff.
We need executive presence because we need to be able to communicate well and be heard, not just speak, but fundamentally be heard in order to, I think, address the most challenging part of being a leader in the new era, which is being able to see the macro changes like the environmental stewardship view and understand how to head in that direction.
You have to be visionary and you have to be able to manage the change and bring the people with you. Leaders need to be very humble and really believe that a good idea can come from anywhere and then once they see it, knowing how to apply it with good scientific rigor and bring their people along with it.
You just have to choose wisely where you’re going to accept more risk and try new things.
Dan Dwight: I think we need digital proficiency. It is an absolute qualification for any kind of new talent, including at the leadership level, And next generation leaders need to have a collaborative nature –whether it is with the supply chain, with AI, or in extending sustainability.
Ron Castro: A global mindset, but also more of a growth mindset.
Jai Sundararaman: There are two key elements to consider. Firstly, digital literacy, as Dan highlighted, and secondly, the digital mindset. The distinction lies in understanding that leading in a digital world necessitates a different approach than simply acquiring skills.
John D. Gagel: I’ll say speed and agility. The ability to process multiple data points in in real time. And then I think the other thing is being able to manage the interface between the digital AI world and the human world. So it’s a classic leadership thing: good people skills, good communication skills. M
About the contributors:
Daniel R. Dwight is President and Chief Executive Officer at Cooley Group.
Ron Castro is Vice President and Chief Supply Chain Officer at IBM.
Dr. Jim Davis is Vice Provost IT Office of Advanced Research Computing at UCLA
John D. Gagel is Chief Sustainability Officer at Lexmark International
Jai Sundararaman is Chief Transformation Officer at Intertape Polymer Group
Dr. Rebecca Teeters is President and Senior Vice President, Chemical Operations and Fluoromaterial Stewardship at 3M
Welcome New Members of the MLC December 2023
Introducing the latest new members to the Manufacturing Leadership Council
Ohad Axelrod
Vice President of Product Management
Standard Industries
standardindustries.com
https://www.linkedin.com/in/ohad-a-4300364/
Matt Fabrizio
Smart Factory Manager
Greene Tweed
gtweed.com
https://www.linkedin.com/in/matthew-fabrizio-3bb5ab25/
Iain James
Vice President of Manufacturing
Knauf Insulation
knaufinsulation.com
https://www.linkedin.com/in/iain-james-0a259355/
Kristopher Slozak
Director
West Monroe
westmonroe.com
https://www.linkedin.com/in/kristopherslozak/
Craig Souser
President and CEO
JLS Automation
jlsautomation.com
https://www.linkedin.com/in/craig-souser-3128106/
Leading through Values at the Vermeer Corporation
From its origins as a one-person shop on a central Iowa farm to its current status as a multinational global operation, the Vermeer Corporation has grown in every sense: number of employees, production locations and dealerships, the industries that it serves, and its product portfolio. But through it all it has maintained a focus on its guiding principles – putting people first, building the best, and giving back.
More than 70 members of the Manufacturing Leadership Council saw those principles in action when they toured the “Vermeer Mile,” Vermeer’s 3,500-employee corporate headquarters and primary production facility in Pella, Iowa.
Vermeer traces its roots to a mechanical wagon hoist invented by its founder, Gary Vermeer, in 1948. The hoist could be used to raise the wagon from the front end to dump its contents, such as grain, out of the back. Now on its third generation of family ownership, the company continues to manufacturer products for the agricultural industry, including hay balers, bale processors and wrappers, feed wagons, and mowers. But they also service the utilities industry with such products as pipeline directional drills and trenchers, and the recycling and forestry industry with products like wood grinders and other equipment to process organic waste.
Vermeer defines itself as a low-volume, high-option manufacturer – they produce roughly 22,000 units annually with many customizations. Plant tour attendees were taken through their Plant 7 building – where precision welding and painting take place – and The Center, an under-construction facility set to open in January 2024 that will bring under one roof the company’s operations technical training, team member solutions, and an employee clinic and pharmacy.
Within its operations, Vermeer has a strong dedication to utilizing Lean principles and is now in its 25th year of Kaizen, having completed 3,082 Kaizen events as of September 2023. They have maintained a strong focus on the basics of Lean, including regular report outs, in what they deem as a relentless pursuit of waste elimination. The company’s practices in Lean and continuous improvement feed into its innovation for new products and processes.
In terms of what drives capital and technology investment decisions, the focus is on those that provide the best ROI in addition to labor savings and safety. Generally, projects that deliver ROI in less than 3 years will get scaled. They are also focused on building supply chain resilience, taking a proactive approach to ESG compliance, and flowing information between disparate systems. Additionally, the company is working through an MES implementation and bringing software onto the plant floor for more data-driven decisions.
Some of the technology that Vermeer has deployed includes smart tools that are connected to operator instructions. This includes digital welding instruction software that can help new welders to learn and experienced welders to improve quality. The company has also installed 11 robotic welding cells between its facilities in Pella and Des Moines, helping to reduce unfilled welding jobs while also boosting quality and productivity.
The company has also implemented a limited amount of automation, such as an autonomous material handling system for purchased parts that handles more than 60 daily deliveries to seven assembly lines. Here, company leaders discussed the lessons they have learned while implementing automation: first, there was a need to train maintenance teams for servicing robots, while also training engineering teams on designing for automation. They also advised to bring in an integrator to advise on best practices and to avoid preventable errors.
Vermeer also puts a high premium on ensuring its team members are set up for success. Every new production employee is given one week of Operations training, regardless of past work experience, to build their competence and confidence for working in a manufacturing environment before transitioning to the next step of technical training or to the production floor. This training includes welding, painting, assembly, safety, and machine shop skills. Additionally, they are given instruction on soft skills and professionalism under the acronym of DOTS – Dependable, Open-Minded, Team Player, Safe.
One of Vermeer’s most popular employee benefits is its on-site pharmacy, run in a partnership with Walgreen’s, that provides both prescription and over-the-counter medication and other pharmacy goods at cost. The company also provides a medical clinic open to employees and their families, as well as retirees. The clinic provides family care and can offer referral to specialists if needed and gives employees an opportunity to be proactive about their health. The company said this has helped them to save on insurance costs.
Another popular employee service is the Vermeer Chaplaincy program, a counseling service that is open to all regardless of any spiritual background or belief. The chaplains can provide a listening ear for issues that occur at work or at home and provide suggestions on possible avenues of support. The program was started in 2007 and has provided more than 4,200 individual support sessions in the last year alone.
Finally, the company also offers an on-site childcare facility, known as the Yellow Iron Academy, providing care for children from infants to school age. It is located on the site of the Vermeer family farm and provides children with education to prepare them for or augment their academic careers.
With a history of pride in innovation and building the best products, plus prioritizing team member success, Vermeer stands as a role model for operating a high-performing global manufacturing business while keeping a focus on value-driven leadership.
Digital Leadership – An Imperative for Manufacturing 4.0
Improving people-centric leadership, psychological safety and intergenerational dynamics drive digital transformation forward
Digital transformation has been around as long as I have been in the workforce. The depth, capabilities and reach of technology has vastly grown, but the reality is we have been working on digital transformation for decades, in all industries and all capabilities. Yet, with all this experience, the percentage of digital transformations that fail continues to hover at around 70%, a dismal number[1].
Today, we are bringing some of our latest technologies in IoT, big data and analytics, and artificial intelligence into the industrial space with vast opportunities in efficiencies, quality improvement and increased safety. It is an exciting time for manufacturers and the stakes are high. However, as Manufacturing 4.0 technologies offer enhanced efficiency, manufacturing leaders are faced with both new and old challenges while implementing these new systems and processes. How can we improve on that 70% failure rate? Is digital transformation different on the shopfloor? How do I get everyone on board?
A digital leadership approach is key to achieving Manufacturing 4.0. It extends beyond the processes and technology. It requires taking a people-centered approach throughout the organization, creating a culture and atmosphere that drives resilience, agility and innovation, and encouraging participation and open communication at all levels of the organization.
The events of the last few years have shown that people are critical to manufacturing operations, even in our digital future. Manufacturers who successfully achieve their adoption of Manufacturing 4.0 technologies will have done so by engaging their leaders and employees and enabling organizational participation from top to bottom. They will have employed digital leadership.
What is Digital Leadership?
At its core, digital leadership involves leading through disruption and transformation, harnessing digital technologies to achieve organizational objectives. It calls for an understanding of emerging digital technologies and the ability to guide their integration into existing processes. But underpinning this is your employee base who must adapt to the fast-paced changes driven by technology. An even more critical key to any transformation’s success, these employees must understand the inner workings of the organization. A digital leader must foster an environment that encourages participation, drives agility and resilience, and rewards innovation at all levels of the organization. It is critical this leadership approach extend beyond the executive suite and managerial roles all the way to the front-line supervisors. Digital leadership focusing on the people first is key to achieving a successful transformation.
What Skills Do Your Leaders Need?
Effective leaders in the digital age are not just those in the C-suite. They are individuals across the organization who champion innovation, collaborate across levels and functions, and prioritize continual learning. that looked at leadership styles and their success during the COVID disruption, leaders using a coaching style had teams that were more resilient, engaged and productive[2].
We will call this digital leadership, and there are a few key skill sets that make digital leaders so effective in driving transformation through a manufacturing environment.
- Communication – Many change management programs focus on outward communication, informing about and justifying change. However, a strong digital leader focuses on active listening and curiosity. Through this type of communication, issues, concerns and blockages will be found earlier and resolved sooner.
- Conflict Resolution – There will be many conflicts that arise in any digital transformation. A successful leader ensures that respect for all parties is the basis upon which any conflict is addressed and resolved. By insisting on and modeling respect first, a leader shows each person they are valued and encourages issues to be brought forward.
- Accountability – Leading by example and doing what you say builds trust. Trust is one of the hardest things to build when introducing new processes and technologies. A digital leader is aware of their words and actions and acts in a way that builds trust.
- Self-Reflection/Vulnerability – Digital leaders have learned to embrace the uncomfortable. They acknowledge their own feelings and are open to where there may be gaps in the transformation program or their own knowledge. It is very important that digital leaders do not feel like they have to be the ultimate experts. A strong digital leader conducts a consistent self-reflection on the program and progress and is open to bringing in outside experts when needed.
- Empathy – A strong leader spends time noticing the people in the organization. They look for who is speaking up and who is quiet. They engage and seek to understand both types of people. In times of disruption, your biggest distractors will not actively speak to you as the leader. It is important to engage every member of the team to bring everyone along and find issues at the place and time they arise. This need for empathy at the individual level is why digital leadership must span the organization, from executive to front-line leader. Leaders must actively involve and include team members, understanding their motivations and aligning individual strengths with organizational goals.
Why Take a People-Centered Approach?
Manufacturers do not run without people. The people in your factories and central offices deeply understand the business and will be on the front lines of adopting the digital changes. In some cases, they will be contributing to the technology itself by supplying the knowledge and input needed for AI and ML models. In all cases, the people running the manufacturing lines will have a front-row seat into the impact and success of any technology implemented. It is critical that these employees and leaders feel comfortable voicing their concerns, sharing ideas and taking calculated risks. By taking a people-centric approach to digital transformation, organizations can tap into an enormous well of knowledge, support and energy to help drive the program’s success. On the contrary, if a command-and-control approach is taken, people will distrust the transformation, issues will not be reported, and innovative ideas will be silenced.
Psychological Safety – the Key to Success
Psychological safety refers to an environment where employees feel comfortable, secure and confident in expressing their opinions, concerns, ideas, and identifying mistakes without the fear of negative consequences. Creating a culture of psychological safety is critical in a manufacturing environment where safety, quality and efficiency are paramount. Considering the added complexity of a Manufacturing 4.0 transformation, building a culture of psychological safety can be the difference between success and failure.
Creating and maintaining psychological safety in manufacturing requires proactive efforts from leadership, clear communication channels, training programs and a commitment to address issues without blame or retaliation. When psychological safety is prioritized, employees are more likely to engage in the ongoing process of identifying and mitigating risks, ultimately contributing to a safer, more efficient, and higher-quality manufacturing operation and a successful digital transformation.
Some of the key components of a psychologically safe manufacturing environment that should be employed throughout the organization:
- Open communication is modeled and fostered
- Failures and learnings from mistakes are openly discussed with no blame
- Raising concerns or issues is celebrated and retaliation is not tolerated
- New ideas are considered and encouraged
- Employees feel comfortable expressing well-being concerns with leadership or HR
Fostering a culture where individuals are encouraged to voice their opinions or concerns and learn from their mistakes is essential. It will not only improve operations during the transformation but for the long haul as well.
Navigating Intergenerational Challenges
Today’s businesses encompass a diverse range of generations, from Generation Z to boomers and much has been made about intergenerational dynamics, particularly when it comes to digital participation. You could probably fill a library with the amount of material written on how to engage each generation, what they care about and how they work. With all of this noise, there is a strong risk that we make assumptions based upon generational classification. As leaders, we must understand how to manage intergenerational dynamics effectively, but at the same time challenge stereotypes and focus on each person individually with empathy and respect.
Baby boomers or Generation X have likely grown up in more of a command-and-control leadership environment which tends to minimize psychological safety. Yet, these more experienced employees also tend to possess invaluable experience and institutional knowledge that you do not want to lose, so building trust through empathy, respect and active listening will be critical to helping this persona be an active participant in the transformation. Building an inclusive environment invites this generation to contribute their experience, transferring know-how to the digital framework and to newer employees.
Younger generations, such as millennials and Generation Z have grown up in more of an open, collaborative environment where information is democratized and individuals have more power. Open communication, active listening and authenticity will be critical for this generation.
Although different generations might have varying approaches and motivations, it is critical that leaders avoid making stereotypical assumptions. Creating an inclusive environment where everyone’s voice matters and everyone is valued will create thriving intergenerational teams
Front Line Leaders are the Key to Success
Front-line leaders (or shopfloor leaders) are normally the newest leaders, have the largest span of control, and touch the largest section of the organization. Yet, these leaders are often not considered critical to a Manufacturing 4.0 transformation. Successful digital leadership expands to all levels of the organization. Since our front-line leaders touch such a large section of the organization, their impact must be considered and encouraged. Here are some ideas:
- Educate these leaders on the transformation’s goals and be open about timelines and changes.
- Actively listen to this leadership level on a regular basis taking their input and ideas into the program. Coach them to do the same with their teams and share that feedback up the chain.
- Supply adequate leadership training and ensure their leaders are modeling those skill sets critical to driving agility, resilience and innovation.
Having all levels of the organization acknowledge front-line leaders as key to a transformation’s success will support a positive outcome.
Digital Transformation is a Team Sport
The art of digital leadership lies in striking a balance between technological innovation and people-centric leadership. But this responsibility does not sit with one person or even a few. Each layer of the organization will be critical for success in both aspects. As organizations undergo digital transformation, it will be critical to supply leaders from the executive suite to the shopfloor guidance and resources needed for success. By fostering a culture of psychological safety, valuing intergenerational perspectives, and embracing employee input and dissent, leaders will build cohesive teams that trust one another and feel a sense of belonging. This will lead to better problem-solving, greater innovation and overall productivity – all critical for thriving through disruption.
Conclusion
Digital disruption and transformation have reached the shopfloor. The combination of IoT, big data and analytics, and artificial intelligence will drive significant improvements in quality, efficiency, safety and energy use. How quickly and extensively a manufacturer can get there will affect everything from that organization’s competitiveness to regulatory compliance. This era of rapid technological advancement requires manufacturing leadership to evolve. It’s not just about knowing how to leverage the latest tools; it’s about knowing how to empower, inspire and guide teams toward a future where technology and human potential intersect seamlessly. Employing this people-centric, digital leadership approach to transformation will provide a lift and accelerant to any Manufacturing 4.0 program.
As industries continue to change, it’s these digital leaders who will navigate the complexities of digital transformation, engage their employees in embracing the change, and propel their organizations to new heights.
About the Author:
Diane Guganig, an experienced Strategic Advisor and Sales Executive at Hitachi Digital Services, began her tech obsession at age five after touring a room-sized computer. Starting as a systems engineer, she spearheaded software development initiatives, led teams, and played pivotal roles in resolving significant business challenges. Transitioning to sales allowed her to partner with and solve a wider number of challenges, including intricate cross-industry issues. Her passion for technology has evolved into a mission to enhance the human experience, leading her to partner with purpose-driven enterprises dedicated to solving real-world problems for a better future.
[1] McKinsey: https://www.mckinsey.com/capabilities/people-and-organizational-performance/our-insights/successful-transformations
[2] https://www.betterup.com/blog/coaching-during-crisis International Journal of Evidence Based Coaching and Mentoring 2022, Vol. 20(2), pp.3-19. DOI: 10.24384/ektn-xx15
How Manufacturers Can Unlock the Power of Data
Manufacturers are using data to improve everything from their supply chains to their workplace culture—and more. Data can lead the way to new innovations, new business models and even new revenue streams. Yet, many manufacturing executives say they are not scaling data-driven use cases successfully, meaning that much of the information they do collect is going to waste.
So how can companies get the most out of their data and ensure they aren’t losing out on key insights?
A unique event hosted by the Manufacturing Leadership Council, the NAM’s digital transformation division, aims to answer these questions and more. “Manufacturing in 2030: The Coming Data Value Revolution,” which will be held on Dec. 6–7 in Nashville, Tennessee, will explore the ways manufacturers can unlock value from their data to boost productivity, value and competitiveness.
On the agenda: This event will have three key areas of focus:
- Data value: Attendees will learn what the future holds for data monetization, data ecosystems and data-driven innovation.
- People and process: They will also hear about the future workforce, including emerging and evolving job roles, data-driven leadership and data culture.
- Technology and data: And lastly, they will peek into a future where artificial intelligence, data visualizations and the industrial metaverse are part of our everyday manufacturing world.
M2030 agenda highlights: The presenters will also share practical insights that participants can put into action right away.
- In “Capturing Intelligence for Business Model Innovation,” IDC’s Bob Parker will examine digital maturity and the future of enterprise intelligence. Parker will explain how to create new business models through enhanced customer experience, as well as how to capture and leverage economies of intelligence.
- In “The Rise of Data Ecosystems,” John Dyck of the Clean Energy Smart Manufacturing Innovation Institute will deliver a practical explanation of Manufacturing-X, Gaia-X and Catena-X as well as their goals and challenges. Dyck will discuss trends driving data-sharing initiatives as well as related technical and governance issues.
- In “Building Great Supply Chain Visibility by 2030,” Supply Chain Insights’ Lora Cecere will address why 80% of the data being generated from supply chains isn’t being used well enough. Cecere will also explore how data can be used to create more resilient supply chains by 2030.
The bottom line: Advanced technologies are only part of the digital transformation story. Manufacturers who want to get ahead need to understand data’s role and value, not to mention how people, process, technology and even data itself will evolve by 2030.
Sign up: Registration is open for Manufacturing in 2030: The Coming Data Value Revolution. Click here to learn more.
NAM Study: Stricter Interest Expense Limitation to Cost Nearly 900,000 Jobs
Harmful Limit Disproportionately Impacts Manufacturing Sector
Washington, D.C. – The National Association of Manufacturers released a new analysis on the impact to the U.S. economy of Congress’ failure to reverse the stricter interest expense limitation that took effect in January 2022.
The jobs impact of the stricter limitation has nearly doubled over the past year given congressional inaction to ensure a pro-growth interest deductibility standard as interest rates have continued to rise. The data show that limiting manufacturers’ ability to deduct interest on debt-financed investments, over the long run, could cost the U.S. economy up to:
- 867,000 jobs;
- $58 billion of employee compensation; and
- $108 billion in GDP.
“A stricter interest expense limitation restricts manufacturers’ ability to invest in new equipment and create jobs. This analysis clearly shows that failing to reverse this damaging change will cut close to 900,000 jobs and billions of dollars of employee pay and harm economic growth. Even more, the study finds that manufacturers and related industries bear 77% of the burden of this policy,” said NAM Managing Vice President of Policy Chris Netram. “Congress must act by year’s end to restore a pro-growth interest deductibility standard and allow manufacturers to continue to invest for the future.”
Background:
Prior to 2022, the interest expense limitation was calculated based on a company’s earnings before interest, tax, depreciation and amortization (EBITDA). Last year, a stricter limitation based on a company’s earnings before interest and tax (EBIT) took effect. By excluding depreciation and amortization from the calculation, the stricter limitation increases the tax burden on manufacturers that make investments in long-lived capital equipment.
To view the full analysis click here.
-NAM-
The National Association of Manufacturers is the largest manufacturing association in the United States, representing small and large manufacturers in every industrial sector and in all 50 states. Manufacturing employs nearly 13 million men and women, contributes $2.91 trillion to the U.S. economy annually and accounts for 55% of private-sector research and development. The NAM is the powerful voice of the manufacturing community and the leading advocate for a policy agenda that helps manufacturers compete in the global economy and create jobs across the United States. For more information about the NAM or to follow us on Twitter and Facebook, please visit www.nam.org.
Dotson Iron Castings’ Story of Survival and Advancement
When a company traces its history back nearly 150 years, its story is likely one of continuous change and evolution. For Dotson Iron Castings of Mankato, Minn., it is also a story of survival, innovation and respect for people.
During the Manufacturing Leadership Council’s recent plant tour, Dotson’s leaders shared elements of this story and gave visitors a firsthand look at its production practices and culture.
Overcoming Obstacles
With its roots dating back to a blacksmith shop founded in 1876, Dotson Iron Castings has persevered through early product failures, a 1937 bankruptcy, the 1980s recession, a 2017 fire, and the COVID-19 pandemic, and emerged stronger due in part to the company’s leadership, people and culture.
In its early history, the company offered diversified products including an automobile, a tractor and its best-seller, the Little Giant Trip Hammer. The company also dealt in brass, aluminum, and steel. Since 1983, the 125,000 square foot foundry has focused solely on ductile iron primarily for the industrial, agriculture, and truck industry segments. By focusing on this single product, Dotson has become an iron casting and Manufacturing 4.0 leader.
Innovating for the Future
As the company has evolved, its leadership and employees have created a culture that respects people and encourages innovation. The company’s Manufacturing 4.0 journey has seen Dotson implement data generation and collection systems including a FARO Quantum Scan Arm that takes 3D measurements to inspect product quality. Other innovations showcased during the MLC tour include machine monitoring data, automated charging in the melt process and automatic mold pouring.
On the sustainability front, the company continues to find new ways to reuse energy and materials. It takes a tremendous amount of energy to reach iron’s 2700 degrees Fahrenheit (1482° C) melting point, which in turn creates heat energy that Dotson captures and uses to heat its facility in winter months, including an in-ground heating system to keep its loading dock area free from ice and snow – both common for Minnesota. The company reuses excess iron that is removed from castings in the finishing process and also reclaims the sand used in its molds, eliminating almost 70% of the non-recyclable waste leaving its facility.
Recognizing an Iron-Willed Team
When an electrical contractor caused a fire that destroyed all the company’s molding lines in 2017, it took Dotson six weeks to rebuild its operation. Rather than send workers home, company leaders kept its frontline workers employed in the cleanup process or by sending them out into Mankato to complete community service work.
After rebuilding and reopening the foundry, the company’s then-owners, Denny Dotson and Jean Bye, envisioned and built a new worker-focused space with showers, changing areas, lockers, upgraded break areas including an outdoor terrace, and a more welcoming reception area. The company calls this new space the “Club House,” and it serves as a further indication of the company’s commitment to its people.
More than Just a Tour
For MLC’s plant tour participants, the visit to Dotson Iron Castings included more than just a tour of the foundry and Club House. Visitors had the opportunity to network with fellow Manufacturing 4.0 professionals, participate in one of three breakout sessions, and ask questions both during the tour and a capstone panel discussion.
The breakout sessions dove deep into key topics facing both Dotson and participants alike: IT/OT Convergence, Energy Efficiency in an Energy Intensive Industry, and The Employee Center and Next Generation Workforce Influence. Dotson’s leadership team shared its experiences and answered questions, shedding light on the company’s continuing evolution.
The event culminated with a wide-ranging panel discussion featuring nine representatives of the host company. The panelists fielded audience questions about workforce turnover, technology innovation, and how the company has perpetually overcome challenges.
The Dotson Iron Castings tour showcased how the company – forged in fire – has equipped its employees with the right technologies and created a culture that is poised to build on its 147-year history.
All photos courtesy Dotson Iron Castings
The Surprising Keys to Manufacturing Digital Transformation
From IT and HR to finance and leadership, the keys to successful digital transformation lie in a cross-functional approach
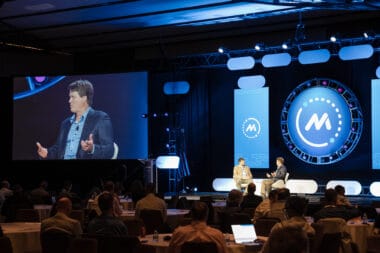
Few would argue that automation and digital transformation (DT) are not critical to the future of industrial automation. According to Gartner, 80% of manufacturing CEOs are increasing investments in digital technologies — led by artificial intelligence (AI), Internet of Things (IoT), and data and analytics — to counter economic pressures and to drive growth and profitability. Meanwhile, a 2023 MLC survey of manufacturing leaders indicates that 85% see an increase or no change to their companies’ Manufacturing 4.0 investment despite economic concerns.
And yet Gartner reports only 8% of industrial organizations say their DT initiatives are successful.
Eight percent?
It is a dismal number. Why so few?
It is tempting to pin the blame on technology snags. But technology is rarely the issue. Most organizations nowadays are engineering-led. They tend to jump on new technology right away. It’s cool and fun, and the solutions typically are readily available in the market.
Digital transformation initiatives in manufacturing fail because of organizational readiness. Or more specifically, the lack thereof.
To be clear, both organizational readiness and technical readiness are critical. But companies are generally better off when it comes to technical readiness due to the aforementioned reasons, and because they have a history of technology investments and the requisite skilled workers. With that as a backdrop, we advise industrial manufacturers to adhere to the following best practices when implementing digital transformation initiatives, with a particular emphasis on managing various organizational readiness issues, which span from the cultural to the financial.
Digital transformations should be cross-functional — but led by manufacturing operations
Digital transformation teams should be cross-functional, with representation from manufacturing, engineering, supply chain, and material operations. But cross-functional DT teams should be led by manufacturing operations. Why? Because manufacturing ops understands the floor — specifically, the problems on the floor and how to drive value.
IT is partner #1
Manufacturing operations and IT have to work hand-in-hand, with IT responsible for reliability, security and data — the latter of which is obviously the fuel for data-driven manufacturing. There are several best-practices specifically when it comes to the data.
- Data must be centralized so that the entire organization is working off of one source of truth.
- Data should be collected according to the problem you are trying to solve. Data isn’t free, so you do not need to collect it all. Start with the problem on the manufacturing floor, and let that dictate the data you collect.
- Data should be driven down to the appropriate people to make the appropriate decisions. Think through any data user — operator, team leader, quality leader, maintenance leader — and their standardized work. Then design your system to get the correct data in their hands for their jobs. (We will come back to some of the implications of getting this wrong.)
Don’t forget HR
HR support is critical in a few regards. First, HR can lead on the critical task of bridging the gap between newer, younger employees and older employees. Our workforce is transitioning and changing, and we are getting many new employees who have a great understanding of the technology and who bring new ways of thinking. At the same time, we have our older workers – I often refer to them as our “oak trees.” They really know how the floor runs and how it operates. Companies need both, and both can learn and benefit from each other.
HR’s other critical role is bringing team leaders and operators on the floor along on the journey. People will have concerns with any DT initiative. Will I get left behind? Is this going to replace me? Is Big Brother watching me? From day one, companies need to engage the floor — operators, team leaders, quality operators, maintenance operators — and make sure that they understand why the company is bringing technology in, the purpose, and how it is ultimately going to make their lives better and their jobs easier.
Be realistic about finances
Digital transformations are often under-capitalized. Ongoing costs are overlooked. Companies need to carefully account for expenses like ongoing maintenance costs, integration work, data collection and potential downtime. Many of these add-on costs aren’t properly captured in the budgeting process and later bite companies during implementation.
Leadership must protect the culture and drive decentralized data-driven decision-making
Leaders must embrace the transformation and ensure that digitization doesn’t degrade or destroy company culture.
First, leaders should never allow “data hoarding” at the top of the company, falling into the trap of thinking, Now I can solve all of these problems myself. Empower the right people with the right data to do their jobs. Problem-solving and continuous improvement should advance as long as data is being drive down to the right level of the organization.
Second, leaders must bring the operator along on the journey so they understand why the organization is making changes. This is similar to HR’s role mentioned above, but the questions that leaders answer are different. Why a wearable? How are these changes going to make me more effective and my job better? Leaders must not only manage the change — they have to inspire the workforce in the process.
Ultimately, company leaders should ask themselves, How do I make sure that we stay true to the philosophies that we learned from the Toyota Way — Kaizen and Genchi and Genbutsu … teamwork, respect and challenge? Culturally, nothing really has to change in the digitized world. The key is staying true to the philosophy of operator and team leader first, while driving data-driven decision-making throughout the organization.
About J.R. Automation
JR Automation, a Hitachi Group Company, partners with industrial manufacturers all over the world to design, build, and integrate advanced automation solutions — from assembly automation, dispensing, and vision systems to process design, controls engineering, and software integrations. We have built custom technology solutions for every application, process and industry, and helped ensure our customers were organizationally ready for the change.
About the Author:
Mike Lashbrook is Vice President Digital Solutions and Senior Vice President, M&A Connected Industry, JR Automation, a Hitachi Group Company.